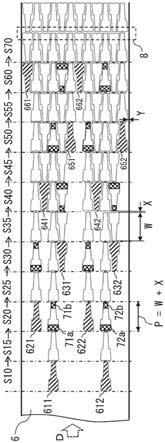
1.本技术涉及用于旋转电机的分割层叠芯体的芯体部件的制造方法和制造装置、以及分割层叠芯体的制造方法。
背景技术:2.在现有的旋转电机用分割层叠芯体的芯体部件的冲裁方法中,在电磁钢板上互不相同地配置作为产品的分割铁心即芯体部件,并在不用于作为产品形状的冲裁的钢板上配置引导销等。由此,提高了钢板在顺流传送方向上的定位精度,实现了产品冲裁尺寸确保以及材料的有效利用。此外,通过引导销来进行冲裁时的钢板的定位。作为这样的旋转电机用分割层叠芯体的芯体部件的冲裁方法,例如有专利文献1。现有技术文献专利文献
3.专利文献1:日本专利特开2016-226140号公报
技术实现要素:发明所要解决的技术问题
4.根据专利文献1所公开的旋转电机的制造装置,作为分割后的定子铁心的芯体部件通过用模具从带状的电磁钢板冲裁而形成。芯体部件的形状由位于旋转电机的外形侧的背磁轭部以及向着内径侧突出的齿部所构成。对于其冲裁时的布局,彼此呈千鸟状地互相改变方向,来进行设为彼此面对的配置。此外,通过在不作为产品形状来使用的钢板上配置引导销等,来提高钢板在顺流传送方向上的定位精度,并实现产品冲裁的尺寸确保以及材料成品率的提高。
5.通常,作为材料的电磁钢板通过引导销来定位,被传送一定量并进行冲裁。然而,在仅基于引导销的定位中,若钢板的刚性不足,则钢板会扭曲或变形,产生无法确保所预期的传送量、材料发生倾斜等问题。特别地,由于引导销仅配置在与材料传送方向正交的方向上的钢板的端部,因此产生如下问题:仅通过引导销来定位无法进行基于冲压的高速传送和高速冲裁。此外,若为了提高材料成品率而使引导销与芯体部件的冲裁部过于接近,则产生芯体部件的模具破损的问题,因此,在确保材料成品率的同时确保冲裁精度成为问题。此外,通过多个冲裁工序冲裁出一个产品形状,对切割连接部进行切割的匹配切割部存在多个,因此存在如下问题:基于引导销的定位尺寸的偏差所造成的影响较大,冲裁尺寸的精度变差。
6.本技术是为了解决上述问题而完成的,其目的在于使得能够从滚轧出的带状的电磁钢板中高精度地冲裁出多个板状芯体部件,并且能在不使材料成品率下降的情况下进行高速冲裁。
用于解决技术问题的技术手段
7.本技术所涉及的制造方法是用于旋转电机的分割层叠芯体的芯体部件的制造方法,其特征在于,包括:第一冲裁工序,该第一冲裁工序中,利用具有带状的电磁钢板的传送装置的冲压机构从所述电磁钢板中直接按产品形状对第一芯体部件进行冲裁;传送工序,该传送工序中,利用所述传送装置来传送所述电磁钢板;以及第二冲裁工序,该第二冲裁工序中,使用所述第一芯体部件的冲裁痕迹形状、并利用具有所述芯体部件的外形的产品形状导正销来进行定位,并且利用所述冲压机构直接按产品形状对第二芯体部件进行冲裁。发明效果
8.本技术的芯体部件的制造方法中,直接按芯体部件的产品形状来进行冲裁,因此能提高产品的尺寸精度。此外,将产品形状的冲裁痕迹用于芯体部件冲裁的定位,因此能进行高速冲裁,而不使材料成品率降低。
附图说明
9.图1是示出使用了实施方式1所涉及的芯体部件和分割层叠芯体的旋转电机的俯视图。图2是示出实施方式1所涉及的芯体部件的俯视图。图3是示出实施方式1所涉及的分割层叠芯体的立体图。图4是说明实施方式1所涉及的芯体部件的制造方法的电磁钢板的俯视图。图5是示出实施方式1所涉及的芯体部件的制造方法的流程图。图6是示出实施方式1所涉及的芯体部件的制造装置的示意图。图7是示出实施方式1所涉及的芯体部件的制造装置的侧视图。图8是示出实施方式1所涉及的芯体部件的制造装置的俯视图。图9a是说明实施方式1所涉及的芯体部件的制造方法的电磁钢板的俯视图。图9b是示出实施方式1所涉及的产品形状导正销的放大图。图10是说明实施方式2所涉及的芯体部件的制造方法的电磁钢板的俯视图。图11是说明实施方式3所涉及的芯体部件的制造方法的电磁钢板的俯视图。图12是说明实施方式4所涉及的芯体部件的制造方法的电磁钢板的俯视图。图13是说明实施方式5所涉及的芯体部件的制造方法的电磁钢板的俯视图。图14是示出实施方式6所涉及的电磁钢板的特性的示意图。图15a是示出实施方式6所涉及的分割层叠芯体的剖视图。图15b是示出实施方式6所涉及的分割层叠芯体的剖视图。
