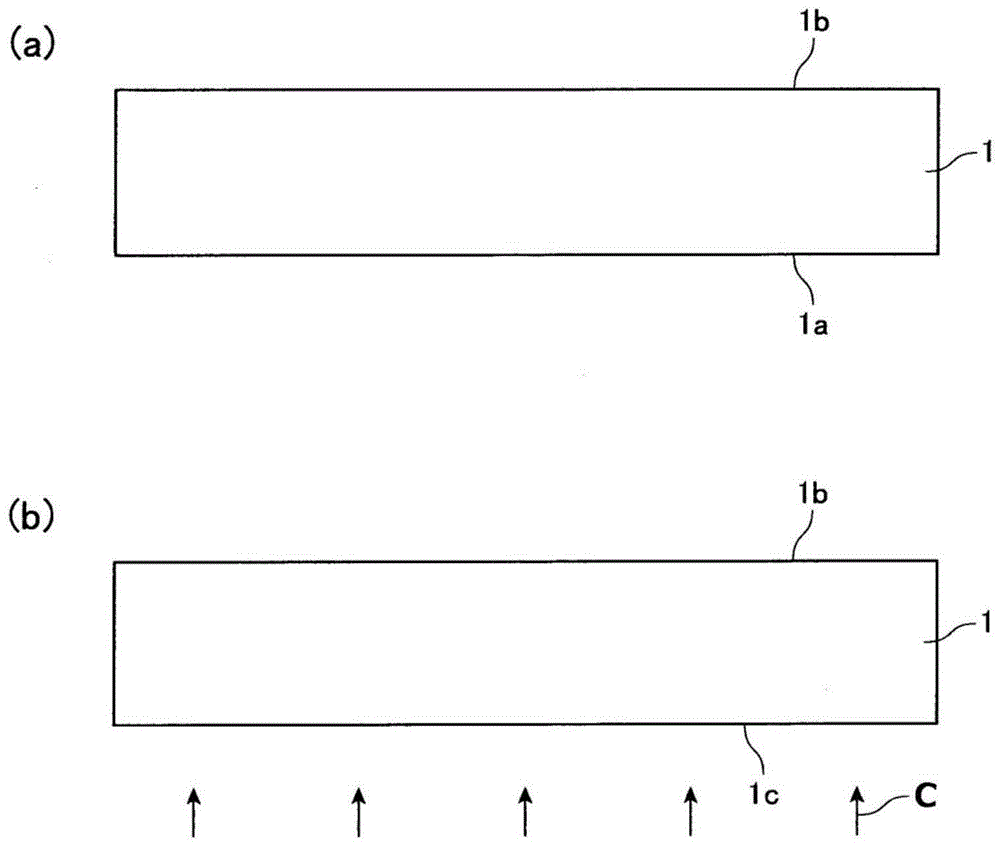
本发明涉及压电性材料基板与支撑基板的接合体、弹性波元件及其制造方法。
背景技术:
:为了实现高性能的半导体元件,广泛使用了由高电阻si/sio2薄膜/si薄膜构成的soi基板。在实现soi基板时,使用了等离子体活化。其原因在于,能够在较低的温度(400℃)下进行接合。为了提高压电器件的特性,提出了类似的由si/sio2薄膜/压电薄膜构成的复合基板(专利文献1)。在专利文献1中,通过离子注入法进行活化后,将由铌酸锂、钽酸锂形成的压电性材料基板和设置有氧化硅层的硅基板接合。还提出了一种多层结构的过滤器,其在接合界面形成单一或多个介电膜(专利文献2)。但是,针对用于实现钽酸锂/氧化硅/硅的结构的接合技术,几乎没有相关的公知信息。在专利文献3中记载了通过等离子体活化法将钽酸锂和蓝宝石、陶瓷隔着氧化硅层接合。在非专利文献1中记载了如下内容:对于钽酸锂基板和设置有氧化硅层的硅基板,持续地照射o2的rie(13.56mhz)等离子体和n2的微波(2.45ghz)等离子体,从而使其接合。在si和sio2/si的等离子体活化接合中,在其接合界面处形成si-o-si键合,由此可得到充分的接合强度。另外,与此同时si被氧化成sio2,从而平滑度提高,在最外表面上述接合被促进(非专利文献2)。现有技术文献非专利文献非专利文献1:ecstransactions,3(6)91-98(2006)非专利文献2:j.appliedphysics113,094905(2013)专利文献专利文献1:日本特开2016-225537专利文献2:日本专利第5910763号专利文献3:日本专利第3774782号技术实现要素:但是,如现有文献所述,通过离子注入使铌酸锂、钽酸锂基板变薄来制作压电元件的情况下,存在特性低这样的问题。认为其原因在于,结晶性会因离子注入时的损伤而劣化。另一方面,将铌酸锂、钽酸锂等的压电性材料基板与硅基板上的氧化硅层接合后,对压电性材料基板进行研磨而使其变薄,在该情况下,能够利用cmp除去加工变质层,因此元件特性不会劣化。但是,当通过研磨加工使压电性材料基板的厚度减小时,所得到的接合体的特性有时会劣化。特别是,已知在将接合体用作弹性波元件的情况下,作为弹性波元件的特性、特别是谐振频率fs下的导纳与反谐振频率fr下的导纳的比率(导纳比)下降。若压电性材料基板的厚度为4.0μm以下、进而为3.0μm以下(特别是2.0μm以下),则该下降倾向变得更为显著。本发明的课题在于,在将由选自由铌酸锂、钽酸锂和铌酸锂-钽酸锂组成的组中的材质形成的压电性材料基板与设置有氧化硅层的支撑基板接合时,能够抑制接合体的特性劣化。本发明的接合体具备:支撑基板;氧化硅层,其设置在所述支撑基板上;以及压电性材料基板,其设置于所述氧化硅层上、并由选自由铌酸锂、钽酸锂和铌酸锂-钽酸锂组成的组中的材质形成,其特征在于,所述压电性材料基板与所述氧化硅层的界面处的氮浓度高于所述氧化硅层与所述支撑基板的界面处的氮浓度。另外,本发明涉及弹性波元件,其特征在于,该弹性波元件具备所述接合体、以及设置于所述压电性材料基板上的电极。