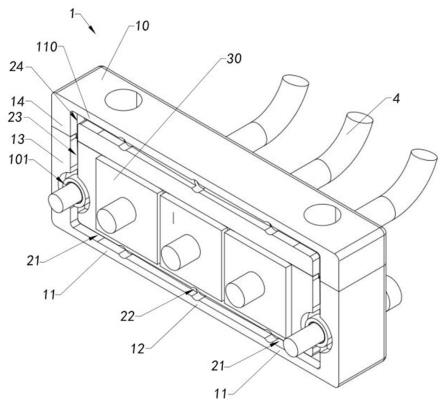
1.本技术涉及结构安装领域,更为具体地涉及安装结构。
背景技术:2.在实际产业中,通常将多个结构装配在一起来实现特定功能。例如,将电缆框架安装于机柜表面来实现电缆与机柜的内部部件(例如,断路器)之间的连接。
3.在一些应用场景中,待装配的两个结构的表面需紧密贴合,以实现密封安装。然而,如果两个结构需要贴合的两个面(即,安装面)中至少一个安装面不平整,两个结构则难以实现紧密贴合,进而难以达到预期的密封效果。
4.具体地,成型工艺、特定的功能需求等原因均可能导致结构形成不平整的安装面。例如,一些需要热成型的结构在成型过程中会产生一定程度的变形,这种变形将导致结构在热成型后形成凹凸不平的安装面,影响其与其他结构之间的安装密封性(即,该结构安装于其他结构后该结构与其他结构之间的密封性)。仍以电缆框架与机柜的配合安装为例,通过热成型工艺加工成型形成的电缆框架的与所述机柜的安装面贴合的面(即,所述电缆框架的安装面)将存在一定程度的变形,影响其与所述机柜的安装密封性。再例如,一些结构需要满足形成不平整表面以增大表面积这一特定功能需求,这与其需形成平整安装面来提高与其他结构之间的安装密封性相矛盾。
5.因此,需要一种适用于安装面不平整的结构的密封安装方案,以改善待装配结构之间的安装密封性。
技术实现要素:6.本技术的一个优势在于提供了一种安装结构,其中,所述安装结构提供了一种适用于安装面不平整的结构的密封安装方案,以改善待装配结构之间的安装密封性。
7.本技术的另一个优势在于提供了一种安装结构,其中,所述安装结构以不同深度的凹槽作为补偿结构来补偿所述安装结构的安装面的各个部分和待与之装配的结构的安装面之间的间隙尺寸差距,这样,所述安装结构在原本结构的基础上经过较为简单的改造(即,设置凹槽)即可改善所述安装结构和待与之装配的结构之间的安装密封性。
8.为了实现上述至少一优势或其他优势和目的,根据本技术的一个方面,提供了一种安装结构,其包括:结构主体;和形成于所述结构主体的至少二凹槽,至少二所述凹槽适于将位于所述安装结构和待装配结构的安装面之间的密封件嵌合其中;其中,至少二所述凹槽的深度不同。
9.在根据本技术所述的安装结构中,至少二所述凹槽第一凹槽和第二凹槽,所述第一凹槽的深度大于所述第二凹槽的深度。
10.在根据本技术所述的安装结构中,所述第二凹槽从所述第一凹槽一体地延伸。
11.在根据本技术所述的安装结构中,所述结构主体包括第一主体部分和第二主体部分,所述第一凹槽形成于所述第一主体部分,所述第二凹槽形成于所述第二主体部分,所述
第二主体部分相对于所述第一主体部分凹陷。
12.在根据本技术所述的安装结构中,所述第二主体部分在第一预设方向上位于所述结构主体的中部,所述第一主体部分在所述第一预设方向上位于所述第二主体部分的外侧。
13.在根据本技术所述的安装结构中,至少二所述凹槽包括第三凹槽和第四凹槽,所述第三凹槽的深度大于所述第四凹槽的深度。
14.在根据本技术所述的安装结构中,所述结构主体包括第三主体部分和第四主体部分,所述第三凹槽形成于所述第三主体部分,所述第四凹槽形成于所述第四主体部分,所述第四主体部分相对于所述第三主体部分凹陷。
15.在根据本技术所述的安装结构中,第四凹槽从所述第三凹槽一体地延伸。
16.在根据本技术所述的安装结构中,所述结构主体具有至少一孔结构,所述第三凹槽在第二预设方向上与所述孔结构的距离小于所述第四凹槽在所述第二预设方向上与所述孔结构的距离。
17.在根据本技术所述的安装结构中,所述安装结构包括设置于所述结构主体的至少一电缆安装模块。
18.通过对随后的描述和附图的理解,本技术进一步的目的和优势将得以充分体现。
19.本技术的这些和其它目的、特点和优势,通过下述的详细说明,附图和权利要求得以充分体现。
附图说明
