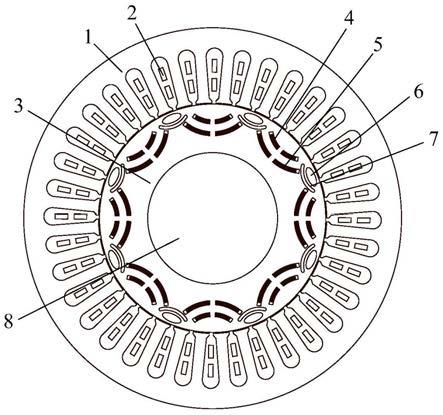
1.本发明涉及一种永磁无刷电机,属于电机制造及控制领域,特指一种适用于电动汽车、航空航天等应用场合需要全工况功率因数最优的永磁无刷电机,涉及一种理想凸极率分布的设计方法。
背景技术:2.近年来,汽车行业正在经历电气化转型,大部分汽车厂商都认为电动汽车将是未来汽车发展的主力军。面对新一代电动汽车对节能、减排的要求,直驱动力系统在混合动力汽车、小型电动汽车、运动型电动汽车等领域的应用前景广阔。同时,随着行驶环境变得不断复杂,存在着“频繁启停、加速、刹车、爬坡、高速巡航”等多个运行工况,对电机及其驱动系统的要求变得越来越苛刻。
3.目前,永磁无刷电机由于高效率、高控制精度、高功率密度等优点,在电动汽车电驱动系统中被广泛应用,但在研究该类电机的过程中,普遍是针对单一工况展开探究,为此,当运行工况改变时,上述的优势能否继续保持有待商榷。
4.中国专利号201510097242.1提出了一种车用宽调速直轴磁场增强型永磁无刷电机,该电机可以实现d轴电感大于q轴电感,并配合分区调磁控制,继承了传统永磁同步功率密度大、运行可靠、效率高的优点,进一步降低铜耗和铁耗,提高了电机效率,并解决了传统永磁同步难以实现弱磁控制的不足。然而,该电机主要针对单一工况进行了性能研究和优化,因而当工况发生变化时,无法保证电机的效率,功率因数也需要提高。
5.中国专利号201510341378.2提出了一种非对称结构和绕组配置的组合式双凸极混合励磁电机,通过合理规划磁路和切向磁化永磁体的放置位置,形成了由永磁部分子电机和混合励磁部分子电机所构成的双凸极混合励磁电机。该电机能实现极宽的恒功率调速区域,同时也具备较高的功率密度,其优良性非常适合应用于电动汽车驱动系统中。然而,持续的电励磁电流产生的铜耗对电机的效率影响较大,也影响了功率因数的大小。
6.由此可见,目前研究的传统驱动电机在满足多工况需求这一方面还需要更深入的研究,如果仅仅考虑额定(单一)工况,将导致电动汽车在实际多工况运行中出现功率因数小、效率低等问题,故难以满足车用驱动电机负载变化所需的多工况要求。因此,解决传统车用电机设计中因仅考虑单一工况而导致的功率因数小、效率低的问题,成为了车用驱动电机领域亟待解决的问题。
技术实现要素:7.本发明提出了一种永磁无刷电机全工况功率因数最优的设计方法,其目的在于解决传统车用电机设计中因仅考虑单一工况而导致的功率因数小、效率低的问题,并提出了一种可控漏磁式广域高效永磁同步电机,该电机属于变漏磁电机的范畴。
8.为了实现上述目的,本发明采用的技术方案是:
9.一种永磁无刷电机全工况功率因数最优的设计方法,包括步骤:当电机处于重载爬坡工况时,为了提高功率因数,电机的电感特性需设计为l
d
>l
q
;当电机处于高速巡航工况时,为了提高功率因数,电机的电感特性需设计为l
d
<l
q
;根据不同工况下的需求,交直轴电感的大小可以做出相应的改变,从而实现了全工况下的电感可逆。
10.一种实现全工况凸极率分布最优式的方法,交直轴电感差值最优,当电机处于重载爬坡工况时,q轴磁阻变大,d轴电感l
d
大于q轴电感l
q
,随着q轴磁阻不断变大,d轴电感l
d
和q轴电感l
q
的差值不断增大,当到达极限值的时候,此时的凸极率ρ=l
q
/l
d
最小且小于1,从而提高了转矩输出能力和功率因数;当电机处于高速巡航工况时,在极间磁桥饱和程度降到最低前,q轴磁阻不断变小,d轴电感l
d
和q轴电感l
q
的差值不断增大,当到达极限值的时候,此时的凸极率ρ=l
q
/l
d
最大且大于1,从而电机高速区的转矩输出能力得到了提高,功率因数也得到了提高。