具体实施方式
10.实施方式1.对用于旋转电机的分割层叠芯体的芯体部件的制造方法及其制造装置进行说明。图1是示出使用了实施方式1所涉及的芯体部件和分割层叠芯体的旋转电机的俯视图。图1中,旋转电机100具有包括定子芯体3和转子4的构造,上述定子芯体在框架1的内部呈环状地连接分割层叠芯体2而得到,上述转子4设置在定子芯体3的内部。图1中示出对转子4设置了磁体5的示例,但也可以是不包含磁体的感应电动机的转子。
11.分割层叠芯体2是对芯体部件进行层叠而得到的层叠铁心,上述芯体部件由外径侧的背磁轭部、以及从所述背磁轭部向内径侧突出并形成磁极的齿部所构成,并且从电磁钢板中被冲裁得到。定子芯体3通过在旋转电机100的圆周方向上环状地连接分割层叠芯体2而形成,并通过压入或冷缩配合保持在圆环状的框架1的内周。
12.图2中示出从带状的电磁钢板中冲裁出的芯体部件20,图3中示出分割层叠芯体2的示例,该分割层叠芯体2层叠芯体部件20,通过焊接或粘接、铆接将芯体部件20彼此固定在层叠方向上,并设为块状态。图2和图3中,示出从背磁轭部21向内径方向突出的齿部22的形状。在背磁轭部21的外径侧的中央,设有在层叠时用于将芯体部件20对准的燕尾槽部23。此外,背磁轭部21设有芯体定位凸部24a和芯体定位凹部24b,它们在连结分割层叠芯体2并组合成圆环状时进行定位。齿部22卷绕有线圈,因此,相对于周向形成得较细。由此,芯体部件20具有背磁轭部21较宽、齿部22较窄的扇形状。
13.接着,对芯体部件20的制造方法进行说明。图4用电磁钢板6的俯视图示出了芯体部件的制造方法的概念。此外,在图5的流程图中示出制造工序的流程。具体而言,由图6所示的作为冲压机构的芯体部件的制造装置500来进行。芯体部件的制造装置500由冲压装置300和模具装置400构成。冲压装置300中,由传送装置310将卷绕成圆柱状的带状的电磁钢板6从开卷机(未图示)送出,由模具装置400对电磁钢板6进行冲裁来制造芯体部件20。
14.图4中,作为本实施方式,示出如下事例:将芯体部件20的冲裁工序分为6个,在各工序中的2处、合计12处进行冲裁。在电磁钢板6的顺流传送方向d上,具有第1冲裁工序的步骤s10至第6冲裁工序的步骤s60、废料切割工序的步骤s70、以及在各工序间传送电磁钢板6的电磁钢板传送的步骤s15至s55。
15.用图5的流程图来说明与电磁钢板6的移动相匹配的图4中的冲裁工序的流程。由传送装置310传送入的电磁钢板6在步骤s10的第一冲裁工序中,在由冲裁痕迹611和612的阴影所示的2处作为第一芯体部件20被冲裁。关于冲裁方向,将背磁轭部21设为传送方向d的上游侧,齿部22设为传送侧d的下游侧。冲裁后,电磁钢板6被传送相当于1节距的长度p。1节距的长度p为将作为产品的芯体部件20的传送方向上的产品尺寸w、与作为冲裁痕迹的传送方向上的间隔的边距宽度x进行合计而得的值。接着,在步骤s15中,作为空闲传送,电磁钢板6被进一步传送相当于1节距的长度p。