20.从下面结合附图对本技术实施例的详细描述中,本技术的这些和/或其它方面和优点将变得更加清楚并更容易理解,其中:
21.图1图示了根据本技术实施例的安装结构与其他结构的装配示意图。
22.图2图示了根据本技术实施例的安装结构与待装配结构的另一装配示意图。
23.图3图示了根据本技术实施例的安装结构的立体示意图。
24.图4图示了根据本技术实施例的安装结构的平面示意图。
25.图5图示了根据本技术实施例的安装结构的截面示意图。
26.图6图示了根据本技术实施例的安装结构的另一截面示意图。
27.图7图示了根据本技术实施例的安装结构的截面放大示意图。
具体实施方式
28.以下说明书和权利要求中使用的术语和词不限于字面的含义,而是仅由发明人使用以使得能够清楚和一致地理解本技术。因此,对本领域技术人员很明显仅为了说明的目的而不是为了如所附权利要求和它们的等效物所定义的限制本技术的目的而提供本技术的各种实施例的以下描述。
29.可以理解的是,术语“一”应理解为“至少一”或“一个或多个”,即在一个实施例中,一个元件的数量可以为一个,而在另外的实施例中,该元件的数量可以为多个,术语“一”不能理解为对数量的限制。
30.虽然比如“第一”、“第二”等的序数将用于描述各种组件,但是在这里不限制那些
组件。该术语仅用于区分一个组件与另一组件。例如,第一组件可以被称为第二组件,且同样地,第二组件也可以被称为第一组件,而不脱离本技术构思的教导。在此使用的术语“和/或”包括一个或多个关联的列出的项目的任何和全部组合。
31.在这里使用的术语仅用于描述各种实施例的目的且不意在限制。如在此使用的,单数形式意在也包括复数形式,除非上下文清楚地指示例外。另外将理解术语“包括”和/或“具有”当在该说明书中使用时指定所述的特征、数目、步骤、操作、组件、元件或其组合的存在,而不排除一个或多个其它特征、数目、步骤、操作、组件、元件或其组的存在或者附加。
32.申请概述
33.如上所述,在实际产业中,通常将多个结构装配在一起来实现特定功能。例如,将电缆框架安装于机柜表面来实现电缆与机柜的内部部件(例如,断路器)之间的连接。
34.在一些应用场景中,待装配的两个结构的表面需紧密贴合,以实现密封安装。然而,如果两个结构需要贴合的两个面(即,安装面)中至少一个安装面不平整,两个结构则难以实现紧密贴合,进而难以达到预期的密封效果。
35.具体地,成型工艺、特定的功能需求等原因均可能导致结构形成不平整的安装面。例如,一些需要热成型的结构在成型过程中会产生一定程度的变形,这种变形将导致结构在热成型后形成凹凸不平的安装面,影响其与其他结构之间的安装密封性(即,该结构安装于其他结构后该结构与其他结构之间的密封性)。仍以电缆框架与机柜的配合安装为例,通过热成型工艺加工成型形成的电缆框架的与所述机柜的安装面贴合的面(即,所述电缆框架的安装面)将存在一定程度的变形,影响其与所述机柜的安装密封性。再例如,一些结构需要满足形成不平整表面以增大表面积这一特定功能需求,这与其需形成平整安装面来提高与其他结构之间的安装密封性相矛盾。
36.理论上,可以在两个待装配的结构的安装面之间设置弹性密封件(例如,密封橡胶圈),利用所述弹性密封件具有弹性、可压缩的特点,通过挤压弹性密封件的方式使得两个待装配结构的安装面分别与所述弹性密封件紧密贴合来实现密封。然而,由于两个待装配的结构的两个安装面中至少一个安装面不平整,其中一个待装配的结构的安装面的不同部分与另一个待装配的结构的安装面的对应部分之间的间隙的尺寸不同,例如,一个待装配结构的安装面的第一部分与另一个待装配的结构的安装面的第一部分之间的间隙的尺寸,和,一个待装配结构的安装面的第二部分与另一个待装配的结构的安装面的第二部分之间的间隙的尺寸之间存在差异。为了使得不平整的安装面的各个部分与所述弹性密封件紧密贴合,弹性密封件将对安装面产生压力,且不平整的安装面的各个部分将承受不同的压力,即,发生受力不均的情况,这将影响待装配的结构的使用寿命、结构稳定性、安装稳定性。具体地,为了实现不平整的安装面的凹陷部分与所述弹性密封件紧密贴合,不平整的安装面的凸起部分将承受较大的压力。且当安装面的平整度较低,安装面凸起部分和凹陷部分之间的凹凸度较大时,即使挤压弹性密封件也难以使得安装面的凹陷部分与所述弹性密封件紧密贴合。
