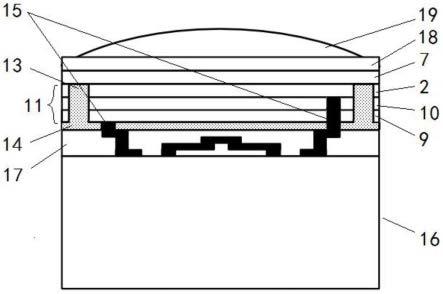
1.本实用新型属于半导体技术领域,涉及一种基于锗p-i-n光电二极管的图像传感器,具体涉及将锗p-i-n光电二极管制造和集成到图像传感器结构中,所述锗p-i-n光电二极管为制造cmos图像传感器的垂直p-i-n光电二极管。
背景技术:2.目前,短波红外cmos图像传感器(swircmos image sensor)已广泛应用于小型无人机系统、机动车辆系统、智能农业系统、监控系统等领域。如本领域所公知的,采用硅材料作为光电二极管对红外吸收的量子效率低下,特别是对于1μm以上的波段几乎没有吸收;与硅相比,基于锗的短波红外cmos图像传感器可捕获来自可见光(0.4μm-0.75μm)和更远波长(一直到1.6μm波长)的图像,而且性能与砷化铟镓(ingaas)相当。基于砷化铟镓的cmos图像传感器,尽管能够提供具有高量子效率及相对较低的暗电流的高质量焦平面阵列(fpa),但目前其制造工艺复杂、价格昂贵、生产制造过程中的成品合格率非常低,难以大规模商业化应用。与砷化铟镓相反,锗在化学上与硅兼容,并且与硅cmos制造工艺兼容。因此,用于短波红外cmos图像传感器的锗基光电二极管的制造工艺更灵活、更具成本效益和可扩展性,并能打开消费者/大众市场的应用。
3.在制造基于锗的cmos图像传感器时,现有技术一般采用在硅目标晶圆上直接外延生长锗,但由于锗和硅之间4.2%的晶格失配,外延生长会产生失配位错和穿透位错(螺纹错位),因而缺陷较多、质量较低,影响探测信噪比和检测灵敏度。此问题目前尽管能够通过一些技术手段得到改善,但会增加器件结构和/或工艺复杂性,例如使用窄孔径选择性制造生长。此外,由于采用在硅目标晶圆上直接外延生长锗是在硅晶圆上低温生长锗,直接导致降低了锗层的质量。
4.基于工业市场及消费者/大众市场的应用需要,目前急需一种工艺更简单、成本更低且能够高效、稳定地将垂直锗p-i-n光电二极管制造和集成到图像传感集成器件结构中的方法。
技术实现要素:5.基于现有技术中存在的问题,本实用新型提供了一种基于锗p-i-n光电二极管的图像传感器,具体涉及将锗p-i-n光电二极管制造和集成到图像传感器结构中,所述锗p-i-n光电二极管为制造cmos图像传感器的垂直p-i-n光电二极管。
6.依据本实用新型的技术方案,本实用新型提供了一种基于锗p-i-n光电二极管的图像传感器,其从下至上依次包括硅控制和读出电路晶圆、表面介电层、锗光电二极管层、抗反射层和透镜层,其中所述锗光电二极管层为层叠结构,从下至上依次包括第二掺杂锗层、未掺杂锗层和第一掺杂锗层,其中未掺杂锗层为本征层;第二掺杂锗层为n型区、第一掺杂锗层为p型区。
7.进一步地,锗光电二极管层还包括贯穿其层叠结构设置的沟槽间介电层,沟槽间
介电层将锗光电二极管层划分为多个独立的像素区域。
8.优选地,在每个像素区域中,表面介电层和锗光电二极管层上自下而上设置有两个金属连接。两个金属连接中的第一连接至第二掺杂锗层,第二连接至第一掺杂锗层。
9.进一步地,硅控制和读出电路晶圆的上部为具有电路的互联层,互联层的电路与金属连接相连接。
10.更优选地,在抗反射层和透镜层之间还具有滤光层,滤光层可以选择性地传输特定波长范围的入射光,同时吸收剩余的光。
11.与现有技术相比,本实用新型基于锗p-i-n光电二极管的图像传感器的有益技术效果如下:
12.1、本实用新型以相对更简单的制造工艺,实现了高速、小像素尺寸的短波红外图像传感器的生产制造工艺。