另外,本发明是将由选自由铌酸锂、钽酸锂和铌酸锂-钽酸锂组成的组中的材质形成的压电性材料基板与设置有氧化硅层的支撑基板接合的方法,其特征在于,在150℃以下对所述压电性材料基板的接合面照射氮等离子体而活化后,将所述压电性材料基板的所述接合面接合于所述氧化硅层的接合面。另外,本发明涉及弹性波元件的制造方法,其特征在于,在通过前述方法获得所述接合体后,在所述压电性材料基板上设置电极。发明效果本发明人对将由铌酸锂等形成的压电性材料基板与设置有氧化硅层的支撑基板直接接合时接合体的特性发生劣化的原因进行了研究。特别是,对谐振频率fs下的导纳与反谐振频率fr下的导纳的比率(导纳比)下降的原因进行了详细研究。结果,得到了以下见解。即,若对si和sio2/si进行例如等离子体活化接合,则沿着接合界面而形成si-o-si键合,从而可得到足够高的接合强度。另外,与此同时si被氧化成sio2,从而使得平滑度提高,在最外表面促进上述接合(非专利文献2:j.appliedphysics113,094905(2013))。与此相对,在将铌酸锂、钽酸锂直接接合于设置有氧化硅层的支撑基板的情况下,沿着接合界面形成有ta(nb)-o-si键合,由此进行接合。但是,sio2/si的最外表面处的si原子的密度为与此相对,压电性材料基板的最外表面处的ta(nb)原子的密度由于是各向异性结晶而依赖于切割角,例如为以下,最外表面处的原子密度低。进一步,与硅不同,铌酸锂、钽酸锂并没有通过氧化而进行平滑化的机制,由此认为无法得到足够高的接合强度。结果,在将由铌酸锂、钽酸锂形成的压电性材料基板与sio2/si直接接合后对压电性材料基板进行加工的情况下,若压电性材料基板变薄,则剪切力施加于氧化硅层和支撑基板的氧化硅层侧区域,认为这导致了结晶性劣化。本发明人立足于这样的假设,尝试了沿着压电性材料基板与氧化硅层的接合界面设置氮浓度相对高的部分。结果发现,能够抑制因氧化硅层或支撑基板的氧化硅层侧区域处的结晶性劣化而导致的特性下降,由此完成了本发明。进一步发现,在150℃以下对压电性材料基板的接合面照射氮等离子体而活化后,将压电性材料基板的接合面接合于氧化硅层的接合面,从而容易沿着压电性材料基板与氧化硅层的界面生成氮浓度相对高的区域。附图说明图1中,(a)示出压电性材料基板1;(b)示出对压电性材料基板1的接合面进行活化而生成活化面1c的状态。图2中,(a)示出在支撑基板4的表面形成了氧化硅层5的状态;(b)示出对氧化硅层5进行了表面活化的状态。图3中,(a)示出将压电性材料基板1与支撑基板4上的氧化硅层5直接接合而得到的接合体7;(b)示出通过研磨使接合体7a的压电性材料基板1a变薄的状态;(c)示出弹性波元件。具体实施方式以下,一边适当参照附图一边对本发明进行详细说明。首先,如图1(a)所示,准备具有一对主面1a、1b的压电性材料基板1。在本例中,将1a作为接合面。接下来,如图1(b)所示,对压电性材料基板1的接合面1a如箭头c那样照射等离子体,得到表面活化后的接合面1c。另一方面,如图2(a)所示,在支撑基板4的表面4a形成氧化硅层5。接下来,如图2(b)所示,对氧化硅层5的表面5a如箭头c那样照射等离子体,从而进行表面活化,形成了活化后的接合面6。