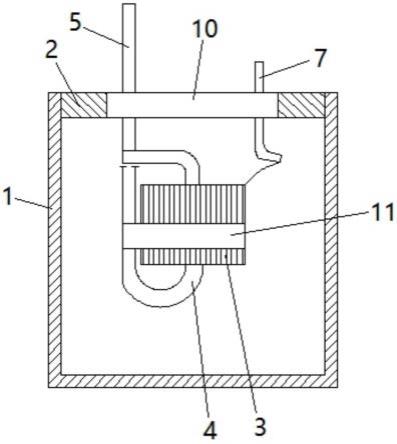
1.本实用新型涉及电子元器件技术领域,具体是一种电子式电流互感器。
背景技术:2.电子式电流互感器作为常见的电子元器件之一,是一种测量用的传感器,一般包括有敞口的壳体、设置于壳体口部的端盖、安装在端盖上的四个接线柱以及设置于壳体内部的线圈和铁芯。壳体口部的下沿沿着壳体的内壁通常设置有环形托架,用来支撑端盖。由于壳体本身的尺寸大小较小(长度和宽度往往均只有几厘米),为了提高壳体的内部空间,该环形托架的宽度很小(往往不足一毫米),导致端盖封装后其边沿易发生翘起或下沉的现象,从而产生缝隙,不仅不美观,而且影响到内部元器件的密封性能和绝缘性能。
3.此外,铁芯从线圈的内部穿过,其两端需要分别与二个接线柱相固定连接(焊接),线圈的二个接线端也需要分别与另外二个接线柱相固定连接,且为了保证电流互感器的正常使用,铁芯与线圈之间以及四个接线柱与线圈之间不能够直接接触,而壳体内部空间比较狭小,这就给内部走线和接线带来了很大的难度和挑战。
技术实现要素:4.本实用新型的目的是为了克服现有技术存在的缺陷和不足,提供一种电子式电流互感器,能够在壳体的内部形成独特的走线和接线结构,以满足内部走线和接线的需要,使得内部元器件之间不产生直接接触,以保证电流互感器的正常使用;此外,还能够提高整个器件的密封性能、绝缘性能以及防潮防水性能。
5.为实现上述目的,本实用新型提供如下技术方案:
6.一种电子式电流互感器,包括有上端敞口的壳体和盖合于壳体上端口的端盖,所述壳体的内部分别设置有线圈和铁芯,所述的端盖上分别固定有呈四角对称分布的第一接线柱、第二接线柱、第三接线柱和第四接线柱,所述第一接线柱、第二接线柱、第三接线柱和第四接线柱的下端均贯穿所述端盖并延伸到所述壳体的内部,其特征在于:所述的铁芯呈竖向贯穿所述线圈的内部,铁芯的上端呈l形折弯后与所述第一接线柱的下端相固定连接,铁芯的下端呈u形折弯后与所述第二接线柱的下端相固定连接;所述第三接线柱和第四接线柱的下端分别向远离所述线圈的一侧呈l形折弯后对应与所述线圈的二个接线端相固定连接;所述的壳体中灌封有环氧树脂胶,将所述线圈和铁芯封装于壳体的内部。
7.进一步的,所述壳体的内侧底面的四角均具有一体连接的支撑柱,所述的支撑柱沿所述壳体的相邻两侧内壁向上延伸到壳体上端口的下方,所述端盖的四角分别对应压置在四角的所述支撑柱上。
8.进一步的,所述支撑柱的顶端与所述壳体的上端口沿的距离等于所述端盖的厚度。
9.进一步的,所述支撑柱的截面呈直角等腰三角形。
10.进一步的,所述线圈的外部和所述的铁芯在位于线圈外侧的竖向部分共同缠绕有
绝缘胶带。
11.进一步的,所述的端盖上设有供灌入环氧树脂胶的通孔。
12.进一步的,所述的通孔为椭圆形通孔。
13.与现有技术相比,本实用新型的有益效果是:
14.1、本实用新型使得铁芯呈竖向贯穿线圈的内部,铁芯的上、下端分别呈l形和u形折弯后对应与第一、二接线柱的下端相固定连接,第三、四接线柱的下端分别向远离线圈的一侧呈l形折弯后对应与线圈的二个接线端相固定连接,能够在壳体的内部形成独特的走线和接线结构,能够充分利用壳体内部比较狭小的空间,满足了内部走线和接线的需要,使得内部元器件之间不产生直接接触,从而保证了电流互感器的正常使用。
15.2、本实用新型采用灌封环氧树脂胶,将线圈和铁芯封装于壳体的内部,提高了整个器件的密封性能和绝缘性能,并提高了防潮防水性能。
16.3、本实用新型在壳体内部的四角均设置支撑柱,既不影响壳体内部元器件的正常布置,又使得端盖在盖合后其边沿不会发生翘起或下沉的现象,避免了因产生缝隙而影响到内部元器件的密封性能和绝缘性能。
附图说明
17.图1为本实用新型在灌封环氧树脂胶前的内部结构示意图一。
18.图2为本实用新型在灌封环氧树脂胶前的内部结构示意图二。
19.图3为本实用新型在灌封环氧树脂胶后的内部结构示意图。
20.图4为本实用新型中壳体的结构俯视图。
