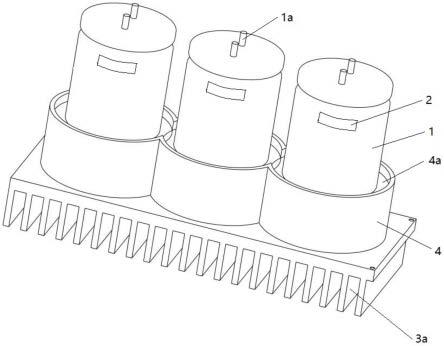
1.本实用新型涉及电子元器件,尤其涉及一种带散热器的大功率电解电容以及车载充电机。
背景技术:2.电解电容由于大容量和耐受电流能力强,所以经常用在大功率电路上用作pfc母线或者输出滤波电容。在这种大功率应用场景下,电解电容损耗极大,会产生很多热量,如果不能将电解电容的热量有效散出去,电解电容温度就会升高,电解电容长期处在高温环境下会加快内部电解液挥发,减短电容寿命,并且加速电容容量衰减。一般在设计上会通过设置多个电解电容来解决寿命的问题,但电解电容体积比较大,增加数量就意味着体积增大。另外由于电解电容的外壳为金属,且并不绝缘,安装时还需考虑电容之间的绝缘距离,这不符合小体积的设计目标。如果能优化电解电容的散热环境,就能减小电容用量,提高电容寿命。所以业内亟需开发一种带散热器的大功率电解电容。
技术实现要素:3.为了解决现有技术中存在的上述缺陷,本实用新型提出一种带散热器的大功率电解电容以及车载充电机。
4.本实用新型采用的技术方案是设计一种带散热器的大功率电解电容,包括柱状的电容本体,所述电容本体的侧壁上设有防爆阀,所述电容本体的尾部设有散热构件,所述散热构件上设有盲孔,所述盲孔的内径形状尺寸与电容本体相适应,电容本体可插入盲孔中、防爆阀和电容本体头端露在盲孔外部。
5.所述电容本体外壳与盲孔之间填充散热胶。
6.所述盲孔的端口设有一圈下沉的灌胶槽。
7.所述盲孔设有多个,相邻盲孔的灌胶槽彼此相互连通。
8.所述散热构件采用风冷式散热构件,散热构件表面设有散热翅片。
9.所述散热构件采用水冷式散热构件,散热构件内部设有散热水道、或者固定散热构件的设备外壳上设有散热水道。
10.所述散热构件上设有散热管,所述盲孔设于散热管内。
11.所述电容本体的外壳采用导热良好的金属材料。
12.所述电容本体安装在pcb板上,pcb板安装在散热构件上。
13.本实用新型还设计了一种车载充电机,包括设备外壳和控制电路,所述控制电路中的电解电容采用上述的带散热器的大功率电解电容。
14.本实用新型与现有技术相比,具有下列优点:
15.1、更改掉传统电解电容防爆阀的位置,由底面改到侧面,且距离底部有一定高度的位置,这样可以利用电容底部部分进行有效散热;
16.2、散热器的整体材料为铝合金或其他导热性强的材料,电容和结构材料之间通过
散热胶水填充,可以直接导热有效解决电解电容的散热问题;
17.3、散热器背部有用于风冷散热的翅片或者水冷散热的水道,且优化了散热路径。经过实际测试,使用本实用新型的散热方法,比起电解电容底部通过导热胶和机壳相连的方案,电解电容温度最高可以降低34℃,最低温度也降低了20℃。使用此实用新型的散热器相当于电容寿命提高了4到8倍左右。可以大幅度提高电容寿命和可靠性。
附图说明
18.下面结合实施例和附图对本实用新型进行详细说明,其中:
19.图1是较佳实施例中电解电容本体的示意图;
20.图2是采用风冷式散热构件的电解电容;
21.图3是采用水冷式散热构件的电解电容;
22.图4是采用水冷式散热构件长散热路径示意图;
23.图5是采用水冷式散热构件短散热路径示意图。
具体实施方式
24.为了使本实用新型的目的、技术方案及优点更加清楚明白,以下结合附图及实施例,对本实用新型作进一步详细说明。应当理解,此处所描述的具体实施例仅仅用于解释本实用新型,并不用于限定本实用新型。
25.本实用新型公开了一种带散热器的大功率电解电容,参看图1其包括柱状的电容本体1,所述电容本体的侧壁上设有防爆阀2;参看图2或图3,所述电容本体的尾部设有散热构件,所述散热构件上设有盲孔,所述盲孔的内径形状尺寸与电容本体相适应,电容本体可插入盲孔中、防爆阀和电容本体头端露在盲孔外部。附图中1a标号所指为电容引脚。
26.需要指出,防爆阀2在侧壁上的高度只要高过盲孔的位置,以及后续提到的灌胶槽的高度就可以,以免防爆阀泄压时被阻挡。
27.现有电解电容的防爆阀一般设置在底部,可利用的散热面积有限,仅仅是电容底面部分面积或用导热硅脂对侧面进行散热,但存在一些问题,例如散热效率差,成本高,且在电解电容和散热结构之间的绝缘导热垫具有一定的厚度,影响散热效果,即使用散热硅脂加强散热,但硅脂不能紧密接触散热面导致散热效果受到影响。
28.本实用新型改变了防爆阀的位置,将电解电容插入散热构件的盲孔中,这样电解电容底部可以有充分的散热空间。使散热构件和电解电容接触的面积增大,极大的提高了散热效果,大幅度提高电容寿命和可靠性。防爆阀的形状在此不作限定。
