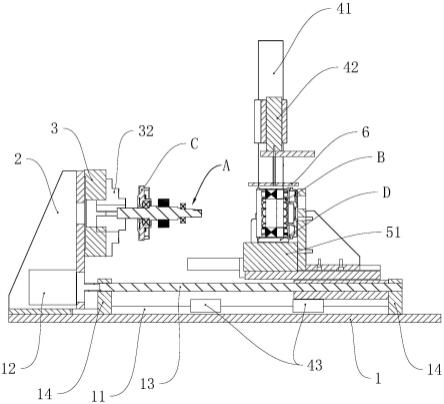
1.本实用新型属于装配设备领域,特别涉及一种改进的定转子安装设备。
背景技术:2.通常水泵采用异步电动机驱动,异步电动机虽然结构简单,但定转子不同步,功率因数低,效率也不高。稀土永磁同步电动机具有结构简单、体积小、重量轻,运行可靠、效率高、功率因数高等显著优点,逐步代替异步电动机。磁同步电动机转子内置永磁体(钕铁硼),装有磁钢的转子吸附力极强,定子、转子之间气隙较小,无法通过手工装配总装。若装配时定转子不同心极易造成定子线圈端部及轴承的损坏,装配后经常发生电机异响。传统装配工艺已无法满足要求,无法保证装配质量。
3.针对以上装配难点,必须采用专用设备工装来进行装配,将定转子分别固定在设备两侧的工装上,用设备精度保证定子、转子同心度。通常定子装配在电机的机筒中,转子上穿设电机的端盖,定转子装配完毕后通过螺栓将端盖和机筒定位,完成装配。现有定转子安装设备具有立式和卧式两种,在立式设备中,定子和转子立式安装,即定子和转子在竖直面内装配,但机筒端部往往不平整,其作为装配基准面时无法满足定位要求,不可靠;此外,由于立式设备对端盖有遮挡,无法直接在立式设备上打紧连接螺栓,需要将定转子装配完毕的机筒拿下来打螺栓,这样操作繁琐,效率低。而卧式设备可以很好地适应不同形状的电机外壳,但现有卧式设备采用与定转子同轴设置的顶针,使用时该顶针穿过定子并抵在转子端部,目前电机使用的转子轴径28~38mm,其端面中心孔较小,采用顶针的方案定位不准确,还容易打滑,不能保证精准度,且整个装配设备呈长条状,整体布局不够紧凑,使用不方便。
技术实现要素:4.针对现有电机排布不紧凑、使用不便技术的问题,本实用新型提供一种改进的定转子安装设备,省去顶针设计,其结构精简,各部件排布紧凑。
5.本实用新型采用技术方案如下:一种改进的定转子安装设备,包括水平设置的工作台,以及设置在工作台上的:
6.转子工装位,包括设置在所述工作台上的底座和竖置在所述底座上的卡盘,所述卡盘夹持待装配的转子,使得待装配的转子保持水平;
7.定子工装位,设置在一可沿所述转子轴向移动的滑移座上,所述定子工装位包括限位座和可移动地设置在限位座上方的压板,所述限位座用于承载内置待装配定子的机筒;
8.所述限位座使得待装配的定子与待装配的转子的中心线保持等高,并将所述机筒的底面、侧面和远离转子的端面抵住,所述压板能够压在机筒的顶面,使得所述机筒定位在所述定子工装位上。
9.本技术中,定子工装位通过滑移座实现移动,限位座将机筒的底面、侧面和端面抵
住,压板将机筒的顶面压住,使得定子在水平向和竖直向均定位,以抵抗定转子之间的磁吸力,有效防止机筒(定子)移位,限位座能使待装配的定子与待装配的转子的中心线保持等高,装配时定子和转子能够始终保持同心,保证定转子精准装配;省去现有技术的顶针设计,避免设备长度过长,以精简结构、简化装配设备。
10.进一步地,所述限位座上设有带凹槽的支撑块,所述机筒下部嵌设在所述凹槽中。凹槽尺寸与机筒下部的尺寸适配,机筒的侧面和底面被凹槽内壁抵住,不同高度、宽度的机筒采用与其适配的支撑块,限位座能使机筒中心线与定子中心线始终保持在同一高度上,保证精准装配。
11.进一步地,所述限位座还包括一设有让位口的挡块,所述挡块位于所述支撑块一侧,并远离所述定子,以抵住机筒远离转子的端面,所述让位口为所述转子让位,挡块能防止机筒在装配过程中受到磁力而从定子工装位上推出,让位口的底部与转子底部高度相当或稍低,以便转子经过定子后继续前行,方便装配。
12.进一步地,所述支撑块上还设有两限位挡边,所述凹槽位于两限位挡边之间,两限位挡边可拆卸式连接在所述限位座顶部。不同尺寸的机筒可以通过更换不同规格的支撑块来实现,限位挡边处于限位座的顶部,更换支撑块时无其他结构干涉,方便支撑块快速拆装更换。