11.一种电动汽车用全工况功率因数最优的永磁无刷电机,包括定子1,转子3和转轴8,转子3同轴位于定子1内部,转子3中心是转轴8,定子1的定子槽内设有电枢绕组2;定子1内壁和转子3外壁之间具有气隙,转子3的每个极上固定镶嵌有四块弧形的第一铁氧体永磁体4和第二铁氧体永磁体5,这四块永磁体分为内、外两层,每层上有两段,外层靠近气隙,内层靠近转轴8,第一铁氧体永磁体4和第二铁氧体永磁体5分布在转子极中心线的两侧且相对于极中心线对称,在转子每极中心线上有椭圆形磁障6和弧形磁障7;相邻两极的铁氧体永磁体采用交替极的充磁方式,且相邻的永磁体之间有导磁桥10,每段永磁体的圆心都位于转子3的直径上。
12.进一步,转子3内部开有弧形的磁钢槽9,每段第一铁氧体永磁体4和第二铁氧体永磁体5固定镶嵌在一个对应的磁钢槽9中,两段磁钢槽9中间是导磁桥10,导磁桥10位于相邻两极永磁体的中心线上且相对于转子3的中心线对称。
13.进一步,磁钢槽9在靠近弧形磁障7的这一端部留有空隙未镶嵌第一铁氧体永磁体4和第二铁氧体永磁体5,磁钢槽9在相邻两极的端部不留空隙。
14.进一步,外层磁钢槽9未嵌有第一铁氧体永磁体4的这部分沿圆周方向的弧度角为θ2,内层磁钢槽9未嵌有第二铁氧体永磁体5的这部分沿圆周方向的弧度角为θ5;外层的两段永磁体之间的导磁桥10所占的弧度角为θ3,内层的两段永磁体之间的导磁桥5所占的弧度角为θ6;外层的单个第一铁氧体永磁体4对应的弧度角为θ1,内层的单个第二铁氧体永磁体5对应的弧度角为θ4;内、外两层上的永磁体均沿着永磁体的中心线径向充磁,同一极上的四个永磁体的充磁方向相同,相邻两极上的永磁体充磁方向相反。
15.本发明采用上述技术方案后的有益效果是:
16.1.本发明提出了“一种全工况电感可逆法”。当电机处于重载爬坡工况时,此时需要通过施加正向的i
d
,使电机工作在增磁区域,从而来降低不可逆退磁的风险,此工况下为了提高功率因数,电机的电感特性需设计为l
d
>l
q
;当电机处于高速巡航工况时,为了提高电机的效率,可以通过降低损耗来实现,在降低损耗的同时,为了满足弱磁升速阶段的条件,此时需要施加负向的i
d
,此工况下为了提高功率因数,电机的电感特性需设计为l
d
<l
q
。
17.2.本发明提出了“一种全工况功率因数最优式永磁无刷电机”。该电机属于变漏磁电机的范畴,磁障部分被设计为椭圆磁障和弧形磁障的结合,利用磁障的特殊形式,限制了磁通的走向,使得漏磁可控,充分利用了漏磁可控的特性。在重载爬坡工况下,能够实现凸
极率ρ=l
q
/l
d
<1,在高速巡航工况下,能够实现凸极率ρ=l
q
/l
d
>1,不同工况下均能够提高电机的功率因数。
18.3.本发明提出了“一种实现全工况凸极率分布最优式的方法”,即交直轴电感差值最优的设计方法。当电机处于重载爬坡工况时,由于电机的漏磁特性,电枢电流使得漏磁磁路饱和,q轴磁阻变大,d轴电感l
d
大于q轴电感l
q
,δl1=l
d
‑
l
q
也变大,凸极率ρ=l
q
/l
d
<1,从而提高了转矩输出能力和功率因数;当电机处于高速巡航工况时,由于电机的漏磁特性,电枢电流全部转变为d轴去磁电流,由于无q轴电流,极间磁桥饱和程度降到最低,q轴磁阻变小,q轴电感l
q
大于d轴电感l
d
,δl1=l
d
‑
l
q
也变大,凸极率ρ=l
q
/l
d
>1,从而电机高速区的转矩输出能力得到了提高,功率因数也得到了提高。
附图说明
19.图1是本发明涉及的电流极限椭圆和电压极限椭圆图,其中(a)、(b)为低速爬坡工况下的凸极率分布,(a)图中的电流角小于(b)图中的电流角;(c)、(d)为高速巡航工况下的凸极率分布,(c)图中的电流角小于(d)图中的电流角;
