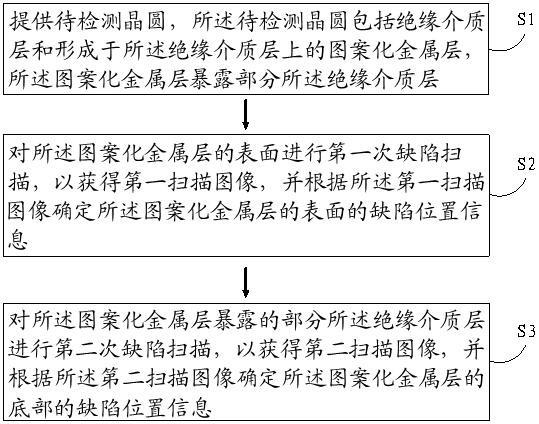
1.本领域涉及半导体集成电路技术领域,具体涉及一种缺陷检测方法。
背景技术:2.顶层金属铝工艺用于形成顶层铝互连线,一般通过刻蚀铝金属层形成铝互连线。在刻蚀铝金属层过程中,由于侧向刻蚀(或称为钻刻)在铝互连线底部容易产生凹陷状的结构缺陷,此结构缺陷称为底部内切(under cut)缺陷。图1所示为顶层金属铝工艺中产生的底部内切缺陷的透射电镜(tem)图,图1中显示,在对底部结构层01上沉积的铝金属层进行刻蚀形成铝金属线02时,由于侧向刻蚀效应,在铝金属线的底部形成了关键尺寸为300nm~400nm的底部内切缺陷03。当铝层越厚时,刻蚀偏差越大,底部内切缺陷03关键尺寸越大。图1中所示的300nm~400nm关键尺寸的底部内切缺陷会影响铝互连线的稳定性,最终会造成铝互连线的剥落,导致器件失效。现有技术中,对底部内切缺陷的检测手段包括失效分析(failure analysis)阶段进行的切片分析和局部的电镜分析(例如聚焦离子束微观分析,fib)。然而,这些检测手段需要手动介入,十分耗时,无法对多个lot、多片晶圆进行线上检测,且对晶圆器件区影响较大,可能会导致晶圆的良率损失。
3.业界的光学或电子束缺陷检测方法可以对晶圆表面存在的缺陷进行线上(inline)自动检测。该缺陷检测过程为:首先,缺陷扫描(defect scan)机台对待检测晶圆表面进行扫描得到缺陷位置信息;然后将所述缺陷位置信息传送给缺陷复检(defect review)机台,缺陷复检机台根据所述缺陷位置信息对缺陷所在位置的结构进行拍摄得到缺陷图像(image),并对缺陷图像进行处理和分析,以确定缺陷的真假、类型和影响,作为进行后续良率分析的判断依据。其中,扫描机台的工作原理一般是采用光学检测的方式对待检测晶圆表面进行扫描,将获取的数字化扫描图像信号作邻近芯片间(die to die)的相互对比,之后将对比结果与预设的阈值比较,并留下超过阈值的缺陷位置。这种缺陷检测方法可克服上述的切片分析和电镜分析等方法的不足,具有可自动线上检测、高效且不影响待检测晶圆的良率等优点。然而现有缺陷检测方法中,在对顶层铝互连线进行缺陷检测时,一般只对铝互连线的上表面进行缺陷扫描,以检测铝互连线上表面的缺陷信息。这种检测方法无法得到铝互连线底部的信息,因而无法检测到铝互连线的底部内切缺陷。因此,急需对现有的缺陷检测方法进行改进,以解决现有的缺陷检测方法无法检测铝互连线的底部内切缺陷的问题。
技术实现要素:4.为解决现有的缺陷检测方法无法检测铝互连线的底部内切缺陷的问题,本发明提供一种缺陷检测方法,包括以下步骤:提供待检测晶圆,待检测晶圆包括绝缘介质层和形成于绝缘介质层上的图案化金属层,图案化金属层暴露部分绝缘介质层;对图案化金属层的表面进行第一次缺陷扫描,以获得第一扫描图像,并根据第一
扫描图像确定图案化金属层的表面的缺陷位置信息;对图案化金属层暴露的部分绝缘介质层进行第二次缺陷扫描,以获得第二扫描图像,并根据第二扫描图像确定图案化金属层的底部的缺陷位置信息。
5.优选地,图案化金属层的底部缺陷包括底部内切缺陷。
6.优选地,图案化金属层包括若干间隔排布的金属线。
7.优选地,图案化金属层包括图案化al层,图案化al层通过al刻蚀工艺形成。