37.本技术的发明人提出,可以在两个待装配的结构的两个安装面之间设置补偿结构来补偿所述两个待装配的结构的两个安装面的各个部分之间的间隙尺寸差距。例如,以凹槽作为所述补偿结构,在两个待装配的结构的两个安装面中至少一个安装面设置深度不一致的凹槽,使得位于一个安装面的各个凹槽的槽底与另一个安装面的对应部分之间的间隙
的尺寸基本一致。这样,在一个安装面的凹槽和另一个安装面的对应部分之间设置密封件,安装面的各个部分承受的密封件的压力基本一致,即,安装面的各个部分受力较为均匀。
38.基于此,本技术提出了一种安装结构,适于与密封件相配合安装于待装配结构的安装面,其特征在于,其包括:结构主体和形成于所述结构主体的至少二凹槽,至少二所述凹槽适于将位于所述安装结构和待装配结构的安装面之间的密封件嵌合其中,其中,至少二所述凹槽的深度不同。
39.在介绍本技术的基本原理之后,下面将参考附图来具体介绍本技术的各种非限制性实施例。
40.示意性安装结构
41.如图1至图7所示,根据本技术实施例的安装结构 1被阐明,其中,所述安装结构 1提供了一种适用于安装面不平整的结构的密封安装方案,以改善待装配的结构之间的安装密封性。例如,适用于安装面不平整的电缆密封框架与机柜的密封安装方案,以改善电缆密封框架与机柜之间的安装密封性。
42.具体地,在所述安装结构 1与待装配结构 2安装配合时,如果所述安装结构的安装面 110和/或与所述安装结构 1相对应的所述待装配结构的安装面 210不平整,所述安装结构的安装面 110和所述待装配结构的安装面 210之间将存在间隙,且所述安装结构的安装面 110的各个部分与所述待装配结构的安装面 210之间的间隙的尺寸存在差异,所述安装结构 1和待装配结构 2难以紧密贴合。这里,将与所述安装结构 1相安装配合的结构称为待装配结构 2,不限定所述待装配结构 2的具体结构,以及,所述安装结构1和所述待装配结构 2的装配方式。例如,在一些具体示例中,所述待装配结构 2固定,所述安装结构 1被移向所述待装配结构 2,并被安装于所述待装配结构 2;在另一些具体示例中,所述安装结构 1固定,所述待装配结构 1被移向所述安装结构 1,并被安装于所述安装结构 1。
43.理论上讲,可以通过在所述安装结构 1和所述待装配结构 2之间设置弹性密封件(例如,密封橡胶圈),利用所述弹性密封件具有弹性、可压缩的特点,通过挤压弹性密封件的方式使得所述安装结构的安装面 110与所述弹性密封件紧密贴合,以及,所述待装配结构的安装面 210与所述弹性密封件紧密贴合来实现密封。然而,由于所述安装结构的安装面 110和/或所述待装配结构的安装面 210不平整,为了使得不平整的安装面的各个部分与所述弹性密封件紧密贴合,不平整的安装面的各个部分将承受来自所述弹性密封件的不同的压力,也就是,发生受力不均的情况,这将影响所述安装结构 1和/或所述待装配结构 2的使用寿命、结构稳定性、安装稳定性。且当不平整的安装面的平整度低于一定值,不平整的安装面的凸起部分和凹陷部分之间的凹凸度较大时,即使挤压弹性密封件也难以使得不平整的安装面的凹陷部分与所述弹性密封件紧密贴合。