20.图2是本发明的全工况功率因数最优式永磁无刷电机;
21.图3是图2中定子结构示意图及三相绕组分布图;
22.图4是图2中转子结构示意图及永磁体充磁示意图;
23.图5是图4中外层永磁体的结构及几何尺寸标注放大示意图;
24.图6是图4中内层永磁体的结构及几何尺寸标注放大示意图;
25.图7是本发明运行在高速轻载下的磁场分布图;
26.图8是本发明运行在额定负载下的磁场分布图。
27.图中:1.定子;2.电枢绕组;3.转子;4.第一铁氧体永磁体;5.第二铁氧体永磁体;6.椭圆形磁障;7.弧形磁障;8.转轴;9.磁钢槽;10.导磁桥。
具体实施方式
28.本发明的一种电动汽车用全工况功率因数最优的永磁无刷电机,包括定子1,转子3和转轴8,转子3同轴位于定子1内部,转子3中心是转轴8,定子1的定子槽内设有电枢绕组2;定子1内壁和转子3外壁之间具有气隙,转子3的每个极上固定镶嵌有四块弧形的第一铁氧体永磁体4和第二铁氧体永磁体5,这四块永磁体分为内、外两层,每层上有两段,外层靠近气隙,内层靠近转轴8,第一铁氧体永磁体4和第二铁氧体永磁体5分布在转子极中心线的两侧且相对于极中心线对称,在转子每极中心线上有椭圆形磁障6和弧形磁障7;相邻两极的铁氧体永磁体采用交替极的充磁方式,且相邻的永磁体之间有导磁桥10,每段永磁体的圆心都位于转子3的直径上。
29.1.为了实现全工况功率因数最优,本发明提供了一种全工况电感可逆法,即:当电机处于重载爬坡工况时,为了提高功率因数,电机的电感特性需设计为l
d
>l
q
;当电机处于高速巡航工况时,为了提高功率因数,电机的电感特性需设计为l
d
<l
q
,具体分析如下:
30.(1)当电动汽车处于低速爬坡工况时,将电机设计为反凸极特性(ρ=l
q
/l
d
<1),此工况下对电机的输出转矩能力要求较高。一般情况下,电机的转矩主要由永磁转矩t
pm
和磁阻转矩t
r
构成,在提高磁阻转矩t
r
的同时存在着不可逆退磁的风险,此时需要通过施加正向
的i
d
,使电机工作在增磁区域,从而来降低不可逆退磁的风险。由电流和电压极限圆(图1(a)、(b))可知,施加正向的i
d
,此时的凸极率ρ=l
q
/l
d
<1。若l
d
不变,l
q
越小(即|ρ
‑
1|越大),则u
lim
/(ωl
q
)越大,γ越大且sin(γ)越大,则功率因数越大。
31.(2)当电动汽车处于高速巡航工况时,将电机设计为正凸极特性(ρ=l
q
/l
d
>1),此工况下对电机的效率要求较高。一般情况下,为了提高电机的效率,可以通过降低损耗(主要是铁耗和铜耗)来实现。在降低损耗的同时,为了满足弱磁升速阶段的条件,此时需要施加负向的i
d
。由电流和电压极限圆(图1(c)、(d))可知,施加反向的i
d
,此时的凸极率ρ=l
q
/l
d
>1。若l
d
不变,l
q
越大(即|ρ
‑
1|越大),则u
lim
/(ωl
q
)越小,γ越大且sin(γ)越大,则功率因数越大。
32.综上所述,在重载爬坡工况时,为了提高功率因数,电机的电感特性需为l
d
>l
q
,即凸极率ρ<1;在高速巡航工况时,为了提高功率因数,电机的电感特性需为l
d
<l
q
,即凸极率ρ>1。因此,不同工况下的凸极率可变有助于功率因数的全面提高。
33.2.本发明提供了一种实现全工况凸极率分布最优式的方法,即交直轴电感差值最优的高转矩永磁无刷电机设计方法。为了进一步提高转矩输出能力和功率因数,在重载爬坡工况和高速巡航工况要需要提高交直轴电感差值δl1和δl2,具体分析如下:
