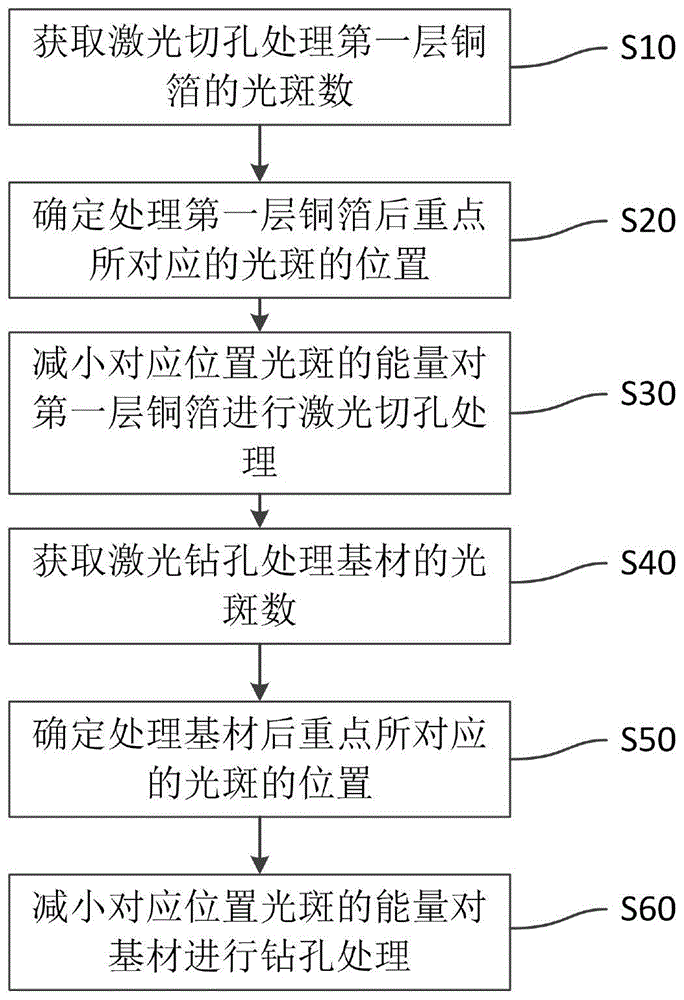
本发明涉及线路板加工领域,具体涉及一种线路板盲孔的加工方法。
背景技术:
:线路板中传统孔的种类除以导通与否简单的区分外,以功能的不同尚可分:零件孔,工具孔,通孔(via),盲孔(blindhole),埋孔(buriedhole)。其中,盲孔在电路板中起到导通的作用。盲孔加工是线路板制作过程中的一项重要工艺。由于近年来随着微电子技术的飞速发展,大规模和超大规模集成电路的广泛应用,微组装技术的进步,使印制电路板的制造向着积层化、多功能化方向发展,使印制电路图形的导线更加细微化、导通孔的加工也越来越小。常见的钻孔方式有机械钻孔、激光钻孔、感光成孔等,不同设备技术应用于不同层次板子。钻孔加工中所采用的机械方式钻孔工艺技术已不能满足此种高端线路板的要求,能胜任这种微孔加工方式的技术就是激光钻孔技术。激光钻孔的优势在于,可以加工相对较小的微通孔、盲孔,可加工孔径在50um—200um,甚至可以更小,且其在加工微孔的成本相对其他成孔方式有较大的优势。现有采用激光钻孔机进行盲孔加工的过程中,首先在激光光斑处于焦点位置时,先将双面铜箔的第一层铜打穿将盲孔位于第一层铜箔的孔切出来,切孔时,孔周首尾处的结合点位置由于光斑会有部分叠加,该位置相对于其他位置会打的比较重伤到底铜造成外观不良。利用螺旋切割的方式钻孔去除盲孔内的基材,由于螺旋轨迹的中间位置的光斑较密,光斑部分叠加,所以在螺旋清除中间基材的时候孔底中间部分也会打的比较重,基材清扫效果不均匀,造成外观不良。现有使用激光加工盲孔会由于光斑叠加的问题造成盲孔底部过烧,盲孔加工品质不良。技术实现要素:本发明要解决的技术问题在于,针对现有技术的上述缺陷,提供一种线路板盲孔的加工方法,克服现有的使用激光加工盲孔由于光斑叠加造成盲孔底部过烧,盲孔加工品质不良的问题。本发明解决其技术问题所采用的技术方案是:提供一种线路板盲孔的加工方法,所述线路板依次向下至少包括第一层铜箔、基材和第二层铜箔,其特征在于,包括步骤:获取激光切孔处理第一层铜箔的光斑数;确定处理第一层铜箔后重点所对应的光斑的位置;减小对应位置光斑的能量对第一层铜箔进行切孔处理;获取激光钻孔处理基材的光斑数;确定处理基材后重点所对应的光斑的位置;减小对应位置光斑的能量对基材进行钻孔处理。