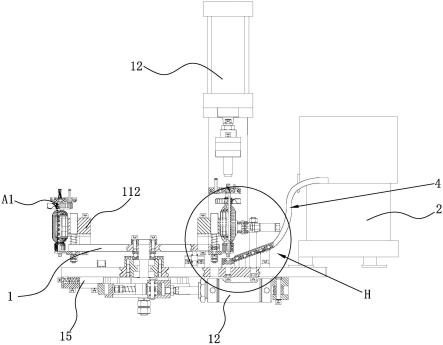
1.本实用新型涉及电动工具装配技术领域,特别是涉及一种转子压装轴承装置。
背景技术:2.电机的轴承压装质量直接影响电机的装配质量和使用寿命。传统的电机组装生产线上,依靠人工进行压装,不仅消耗大量的人力,而且压装效率非常低。由于电机转子的轴承在压装过程中对轴承的装配精度要求很高,因此依靠人工进行压装极易出现偏差而损坏轴承,从而导致电机转子压装轴承的成本增加;现有的转子压装轴承工装在安装使用时存在一定的弊端,传统的压装工艺效率低、操作繁琐、精度较低以及压装时高度问题,产生的易损坏转轴和压装效果不理想的问题,给人们的使用过程带来了一定的不利影响;并且一次只能实现一个轴承的压装,效率低下,不适用于生产线使用。
3.针对以上问题提出一种转子压装轴承装置,解决上述问题。
技术实现要素:4.本实用新型的目的在于提供一种转子压装轴承装置,利用气缸带动棘轮盘和回转机构转动,解决电机高速转动时易产生误差的问题,增加压装精度,替代人工压装并增加压装效率。
5.为解决此技术问题,本实用新型的技术方案是: 一种转子压装轴承装置,包括设置有压紧端和下料端的回转压紧机构、震动送料盘和设置于回转压紧机构下料端的下料搬运机构;所述回转压紧机构包括回转工作台组件、驱动组件和压装气缸;所述驱动组件包括与回转工作台组件同轴键连接的棘轮盘、带动棘轮盘转动的棘轮气缸和防止棘轮盘回退的定位棘爪件;所述棘轮气缸的一端与所述棘轮盘铰接,所述定位棘爪件与棘轮盘卡接,所述棘轮气缸伸出或缩回驱动棘轮盘转动;所述震动送料盘通过输送轨将轴承送至所述压装气缸的正下方,所述回转工作台装夹转子的中心轴与所述压装气缸的活塞杆呈同一直线。
6.进一步改进,还包括设置于回转压紧机构的压紧端一侧的转子防倾组件,包括防倾气缸和与防倾气缸的活塞杆固定连接的推板,推板内设置有第一弹性件;防倾气缸与压装气缸均与气泵相连接,当转子运动至压紧端时,防倾气缸推出将转子向工作台一侧压紧,而后压装气缸推出,将转子向下推动,将轴承压紧进中心轴中,形成自动装配,增加装配精度。
7.进一步改进,所述回转工作台组件包括工作台主体和以工作台主体为圆心环形阵列分布的转子支架;所述转子支架与所述工作台主体固定连接;设置有多个转子支架能够进行连续装配轴承,与现有技术中一次只能压装一个转子与轴承相比,大大提升了装配效率。
8.进一步改进,所述转子支架包括安装件、一端与安装件固定连接的滑柱和与滑柱滑动连接的托板,所述安装件与托板之间设置有第二弹性件,所述第二弹性件套设于所述滑柱上;利用安装件与托板之间第二弹性件,能够时转子支架放置不同型号长度的转子,不
需要进行拆卸更换相应型号的支架,增加适用性,并提升了装配效率,减少使用者的工作量;并在转子压装好轴承后,利用第二弹性件复位产生的力,带动压装好的转子回到原先高度,使其在跟随回转工作台组件转动时,不会触碰到其他零件。
9.进一步改进,所述安装件内设置有磁性件,所述安装件远离工作台主体一侧呈v型;确保转子在工作台转动时不会倾倒,使其能够跟随回转工作台组件转动。
10.进一步改进,所述下料搬运机构包括下料抓手和输送机;所述下料抓手与所述输送机设置于所述回转压紧机构的下料端;下料抓手与气泵相连接,下料抓手抓夹压装完成的转子,将其放置在输送机上进行下料,形成半自动化装配,加快装配效率。
11.进一步改进,所述下料抓手的夹持部设置为弧形;便于抓夹转子,时期能够更加稳固的装夹转子。
12.进一步改进,所述棘轮盘的外圈设有若干均匀分布的棘齿,所述定位棘爪件伸出插设于棘轮盘的齿槽内;利用棘轮气缸替代电机进行驱动,解决了电机在高速转动状态下停止时易产生误差的问题,并由于棘轮上均匀等距分布的棘齿与棘轮气缸相配合,使其转动距离能够控制的更加精准;使用定位棘爪件插设于棘轮盘的齿槽内,使棘轮盘只能向一个方向旋转,而不能倒转,防止回退。