44.本技术的发明人提出,可以在所述安装结构 1和所述待装配结构 2之间设置补偿结构来补偿所述安装结构的安装面 110的各个部分和所述待装配结构的安装面 210之间的间隙的尺寸差距。例如,以深度不一致的凹槽作为所述补偿结构,在所述安装结构 1和/或所述待装配结构 2设置深度不一致的至少二凹槽,使得位于所述安装结构 1的各个凹槽的槽底与所述待装配结构的安装面 210之间的间隙的尺寸基本一致。这样,在所述安装结构 1的凹槽和所述待装配结构的安装面 210之间设置密封件 3,所述安装结构的安装面 110的各个部分承受的密封件 3的压力基本一致,即,所述安装结构的安装面 110的各个部
分受力较为均匀。
45.相应地,在本技术实施例中,所述安装结构 1适于与密封件 3相配合安装于待装配结构的安装面 210。所述安装结构 1包括结构主体 10和形成于所述结构主体 10的至少二凹槽,至少二所述凹槽的深度不同,至少二所述凹槽适于将位于所述安装结构 1和所述待装配结构的安装面 210之间的密封件 3(如图2所示)嵌合其中,通过这样的方式使得所述安装结构 1密封地安装于所述待装配结构 2。所述凹槽还在一定程度上起到定位作用,防止所述密封件 3在所述安装结构 1和所述待装配结构 2之间滑动。
46.值得一提的是,所述凹槽的深度需根据所述安装结构 1和所述待装配结构 2的结构特点来设计。具体地,在本技术的一些实施方式中,所述安装结构的安装面 110不平整,为了补偿所述安装结构的安装面 110的各个部分与所述待装配结构的安装面 210之间的间隙的尺寸差距,可在所述安装结构的安装面 110的凹陷处设置深度较浅的凹槽,在所述安装结构的安装面 110的凸起处设置深度较深的凹槽,使得位于所述安装结构的安装面 110的凹陷处的凹槽的槽底与所述待装配结构的安装面 210之间的距离尽可能地接近位于所述安装结构的安装面 110的凸起处的凹槽的槽底与所述待装配结构的安装面 210之间的距离。或者,在本技术的另一些实施方式中,所述安装结构的安装面 110为平整的安装面,所述待装配结构的安装面 210为不平整的安装面,为了补偿所述所述待装配结构的安装面 210的各个部分与所述安装结构的安装面 110之间的间隙的尺寸差距,可在所述安装结构的安装面 110的与所述待装配结构 2的凹陷处相对应的位置设置深度较浅的凹槽,在所述安装结构的安装面 110的与所述待装配结构 2的凸起处对应的位置设置深度较深的凹槽,使得位于所述安装结构的安装面 110的与所述待装配结构 2的凹陷处相对应的凹槽的槽底与所述待装配结构的安装面 210之间的距离尽可能地接近位于所述安装结构的安装面 110的与所述待装配结构 2的凸起处相对应的凹槽的槽底与所述待装配结构的安装面 210之间的距离。再或者,在本技术的又一些实施方式中,所述安装结构的安装面 110和所述待装配结构的安装面 210均为不平整的安装面,可根据所述安装结构的安装面 110的面型和所述待装配结构的安装面 210的面型在所述安装结构 1的和/或所述待装配结构 2设置合适的凹槽。
47.相应地,在本技术的一个具体示例中,所述安装结构的安装面 110不平整,所述凹槽形成于所述安装结构 1的不平整的安装面。例如,在安装面不平整的电缆密封框架与机柜的密封安装方案中,所述安装结构 1被实施为所述电缆密封框架,所述待装配结构 2被实施为机柜,所述凹槽可形成于所述电缆密封框架的不平整的安装面。
48.在该具体示例中,所述结构主体 10包括第一主体部分 11和第二主体部分 12,如图3至图5所示。所述第二主体部分 12相对于所述第一主体部分 11凹陷,所述第一主体部分 11的第一表面和所述第二主体部分 12的第二表面形成所述安装结构的安装面 110的一不平整部分。至少二所述凹槽包括第一凹槽 21和第二凹槽 22,所述第一凹槽 21形成于所述第一主体部分 11,所述第二凹槽 22形成于所述第二主体部分 12。也就是,所述第一凹槽 21形成于所述结构主体 10的凸起处,所述第二凹槽 22形成于所述结构主体 10的凹陷处。所述第一凹槽 21的深度大于所述第二凹槽 22的深度,如图5所示。所述第二主体部分 12在所述第一凹槽 21的深度方向上相对于所述第一主体部分 11凹陷,所述第二主体部分 12的第二表面在所述第一凹槽 21的深度方向上相对于所述第一主体部分 11的第一