29.在较佳实施例中,所述电容本体1外壳与盲孔之间填充散热胶。使用散热胶灌胶处理可以改善电解电容的散热问题。参看图2或图3示出的实施例,所述盲孔的端口设有一圈下沉的灌胶槽4a。灌胶槽的设置可减小散热胶的用量。其中,散热胶可固化。灌胶槽的高度低于电解电容的防爆阀的位置。
30.在一些实施例中,所述盲孔设有多个,相邻盲孔的灌胶槽4a彼此相互连通。在图2和图3示出的实施例中,有3个盲孔,可放置3个电解电容。
31.在图2示出的实施例中,所述散热构件采用风冷式散热构件,散热构件表面设有散热翅片3a。散热构件的整体材料为铝合金或其他导热性强的材料,提高散热器周围和空气
的接触面积,增强散热构件和空气的热交换。电解电容安装在散热构件设有散热翅片的背面,通过散热胶与散热构件连接。
32.在图3示出的实施例中,所述散热构件采用水冷式散热构件,散热构件内部设有散热水道3b。水道和大功率电子电力设备中的冷却水道为一体的,在该散热方式下,电解电容的温度散热效果明显,极大增加了电解电容的寿命。在另一个实施例中,散热构件安装在设备外壳上,设备外壳上设有散热水道。在该实施例中,散热构件、设备外壳、散热水道一体成型。电解电容发出的热量经散热构件、设备外壳到达散热水道进行散热。
33.为了节省散热构件材料的消耗,在散热构件上设置散热管4,所述盲孔设于散热管内。这样比在整块的材料上钻盲孔,可节省大量的材料。
34.在较佳实施例中,所述电容本体1的外壳采用导热良好的金属材料,以获得良好的散热效果。
35.在较佳实施例中,所述电容本体1的侧壁和底面包裹一层绝缘材料。底面可以用很薄的绝缘材料垫着,即电容表面绝缘材料束缚住。绝缘材料包裹之后,电解电容对周围部件的安规距离需求大大减小,而且包裹绝缘材料之后能减小电容轻微碰撞导致的损伤。
36.在较佳实施例中,所述电容本体1安装在pcb板上,pcb板安装在散热构件上。pcb板和散热构件之间用螺丝或其他方式进行固定,方便在其他应用场合使用;散热构件和灌胶槽还可以与机壳一体成型,大大节省成本。
37.本实用新型将防爆阀改动到侧面,就可以充分利用底面进行散热。使用灌封胶比硅脂来说价格更便宜,而且不需要施加紧密贴合的力也可以得到非常好的散热效果。另外用绝缘材料包裹电容,可以不用考虑电容和散热部件之间的绝缘距离,只需要考虑安装距离即可。电容和散热面的距离减小,一方面减低热阻,提高散热效率,另一方面可以减小导热胶的使用。经过计算,电解电容包裹绝缘材料之后,电容到壳体之间的距离可以由4mm减小到0.5mm,导热胶用量可以减少80%,电解电容温度可以进一步降低5℃。高导热系数的散热胶价格昂贵,减小80%散热胶而且能提高散热效率,对于产品而言优势巨大。
38.此种散热构件不仅是作为单独的散热器来使用,也可以利用给电解电容灌胶散热处理的方法,灵活应用在各种需要电解电容散热场合。
39.本实用新型已经经过试验对比测试,方案1为电解电容未经特殊处理,电容底部和机壳之间通过导热硅脂连接散热,电容底部机壳未直接连接散热源(水道)的方案,和水道之间有较长的散热路径。方案2为部分利用本实用新型方案,参看图4示出的长散热路径示意图,所述散热构件安装在设备外壳上,将电解电容放入散热槽中,在散热槽灌胶,设备外壳上设有散热水道。散热构件和散热水道相距较远。方案3为本实用新型方案,参看图5示出的短散热路径示意图,散热盲孔和散热构件一体成型,电池和盲孔之间填充散热胶,水道和电解电容之间距离非常接近。
40.三种方案中方案1是最简单最容易实现的,也是应用最广的方案,但散热效果比较差。方案2是增加和电容的接触面积,同样也优化了热源和冷却部件之间的散热路径,散热效果相比方案1有了很大的提升。方案3是在方案2的基础上进一步优化了散热路径。
41.测试在水温65℃下满载进行。测试到温度稳定后电容温度。可以看到电容外壳温度已经非常接近冷却液温度了。
42.电容位号方案1方案2方案3
c190.3875.14870.302c297.6279.30573.215c3101.7476.86971.138.c4107.7180.44974.241
43.比起方案1的散热方法,使用本实用新型,可以大幅度降低电解电容温度。
44.本实用新型还公开了一种车载充电机,包括设备外壳和控制电路,所述控制电路中的电解电容采用上述的带散热器的大功率电解电容。
45.以上实施例仅为举例说明,非起限制作用。任何未脱离本技术精神与范畴,而对其进行的等效修改或变更,均应包含于本技术的权利要求范围之中。