13.进一步地,所述支撑块和所述压板采用塑料件。现有限位定子的部件通常采用金属件,而金属材质较硬、不易变形,这就需要装配时保持绝对同心,否则会由于匹配度稍差而压坏轴承或定子,因此增加了装配难度;塑料材质较金属弹性好、质软,支撑块和压板采用塑料件能够利用其自身弹性将机筒夹紧,保证定位效果,通过调整压板的下压力能够实现竖直面内位置的微调,为定转子装配提供微调空间,以降低装配难度,有效缩减装配时间。
14.进一步地,所述支撑块的底部连接一延伸台,所述延伸台与所述支撑块垂直,所述限位座上设有装配槽,所述支撑块和所述延伸台嵌设在所述装配槽内。延伸台与支撑块垂直设置,能够直观地观察支撑块是否安装到位,并且延伸台能够分担支撑块承受的压力,增强支撑块的承压能力。
15.进一步地,所述滑移座上设有一立柱,一支架夹持在所述立柱上,所述支架上设有一气缸,所述气缸的下部连接所述压板,以便所述压板升降且能施加下压力。夹持在立柱上的支架能够沿立柱转动,有利于快速调整压板的位置。
16.进一步地,所述卡盘上设有三个径向且等角设置的滑槽,每个滑槽内滑动设置一个液压夹头,以便在所述卡盘的中心处夹持所述转子,使得转子均匀受力。
17.进一步地,所述工作台上设有与所述转子平行的导轨,所述滑移座通过滑块与所述导轨相连,所述滑移座与一被电机驱动的丝杆联动,所述丝杆与所述导轨平行设置。
18.进一步地,所述丝杆的两端均套设限位件,所述限位件位于所述工作台上,以使丝杆转动平稳。
19.本实用新型具有的有益效果:本技术中,定子工装位通过滑移座实现移动,限位座将定子的底面、侧面和端面抵住,压板将定子的顶面压住,使得定子在水平向和竖直向均定位,以抵抗定转子之间的磁吸力,有效防止定子移位,限位座能使待装配的定子与待装配的转子的中心线保持等高,保证定转子精准装配;省去现有技术的顶针设计,避免设备长度过
长,以精简结构、简化装配设备。
附图说明
20.图1为改进的定转子安装设备的侧向结构示意图;
21.图2为图1中a-a向的结构示意图;
22.图3为限位座的结构示意图;
23.图4为卡盘的结构示意图;
24.图中:1-工作台;11-导轨;12-电机;13-丝杆;14-限位件;2-底座;3-卡盘;31-滑槽;32-液压夹头;4-滑移座;41-立柱;42-支架;43-滑块;5-限位座;51-支撑块;52-凹槽;53-挡块;54-让位口;55-限位挡边;56-延伸台;6-压板;7-气缸;a-转子;b-定子;c端盖;d-机筒。
具体实施方式
25.下面结合本实用新型的附图,对本实用新型实施例的技术方案进行解释和说明,但下述实施例仅为本实用新型的优选实施例,并非全部。基于实施方式中的实施例,本领域技术人员在没有做出创造性劳动的前提下所获得其他实施例,都属于本实用新型的保护范围。
26.本实施例的改进的定转子安装设备,如图1、图2所示,包括水平设置的工作台1,以及设置在工作台1上的:
27.转子工装位,包括设置在所述工作台1上的底座2和竖置在所述底座2上的卡盘3,所述卡盘3夹持待装配的转子a,使得待装配的转子a保持水平;
28.定子工装位,设置在一可沿所述转子a轴向移动的滑移座4上,所述定子工装位包括限位座5和可移动地设置在限位座5上方的压板6,所述限位座5用于承载内置待装配定子b的机筒d;
29.所述限位座5使得待装配的定子b与待装配的转子a的中心线保持等高,并将所述机筒d的底面、侧面和远离转子a的端面抵住,所述压板6能够压在机筒d的顶面,使得所述机筒定位在所述定子工装位上。本实施例中转子上套设轴承,当机筒与转子装配完毕后,轴承位于所述机筒内。
30.本技术中,定子工装位通过滑移座4实现移动,限位座5将机筒的底面、侧面和端面抵住,压板6将机筒的顶面压住,使得定子在水平向和竖直向均定位,以抵抗定转子之间的磁吸力,有效防止机筒(定子)移位,限位座5能使待装配的定子与待装配的转子a的中心线保持等高,装配时定子和转子a能够始终保持同心,保证定转子a精准装配;省去现有技术的顶针设计,避免设备长度过长,以精简结构、简化装配设备。
