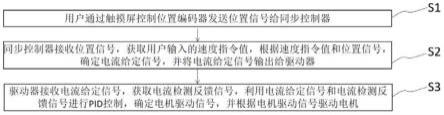
1.本发明属于驱动器控制技术领域,特别是涉及一种多驱动器联动的同步控制方法。
背景技术:2.同步控制是工业控制中常见的控制方式,在工程运用中,通常需要采用几台电机同时驱动,要求几台电机速度同步才能保证传动链的正常运行,否则就会产生链条堆积或断裂,使系统不能很好的运行。在多个电机/多个软起动器的情况下,在起动时通常会发生一台电动机(和软起动器)会比其他电动机(和软起动器)承担更多的负载,严重时会只有其中部分电动机转动,其余电动机不转动的,结果导致电动机跳闸或皮带被拉断。这是因为即使出自同一厂家相同型号的电机,其机械电气性能也不可能完全相同。何况当电动机和软起动器处于不同位置时,变化的电源压降和电源阻抗导致每台设备有不同的电压。当两台电机承担的负载不同时转差亦不相同,负载重的电机转速较低、负载轻的电机转速较高。如果采用两个独立的速度闭环控制系统对两电机同步驱动,控制相对复杂,难以完全保证良好的同步。如果个别电机因为转速比其它都快,电机的负载将会比正常负载大,定子电流急升,增加电机发热量,严重时会烧坏电机。在大功率场合由于外界扰动比较大、不稳定因素多,各电机的稳定性和同步精度很难保证。如果各个电机之间存在一定的速度差,系统的相关应力会成倍增加。严重时可能导致系统的毁坏。由于各电机的性能和工况存在微弱差异,加之它们的工作状态又相互影响,它们之间必然会产生细微的转速差。微弱的转速差产生的拖动不同步,可能会使系统结构应力成倍增加。严重是会毁坏系统。为了解决这个问题,常规做法一般选用高性能的可编程序同步控制器(plc),但这种多台电动机同步拖动运行的设备采用变频器拖动异步电动机加可编程序同步控制器(plc)的控制模式,常出现被动跟随电动机忽快忽慢的现象。同时要在实际生产过程中,根据负荷状况的不同,精确设定变频器加、减速时间,如此用户操作、参数设定很不方便。而且存在操作复杂、成本偏高,以及结构复杂,故障机会多的缺点。
3.目前,市面上常见的步进电机驱动器一般都是单轴驱动器。传统的电机驱动器是一台电机对应一张驱动电路板,这样在需要对多台电机进行独立控制的场合就需要多张驱动电路板,进一步的,在系统架构时就需要对每张驱动电路板设计相应的相位定序表、高频控制线路及复杂的编程对接接口才能实现多个电机的驱动,而在一些对电机驱动器的重量和体积要求特别严格应用场合,比如:中小型无人机的电动起落架收放、输送机的传动控制、舵机系统等。如果采用传统的多个驱动电路板方案,则会增加整个系统的体积和重量,而无法满足这类系统的需求,一种更为轻便灵活且能够集成多电机驱动的控制器亟待被发明。
技术实现要素:4.本发明的目的在于提供一种多驱动器联动的同步控制方法,通过多个电机编码器
的值读到plc的高速计数器hsc1、hsc2,以其中一电机作为主电机,其余电机做从电机,再通过plc程序将从电机的速度给定值做动态调整,使之与主电机速度同步,解决了现有的驱动器同步控制成本高、体积大的问题。
5.为解决上述技术问题,本发明是通过以下技术方案实现的:
6.本发明为一种多驱动器联动的同步控制方法,包括如下步骤:
7.步骤s1:用户通过触摸屏控制位置编码器发送位置信号给同步控制器;
8.步骤s2:同步控制器接收位置信号,获取用户输入的速度指令值,根据速度指令值和位置信号,确定电流给定信号,并将电流给定信号输出给驱动器;
9.步骤s3:驱动器接收电流给定信号,获取电流检测反馈信号,利用电流给定信号和电流检测反馈信号进行pid控制,确定电机驱动信号,并根据电机驱动信号驱动电机。
10.作为一种优选的技术方案,所述多电机同步控制系统包括可编程序同步控制器、定轴轮系和分别与定轴轮系的输入轴机械连接的至少两个电机;所述定轴轮系的输出轴上设置有电机编码器;所述电机编码器与可编程序同步控制器plc之间还连接有变频器。
11.作为一种优选的技术方案,所述可编程序同步控制器包括电源转换电路板、cpu电路板和驱动电路板;所述电源转换电路板、cpu电路板和驱动电路板通道之间通过连接线相连组成闭环驱动电路;