13.2、本实用新型的技术方案实现了批量、高生产合格率生产制造的低成本、cmos兼容的短波红外图像传感器(具有焦平面阵列)。
14.3、采用本实用新型生产工艺制造的图像传感器,其具有从可见光到短波红外波长的更低的暗电流、更高的灵敏度。
15.4、本实用新型的技术方案利用针对离子注入、洁净、键合、退火、剥离、化学机械研磨等进行有机组合,使其生产工艺相对简单、技术成熟、适于工业化大规模生产。
16.5、本实用新型将锗p-i-n光电二极管制造和集成到图像传感器结构中的工艺,采用锗-硅层转移技术获得高质量的光电二极管层单晶锗层,与在硅目标晶圆上直接外延生长锗层相比,具有更高的质量和更少的缺陷。
附图说明
17.图1至图14为依据本实用新型的基于锗p-i-n光电二极管的图像传感器结构示意图及制造流程示意图。
18.图中附图标记所指示的部件名称如下:
19.1、锗供体晶圆;2、第一掺杂锗层;3、锗转移层;4、硅目标晶圆;5、缓冲氧化层;6、研磨蚀刻停止层;7、抗反射层;8、锗硅混合晶圆;9、第二掺杂锗层;10、未掺杂锗层;11、锗光电二极管层;12、隔离沟槽;13、沟槽间介电层;14、表面介电层;15、金属连接;16、硅控制和读出电路晶圆;17、互联层;18、滤光层;19、透镜层。
具体实施方式
20.下面将结合本实用新型实施例中的附图,对本实用新型实施例中的技术方案进行清楚、完整的描述。显然,所描述的实施例仅仅是本实用新型的一部分实施例,而不是全部的实施例。基于本实用新型中的实施例,本领域普通技术人员在没有做出创造性劳动前提下所获得的所有其他实施例,都属于本实用新型保护的范围。另外地,不应当将本实用新型的保护范围仅仅限制至下述具体结构或部件或具体参数。
21.在本实用新型的描述中,需要理解的是,术语“上”、“下”、“前”、“后”、“左”、“右”、“顶”、“底”、“内”、“外”等指示的方位或位置关系为基于附图所示的方位或位置关系,仅是为了便于描述本实用新型和简化描述,而不是指示或暗示所指的装置或组件必须具有特定
的方位、以特定的方位构造和操作,因此不能理解为对本实用新型的限制。
22.本实用新型提供一种基于锗p-i-n光电二极管的图像传感器,具体涉及将锗p-i-n光电二极管制造和集成到图像传感器结构中,所述锗p-i-n光电二极管为制造cmos图像传感器的垂直p-i-n光电二极管。本实用新型以相对更简单的制造工艺,实现了高速、小像素尺寸的短波红外图像传感器的生产制造工艺;以及实现了批量、高生产合格率生产制造的低成本、cmos兼容的短波红外图像传感器(具有焦平面阵列)。采用本实用新型的图像传感器,其具有从可见光到短波红外波长的更低的暗电流、更高的灵敏度。
23.请参阅图14,本实用新型的基于锗p-i-n光电二极管的图像传感器,从下至上依次包括硅控制和读出电路晶圆16、表面介电层14、锗光电二极管层11、抗反射层7和透镜层19。锗光电二极管层11为层叠结构,从下至上依次包括第二掺杂锗层9、未掺杂锗层10和第一掺杂锗层2,其中未掺杂锗层10为本征层,第二掺杂锗层9为n型区、第一掺杂锗层2为p型区。锗光电二极管层11还包括贯穿其层叠结构设置的沟槽间介电层13,沟槽间介电层13将锗光电二极管层11划分为多个独立的像素区域。在每个像素区域中,表面介电层14和锗光电二极管层11上自下而上设置有两个金属连接15,其第一连接至第二掺杂锗层9,第二连接至第一掺杂锗层2。硅控制和读出电路晶圆16的上部为具有电路的互联层17,互联层17的电路与金属连接15相连接。
24.优选地,在抗反射层7和透镜层19之间还具有滤光层18,滤光层可以选择性地传输特定波长范围的入射光,同时吸收剩余的光。