表面凹陷,其中,所述第一凹槽 21的深度方向与所述第二凹槽 22的深度方向相一致。这样,所述第一凹槽 21的槽底与所述安装结构的安装面 110的凸起处的距离大于所述第二凹槽 22的槽底与所述安装结构的安装面 110的凹陷处的距离,通过这样的方式,补偿所述安装结构的安装面 110的凹陷处(例如,所述第二主体部分 12的第二表面)和凸起处(例如,所述第一主体的第一表面)在所述第一凹槽 21的深度方向上的不平整度,进而补偿所述安装结构的安装面 110的凹陷处与所述待装配结构的安装面 210之间的间隙和所述安装结构的安装面 110的凸起处与所述待装配结构的安装面 210之间的间隙的尺寸差距。
49.在本技术的另一个具体示例中,所述待装配结构的安装面 210不平整,所述安装结构的安装面 110较为平整,所述凹槽形成于所述安装结构 1的较为平整的安装面。例如,在安装面不平整的电缆密封框架与机柜的密封安装方案中,所述安装结构 1被实施为所述电缆密封框架,所述待装配结构 2被实施为机柜,所述凹槽可形成于所述机柜的较为平整的安装面。
50.在该具体示例中,在所述安装结构 1安装于所述待装配结构 2的过程中,所述结构主体 10的第一主体部分 11对应于所述待装配结构的安装面 210的凸起处,所述结构主体 10的第二主体部分 12对应于所述待装配结构的安装面 210的凹陷处。设置于所述第一主体部分 11的第一凹槽 21的深度大于设置于所述第二主体部分 12的第二凹槽 22的深度,通过这样的方式,补偿所述待装配结构的安装面 210的凹陷处与所述安装结构的安装面 110之间的间隙和所述待装配结构的安装面 210的凸起处与所述安装结构的安装面 110之间的间隙的尺寸差距,使得位于所述安装结构 1的深度较深的第一凹槽 21的槽底与所述待装配结构的安装面 210的凸起处的距离接近位于所述安装结构 1的深度较浅的第二凹槽 22的槽底与所述待装配结构的安装面 210的凹陷处的距离。
51.在本技术的又一个具体示例中,所述安装结构的安装面 110不平整,且所述结构主体 10还包括第三主体部分 13和第四主体部分 14,如图3和图4所示。至少二所述凹槽还包括形成于所述第三主体部分 13的第三凹槽 23和形成于所述第四主体部分 14的第四凹槽 24。
52.在该具体示例中,所述第四主体部分 14在所述第三凹槽 23的深度方向相对于所述第三主体部分 13凹陷,所述第三主体部分 13的第三表面和所述第四主体部分 14的第四表面形成所述安装结构的安装面 110的另一不平整部分。也就是,所述第三凹槽 23形成于所述结构主体 10的凸起处,所述第四凹槽 24形成于所述结构主体 10的凹陷处。所述第三凹槽 23的深度大于所述第四凹槽 24的深度,如图6和图7所示。所述第四主体部分 14在所述第三凹槽 23的深度方向上相对于所述第三主体部分 13凹陷,所述第四主体部分 14的第四表面在所述第三凹槽 23的深度方向上相对于所述第三主体部分 13的第三表面凹陷,其中,所述第三凹槽 23的深度方向与所述第四凹槽 24的深度方向相一致。这样,所述第三凹槽 23的槽底与所述安装结构的安装面 110的凸起处的距离大于所述第四凹槽 24的槽底与所述安装结构的安装面 110的凹陷处的的距离,通过这样的方式,补偿所述安装结构的安装面 110的凹陷处(例如,所述第四主体部分 14的第四表面)和凸起处(例如,所述第三主体的第三表面)在所述第三凹槽 23的深度方向上的不平整度,进而补偿所述安装结构的安装面 110的凹陷处与所述待装配结构的安装面 210之间的间隙和所述安装结构的安装面 110的凸起处与所述待装配结构的安装面 210之间的间隙的尺寸差距。