接着,如图3(a)所示,使压电性材料基板1上的活化后的接合面1c与支撑基板4上的氧化硅层5的活化后的接合面6接触,进行直接接合,得到接合体7。可以在该状态下在压电性材料基板1上设置电极。但是,优选的是,如图3(b)所示,对压电性材料基板1的主面1b进行加工而使基板1变薄,得到薄板化后的压电性材料基板1a。1d为加工面。接着,如图3(c)所示,在接合体7a的压电性材料基板1a的加工面1d上形成规定的电极8,能够得到弹性波元件10。此处,在本发明中,压电性材料基板1(1a)与氧化硅层5的界面a处的氮浓度na(参照图3)高于氧化硅层5和支撑基板4的界面b处的氮浓度nb。这意味着沿着界面a存在有氮浓度相对高的区域。在界面a存在有氮浓度高的区域的情况下,通常氮也扩散到氧化硅层5中,在氧化硅层5中存在氮浓度梯度,在界面b处氮浓度相对变低。但是,本发明并不限于此,即使不存在氧化硅层5中的氮浓度梯度而是氮浓度恒定,只要压电性材料基板1(1a)与氧化硅层5的界面a处的氮浓度na高于氧化硅层5与支撑基板4的界面b处的氮浓度nb,就包括在本发明中。此处,压电性材料基板1(1a)和氧化硅层5的界面a处的氮浓度na相对于氧化硅层5和支撑基板4的界面b处的氮浓度nb的比率(na/nb)优选为10以上,进一步优选为100以上。另外,比率(na/nb)实际上优选为1000以下。在优选的实施方式中,压电性材料基板1(1a)与氧化硅层5的界面a处的氮浓度na为1e19~1e21(1×1019~1×1021)atoms/cm3,进一步优选为5e19~5e20(5×1019~5×1020)。另外,氧化硅层5与支撑基板4的界面b处的氮浓度nb优选为1e19(1×1019)以下,进一步优选为7e18(7×1018)以下。在优选的实施方式中,压电性材料基板与氧化硅层的界面a处的碳浓度ca高于氧化硅层与支撑基板的界面b处的碳浓度cb。另外,压电性材料基板1(1a)与氧化硅层5的界面a处的碳ca相对于氧化硅层5与支撑基板4的界面b处的碳浓度cb的比率(ca/cb)优选为100以上,进一步优选为1000以上。另外,比率(ca/cb)实际上优选为1000以下。另外,在优选的实施方式中,压电性材料基板1(1a)与氧化硅层5的界面a处的碳浓度ca更优选为1e20~3e21(1×1020~3×1021)atoms/cm3。另外,氧化硅层5与支撑基板4的界面b处的碳浓度cb优选为1e18(1×1018)atoms/cm3以下。在优选的实施方式中,压电性材料基板与氧化硅层的界面a处的氟浓度fa高于氧化硅层与支撑基板的界面b处的氟浓度fb。另外,压电性材料基板1(1a)和氧化硅层5的界面a处的氟浓度fa相对于氧化硅层5和支撑基板4的界面b处的氟浓度fb的比率(fa/fb)优选为5以上,进一步优选为50以上。另外,比率(fa/fb)实际上优选为500以下。另外,压电性材料基板1(1a)与氧化硅层5的界面a处的氟fa优选为1e19~3e20(1×1019~3×1020)atoms/cm3。另外,氧化硅层5与支撑基板4的界面b处的氟浓度fb优选为5e18(5×1018)atoms/cm3以下。以下,依次对本发明的各构成要素进行说明。