25.制造本实用新型基于锗p-i-n光电二极管的图像传感器的流程示意图,请参阅图1至图14。
26.如图1所示,在锗供体晶圆1的顶部实施磷掺杂锗,即将磷离子注入锗供体晶圆1,进而形成n型区。如图1和图2所示,第一掺杂锗层2为n型区,注入的第一掺杂元素离子为磷离子(p
+
);如图7所示,第二掺杂锗层9为p型区,注入的第二掺杂元素离子为硼离子(b
+
)。制造本实用新型基于锗p-i-n光电二极管的图像传感器的流程包括如下步骤。
27.图1所示为步骤s1至步骤s2的示意图。
28.步骤s1,提供锗供体晶圆1;在优选实施例中,对锗供体晶圆1进行清洁和干燥,然后对锗供体晶圆1表面进行研磨,所述研磨采用化学机械研磨工艺,化学机械研磨工艺包括采用一定值ph值的研磨液对锗供体晶圆表面进行研磨;研磨液的ph值优选7~9,更优选地ph值为9。在研磨的过程中,根据研磨的进度及锗供体晶圆1平面的平整度,通过调整研磨液的流量和施加ph值调整液进来控制研磨进度,所述ph值调整液优选去离子水。所适用的锗供体晶圆的化学机械研磨设备包括研磨转盘、研磨垫、研磨液喷嘴以及ph值调整液喷嘴,其中研磨转盘用于固定待研磨锗供体晶圆并为所述待研磨锗供体晶圆提供旋转动力;研磨垫用于在与所述待研磨锗供体晶圆的相对运动中将所述待研磨锗供体晶圆的表层机械去除;研磨液喷嘴设置于研磨垫上方,用于将一定值ph值的研磨液注入至研磨垫上;ph值调整液喷嘴与研磨液喷嘴靠近设置,用于将ph值调整液注入至研磨垫上,并在研磨垫上与具有一定值ph值的研磨液混合,以形成第二ph值的研磨液;ph值调整液喷嘴上还设置有流量控制器,用于调整所述ph值调整液的流量,以将所述第二ph值调整至目标ph值。ph值调整液喷嘴以及研磨液喷嘴上均设置有流量控制器,分别用于调整ph值调整液的流量以及研磨液的流量,以将所述第二ph值调整至目标ph值。所述化学机械研磨设备还包括一ph值检测仪,用于
检测所述研磨垫上的研磨液的ph值。
29.步骤s1提供锗供体晶圆1进一步包括,可在锗供体晶圆1上沉积一层薄薄的掩蔽膜,例如等离子增强化学气相沉积(pecvd)二氧化硅(sio2)膜,以在随后的(步骤s2)磷离子和(步骤s3)氢离子注入期间保护锗供体晶圆1的表面,并且该二氧化硅膜可在磷离子和氢离子注入后移除。掩蔽膜也可以选择氮化硅、al2o3或光刻胶。
30.如图2所示,步骤s2将第一掺杂元素离子磷离子(p
+
)注入锗供体晶圆1的顶部锗区以形成第一掺杂锗层2(例如n型区)。随后进行退火以激活掺杂物。其中,掺杂物也称掺杂剂、植入物等,为已注入的磷原子。图2所示为步骤s2完成后状态的示意图。
31.图3所示为步骤s3的示意图。步骤s3,将氢离子(h
+
)注入锗供体晶圆1至选定深度,以确定锗转移层3(即,待转移的锗薄膜)的厚度。锗转移层3的厚度大于第一掺杂锗层2的厚度。在后续过程中,锗转移层3位置处形成锗光电二极管层。
32.在一些具体实施例中,氢离子注入可采用束线离子注入或等离子体浸没离子注入,注入条件例如:剂量范围:1
×
10
15
原子/cm
2-1
×
10
18
原子/cm2(优选》10
16
原子/cm2);能量范围:1kev-1mev(一般为~50kev);温度范围:室温(例如25摄氏度)至600摄氏度(优选《400摄氏度,从而尽量减少注入粒子通过扩散而逸出);选定的深度精度:
±
0.03微米至
±
0.05微米。