8.优选地,待检测晶圆包括硅片;和/或,绝缘介质层包括sio2层。
9.优选地,第一次缺陷扫描和第二次缺陷扫描包括明场扫描。
10.优选地,待检测晶圆包括多个芯片单元,多个芯片单元的结构相同。
11.优选地,第一扫描图像包括多个芯片单元的第一图像块,根据第一扫描图像确定图案化金属层的表面的缺陷位置信息的方法包括:设置图案化金属层的表面相应的第一缺陷阈值;将相邻芯片单元的第一图像块进行叠加相消得到对比图像块,根据对比图像块的关键尺寸或面积确定对应芯片单元的缺陷信号值;当芯片单元的缺陷信号值大于第一缺陷阈值时,判定对比图像块对应的位置为缺陷位置,并记录缺陷位置的信息。
12.优选地,第二扫描图像包括多个芯片单元的第二图像块,根据第二扫描图像确定图案化金属层的底部的缺陷位置信息的方法包括:设置图案化金属层的底部相应的第二缺陷阈值;将相邻芯片单元的第二图像块进行叠加相消得到对比图像块,根据对比图像块的关键尺寸或面积确定对应芯片单元的缺陷信号值;当芯片单元的缺陷信号值大于第一缺陷阈值时,判定对比图像块对应的位置为缺陷位置,并记录缺陷位置的信息。
13.优选地,缺陷位置信息包括缺陷在待检测晶圆中的位置坐标信息,以及缺陷在单个芯片单元中的位置坐标信息。
14.与现有技术相比,本发明提供的缺陷检测方法具有以下优点:本发明提供的缺陷检测方法,在对图案化金属层的表面进行常规的第一次缺陷扫描之前或之后,增加对图案化金属层的底部进行第二次缺陷扫描,所述第一次缺陷扫描可对图案化金属层的表面缺陷进行有效检测,所述第二次缺陷扫描可对图案化金属层的底部缺陷进行检测,解决了现有的检测方法中,难以检测到图案化金属层的底部内切缺陷的问题;本发明提供的检测方法,可实现对底部内切缺陷的自动线上检测,相比于现有的通过切片分析和电镜分析检测底部内切缺陷的方法,可提高检测效率,确保晶圆的良率。
附图说明
15.图1所示为顶层金属铝工艺中产生的底部内切缺陷的透射电镜图;图2所示为本发明一实施例提供的缺陷检测方法的步骤流程图;图3所示为一实施例提供的待检测晶圆的结构示意图;图4所示为一实施例提供的缺陷检测方法中的第一次缺陷扫描的示意图;图5所示为一实施例提供的缺陷检测方法中的第一次缺陷扫描得到的第一扫描图像;图6所示为一实施例提供的缺陷检测方法中的第二次缺陷扫描的示意图;图7所示为一实施例提供的缺陷检测方法中的第二次缺陷扫描得到的第二扫描图像;
图8所示为一实施例提供的缺陷检测方法中得到的对比图像块的示意图;其中,附图标记说明如下:图1中,01-底部结构层;02-铝金属线;03-底部内切缺陷;图3~图8中,1-待检测晶圆;11-绝缘介质层;12-图案化金属层;121-第一金属线;122-第二金属线;13-底部内切缺陷;20-反射光;3-明场扫描机台;31-聚光镜;32-反射镜;33-光学探测器;1211-第一金属线的表面图像块;1221-第二金属线的表面图像块;1212-第一金属线的底部图像块;1222-第二金属线的底部图像块;120-对比图像块。
具体实施方式
16.为使本发明的目的、优点和特征更加清楚,以下结合附图对本发明所提供的一种缺陷检测方法作进一步详细说明。需说明的是,附图均采用非常简化的形式且均使用非精准的比例,仅用以方便、明晰地辅助说明本发明实施例的目的。