支撑基板4的材质没有特别的限定,优选包含选自由硅、水晶、硅铝氧氮陶瓷、莫来石、蓝宝石以及透光性氧化铝组成的组中的材质。由此,能够进一步改善弹性波元件10的频率的温度特性。在支撑基板4上形成氧化硅层5。该氧化硅层5的成膜方法没有限定,可以举例溅射、化学气相沉积法(cvd)、蒸镀。优选的是,支撑基板4为硅基板,此时,可以通过对硅基板表面进行氧的溅射或离子注入、在氧化气氛下加热来形成氧化硅层5。从本发明的观点出发,氧化硅层5的厚度优选为0.05μm以上,进一步优选为0.1μm以上,特别优选为0.2μm以上。另外,氧化硅层5的厚度优选为3μm以下,优选为2.5μm以下,进一步优选为2.0μm以下。本发明中使用的压电性材料基板1(1a)为钽酸锂(lt)单晶、铌酸锂(ln)单晶、铌酸锂-钽酸锂固溶体。由于它们的弹性波的传播速度快、机电耦合系数大,因此,适合作为高频且宽带频率用的弹性表面波器件。另外,压电性材料基板1(1a)的主面的法线方向没有特别限定,例如在压电性材料基板1(1a)由lt形成时,使用以弹性表面波的传播方向亦即x轴为中心、从y轴向z轴旋转了32°~50°的方向的压电性材料基板、即以欧拉角表示为(180°,58°~40°,180°)的压电性材料基板由于传播损失小,因此优选。在压电性材料基板(1a)由ln形成时,(a)使用以弹性表面波的传播方向亦即x轴为中心、从z轴向-y轴旋转了37.8°的方向的压电性材料基板、即以欧拉角表示为(0°,37.8°,0°)的压电性材料基板由于机电耦合系数大,因此优选;或者,(b)使用以弹性表面波的传播方向亦即x轴为中心、从y轴向z轴旋转了40°~65°的方向的压电性材料基板、即以欧拉角表示为(180°,50°~25°,180°)的压电性材料基板由于可得到高声速,因此优选。进一步,压电性材料基板1(1a)的大小没有特别的限定,例如直径为100mm~200mm、厚度为0.15μm~1μm。接着,在150℃以下对压电性材料基板1的接合面1a照射等离子体,使接合面1a活化。从本发明的观点出发,优选照射氮等离子体,但在照射氧等离子体的情形也能够得到本发明的接合体。表面活化时的压力优选为100pa以下,进一步优选为80pa以下。另外,气氛可以仅为氮,也可以仅为氧,还可以为氮、氧的混合物。等离子体照射时的温度为150℃以下。由此,能够得到接合强度高、且无结晶性劣化的接合体7、7a。从该观点出发,使等离子体照射时的温度为150℃以下,进一步优选为100℃以下。另外,等离子体照射时的能量优选为30w~150w。另外,等离子体照射时的能量与照射时间的乘积优选为0.12wh~1.0wh。在优选的实施方式中,在等离子体处理前,对压电性材料基板1的接合面1a及氧化硅层5的接合面5a进行平坦化加工。使各接合面1a、5a平坦化的方法有精研(1ap)研磨、化学机械研磨加工(cmp)等。另外,平坦面优选为ra≤1nm,进一步优选为0.3nm以下。氧化硅层5的接合面5a也可以进行等离子体处理。此时,可以利用氧、氮等的等离子体,特别优选为氮等离子体、氧等离子体。另外,等离子体处理时的温度优选为150℃以下,进一步优选为100℃以下。