13.进一步改进,所述定位棘爪件包括安装部、插接于安装部内的卡接部和设置于安装部与卡接部之间的第三弹性件;在棘轮气缸带动棘轮转动时,卡接部压缩第三弹性件,缩进安装部内,使棘轮盘完成转动;转动后,第三弹性件复位件卡接部顶升至棘轮盘的齿槽内,防止棘轮盘以及同轴连接的回转工作台组件回退。
14.通过采用上述技术方案,本实用新型的有益效果是:利用气缸与棘轮盘的配合带动回转机构转动,替代了现有技术中的电机驱动,解决电机高速转动易产生误差,不好控制转动角度的问题;设置震动送料件,使轴承能够自动输送至压装气缸与转子的正下方,替代人工防止轴承,增加装配的精确度;并在下料端设置下料搬运机构,将压装好轴承的转子自动搬运至输送机上,使其能够自动流入装配流水线中进行后续装配操作,加快装配效率,增加企业自动化程度。
15.从而实现本实用新型的上述目的。
附图说明
16.图1是本实用新型的示意图;
17.图2是本实用新型的示意图;
18.图3是本实用新型的示意图;
19.图4是本实用新型的示意图;
20.图5是本实用图1中h向的局部放大图。
21.图中:
22.回转压紧机构1;震动送料盘2;下料搬运机构3;回转工作台组件11;压装气缸12;棘轮盘13;棘轮气缸14;定位棘爪件15;输送轨4;转子防倾组件5;防倾气缸51;推板52;第一弹性件53;工作台主体111;转子支架112;安装件1121;滑柱1122;托板1123;第二弹性件1124;下料抓手31;输送机32;安装部151;卡接部152;第三弹性件153;转子a1;轴承a2。
具体实施方式
23.为了进一步解释本实用新型的技术方案,下面通过具体实施例来对本实用新型进行详细阐述。
24.本实施例公开一种转子压装轴承装置,如图1至图5所示: 包括设置有压紧端和下料端的回转压紧机构1、震动送料盘2和设置于回转压紧机构1下料端的下料搬运机构3;所述回转压紧机构1包括回转工作台组件11、驱动组件和压装气缸12;所述驱动组件包括与回转工作台组件11同轴键连接的棘轮盘13、带动棘轮盘13转动的棘轮气缸14和防止棘轮盘13回退的定位棘爪件15;所述棘轮气缸14的一端与所述棘轮盘13铰接,所述定位棘爪件15与棘轮盘13卡接,所述棘轮气缸14伸出或缩回驱动棘轮盘13转动;所述震动送料盘2通过输送轨4将轴承a2送至所述压装气缸12的正下方,所述回转工作台装夹转子a1的中心轴与所述压装气缸12的活塞杆呈同一直线。
25.本实施例中还包括设置于回转压紧机构1的压紧端一侧的转子防倾组件5,包括防倾气缸51和与防倾气缸51的活塞杆固定连接的推板52,推板52内设置有第一弹性件53;防倾气缸51与压装气缸12均与气泵相连接,当转子a1运动至压紧端时,防倾气缸51推出将转子a1向工作台一侧压紧,而后压装气缸12推出,将转子a1向下推动,将转子a1压紧进轴承a2中,形成自动装配,增加装配精度。
26.本实施例中所述回转工作台组件11包括工作台主体111和以工作台主体111为圆心环形阵列分布的转子支架112;所述转子支架112与所述工作台主体111固定连接;设置有多个转子支架112能够进行连续装配轴承a2,与现有技术中一次只能压装一个转子a1与轴承a2相比,大大提升了装配效率。