16.步骤s20中,作为第二冲裁步骤,使用之前在第一冲裁工序中被冲裁后的冲裁痕迹611和612被传送来的冲裁痕迹形状,对冲裁痕迹611使用产品形状导正销71a、71b,对冲裁痕迹612使用产品形状导正销72a、72b来进行定位。在定位后的状态下,由冲裁痕迹621和622的阴影所示的2处作为第二芯体部件20被冲裁。冲裁方向与步骤s10同样地,将背磁轭部21设为传送方向d的上游侧。冲裁后,电磁钢板6被传送相当于1节距的长度p。在步骤s25中,作为空闲传送,电磁钢板6被进一步传送相当于1节距的长度p。
17.之后的工序中,步骤s30、s35、s40、s45和s55重复与步骤s20和步骤s25相同的动作,因此省略详细说明。步骤s30中,由冲裁痕迹631和632的阴影所示的2处作为第三芯体部件20被冲裁。然而,如冲裁痕迹631和632所示那样,芯体部件20的冲裁方向与步骤s10和步骤s20成为相反方向,将背磁轭部21设为朝向发送方向d的下游的方向。步骤s40中,由冲裁痕迹641和642的阴影所示的2处作为第四芯体部件20被冲裁。冲裁方向与步骤s30相同。步骤s50中,由冲裁痕迹651和652的阴影所示的2处作为第五芯体部件20被冲裁。冲裁方向与
步骤s10相同。
18.接着,步骤s60中,由冲裁痕迹661和662的阴影所示的2处作为第六芯体部件20被冲裁。冲裁方向与步骤s10相同。冲裁后,电磁钢板6被传送相当于1节距的长度p。如上所述,在电磁钢板6的宽度方向上,在芯体部件20冲裁后的冲裁痕迹形状排列在彼此不同的方向上的状态下,成为仅宽度方向的边距宽度y剩余而所有都被冲裁的状态。最后的步骤s70中,在废料切割工序中,在切割部8所示的区域中对这些边距部进行废料切割。
19.如上所述,在一系列步骤中,芯体部件20通过模具在第一至第六的各个冲裁工序中被直接冲裁成每2个的产品形状,因此,由冲压机构进行1次冲裁可冲裁出每12个产品。上述工序在作为冲压机构的制造装置500的内部同时并行地进行,因此,电磁钢板6每次被传送1节距就能同时制造每12个芯体部件20。
20.电磁钢板6的传送节距p设为产品尺寸w+边距宽度x,通过平行地配置或彼此不同地配置多个芯体部件20,从而实现了材料的有效利用。此外,芯体部件20的冲裁中,设为通过一次冲裁来构成产品形状的总冲裁,剪切加工方向一致,无需匹配切割,因此,能提高产品冲裁尺寸精度。此外,能使模具结构简化,具有产品尺寸的精度提高以及模具费用降低等生产性提高的效果。另外,各冲裁工序中,也能构成为对2处以上的多处进行冲裁,能进一步实现生产性的提高。
21.接着,使用图7来说明芯体部件20的制造装置500。图7示出使用了冲压装置300(包含未图示的开卷机)和模具装置400的芯体部件的制造装置500的侧视图。模具装置400通过引导柱320被冲压装置300所支承。此外,模具装置400包含进行第一冲裁工序的步骤s10的第一冲裁部410、以及进行第二冲裁工序的步骤s20的第二冲裁部420。此外,具备进行第三冲裁工序的步骤s30的第三冲裁部430至进行第六冲裁工序的步骤s60的第六冲裁部460的各冲裁部。此外,具备最终在废料切割工序的步骤s70中进行废料切割的废料切割部470。
22.在冲裁芯体部件20的第一冲裁部410至第六冲裁部460中,分别设有冲模401a和凹模401b,在各工序中被冲裁出的芯体部件20被排出到芯体部件排出部330。此外,第二冲裁部420至第六冲裁部460中,配置有冲裁时用于定位的产品形状导正销402。冲裁芯体部件20的模具401具有作为上模的冲模401a、以及作为下模的凹模401b,它们分别配置在构成各冲裁部的冲裁区域的2处。此外,模具装置400具备用于将冲裁出的芯体部件20从模具401剥离的剥料板404。这里,产品形状导正销402、实际上如图4所示在第二冲裁部420中使用的产品形状导正销与芯体部件20的冲裁痕迹621、622的背磁轭部和所述齿部各自的冲裁痕迹形状相对应地分割为4个来配置。此外,在第三冲裁部430至第六冲裁部460中,产品形状导正销也同样地各配置有4个。之后,在作为模具装置400的部件来处理时统称为产品形状导正销402,在用于在电磁钢板6上进行定位的情况下,作为产品形状导正销71a、71b、72a、72b并用单独的标号来表示。