另外,对氧化硅层5的接合面5a进行等离子体照射时的压力优选为100pa以下,进一步优选为80pa以下。此时的能量优选为30w~150w。另外,等离子体照射时的能量与照射时间的乘积优选为0.12wh~1.0wh。接着,使压电性材料基板1的接合面1c与氧化硅层5的接合面6接触并接合。之后,优选通过进行退火处理来提高接合强度。退火处理时的温度优选为100℃以上300℃以下。本发明的接合体7、7a适合用于弹性波元件10。作为弹性波元件10,已知弹性表面波器件、兰姆波元件、薄膜谐振器(fbar)等。例如,弹性表面波器件在压电性材料基板1、1a的表面设置了激发弹性表面波的输入侧的idt(叉指式换能器,interdigitaltransducer)电极(也称为梳形电极、帘状电极)和接收弹性表面波的输出侧的idt电极。如果对输入侧的idt电极施加高频信号,则在电极间产生电场,激发弹性表面波,并在压电性材料基板1、1a上传播。而且,从在传播方向上设置的输出侧的idt电极,能够将传播的弹性表面波作为电信号输出。构成压电性材料基板1、1a上的电极8的材质优选为铝、铝合金、铜、金,进一步优选为铝或铝合金。铝合金优选使用在al中混合0.3重量%至5重量%的cu而成的铝合金。在该情况下,也可以使用ti、mg、ni、mo、ta来代替cu。实施例(实施例a1)根据参照图1~图3所说明的方法,制作了图3(c)所示的弹性波元件10。具体而言,准备了厚度为200μm、且两面进行了镜面研磨的42y切割x传播litao3基板(压电性材料基板)1、和厚度为675μm的高电阻(>2kω·cm)si(100)基板(支撑基板)4。基板尺寸均为150mm。在支撑基板4上,利用溅射法以500nm的厚度形成氧化硅层5的膜。由于成膜后的氧化硅层5的表面粗糙度ra为0.6nm,因此使用cmp(化学机械研磨)对表面稍微进行研磨,将ra改善至0.3nm。接下来,分别对压电性材料基板1的接合面1a和支撑基板4上的氧化硅层5的接合面5a进行清洗和表面活化。具体而言,实施使用了纯水的超声波清洗,通过旋转干燥使基板表面干燥。接着,将清洗后的支撑基板4导入等离子体活化腔室,利用氮气等离子体在30℃对接合面5a进行活化。另外,同样地将压电性材料基板1导入等离子体活化腔室,利用氮气等离子体在30℃对接合面1a进行表面活化。将表面活化时间设为40秒,将能量设为100w。为了除去表面活化中所附着的颗粒,再次实施了与上述操作相同的超声波清洗、旋转干燥。接着,进行各基板1、4的对位,在室温下使基板1、氧化硅层5的活化后的接合面1c、6彼此接触。使压电性材料基板1侧在上而进行接触。结果,观测到基板1与氧化硅层5的密合扩展的样子(所谓的接合波),可以确认到良好地进行了预接合。接着,为了增加接合强度,将接合体7投入氮气氛的烘箱并在120℃下保持10小时。对于得到的接合体7,使用sims法(二次离子质谱法)测定各部分中的氮浓度、碳浓度、氟浓度。作为sims测定装置使用camecaims-7f,在一次离子种为cs+、一次加速电压为15.0kv的条件下进行。检测区域为30μmφ。将测定结果示于表1。对加热后的接合体7的压电性材料基板1的表面1b实施磨削加工、精研加工以及cmp加工,使压电性材料基板1a的厚度成为16μm、8μm、4μm、2μm、1μm。