53.在本技术的又一个具体示例中,所述待装配结构的安装面 210不平整,所述安装结构的安装面 110较为平整,所述第三凹槽 23和所述第四凹槽 24形成于所述安装结构 1的较为平整的安装面。
54.在该具体示例中,在所述安装结构 1安装于所述待装配结构 2的过程中,所述结构主体 10的第三主体部分 13对应于所述待装配结构的安装面 210的凸起处,所述结构主体 10的第四主体部分 14对应于所述待装配结构的安装面 210的凹陷处。设置于所述第三主体部分 13的第三凹槽 23的深度大于设置于所述第四主体部分 14的第四凹槽 24的深度,通过这样的方式,补偿所述待装配结构的安装面 210的凹陷处与所述安装结构的安装面 110之间的间隙和所述待装配结构的安装面 210的凸起处与所述安装结构的安装面 110之间的间隙的尺寸差距,使得位于所述安装结构 1的深度较深的第三凹槽 23的槽底与所述待装配结构的安装面 210的凸起处的距离接近位于所述安装结构 1的深度较浅的第四凹槽 24的槽底与所述待装配结构的安装面 210的凹陷处的距离。
55.值得一提的是,所述安装结构 1的深度不一致的部位的数量并不为本技术所局限,例如,在本技术的一个具体示例中,所述安装结构的第二主体部分 12包括第五主体部分和第六主体部分,所述第六主体部分相对于所述第五主体部分凹陷,所述第二凹槽 22包括形成于所述第五主体部分的第五凹槽和形成于所述第六主体部分的第六凹槽,形成于所述第五主体部分的第五凹槽的深度大于形成于所述第六主体部分的第六凹槽的深度。
56.应可以理解,所述第二凹槽 22的深度和所述第一凹槽 21的深度的差值,以及,所述第四凹槽 24的深度和所述第三凹槽 23的深度的差值根据实际需求设定。具体地,可根据所述安装结构 1的与所述第一凹槽 21对应的部位和所述安装结构 1的与所述第二凹槽 22对应的部分之间的平整度,以及,所述待装配结构 2的与所述第一凹槽 21对应的部位和所述待装配结构 2的与所述第二凹槽 22对应的部分之间的平整度来设定所述第二凹槽 22的深度和所述第一凹槽 21的深度的差值。可根据所述安装结构 1的与所述第三凹槽 23对应的部位和所述安装结构 1的与所述第四凹槽 24对应的部分之间的平整度,以及,所述待装配结构 2的与所述第三凹槽 23对应的部位和所述待装配结构 2的与所述第四凹槽 24对应的部分之间的平整度来设定所述第四凹槽 24的深度和所述第三凹槽 23的深度的差值。
57.在本技术的一个具体示例中,所述第二凹槽 22的深度和所述第一凹槽 21的深度的差值为大于零且小于或等于1毫米,所述第四凹槽 24的深度和所述第三凹槽 23的深度的差值为大于零且小于或等于1毫米。
58.在本技术的一些实施方式中,所述第二凹槽 22从所述第一凹槽 21一体地延伸,形成一体式结构,如图4和图5所示。所述第四凹槽 24从所述第三凹槽 23一体地延伸,形成一体式结构,如图4、图6和图7所示。在本技术的一个具体示例中,所述第一凹槽 21、所述第二凹槽 22、所述第三凹槽 23和所述第四凹槽 24形成环形凹槽,所述密封件 3被实施为与所述环形凹槽相匹配的环形密封件 3,在所述环形凹槽和所述环形密封件 3的配合下,可在所述安装结构 1和所述待装配结构 2之间实现全方位密封封装。
59.应可以理解,所述第二凹槽 22和所述第一凹槽 21也可相互独立,为分体式结构,所述第四凹槽 24和所述第三凹槽 23也可相互独立,为分体式结构,对此,并不为本技术所局限。
60.值得一提的是,在本技术的一些实施方式中,所述安装结构 1通过热成型工艺成型,通过热成型工艺成型后的安装结构 1表面将发生微小变形,主要表现为至少部分表面发生弯曲,特定部位凹陷。