34.(1)当电动汽车处于重载爬坡工况时,随着q轴电流的增大,由于变漏磁电机的漏磁特性,此时的q轴磁通与漏磁通、d轴磁通与主磁通均反向串联,极间磁桥在达到完全饱和之后,漏磁路径被封堵,永磁磁通全部进入定子,形成d轴有效磁通。由于电枢电流使漏磁磁路饱和,因此q轴磁阻变大,d轴电感l
d
大于q轴电感l
q
,δl1=l
d
‑
l
q
也变大,凸极率ρ=l
q
/l
d
<1,从而提高了转矩输出能力和功率因数。
35.(2)当电动汽车处于高速巡航工况时,电机进入弱磁升速的阶段,此时定子电流分量由q轴向d轴转变,q轴电枢磁通减弱,d轴去磁磁通随着d轴电流的增大而逐渐增大,当电枢电流全部转变为d轴去磁电流分量的时候,由于无q轴电流,极间磁桥饱和程度降到最低,q轴磁阻变小,q轴电感l
q
大于d轴电感l
d
,δl1=l
d
‑
l
q
也变大,凸极率ρ=l
q
/l
d
>1,从而电机高速区的转矩输出能力得到了提高,功率因数也得到了提高。
36.参照图1,为涉及的电流极限椭圆和电压极限椭圆图。通过对比图1(a)、(b)可以发现,在重载爬坡工况下,施加正向的i
d
,此时的凸极率ρ=l
q
/l
d
<1。若l
d
不变,l
q
越小(即|ρ
‑
1|越大),则u
lim
/(ωl
q
)越大,γ越大且sin(γ)越大,则功率因数越大。对比图1(c)、(d),在高速巡航工况下,施加反向的i
d
,此时的凸极率ρ=l
q
/l
d
>1。若l
d
不变,l
q
越大(即|ρ
‑
1|越大),则u
lim
/(ωl
q
)越小,γ越大且sin(γ)越大,则功率因数越大。
37.图2为本发明提出的全工况功率因数最优式永磁无刷电机拓扑结构图。具体分析如图3和图4所示。图3和图4为本发明所提出电机的定子结构和转子结构。定子1由定子齿10、定子槽11、定子轭12组成。在定子槽11内安放了双层电枢绕组,其中“+”为电枢绕组的进线方向,
“‑”
为电枢绕组的出线方向。转子3内部的永磁体极对数为4,永磁体的充磁方向沿着永磁体中心线径向方向充磁。
38.图5和图6分别为本发明所提出电机的内、外层永磁体的结构及几何尺寸标注放大示意图。转子3上每极均有四段弧形永磁体组成,这四段永磁体分为内、外层,每层上有两段。外层靠近气隙,内层靠近转轴8。每段永磁体固定镶嵌在一个对应的磁钢槽9中,两段磁
钢槽9中间是导磁桥10,导磁桥10位于相邻两极永磁体的中心线上且相对于转子3的中心线对称。
39.图7和图8分别为本发明运行在高速轻载下和额定负载下的磁场分布图。由图可见,在额定负载工况下,永磁磁通穿过气隙进入定子,此时需要依靠永磁磁链产生输出转矩。在高速轻载工况下,较多的磁通经过漏磁支路进入到相邻的磁体中,剩余的一部分磁通会流入定子齿中,在此工况下,电机的弱磁控制可以通过漏磁可控实现一部分磁通的削弱,从而不需要深度弱磁。在弱磁升速阶段,由于弱磁电流的减小,一方面降低了永磁体不可逆退磁的风险,另一方面减小了损耗,从而在拓宽电机调速范围的同时也提高了电机的运行效率。
40.在本说明书的描述中,参考术语“一个实施例”、“一些实施例”、“示意性实施例”、“示例”、“具体示例”、或“一些示例”等的描述意指结合该实施例或示例描述的具体特征、结构、材料或者特点包含于本发明的至少一个实施例或示例中。在本说明书中,对上述术语的示意性表述不一定指的是相同的实施例或示例。而且,描述的具体特征、结构、材料或者特点可以在任何的一个或多个实施例或示例中以合适的方式结合。
41.尽管已经示出和描述了本发明的实施例,本领域的普通技术人员可以理解:在不脱离本发明的原理和宗旨的情况下可以对这些实施例进行多种变化、修改、替换和变型,本发明的范围由权利要求及其等同物限定。