17.请参阅图2,本发明提供的一种缺陷检测方法,包括以下步骤:步骤s1:提供待检测晶圆,所述待检测晶圆包括绝缘介质层和形成于所述绝缘介质层上的图案化金属层,所述图案化金属层暴露部分所述绝缘介质层;步骤s2:对所述图案化金属层的表面进行第一次缺陷扫描,以获得第一扫描图像,并根据所述第一扫描图像确定所述图案化金属层的表面的缺陷位置信息;步骤s3:对所述图案化金属层暴露的部分所述绝缘介质层进行第二次缺陷扫描,以获得第二扫描图像,并根据所述第二扫描图像确定所述图案化金属层的底部的缺陷位置信息。
18.请参阅图3,执行步骤s1,提供待检测晶圆1,所述待检测晶圆1包括绝缘介质层11和形成于所述绝缘介质层11上的图案化金属层12,所述图案化金属层暴露部分所述绝缘介质层11。
19.在本实施例中,优选地,待检测晶圆1包括硅片,但不限于此,也可以是其他半导体晶圆;所述绝缘介质层11包括sio2层,但不限于此,也可以是其他合适的介质层。
20.在本实施例中,所述图案化金属层12优选为图案化al层,所述图案化al层可通过al刻蚀工艺形成。所述图案化金属层12包括若干间隔排布的金属线,在本实施例中,所述金属线可以包括第一金属线121和第二金属线122,所述第一金属线121和第二金属线122关键尺寸相同,唯一的区别在于所述第二金属线122在底部形成有底部内切缺陷13,所述第一金属线121没有形成底部内切缺陷。可以理解的是,所述图案化金属层12可以包括若干个第一金属线121和若干个第二金属线122,为附图清晰简明,图3中仅示意性地示出了一个第一金属线121和一个第二金属线122。
21.在本实施例中,所述待检测晶圆1包括多个芯片单元(图3中未示出),所述多个芯片单元的结构相同(不包括缺陷结构),每个芯片单元至少包含一个第一金属线121或第二金属线122,还包括部分绝缘介质层11。为方便说明,图3中所示的第一金属线121和第二金属线122分别属于相邻的两个芯片单元,并且对应于相邻的两个芯片单元中的相同位置。
22.请参阅图4和图5,执行步骤s2,对所述图案化金属层12的表面进行第一次缺陷扫描,以获得第一扫描图像,并根据所述第一扫描图像确定所述图案化金属层12的表面的缺陷位置信息。
23.所述第一次缺陷扫描用于捕获所述图案化金属层12表面的缺陷位置。如图4所示为第一次缺陷扫描示意图,所述第一次缺陷扫描优选为明场扫描,所述明场扫描可在明场扫描机台中进行。所述明场扫描机台3至少包括光源(图4中未示出)、聚光镜31、反射镜32以及光学探测器33。在所述第一次缺陷扫描时,所述光源聚焦于所述图案化金属层12的表面,从该表面产生反射光20,所述反射光20经所述聚光镜31会聚后,再经所述反射镜32转向,最终被所述光学探测器33收集并形成所述第一扫描图像。
24.根据所述第一扫描图像确定所述图案化金属层12的表面缺陷的位置信息的方法可参考现有技术,例如,可采用常规的邻近芯片间的对比的方法来确定缺陷位置信息,具体可包括以下步骤:设置所述图案化金属层12的表面相应的第一缺陷阈值;将相邻芯片单元的第一图像块进行叠加相消得到对比图像块,根据所述对比图像块的关键尺寸或面积确定对应芯片单元的缺陷信号值;当芯片单元的缺陷信号值大于所述第一缺陷阈值时,判定所述对比图像块对应的位置为缺陷位置,并记录所述缺陷位置的信息。可依次对每一个芯片单元的第一图像块与相邻的芯片单元的第一图像块进行叠加相消并进行判断,最终可以根据芯片单元的缺陷位置信息获得整个待检测晶圆1上的图案化金属层的表面的缺陷位置信息。所述缺陷位置信息包括缺陷在所述待检测晶圆中的位置坐标信息,以及缺陷在单个芯片单元中的位置坐标信息。