23.接着,对图7所涉及的制造装置500的移动进行说明。首先,通过传送装置310以顺流方式将带状的电磁钢板6传送到模具装置400内。第一冲裁部410中,进行用第一模具401(冲模401a、凹模401b)对第一芯体部件20进行冲裁的第一冲裁工序的步骤s10。由此,形成冲裁痕迹611、612。第二冲裁部420中,使用配置在之前冲裁出的冲裁痕迹的产品形状导正销402来进行定位,并进行用第二模具401(冲模401a、凹模401b)来冲裁第二芯体部件20的第二冲裁工序的步骤s20。第三冲裁部430至第六冲裁部460中,通过与第二冲裁部420相同
的动作,基于产品形状导正销402的定位以及基于模具401的冲裁作为第三冲裁工序的步骤s30至第六冲裁工序的步骤s60来进行。此外,废料切割部470中,进行对到第六冲裁工序的步骤s60为止被冲裁出的电磁钢板6的废料进行切割的废料切割工序的步骤s70。
24.本实施方式中,配置模具401,以使得在第一冲裁部410至第六冲裁部460中同时对各2处进行冲裁,因此,通过冲压装置300的一次冲裁动作同时在12处生成芯体部件20。此外,本实施方式中,采用将芯体部件20的各冲裁部的冲裁个数设为2个、将冲裁部的数量设为6个的结构,但通过将之前工序中冲裁出的芯体部件20的冲裁痕迹用于定位,从而能构成为即使在增加了冲裁个数和冲裁部的数量的情况下也能进行同样的动作。
25.此外,通过使用产品形状导正销402,从而能使冲裁载荷均等化,模具401的倾斜被抑制,冲模401a与凹模401b之间的间隙变得稳定,因此冲裁精度得以提高。此外,由于在传送时不产生相当于定位间隙的偏移,因此具有产品形状的精度得以提高的效果。此外,被冲裁的冲裁形状、以及模具401的结构在各冲裁部中相同,因此冲压载荷不容易产生偏差。特别地,在使用0.3mm以下的薄板材的情况下,间隙的允许尺寸变窄(板厚的6%,0.018mm),因此上述那样的冲压载荷的均等化是有效的。具有可进行基于模具的稳定的冲裁、以及产品形状的精度得以提高的效果。
26.图8中,示出了制造装置500的俯视图。由模具装置400的第一冲裁部410至第六冲裁部460冲裁出的芯体部件20按各个冲裁部被层叠并被排出到芯体部件排出部330。所排出的芯体部件20由带式传送机等传送装置来收集。
27.在图4和图9a所示的带状的电磁钢板6上,配置有多个芯体部件20的冲裁痕迹,由冲模401a、凹模401b冲裁的区域采用如下配置:至少1处以上被配置在与传送方向d正交的方向上的产品形状导正销71a、71b、72a、72b所夹住。在第二冲裁工序的步骤s20中被冲裁的第二芯体部件20的冲裁痕迹622设置在范围spa之间,该范围spa被基于第一芯体部件20的冲裁痕迹611的产品形状导正销71a、71b、与基于冲裁痕迹612的产品形状导正销72a、72b所夹住。其结果是,能使顺流传送时的电磁钢板6的边距宽度x稳定化,具有冲裁的高速化变得稳定的效果。