12.其中,驱动电路板上集成了三个相同且相互独立的驱动模块,三个驱动模块组成三路无刷直流电机的驱动电路;所述cpu电路板至少集成了模拟量采集模块、电机控制接口模块、电平转换模块、cpld模块、dsp模块和rs422通信模块;所述驱动电路板根据输入的信号和细分参数的设置产生电机的控制信号,所述模拟量采集模块通过电机控制接口模块采集驱动电路板的电机位置、电流、转速信息,cpld模块对各类输入/输出离散量进行逻辑变换处理,dsp模块与cpld接口获取/发送逻辑信号、解析处理rs422通信模块中的rs422通信数据,输出控制信息到驱动电路板,对电机控制电路进行动作控制,控制电机按照预定参数运转,完成同时控制或单独控制多路直流电机的转向和转速。
13.作为一种优选的技术方案,所述cpu电路板包括顺次串联的硬件触摸屏、dsp模块、cpld模块、电平转换模块、电机控制接口模块和模拟量采集模块,以及通过dsp模块连接的rs422通信模块。
14.作为一种优选的技术方案,所述dsp模块将采集电机的各相电流作为自动限流、过流保护的依据,同时通过数字信号处理器dsp片内模数转换器adc采集电源电压,检测电源转换电路板的电源电压;利用数字信号处理器dsp芯片内256k*16位flash作为程序存储器,该存储器驻存有工作软件。
15.作为一种优选的技术方案,所述模拟量采集模块检测电机电流并实现自动限流,以及对电源电压的监测,通过采用线性电流传感器acs712的电检测电路进行电流检测,检测每个电机母线电流、三相中两相的电流,线性电流传感器acs712经过由集成运算放大器组成的信号调理电路再送给中央处理器cpu进行处理。
16.作为一种优选的技术方案,所述步骤s2中,速度指令值和位置信号,确定电流给定信号,包括:
17.所述同步控制器对所述速度指令值和所述速度反馈值做差,得到第一差值,并利用pid算法对所述第一差值进行控制计算,得到所述电流给定信号。
18.作为一种优选的技术方案,所述步骤s3中,利用电流给定信号和电流检测反馈信号进行pid控制,确定电机驱动信号,包括:
19.所述驱动器对所述电流给定信号和所述电流检测反馈信号做差,得到第二差值,并利用pid算法对所述第二差值进行控制计算,得到所述电机驱动信号。
20.作为一种优选的技术方案,所述步骤s3中,电机驱动信号驱动电机的流程如下:
21.步骤d1:主速度给定信息输入d/a转换模块进行转换;
22.步骤d2:转换后的信息输入变频器1,变频器1控制电机1进行转动;
23.步骤d3:plc对电机1编码器的计数值设置;
24.步骤d4:电机1对用电器进行做功;
25.步骤d5:电流给定信号和电流检测反馈信号进行pid控制,确定电机驱动信号;
26.步骤d6:电机驱动信号经过d/a转换模块转换输入至变频器2;
27.步骤d7:变频器2控制电机2进行转动:
28.步骤d8:plc对电机2编码器的计数值设置;
29.步骤d9:电机2对用电器进行做功。
30.本发明具有以下有益效果:
31.本发明通过多个电机编码器的值读到plc的高速计数器hsc1、hsc2,以其中一电机作为主电机,其余电机做从电机,再通过plc程序将从电机的速度给定值做动态调整,使之与主电机速度同步,工作参数设置方便、结构和操作简单,减少了生产成本和占地面积。
32.当然,实施本发明的任一产品并不一定需要同时达到以上所述的所有优点。
附图说明
33.为了更清楚地说明本发明实施例的技术方案,下面将对实施例描述所需要使用的附图作简单地介绍,显而易见地,下面描述中的附图仅仅是本发明的一些实施例,对于本领域普通技术人员来讲,在不付出创造性劳动的前提下,还可以根据这些附图获得其他的附图。
34.图1为本发明的一种多驱动器联动的同步控制方法流程图;
35.图2为多电机同步控制系统的结构示意图;
36.图3为多电机同步控制系统的控制原理图。
具体实施方式
37.下面将结合本发明实施例中的附图,对本发明实施例中的技术方案进行清楚、完整地描述,显然,所描述的实施例仅仅是本发明一部分实施例,而不是全部的实施例。基于本发明中的实施例,本领域普通技术人员在没有作出创造性劳动前提下所获得的所有其它实施例,都属于本发明保护的范围。
38.请参阅图1所示,本发明为一种多驱动器联动的同步控制方法,包括如下步骤:
39.步骤s1:用户通过触摸屏控制位置编码器发送位置信号给同步控制器;
40.步骤s2:同步控制器接收位置信号,获取用户输入的速度指令值,根据速度指令值和位置信号,确定电流给定信号,并将电流给定信号输出给驱动器;