压电性材料基板1a的厚度通过使用了光干涉的光学式测定机(filmetrix公司制f20)进行测定。在研磨后的压电性材料基板1a的表面1d上,利用光刻工艺设置由铝金属形成的idt电极8。使电极的周期λ为4μm,以使振荡频率达到1000mhz左右。idt电极8的厚度为200nm,在200对idt电极8的两侧设置由80对形成的反射器,制作了单端口弹性波元件10(saw谐振器)。用agilent公司制网络分析仪e5071c对所制成的弹性波元件(saw谐振器)10的阻抗特性进行了测定。结果,在1000mhz附近(fs)观测到谐振峰值,在1050mhz附近(fr)观测到反谐振的峰值。测定了谐振频率fs下的导纳值相对于反谐振频率fr下的导纳值的比率。将该结果示于表3。(实施例a2)在实施例a1中,使用氮气80%、氧气20%的混合气体的等离子体来代替氮等离子体。当变更气体组成时,适当变更匹配,以使rf的反射功率达到最小。其它与实施例a1同样地进行了实验。与实施例a1同样地操作,对得到的接合体7,测定各部分中的氮浓度、碳浓度、氟浓度,并将测定结果示于表1。另外,与实施例a1同样地操作,按压电性材料基板1a的厚度成为16μm、8μm、4μm、2μm、1μm进行加工,测定了谐振频率fs下的导纳值相对于反谐振频率fr下的导纳值的比率。将该结果示于表3。(比较例a1)与实施例a1同样地操作,制作各接合体7、7a以及弹性波元件10(saw元件),进行与实施例a1同样的测定。其中,氧化硅层5的膜形成于压电性材料基板1上,在支撑基板4侧未进行成膜。另外,进行氧化硅层5的表面活化和支撑基板4的表面活化,利用氮等离子体照射将氧化硅层5和支撑基板4的活化面直接接合。对得到的接合体,测定各部分中的氮浓度、碳浓度、氟浓度,并将测定结果示于表2。另外,与实施例a1同样地操作,按压电性材料基板的厚度成为16μm、8μm、4μm、2μm、1μm进行加工,测定了谐振频率fs下的导纳值相对于反谐振频率fr下的导纳值的比率。将该结果示于表3。[表1][表2][表3]导纳值的比率(db)加工后的压电性材料基板的厚度(μm)实施例a1实施例a2比较例a116.042.544.043.38.040.742.542.84.043.342.240.02.044.345.139.31.046.544.935.8如表3所示,对于使用了本发明的接合体7、7a的弹性波元件10(saw元件)而言,即使在将压电性材料基板1a的厚度加工为极薄的2.0μm~1.0μm的情况下,谐振频率fs下的导纳值相对于反谐振频率fr下的导纳值的比率也良好,并未劣化。另一方面,对于比较例的接合体而言,随着压电性材料基板1a的厚度变薄,谐振频率fs下的导纳值相对于反谐振频率fr下的导纳值的比率劣化。特别是,对于比较例al的接合体而言,若将压电性材料基板1a的厚度加工至4.0μm以下,则谐振频率fs下的导纳值相对于反谐振频率fr下的导纳值的比率显著劣化。(实施例b)在实施例al中,将压电性材料基板1、1a的材质变更为128y切割x传播铌酸锂。结果,得到了与实施例a1同样的结果。当前第1页12