21.图5为本实用新型中端盖的结构俯视图。
具体实施方式
22.下面将结合本实用新型实施例中的附图,对本实用新型实施例中的技术方案进行清楚、完整地描述,显然,所描述的实施例仅仅是本实用新型一部分实施例,而不是全部的实施例。基于本实用新型中的实施例,本领域普通技术人员在没有做出创造性劳动前提下所获得的所有其他实施例,都属于本实用新型保护的范围。
23.参见图1-5,一种电子式电流互感器,包括有上端敞口的壳体1和盖合于壳体1上端口的端盖2,壳体1的内部分别设置有线圈3和铁芯4,端盖2上分别固定有呈四角对称分布的第一接线柱5、第二接线柱6、第三接线柱7和第四接线柱8,第一接线柱5、第二接线柱6、第三接线柱7和第四接线柱8的下端均贯穿端盖2并延伸到壳体1的内部,铁芯4呈竖向贯穿线圈3的内部,铁芯4的上端呈l形折弯后与第一接线柱5的下端相固定连接,铁芯4的下端呈u形折弯后与第二接线柱6的下端相固定连接;第三接线柱7和第四接线柱8的下端分别向远离线圈3的一侧呈l形折弯后对应与线圈3的二个接线端相固定连接;壳体1中灌封有环氧树脂胶12,将线圈3和铁芯4封装于壳体1的内部。
24.本实用新型中,壳体1的内侧底面的四角均具有一体连接的支撑柱9,支撑柱9沿壳体1的相邻两侧内壁向上延伸到壳体1上端口的下方,端盖2的四角分别对应压置在四角的支撑柱9上。由此,既起到可靠支撑端盖2的作用,又不影响壳体1内部元器件的正常布置。
25.具体的,支撑柱9的顶端与壳体1的上端口沿的距离等于端盖2的厚度。由此,在端
盖2的四角分别对应压置在四角的支撑柱9上后,端盖2的上表面刚好与壳体1的上端口沿相平齐,使得端盖2的边沿不会发生翘起或下沉的现象。
26.此外,支撑柱9的截面呈直角等腰三角形,结构稳定,能够为端盖2提供可靠的支撑。
27.本实用新型中,线圈3的外部和铁芯4在位于线圈3外侧的竖向部分共同缠绕有绝缘胶带11,起到辅助固定的作用。
28.本实用新型中,端盖1上设有供灌入环氧树脂胶12的通孔10。
29.具体的,通孔10为椭圆形通孔,相较于圆形通孔,不仅更加美观,而且其截面积更大,更有利于环氧树脂胶12的灌入和迅速硬化。
30.以下结合附图对本实用新型作进一步的说明:
31.装配时,首先将铁芯4呈竖向贯穿线圈3的内部,再将铁芯4的上端呈l形折弯后与第一接线柱5的下端相固定连接(焊接),并将铁芯4的下端呈u形折弯后与第二接线柱6的下端相固定连接(焊接)。
32.此外,将第三接线柱7和第四接线柱8的下端分别向远离线圈3的一侧呈l形折弯后对应与线圈3的二个接线端相固定连接(焊接)。
33.接着,在线圈3的外部和铁芯4位于线圈3外侧的竖向部分共同缠绕绝缘胶带11,尽量保持铁芯4与线圈3同轴设置。
34.然后,将上述装配好的线圈3和铁芯4放入壳体1的内部,并使得端盖2的四角分别对应压置在四角的支撑柱9上。
35.然后,通过通孔10向壳体1的内部灌入环氧树脂胶12,待其硬化后,将线圈3和铁芯4封装于壳体1的内部,并将端盖2固定于壳体1的上端口。
36.使用时,通过第一接线柱5、第二接线柱6、第三接线柱7和第四接线柱8进行相应的接线即可。
37.需要说明的是,为了便于铁芯4的上端和下端分别对应与第一接线柱5和第二接线柱6相固定连接(焊接),也为了保证连接的牢靠性,第一接线柱5和第二接线柱6均应当采用与铁芯4的直径相适配的粗径接线柱。
38.此外,由于第三接线柱7和第四接线柱8仅分别对应与线圈3的二个接线端相固定连接(焊接),因此,第三接线柱7和第四接线柱8均可采用细径接线柱。
39.虽然本说明书按照实施方式加以描述,但并非每个实施方式仅包含一个独立的技术方案,说明书的这种叙述方式仅仅是为清楚起见,本领域技术人员应当将说明书作为一个整体,各实施例中的技术方案也可以经适当组合,形成本领域技术人员可以理解的其他实施方式。
40.故以上所述仅为本技术的较佳实施例,并非用来限定本技术的实施范围;即凡依本技术的权利要求范围所做的各种等同变换,均为本技术权利要求的保护范围。