31.所述限位座5上设有带凹槽52的支撑块51,所述机筒d下部嵌设在所述凹槽52中。凹槽52尺寸与机筒d下部的尺寸适配,机筒d的侧面和底面被凹槽52内壁抵住,不同高度、宽度的机筒d采用与其适配的支撑块51,限位座5能使机筒d中心线与定子中心线始终保持在同一高度上,保证精准装配。
32.如图3所示,所述限位座5还包括设有让位口54的挡块53,所述挡块53位于所述支撑块51一侧,并远离所述定子,以抵住机筒d远离转子a的端面,所述让位口54为所述转子a
让位,挡块53能防止机筒d在装配过程中受到磁力而从定子工装位上推出,让位口54的底部与转子a底部高度相当或稍低,以便转子a经过定子后继续前行,方便装配。
33.所述支撑块51上还设有两限位挡边55,所述凹槽52位于两限位挡边55之间,两限位挡边55可拆卸式连接在所述限位座5顶部。不同尺寸的机筒d可以通过更换不同规格的支撑块51来实现,限位挡边55处于限位座5的顶部,更换支撑块51时无其他结构干涉,方便支撑块51快速拆装更换。
34.所述支撑块51和所述压板6采用塑料件。现有限位定子的部件通常采用金属件,而金属材质较硬、不易变形,这就需要装配时保持绝对同心,否则会由于匹配度稍差而压坏轴承或定子,因此增加了装配难度;塑料材质较金属弹性好、质软,支撑块51和压板6采用塑料件能够利用其自身弹性将机筒d夹紧,保证定位效果,通过调整压板6的下压力能够实现竖直面内位置的微调,为定转子a装配提供微调空间,以降低装配难度,有效缩减装配时间。
35.所述支撑块51的底部连接一延伸台56,所述延伸台56与所述支撑块51垂直,所述限位座5上设有装配槽,所述支撑块51和所述延伸台56嵌设在所述装配槽内。延伸台56与支撑块51垂直设置,能够直观地观察支撑块51是否安装到位,并且延伸台56能够分担支撑块51承受的压力,增强支撑块51的承压能力。
36.所述滑移座4上设有立柱41,支架42夹持在所述立柱41上,所述支架42上设有气缸7,所述气缸7的下部连接所述压板6,以便所述压板6升降且能施加下压力。夹持在立柱41上的支架42能够沿立柱41转动,有利于快速调整压板6的位置。
37.如图4所示,所述卡盘3上设有三个径向且等角设置的滑槽31,每个滑槽31内滑动设置一个液压夹头32,以便在所述卡盘3的中心处夹持所述转子a,使得转子a均匀受力。
38.所述工作台1上设有与所述转子a平行的导轨11,所述滑移座4通过滑块43与所述导轨11相连,所述滑移座4与被电机12驱动的丝杆13联动,所述丝杆13与所述导轨11平行设置。本实施例中电机12设置在底座2,这一方式使得整个设备,布局合理
39.所述丝杆13的两端均套设限位件14,所述限位件14位于所述工作台1上,以使丝杆13转动平稳。
40.装配时,将装好前端盖c的转子a轴伸端装夹在液压卡盘3上,前端盖c靠近卡盘3;将装好后端盖c的定子放在定子工装上定位,后端盖c靠紧挡块53,驱动压板6下压定子顶面;驱动滑移座4,使得滑移座4带动定子工装位缓慢靠近转子a工装位,直至待装配的定子穿设在待装配的转子a中,径向调整前端盖c,采用螺栓插入前端盖c安装孔内,再将定子止口压入前端盖c止口内,转子a右侧轴承进入后端盖c轴承室内;打紧连接螺栓,将端盖c、机筒d连接紧固,完成装配;移开压板6、松弛卡盘3,移动滑移座4,将装配好的工件取下。现有手工装配方式装配一台电机12大致80s,本技术的设备装配一台电机需要40s左右,且装配好的电机无异响,合格率较高,提高生产效率并保证装配质量,提高产品市场竞争力。
41.以上所述,仅为本实用新型的具体实施方式,但本实用新型的保护范围并不局限于此,熟悉该领域的技术人员应该明白本实用新型包括但不限于附图和上面具体实施方式中描述的内容。任何不偏离本实用新型的功能和结构原理的修改都将包括在权利要求的范围中。