33.步骤s4,提供硅目标晶圆4,优选地,对硅目标晶圆表面进行研磨,所述研磨工艺或设备采用步骤s1中的化学机械研磨工艺或设备。此处的硅目标晶圆4可以是低成本的牺牲性硅晶圆。该步骤s4的硅目标晶圆4将在随后的步骤中被完全移除,即在最终产品中不存在此硅目标晶圆4作为光电二极管层的一部分,因此硅目标晶圆4不必是高质量的材料,可以使用质量较低的硅晶圆,从而降低成本。
34.步骤s5,在硅目标晶圆4上依次沉积缓冲氧化层5(又称氧化物缓冲层)和研磨蚀刻停止层6(cmp/etch stop),如图4所示。研磨蚀刻停止层6用于在后续步骤中控制硅的去除,以及用于阻止/停止研磨蚀刻过程;硅目标晶圆4和研磨蚀刻停止层6之间的抛光/蚀刻速率不同,研磨蚀刻停止层6还用作屏障和防止过度抛光,以防止锗转移层3被质量较低的硅晶圆污染。缓冲氧化层5是设置在硅目标晶圆4和研磨蚀刻停止层6之间的过渡材料,在硅目标晶圆4采用的是质量较低的牺牲性硅晶圆的情况下,缓冲氧化层5可以用于消除锗转移层3的应力。在另外的实施例中,在研磨蚀刻停止层6上还沉积有抗反射层7。图4所示为步骤s5完成后状态的示意图。
35.步骤s6,对锗供体晶圆1和硅目标晶圆4的表面进行洁净,以便进行贝塔(beta)键合。进行洁净(cleaning)步骤的目的是去除表面的氧化物,具体方法例如:
36.在锗晶圆表面上,采用丙酮、甲醇/乙醇和去离子水进行超声波清洗;在优选实施例中,采用去离子水和h2o2按照20:1稀释液进一步清洁,然后使用去离子水和hf按照50:1的稀释液,最后使用20:1稀释的h2o2稀释液再次清洁。
37.在硅晶圆表面上,采用rca-i和rca-ii溶液按前后顺序洁净,然后采用h2o2-h2so4洁净液进行洁净;在洁净之后,用干燥器去除晶圆表面的剩余液体或颗粒。在另外的实施例中,可采用将晶圆浸在氢氟酸中的方式,替代上述洁净工艺。
38.在介质表面上,采用丙酮、甲醇/乙醇和去离子水进行超声波清洗。
39.步骤s7,贝塔键合锗供体晶圆1和硅目标晶圆4的表面。更进一步地,此步骤中实际
接合的表面是第一掺杂锗层2的表面(锗供体晶圆1的一部分)和研磨蚀刻停止层6(如有抗反射层7,则是抗反射层7)的表面(硅目标晶圆4的一部分),如图5所示。
40.贝塔键合工艺又称自键合工艺、自粘合工艺等(self-bonding process),其方法具体例如方法一和方法二:
41.上述方法一,低温键合工艺,包括低温热步骤,在中等下将已洁净和/或已激活的表面压在一起,所述中等压力优选0.5mpa
–
2.0mpa,确保注入的粒子(氢离子或微气泡)不会引发断裂,或扩散或排出气体。此弱键合是由静电作用(范德华力)引起的。
42.上述方法二,等离子体洁净活化,采用来自ar、n2、nh3、ne、h2o、o2的等离子体撞击硅目标晶圆4,等离子体激活晶圆表面(晶圆表面产生悬挂键),然后将激活的硅目标晶圆4表面贴在锗供体晶圆1表面上,并对晶圆施加压力,使其在层对层界面上进行自键合。图5所示为步骤s7完成后状态的示意图。
43.步骤s8,将(键合粘附在硅目标晶圆4上的)锗转移层3与锗供体晶圆1分离(即剥离,使用热、机械或其他合适的技术进行剥离),得到锗硅混合晶圆8(即锗转移层3和硅目标晶圆4所构成的混合晶圆)。图6所示为步骤s8的示意图。
44.其中,剥离方法例如采用选择性剥离能量放置方法(selective cleave energy placement step),选择性剥离能量放置方法具体采用能量脉冲技术手段,能量脉冲就是通过提供局部(小范围内)能量脉冲、诸如采用热源(例如激光、加热灯)、冷源和机械源,从而实现例如扭转剥离;具体为加热(例如采用大约350摄氏度热源加热)或冷却或差异加热或差异冷却衬底(锗供体晶圆1或硅目标晶圆4)的一侧。在另外的实施例中,剥离方法采用离子注入气泡分离方法(implantation blister-separation step),具体包括将氢离子(h