28.在图9a中,说明对电磁钢板6进行定位的产品形状导正销402的详细内容和结构。对芯体部件20进行冲裁而得的冲裁痕迹并不是圆孔形状,因此,仅通过一般的引导销无法进行定位。因此,本实施方式中,在产品形状的冲裁区域内,将与产品形状的一部分为相同形状的产品形状导正销402分割地配置于各个背磁轭部21、齿部22,并在冲裁痕迹611中使用产品形状导正销71a、71b来进行定位。图9b中,示出配置于该冲裁痕迹611的产品形状导正销71a、71b的放大图。冲裁痕迹611是通过芯体部件20的冲模401a和凹模401b被冲裁成产品形状而得到的,其切口具有作为剪切加工面的性质。剪切加工面直接保持冲模401a的外形形状和尺寸,能利用该剪切面来高精度地进行定位。如图9b所示,产品形状导正销71a使用剪切加工面71aa、71ab、71ac这3面来进行定位。此外,产品形状导正销71b使用剪切加工面71ba、71bb、71bc这3面来进行定位。对于冲裁痕迹612,也使用产品形状导正销72a、72b同样地进行定位。由此,能使用冲裁痕迹形状的4处。若使用冲裁痕迹的剪切加工面的3面以上,则能进行电磁钢板6的定位,因此,本实施方式中,能进行使用了3面
×
4处的合计12面的剪切加工面的定位,能更高精度地进行定位。
29.此外,通过将背磁轭部21的外径侧的燕尾槽部23作为背磁轭部21侧的产品形状导正销71a、72a的形状来利用,从而具有使钢板的定位精度提高的效果。由此,能降低边距宽度x,并能进行冲压高速冲裁。此外,产品形状导正销402的形状能与产品形状相匹配地来构成,因此,也能构成为所需最小限度的形状、尺寸,产品形状导正销402设计时的自由度也得以提高。此外,通过利用芯体部件20的产品冲裁区域并利用产品形状,从而无需引导销等导正销孔的冲裁工序,无需传送边距以外的废料。此外,具有如下效果:能削减模具部件数量并抑制模具尺寸。其结果是,能通过确保产品冲裁尺寸精度、基于冲压的高速冲裁以及线圈材料宽度的大幅缩小来提高材料成品率。
30.如上所述,实施方式1所涉及的芯体部件的制造方法进行如下步骤:利用具有带状的电磁钢板6的传送装置310的冲压机构即制造装置500从电磁钢板6中直接按产品形状对第一芯体部件20进行冲裁的第一冲裁工序的步骤s10;利用传送装置310来传送电磁钢板6的传送工序;以及利用与芯体部件20的外形相匹配的产品形状导正销402、并使用第一芯体部件20的冲裁痕迹形状来进行定位,并且利用冲压机构即制造装置500直接按产品形状对第二芯体部件20进行冲裁的第二冲裁工序的步骤s20。
31.根据这样的芯体部件20的制造方法,可直接按芯体部件20的产品形状来进行冲裁,因此能提高产品的尺寸精度。此外,将产品形状的冲裁痕迹用于芯体部件20的冲裁的定位,因此,无需产品以外的多余的废料和模具,能进行高速冲裁,而不使材料成品率降低。
32.实施方式2.实施方式2是实施方式1的一部分变形例,对其变更点进行说明。图10示出实施方式2所涉及的电磁钢板6的俯视图。实施方式1中,仅通过产品形状导正销71a、71b、72a、72b来进行传送方向的定位,但在本实施方式中,对组合引导销71c而得的结构进行说明。在周向上分割的芯体部件中,设有在周向和径向上进行圆环排列时使用的凹凸部即芯体定位凸部24a以及芯体定位凹部24b的情况较多。因此,作为确保定位精度、并使模具装置简化的手段,对芯体部件的冲裁区域的芯体定位凹部24b配置引导销71c,通过将产品形状导正销72a、72b与引导销71c相组合来对第二芯体部件20进行冲裁,能够使用于电磁钢板6的定位。
33.由此,能使模具装置400的构成方法增加,模具布局的自由度得以增加。此外,越是之后工序的冲裁工序,电磁钢板6仅为边距宽度x,刚性越是下降,因此,通过将引导销71c与产品形状导正销72a、72b相组合,从而能确保电磁钢板6的定位精度、并使模具装置400简化。此外,通过使模具结构简化,从而能进行高速冲裁。