41.步骤s3:驱动器接收电流给定信号,获取电流检测反馈信号,利用电流给定信号和
电流检测反馈信号进行pid控制,确定电机驱动信号,并根据电机驱动信号驱动电机。
42.请参阅图2所示,多电机同步控制系统包括可编程序同步控制器、定轴轮系和分别与定轴轮系的输入轴机械连接的至少两个电机;定轴轮系的输出轴上设置有电机编码器;电机编码器与可编程序同步控制器plc之间还连接有变频器。
43.可编程序同步控制器包括电源转换电路板、cpu电路板和驱动电路板;电源转换电路板、cpu电路板和驱动电路板通道之间通过连接线相连组成闭环驱动电路;
44.其中,驱动电路板上集成了三个相同且相互独立的驱动模块,三个驱动模块组成三路无刷直流电机的驱动电路;cpu电路板至少集成了模拟量采集模块、电机控制接口模块、电平转换模块、cpld模块、dsp模块和rs422通信模块;驱动电路板根据输入的信号和细分参数的设置产生电机的控制信号,模拟量采集模块通过电机控制接口模块采集驱动电路板的电机位置、电流、转速信息,cpld模块对各类输入/输出离散量进行逻辑变换处理,dsp模块与cpld接口获取/发送逻辑信号、解析处理rs422通信模块中的rs422通信数据,输出控制信息到驱动电路板,对电机控制电路进行动作控制,控制电机按照预定参数运转,完成同时控制或单独控制多路直流电机的转向和转速。
45.cpu电路板包括顺次串联的硬件触摸屏、dsp模块、cpld模块、电平转换模块、电机控制接口模块和模拟量采集模块,以及通过dsp模块连接的rs422通信模块。
46.dsp模块将采集电机的各相电流作为自动限流、过流保护的依据,同时通过数字信号处理器dsp片内模数转换器adc采集电源电压,检测电源转换电路板的电源电压;利用数字信号处理器dsp芯片内256k*16位flash作为程序存储器,该存储器驻存有工作软件。
47.模拟量采集模块检测电机电流并实现自动限流,以及对电源电压的监测,通过采用线性电流传感器acs712的电检测电路进行电流检测,检测每个电机母线电流、三相中两相的电流,线性电流传感器acs712经过由集成运算放大器组成的信号调理电路再送给中央处理器cpu进行处理。
48.步骤s2中,速度指令值和位置信号,确定电流给定信号,包括:
49.同步控制器对速度指令值和速度反馈值做差,得到第一差值,并利用pid算法对第一差值进行控制计算,得到电流给定信号。
50.步骤s3中,利用电流给定信号和电流检测反馈信号进行pid控制,确定电机驱动信号,包括:
51.驱动器对电流给定信号和电流检测反馈信号做差,得到第二差值,并利用pid算法对第二差值进行控制计算,得到电机驱动信号。
52.请参阅图3所示,步骤s3中,电机驱动信号驱动电机的流程如下:
53.步骤d1:主速度给定信息输入d/a转换模块进行转换;
54.步骤d2:转换后的信息输入变频器1,变频器1控制电机1进行转动;
55.步骤d3:plc对电机1编码器的计数值设置;
56.步骤d4:电机1对用电器进行做功;
57.步骤d5:电流给定信号和电流检测反馈信号进行pid控制,确定电机驱动信号;
58.步骤d6:电机驱动信号经过d/a转换模块转换输入至变频器2;
59.步骤d7:变频器2控制电机2进行转动:
60.步骤d8:plc对电机2编码器的计数值设置;
61.步骤d9:电机2对用电器进行做功。
62.值得注意的是,上述系统实施例中,所包括的各个单元只是按照功能逻辑进行划分的,但并不局限于上述的划分,只要能够实现相应的功能即可;另外,各功能单元的具体名称也只是为了便于相互区分,并不用于限制本发明的保护范围。
63.另外,本领域普通技术人员可以理解实现上述各实施例方法中的全部或部分步骤是可以通过程序来指令相关的硬件来完成,相应的程序可以存储于一计算机可读取存储介质中。
64.以上公开的本发明优选实施例只是用于帮助阐述本发明。优选实施例并没有详尽叙述所有的细节,也不限制该发明仅为所述的具体实施方式。显然,根据本说明书的内容,可作很多的修改和变化。本说明书选取并具体描述这些实施例,是为了更好地解释本发明的原理和实际应用,从而使所属技术领域技术人员能很好地理解和利用本发明。本发明仅受权利要求书及其全部范围和等效物的限制。