61.进一步地,本技术的发明人发现,所述安装结构 1在热成型的过程的发生的变形具有一定的规律,可根据所述安装结构 1在热成型的过程中的变形规律来设计所述凹槽的深度。
62.在本技术的一些实施方式中,所述安装结构 1经过热成型工艺加工后其在第一预设方向上(例如,所述安装结构 1的长度方向上)中部相对于两个侧部向内凹陷。相应地,基于这一变形规律,在本技术的一个具体示例中,所述第二主体部分 12在所述第一预设方向上位于所述结构主体 10的中部,所述第一主体部分 11在所述第一预设方向上位于所述第二主体部分 12的外侧,所述第一主体部分相对于所述第二主体部分凸出。位于所述结构主体 10的中部的第一主体部分 11的凹槽(即,第一凹槽 21)的深度大于位于所述结构主体 10的中部外侧的第二主体部分 12的凹槽(即,第二凹槽 22)的深度,以补偿所述结构主体 10的中部与所述待装配结构的安装面 210之间的间隙和所述结构主体 10的侧部与所述待装配结构的安装面 210之间的间隙的尺寸差距。
63.在本技术的一些实施方式中,所述安装结构 1具有至少一孔结构 101,所述安装结构 1经过热成型工艺加工后其在第二预设方向上(例如,所述安装结构 1的宽度方向上)距离所述孔结构 101较近的部位相对于距离所述孔结构 101较远的部分凸出。相应地,基于这一变形规律,在本技术的一个具体示例中,所述第三主体部分 13在所述第二预设方向上与所述孔结构 101的距离小于所述第四主体部分 14在所述第二预设方向上与所述孔结构 101的距离,即,所述第三主体部分 13在所述第二预设方向上与所述孔结构 101的距离较近,所述第三主体部分 13相对于所述第四主体部分 14凸出。在所述第二预设方向上距离所述孔结构 101较近的第三主体部分 13的凹槽(即,第三凹槽 23)的深度大于距离所述孔结构 101较较远的第四主体部分 14的凹槽(即,第四凹槽 24)的深度,以补偿所述结构主体 10的靠近所述孔结构 101的部分与所述待装配结构的安装面 210之间的间隙和所述结构主体 10的远离所述孔结构 101的部分与所述待装配结构的安装面 210之间的间隙的尺寸差距。
64.在本技术的一些实施方式中,所述孔结构 101适配于用于连接所述安装结构 1和所述待装配结构 2的连接件(例如,螺栓),这样,所述连接件可在与所述孔结构 101的配合下将所述安装结构 1安装于所述待装配结构 2。
65.值得一提的是,在本技术的变形实施例中,可只在所述安装结构 1的特定部位设置凹槽,例如,仅在所述安装结构 1的凸起处设置凹槽。相应地,在本技术的变形实施例中,可仅在所述安装结构 1的第一主体部分 11和所述第三主体部分 13设置凹槽。
66.在本技术的一些实施方式中,所述安装结构 1适于安装电缆 4,如图1所示。相应地,在本技术的一个具体示例中,所述安装结构 1包括设置于所述结构主体 10的至少一电缆安装模块 30,所述电缆安装模块 30具有用于允许电缆 4通过的电缆安装孔。在该具体示例中,所述结构主体 10具有用于容纳所述电缆安装模块 30的至少一容置腔。应可以理解,所述电缆安装模块 30也可与所述结构主体 10一体成型,对此,并不为本技术所局限。所述电缆安装模块 30可被实施为kt型电缆控制头套,也可被实施为其他结构,对此,并不
为本技术所局限。
67.综上,所述安装结构 1被阐明,所述安装结构 1提供了一种适用于安装面不平整的结构的密封安装方案,以改善待装配结构 2之间的安装密封性。
68.以上结合具体实施例描述了本技术的基本原理,但是,需要指出的是,在本技术中提及的优点、优势、效果等仅是示例而非限制,不能认为这些优点、优势、效果等是本技术的各个实施例必须具备的。另外,上述公开的具体细节仅是为了示例的作用和便于理解的作用,而非限制,上述细节并不限制本技术为必须采用上述具体的细节来实现。