25.请参阅图5,图5所示为本实施例中的第一扫描图像的示意图。在本实施例中,所述待检测晶圆包括多个芯片单元,所述第一扫描图像包括所述多个芯片单元的第一图像块,所述第一图像块至少包括图像块1211或图像块1221。其中,图像块1211和图像块1221分别为第一金属线121和第二金属线122的表面图像块。在本实施例中,所述图像块1211和图像块1221分别属于两个相邻的芯片单元。
26.在本实施例中,所述第一金属线121和第二金属线122的表面均没有缺陷,则所述图像块1211和图像块1221完全相同,图像块1211和图像块1221叠加相消形成的对比图像块不显示缺陷信号。在其他实施例中,所述第一金属线121或第二金属线122表面存在缺陷,所述图像块1211和图像块1221不完全相同,所述图像块1211和图像块1221叠加相消形成的对比图像块会显示缺陷信号。可根据所述对比图像块的关键尺寸或面积确定缺陷信号值,当所述缺陷信号值超过所述第一缺陷阈值时,可将所述第一金属线121或第二金属线122的表面位置确定为缺陷位置。
27.请参阅图6和图7,执行步骤s3,对所述图案化金属层12暴露的部分所述绝缘介质层11进行第二次缺陷扫描,以获得第二扫描图像,并根据所述第二扫描图像确定所述图案化金属层的底部的缺陷位置信息。
28.所述第二次缺陷扫描用于捕获所述图案化金属层12底部的缺陷位置。如图6所示为所述第二次缺陷扫描示意图,所述第二次缺陷扫描优选为明场扫描,所述明场扫描可在明场扫描机台3中进行。所述明场扫描机台3至少包括光源(图6中未示出)、聚光镜31、反射镜32以及光学探测器33。在所述第二次缺陷扫描时,所述光源聚焦于所述图案化金属层12保留的部分所述绝缘介质层11的表面,以此获得所述图案化金属层12的底部图像。从所述绝缘介质层11的表面产生反射光20,所述反射光20经所述聚光镜31会聚后,再经所述反射镜32转向,最终被所述光学探测器33收集并形成所述第二扫描图像。
29.与根据所述第一扫描图像确定所述图案化金属层12的表面缺陷的位置信息同理,根据所述第二扫描图像确定所述图案化金属层12的底部缺陷的位置信息的方法可包括以下步骤:设置所述图案化金属层的底部相应的第二缺陷阈值;将相邻芯片单元的第二图像块进行叠加相消得到对比图像块,根据所述对比图像块的关键尺寸或面积确定对应芯片单元的缺陷信号值;当芯片单元的缺陷信号值大于所述第二缺陷阈值时,判定所述对比图像块对应的位置为缺陷位置,并记录所述缺陷位置的信息。可依次对每一个芯片单元的第二图像块与相邻的芯片单元的第二图像块进行叠加相消并进行判断,最终可以根据芯片单元的缺陷位置的信息获得整个待检测晶圆1上的图案化金属层的底部的缺陷位置信息。所述缺陷位置信息包括缺陷在所述待检测晶圆中的位置坐标信息,以及缺陷在单个芯片单元中的位置坐标信息。
30.在本实施例中,所述第二扫描图像如图7所示,在本实施例中,所述待检测晶圆包括多个芯片单元,所述第二扫描图像包括所述多个芯片单元的第二图像块,所述第二图像块至少包括图像块1212或图像块1222,其中,图像块1212和图像块1222分别为第一金属线121和第二金属线122的底部图像块,在本实施例中,所述图像块1212和图像块1222分别属于两个相邻的芯片单元。
