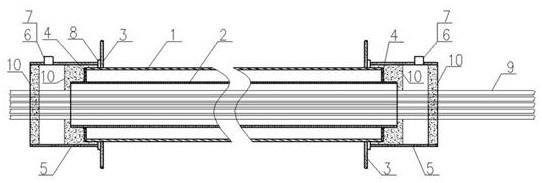
1.本实用新型涉及一种适用于电缆穿越油舱的结构。
背景技术:2.随着船舶自动化要求的提高,设备电缆越来越多,船体空间有限,电缆布置设计越来越困难,尤其是船舶电缆敷设工艺cb/t3908
‑
2007中规定,电缆严禁穿越油舱,电缆距离油舱壁不少于50mm的距离要求和电缆穿管系数不大于0.4等,给船舶电缆布置设计带来了更严峻的挑战。虽然有的公司提出采用多根电缆管穿越油舱的设计方式,但面临穿电缆数量有限或占用油舱空间较大等等问题。
技术实现要素:3.本实用新型其目的就在于提供一种适用于电缆穿越油舱的结构,以解决现有多根电缆管穿越油舱的设计方式存在穿电缆数量有限或占用油舱空间较大的问题。
4.为实现上述目的而采取的技术方案是,一种适用于电缆穿越油舱的结构,包括穿舱套管,所述穿舱套管的两端穿过油舱固定焊接于油舱壁上,穿舱套管的两端位于油舱壁的外侧均设有圆形腹板,圆形腹板分别与油舱壁、穿舱套管之间通过焊接固定,所述穿舱套管的两端还均套装有电缆盒,电缆盒的一端焊接固定在圆形腹板上,电缆盒上还焊接有防火堵料浇注口和透气口,电缆盒的内部两端均设有备用模块,所述穿舱套管内经定位环对中固定有电缆管,电缆管内敷设有成束电缆。
5.进一步,所述定位环有2个,2个定位环分别焊接固定于穿舱套管的两端,电缆管的两端分别穿过定位环,电缆管与2个定位环之间通过焊接固定。
6.进一步,所述电缆盒为管状结构,电缆盒内部两端均设有备用模块,电缆盒与2个备用模块之间形成的空腔的上方焊接固定有防火堵料浇注口和透气口。
7.有益效果
8.与现有技术相比本实用新型具有以下优点。
9.本实用新型的优点是,该结构能够在船体有限的空间内,解决成束电缆穿越油舱敷设的问题,具有制作简单、成本低的特点。
附图说明
10.以下结合附图对本实用新型作进一步详述。
11.图1为本实用新型的结构正视图;
12.图2为本实用新型的结构俯视图;
13.图3为本实用新型的结构侧视图;
14.图4为本实用新型电缆管与穿舱套管的组装图;
15.图5为本实用新型的电缆盒的结构正视图;
16.图6为本实用新型的电缆盒的结构侧视图。
具体实施方式
17.下面结合实施例及附图对本实用新型作进一步描述。
18.一种适用于电缆穿越油舱的结构,包括穿舱套管1,如图1
‑
图6所示,所述穿舱套管1的两端穿过油舱固定焊接于油舱壁3上,穿舱套管1的两端位于油舱壁3的外侧均设有圆形腹板8,圆形腹板8分别与油舱壁3、穿舱套管1之间通过焊接固定,所述穿舱套管1的两端还均套装有电缆盒5,电缆盒5的一端焊接固定在圆形腹板8上,电缆盒5上还焊接有防火堵料浇注口6和透气口7,电缆盒5的内部两端均设有备用模块10,所述穿舱套管1内经定位环4对中固定有电缆管2,电缆管2内敷设有成束电缆9。
19.所述定位环4有2个,2个定位环4分别焊接固定于穿舱套管1的两端,电缆管2的两端分别穿过定位环4,电缆管2与2个定位环4之间通过焊接固定。
20.所述电缆盒5为管状结构,电缆盒5内部两端均设有备用模块10,电缆盒5与2个备用模块10之间形成的空腔的上方焊接固定有防火堵料浇注口6和透气口7。
21.本实用新型中,所述电缆管2的两端经定位环4与穿舱套管1焊接固定,穿舱套管1的两端穿过油舱固定焊接于油舱壁3上,所述穿舱套管1的两端采用圆形腹板8分别与油舱壁3、穿舱套管1焊接固定,穿舱套管1的两端口外围均罩设有电缆盒5,电缆盒5固定焊接于圆形腹板8,所述电缆盒5上固定焊接有防火堵料浇注口6和方便浇注的透气口7,电缆盒5的端口处设有备用模块10;所述电缆管1内敷设成束电缆9。
22.本实用新型在具体实施时,首先是在外场将电缆管2、定位环4与穿舱套管1焊接完成;再将其整体一同调入分段油舱内与油舱壁3焊接固定,并用圆形腹板8加强固定;在穿舱套管1的两端口外围罩设电缆盒5,并与圆形腹板8焊接固定;在准备就绪后,将成束电缆9穿越油舱敷设在电缆管1内,成束电缆9敷设完毕后,再将备用模块10安装在电缆盒5内,再将液体防火堵料从防火堵料浇注口6灌入电缆盒5内即可,操作简单、方便。