+
)注入锗供体晶圆1,注入的氢离子捕获电子形成氢气,氢气在起泡层中形成微气泡层,平行于解理面(晶体的裂开面),加热锗硅混合晶圆8并沿解理面进行剥离;其中洁净步骤和自键合过程可参照前述贝塔键合相关过程。
45.可选地,对于分离后的锗供体晶圆1,通过研磨(化学机械研磨(cmp))表面并对表面进行洁净处理后,可重复使用;即反复使用一片锗供体晶圆1作为步骤s1的原料来产生锗转移层3,直至其厚度薄至无法继续使用。
46.步骤s9,完成锗硅混合晶圆8最终键合。
47.最终键合步骤采用如下键合步骤,例如:键合步骤方法一,退火键合步骤,在小于或等于400摄氏度的工艺环境下持续数小时,优选地,在300摄氏度的工艺环境下持续3小时。键合步骤方法二,施加电压键合步骤,施加电压以建立通过混合晶圆的电流,限制晶圆中引入的晶体缺陷,电流加热并导致晶圆之间的键合,优选采用界面局部加热键合,例如通过增加串联电阻局部加热进行键合。
48.步骤s10,研磨锗硅混合晶圆8的锗转移层3的表面。
49.其中,研磨例如采用化学机械研磨,具体地,浆液中含有温和的研磨剂和氧化剂(混合在去离子水中),研磨剂例如为硼硅酸盐玻璃、二氧化钛、氮化钛、氧化铝、三氧化铝、硝酸铁、氧化铈、二氧化硅(胶体二氧化硅)、氮化硅、碳化硅、石墨、金刚石,氧化剂例如为h2o2、kio3、硝酸铁。
50.图7为步骤s11的示意图。
51.步骤s11,将第二掺杂元素离子硼离子(b
+
)注入锗硅混合晶圆8顶部的锗转移层3,
使锗转移层3靠近表面的部分被注入硼而形成第二掺杂锗层9(p型区),第二掺杂锗层9和第一掺杂锗层2之间的部分为未掺杂锗层10(硼离子无法到达,故无硼,为本征区)。随后进行退火以激活掺杂物。此步骤完成后,之前的锗转移层3部分便形成了锗光电二极管层11,锗光电二极管层11是指,依次相连接的第一掺杂锗层2、未掺杂锗层10以及第二掺杂锗层9,此三层结构的部分。
52.图8、图9所示为步骤s12的示意图,图8为步骤s12.1完成后状态的示意图,图9为步骤s12.3完成后状态的示意图。需要说明的是,图9至图14均为单个像素区域的放大视图,例如图8中a所示部分。
53.步骤s12,在锗光电二极管层11中形成像素到像素之间的隔离结构,以界定光电二极管区域(即光电二极管阵列,亦即像素区域)。
54.步骤s12进一步包括:
55.步骤s12.1,构成隔离图案并通过蚀刻形成隔离沟槽12,以定义(划分)每个光电二极管区域(像素区域);例如,如果所需构成的像素的形状为方形,则隔离图案类似于方形网格;使用光刻方法对该网格进行图形化,然后进行蚀刻以生成隔离沟槽12;
56.步骤s12.2,用可流动的介电材料(例如聚酰亚胺)填充隔离沟槽12,形成沟槽间介电层13;
57.步骤s12.3,过量填充可流动的介电材料,使其填满隔离沟槽12后溢出,覆盖到像素区域,形成表面介电层14。
58.图10所示为步骤s13的示意图。
59.步骤s13,对第二掺杂锗层9(n型区)和第一掺杂锗层2(p型区)分别单独形成金属连接15。
60.步骤s13进一步包括:
61.步骤s13.1,构成金属连接图案并蚀刻过孔(即过孔形成)至第二掺杂锗层9(n型区)和第一掺杂锗层2(p型区)。通过物理气相沉积(pvd)在过孔的侧壁上形成阻挡金属(bm)和铜(cu)籽晶,通过铜电化学沉积填充过孔,形成金属连接15。
62.步骤s13.2,对表面进行研磨(例如化学机械研磨),去除多余的铜,露出铜垫和介质场,使金属连接15与表面介电层14相齐平。其中,表面介电层14可能在化学机械研磨后变薄。