34.此外,该情况下,在第二冲裁工序的步骤s20中冲裁出的第二芯体部件20的冲裁痕迹622设置在范围spb之间,该范围spb被基于第一芯体部件20的冲裁痕迹612的产品形状导正销72a、72b、与基于冲裁痕迹611的芯体定位凹部24b的引导销71c所夹住,该情况对于冲裁的稳定化是有效的。此外,引导销71c在传送方向上具有与产品形状导正销72a之间的传送方向d上的位置间隔spc、以及与产品形状导正销72b之间的传送方向d上的位置间隔spd,能在3处进行稳定的定位。
35.实施方式3.实施方式3是实施方式1的其它一部分变形例,对其变更点进行说明。图11示出实施方式3所涉及的电磁钢板6的俯视图。本实施方式中,与最初的冲裁工序即第一冲裁工序的步骤s10同时,在与钢板传送方向d正交的方向、且在两端的2处冲裁引导销用的引导孔
613、614。钢板的两端设为不作为产品来使用的无效区域,因此能配置引导孔,而不使材料成品率降低。此外,图11中,两端以外的导正销通过与实施方式1相同的产品形状导正销402来构成。此外,两端引导销71d、72d的中心轴配置在与产品形状导正销71a、72a的中心轴、以及产品形状导正销71b、72b的中心位置分别在传送方向d上偏移了位置间隔spe和spf的位置。其结果是,除了实施方式1中的产品形状导正销71a、71b、72a、72b的定位,还能利用基于本实施方式的两端引导销71d、72d的定位。因此,定位精度进一步提高,能使边距宽度x稳定。由此,能提高冲裁精度,能进行基于高速冲压的冲裁。
36.实施方式4.实施方式4是将实施方式2与实施方式3相组合而得到的。图12示出实施方式4所涉及的电磁钢板6的俯视图。本实施方式中,使用了引导销71c、引导销71d和引导销72d,引导销71c利用了产品形状导正销402与产品形状的径向定位部即芯体定位凹部24b,引导销71d和引导销72d设置在电磁钢板6的两端。此时,电磁钢板6的两端的引导销71d、72d的中心轴配置在与利用了芯体定位凹部24b的引导销71c在传送方向d上偏离了位置间隔spg的位置。其结果是,除了实施方式2所涉及的将产品形状导正销72a、72b与引导销71c相组合的定位,还能利用基于实施方式3所涉及的两端引导销71d、72d的定位。因此,即使在带状电磁钢板的材料宽度增加了的情况下,也能进一步提高线圈材料的定位精度,并使边距宽度稳定。其结果是,能抑制冲裁时的偏移和振动,能实现高精度的冲裁尺寸。此外,能实现基于冲压的超高速化,生产性得以提高。
37.实施方式5.实施方式5是实施方式1的其它一部分变形例,对其变更点进行说明。图13示出本实施方式所涉及的电磁钢板6的俯视图。图13的电磁钢板6上,芯体部件20的冲裁方向与实施方式1不同。即,芯体部件20的冲裁痕迹611a、612a、621a、622a的方向成为背磁轭部21或齿部22在与电磁钢板6的传送方向d正交的方向上相对的排列。此外,产品形状导正销73a、73b、74a、74b也配置在与冲裁痕迹形状相匹配的位置。图13中,在电磁钢板6的传送方向上,芯体部件的冲裁痕迹形状以彼此不同的方式排列成4列。冲裁工序变为步骤s10a、s20a、s30a、s40a这4个,根据芯体部件20的形状,能缩小电磁钢板6的传送节距pa。若将图4与图9的情况进行比较,则可知即使边距宽度xa设为与边距宽度x相同,也能使节距pa变得比节距p小得多。此外,在扩大电磁钢板6的宽度并配置了比4列更多的多列芯体部件20的情况下,也能采用同样的制造方法。
38.本实施方式中,顺流传送方向的节距pa变小,因此模具全长能减小,能进一步实现高速的冲压冲裁。此外,通过模具装置400的小型化,也具有能减小冲压装置300和制造装置500的尺寸的效果。此外,若采用仅产品形状导正销73a、73b、74a、74b的结构,则与实施方式1相同而无需引导销,能提高材料成品率。