27.本实施例中所述转子支架112包括安装件1121、一端与安装件1121固定连接的滑柱1122和与滑柱1122滑动连接的托板1123,所述安装件1121与托板1123之间设置有第二弹性件1124,所述第二弹性件1124套设于所述滑柱1122上;利用安装件1121与托板1123之间第二弹性件1124,能够时转子支架112放置不同型号长度的转子a1,不需要进行拆卸更换相应型号的支架,增加适用性,并提升了装配效率,减少使用者的工作量;并在转子a1压装好轴承a2后,利用第二弹性件1124复位产生的力,带动压装好的转子a1回到原先高度,使其在跟随回转工作台组件11转动时,不会触碰到其他零件。
28.本实施例中所述安装件1121内设置有磁性件,所述安装件1121远离工作台主体111一侧呈v型;确保转子a1在工作台转动时不会倾倒,使其能够跟随回转工作台组件11转动。
29.本实施例中所述下料搬运机构3包括下料抓手31和输送机32;所述下料抓手31与所述输送机32设置于所述回转压紧机构1的下料端;下料抓手31与气泵相连接,下料抓手31抓夹压装完成的转子a1,将其放置在输送机32上进行下料,形成半自动化装配,加快装配效率。
30.本实施例中所述下料抓手31的夹持部设置为弧形;便于抓夹转子a1,时期能够更加稳固的装夹转子a1。
31.本实施例中所述棘轮盘13的外圈设有若干均匀分布的棘齿,所述定位棘爪件15伸出插设于棘轮盘13的齿槽内;利用棘轮气缸14替代电机进行驱动,解决了电机在高速转动状态下停止时易产生误差的问题,并由于棘轮上均匀等距分布的棘齿与棘轮气缸14相配
合,使其转动距离能够控制的更加精准;使用定位棘爪件15插设于棘轮盘13的齿槽内,使棘轮盘13只能向一个方向旋转,而不能倒转,防止回退。
32.本实施例中所述定位棘爪件15包括安装部151、插接于安装部151内的卡接部152和设置于安装部151与卡接部152之间的第三弹性件153;在棘轮气缸14带动棘轮转动时,卡接部152压缩第三弹性件153,缩进安装部151内,使棘轮盘13完成转动;转动后,第三弹性件153复位件卡接部152顶升至棘轮盘13的齿槽内,防止棘轮盘13以及同轴连接的回转工作台组件11回退。
33.本实用新型的具体工作过程:
34.使用时,操作者需把轴承a2放置进震动送料盘2中,将转子a1装夹在转子支架112的安装件1121与托板1123上,由于转子支架112上设置有磁性件,将转子a1吸附在安装件1121上,防止转子a1在移动过程中倾倒,并利用滑柱1122与托板1123的滑动连接,使转子支架112能够防止不同型号不同长度的转子a1,增加适用性,不需要进行拆卸更换相应型号的支架,增加适用性,并提升了装配效率,减少使用者的工作量;
35.准备完成后,启动本装置,驱动组件中的棘轮气缸14缩回,带动棘轮盘13与回转工作台组件11转动,定位棘爪件15上的卡接部152伸出插设于棘轮盘13的齿槽内,使棘轮盘13只能向一个方向旋转,而不能倒转,防止回退;将以工作台主体111为圆心环形阵列分布的转子支架112上装夹的转子a1转动至压紧端,震动送料盘2震动,将其内部的轴承a2通过输送轨4送至回压紧端,此时转子防倾组件5中的防倾气缸51顶出,将转子a1压在转子支架112上,而后压装气缸12推出,将转子a1向下推动,转子a1与托板1123同时向下运动,第二弹性件1124拉伸,直至轴承a2压紧进转子a1的中心轴中,完成压装,压装气缸12缩回,第二弹性件1124复位带动压装好的转子a1回到原先高度,防倾气缸51缩回,完成一次压装;
36.重复上述步骤,直至压装好的转子a1到达下料端,即下料搬运机构3所在位置,下料抓手31抓夹压装完成的转子a1,将其放置在输送机32上进行下料,形成半自动化装配,替代人工下料,加快装配效率。
37.上述实施例和图式并非限定本实用新型的产品形态和式样,任何所属技术领域的普通技术人员对其所做的适当变化或修饰,皆应视为不脱离本实用新型的专利范畴。