63.步骤s14,在表面介电层14朝外侧的表面(通过任意合适的技术)形成对齐标记(alignment marks)。
64.图11所示为步骤s15的示意图。
65.步骤s15,提供硅控制和读出电路晶圆16。
66.其中,硅控制和读出电路晶圆16为p-i-n光电二极管阵列层(即,锗光电二极管层11)提供控制、读出和/或其他合适的电路,靠近外侧的表面为具有电路的互联层17,并且,互联层17朝外侧的表面为铜和阻挡金属化学机械研磨后形成的表面,即,表面暴露有电路金属触点(铜垫)。
67.以及,步骤s15进一步包括:
68.步骤s15.1,在互联层17朝外侧的表面(通过任意合适的技术)形成对齐标记。此对齐标记与步骤s14在表面介电层14表面形成的对齐标记相配合,从而在后续组合时实现辅
助对齐的效果。
69.步骤s16,将硅控制和读出电路晶圆16的互联层17朝外侧的表面与锗光电二极管层11的表面介电层14朝外侧的表面相对接,通过二者上的对齐标记保证二者对齐,使锗光电二极管层11的金属连接15与互联层17的电路相连接。并在二者之间进行键合,例如混合键合(铜-铜键合和氧化物-氧化物键合)。铜-铜键合过程为,在铜晶粒生长过程中,通过铜的相互扩散来连接上侧的铜垫和下侧的铜垫(金属连接15和互联层17的电路相对接的两铜部分的界面)。
70.其中,上述的对齐标记,也称对准标记,为现有技术。为了使器件能够工作,锗光电二极管层11的金属连接15与硅控制和读出电路晶圆16的互联层17的电路必须彼此对齐(电路相连通)。为此需要设置至少一组对齐标记,这些对齐标记是高精度特征,在组合定位时用作参考。对齐标记的设置根据现有技术即可实现,故本文不再赘述。
71.图12所示为步骤s16完成后状态的示意图(翻转视图)。
72.步骤s17,进行退火以完成键合。氧化物-氧化物键合过程为,退火时,通过脱水缩合反应连接上部和下部介质场,也就是连接互联层17和表面介电层14。
73.步骤s18,通过研磨(如化学机械研磨)、蚀刻(如湿法蚀刻),或其他合适的技术,去除硅目标晶圆4、缓冲氧化层5和研磨蚀刻停止层6。
74.图13所示为步骤s18完成后状态的示意图。
75.步骤s19,在抗反射层7顶部形成透镜层19。若步骤s5中已沉积了抗反射层7,则直接在其上形成透镜层19。若步骤s5中未沉积抗反射层7,则需先在表面(第一掺杂锗层2及沟槽间介电层13共同构成的表面)沉积抗反射层7,然后再在其上形成透镜层19。
76.优选地,在抗反射层7顶部和透镜层19之间还形成有滤光层18。
77.图14所示为优选实施方式中步骤s19完成后状态的示意图,即为最终产品的结构示意图。
78.综上所述,本实用新型以低成本、相对更简单的制造工艺实现了高速、小像素尺寸、cmos兼容的短波红外图像传感器(具有焦平面阵列),适于工业化大规模生产。同时,采用本实用新型的方法所制造的图像传感器从可见光到短波红外波长的暗电流更低、灵敏度更高。此外,本实用新型的方法中,锗供体晶圆可重复利用以产生更多锗转移层,资源利用率更高,以及硅目标晶圆采用质量较低的牺牲性硅晶圆,进一步降低制造成本。
79.以上所述,仅为本实用新型较佳的具体实施方式,但本实用新型的保护范围并不局限于此,任何熟悉本技术领域的技术人员在本实用新型揭露的技术范围内,可轻易想到的变化或替换,都应涵盖在本实用新型的保护范围之内。本领域普通的技术人员可以理解,在不背离所附权利要求定义的本实用新型的精神和范围的情况下,可以在形式和细节中做出各种各样的修改。