39.实施方式6.实施方式6示出层叠芯体部件20而得的分割层叠芯体的制造方法。图14是用于说明作为电磁钢板6的特性的板厚偏差的示意图。如图14所示,与电磁钢板6的传送方向d正交的宽度方向的截面cc具有中央部的厚度稍厚的半圆柱状的形状。图中夸张地表示,因此实际上为数十微米以内的差。图14所示的示例中,芯体部件20排列成与电磁钢板6的传送方向d的方向正交的6列而被冲裁。因此,在每列中芯体部件20的厚度出现差异。例如,将从电磁
钢板6的端部冲裁出的芯体部件设为20a、将在中央的列被冲裁出的芯体部件设为20b。
40.如图15a所示,仅收集相同的芯体部件20a而层叠出的分割层叠芯体2的厚度的偏差被放大相当于芯体部件20a的层叠块数。因此,分割层叠芯体2的整体的尺寸在与仅层叠其它部位、例如芯体部件20b而得的分割层叠芯体之间出现差异。此外,产生在层叠阶段分割层叠芯体发生倾斜的问题。
41.为了解决上述问题,本实施方式所示的分割层叠芯体2中,用冲裁列来管理冲裁出的芯体部件20的部位,在层叠芯体部件20的阶段,将多个列组合来层叠,由此来减小误差。图15b示出该示例。图15b中,通过将板厚较薄的芯体部件20a与板厚较厚的芯体部件20b相组合,从而能减少层叠后的板厚偏差影响。
42.此外,若关注图4所示的冲裁位置,则在第一冲裁工序到第六冲裁工序中将各工序中的芯体部件20的冲裁痕迹在各2处相组合,以减小电磁钢板6的板厚偏差。因此,通过按冲裁工序来管理和组合在各工序中被冲裁出的芯体部件排出部330,从而能减少板厚偏差影响,并减小尺寸误差。
43.如上所述,按每个列来管理从电磁钢板6在排列在传送方向d上的多个列上冲裁出的芯体部件20,并利用使电磁钢板6的宽度方向的板厚偏差所引起的尺寸误差减少的组合来层叠2个以上的不同列的芯体部件20。由此,分割层叠芯体2能减小层叠后的板厚偏差的影响,并能减小尺寸误差。此外,由此能确保呈圆环状组装分割层叠芯体2时的定子芯体3的尺寸精度,因此生产性得以提高。
44.另外,实施方式1至5中,示出仅对芯体部件20进行冲裁的工序的制造方法,但可以将在层叠间进行固定的铆接形成部配置在冲裁工序的前后。此外,上述所说明的各实施方式中,说明了应用于定子芯体3用的芯体部件20的示例,然而,例如,在转子4侧卷绕有线圈的旋转电机100中,也能应用于构成该转子4的具有背磁轭部和齿部的分割层叠芯体及其制造方法、以及制造装置。
45.本技术记载了各种例示的实施方式和实施例,但一个或多个实施方式中记载的各种特征、形态及功能并不限于特定实施方式的应用,可单独或以各种组合来应用于实施方式。因此,可以认为未例示的无数变形例也包含在本技术说明书所公开的技术范围内。例如,假设包括对至少1个构成要素进行变形、添加或省略的情况,以及提取至少1个构成要素并与其它实施方式的构成要素进行组合的情况。标号说明
46.1 框架2 分割层叠芯体20、20a、20b 芯体部件21 背磁轭部22 齿部23 燕尾槽部3 定子芯体4 转子5 磁体6 电磁钢板
611、611a、612、612a、621、621a、622、622a、631、632、641、642、651、652、661、662 冲裁痕迹613、614 引导孔71a、71b、72a、72b、73a、73b、74a、74b 产品形状导正销71c、71d、72d 引导销71aa、71ab、71ac、71ba、71bb、71bc 剪切加工面8 切割部100 旋转电机300 冲压装置310 传送装置320 引导柱330 芯体部件排出部400 模具装置401 模具401a 冲模401b 凹模402 产品形状导正销404 剥料板410 第一冲裁部420 第二冲裁部430 第三冲裁部440 第四冲裁部450 第五冲裁部460 第六冲裁部470 废料切割部500 制造装置(冲压机构)。