31.在本实施例中,所述第二金属线122存在底部内切缺陷13,所述第一金属线121不存在底部内切缺陷,对应地,所述第二金属线122的底部图像块1222的宽度会小于所述第一金属线121的底部图像块1212的宽度。因此,将图像块1212和图像块1222叠加相消后得到的对比图像块120会显示为如图8中所示的条纹。可根据所述对比图像块的关键尺寸或面积确定缺陷信号值,当所述缺陷信号值超过所述第二缺陷阈值时,可将所述第二金属线122的位置确定为缺陷位置。进一步地,所述对比图像块120的关键尺寸对应所述底部内切缺陷13的关键尺寸,因此,所述第二次缺陷扫描,不仅可以得到对应的缺陷位置信息,还可以通过所述对比图像块120获得所述底部内切缺陷13的关键尺寸信息,可减少后续的复检步骤的工作量。
32.所述第二次缺陷扫描时,光源聚焦于所述绝缘介质层11表面,由于所述绝缘介质层11表面对光的反射率较小,反射光20的强度相比于所述第一次缺陷扫描时的反射光20的强度小,因此,优选地,所述第二次缺陷扫描的光源的强度大于所述第一次缺陷扫描的光源的强度,以提高所述第二次缺陷扫描形成的所述第二扫描图像的质量。
33.需说明的是,上述的步骤s2和步骤s3的顺序可以交换,例如,在另一实施例中,可以先进行所述步骤s3,再进行所述步骤s2。
34.综上所述,本发明提供的缺陷检测方法,在对图案化金属层的表面进行常规的第一次缺陷扫描之前或之后,增加对图案化金属层的底部进行第二次缺陷扫描,所述第一次缺陷扫描可对图案化金属层的表面缺陷进行有效检测,所述第二次缺陷扫描可对图案化金属层的底部缺陷进行检测,解决了现有的检测方法中,难以检测到图案化金属层的底部内切缺陷的问题;本发明提供的检测方法,可实现对底部内切缺陷的自动线上检测,相比于现有的通过切片分析和电镜分析检测底部内切缺陷的方法,可提高检测效率,确保晶圆的良率。
35.此外,可以理解的是,虽然本发明已以较佳实施例披露如上,然而上述实施例并非
用以限定本发明。对于任何熟悉本领域的技术人员而言,在不脱离本发明技术方案范围情况下,都可利用上述揭示的技术内容对本发明技术方案作出许多可能的变动和修饰,或修改为等同变化的等效实施例。因此,凡是未脱离本发明技术方案的内容,依据本发明的技术实质对以上实施例所做的任何简单修改、等同变化及修饰,均仍属于本发明技术方案保护的范围内。而且还应该理解的是,本发明并不限于此处描述的特定的方法、化合物、材料、制造技术、用法和应用,它们可以变化。还应该理解的是,此处描述的术语仅仅用来描述特定实施例,而不是用来限制本发明的范围。必须注意的是,此处的以及所附权利要求中使用的单数形式“一个”、“一种”以及“该”包括复数基准,除非上下文明确表示相反意思。因此,例如,对“一个步骤”引述意味着对一个或多个步骤的引述,并且可能包括次级步骤。应该以最广义的含义来理解使用的所有连词。因此,词语“或”应该被理解为设有逻辑“或”的定义,而不是逻辑“异或”的定义,除非上下文明确表示相反意思。此处描述的结构将被理解为还引述该结构的功能等效物。可被解释为近似的语言应该被那样理解,除非上下文明确表示相反意思。