本发明的更进一步优选方案是:所述确定处理第一层铜箔后重点所对应的光斑的位置包括步骤:根据获取的光斑数使用小能量的激光加工获取光斑轨迹;将获取的光斑轨迹与实际加工效果进行比较确定重点所对应的光斑的位置。本发明的更进一步优选方案是:所述加工方法还包括步骤:减小处理第一层铜箔后重点对应不同位置光斑的能量获取不同的加工效果;比较不同的加工效果确定需要减小能量的光斑的位置;减小对应位置光斑的能量对第一层铜箔进行切孔处理。本发明的更进一步优选方案是:确定处理基材后重点所对应的光斑的位置包括步骤:根据获取的光斑数使用小能量的激光加工获取光斑轨迹;将获取的光斑轨迹与实际加工效果进行比较确定重点所对应的光斑的位置。本发明的更进一步优选方案是:所述加工方法还包括步骤:减小处理基材后重点对应不同位置光斑的能量获取不同的加工效果;比较不同的加工效果确定需要减小能量的光斑的位置;减小对应位置光斑的能量对基材进行钻孔处理。本发明的更进一步优选方案是:通过减小光斑的脉宽以减小对应位置光斑的能量。本发明的更进一步优选方案是:采用紫外激光以圆轨迹对第一层铜箔进行切孔处理,以螺旋切割轨迹对基材进行钻孔处理。本发明的更进一步优选方案是:根据激光加工参数获取加工处理第一层铜箔/基材的光斑数。本发明的更进一步优选方案是:所述激光加工参数至少包括盲孔加工孔径、加工速度、加工次数、激光频率,以及光斑直径。本发明的更进一步优选方案是:所述线路板包括柔性线路板和pcb板中的一种。本发明的有益效果在于,通过获取激光切孔处理第一层铜箔的光斑数,确定处理第一层铜箔后重点所对应的光斑的位置并减小对应位置光斑的能量对第一层铜箔进行切孔处理,以及,获取激光钻孔处理基材的光斑数,确定处理基材后重点所对应的光斑的位置并减小对应位置光斑的能量对基材进行钻孔处理,实现线路板盲孔的加工,解决盲孔加工的重点问题,防止盲孔底部过烧,达到盲孔孔底加工效果的一致性,提高盲孔加工品质。附图说明下面将结合附图及实施例对本发明作进一步说明,附图中:图1是本发明的线路板盲孔的加工方法的流程框图;图2是本发明的确定处理第一层铜箔后重点所对应的光斑的位置的流程框图;图3是本发明的减小对应位置光斑的能量对第一层铜箔进行切孔处理的流程框图;图4是本发明的确定处理基材后重点所对应的光斑的位置的流程框图;图5是本发明的减小对应位置光斑的能量对基材进行钻孔处理的流程框图;图6是本发明的线路板的简要结构图;图7是本发明的盲孔加工后线路板的简要结构图;图8是本发明的螺旋切割轨迹的简要示意图。具体实施方式现结合附图,对本发明的较佳实施例作详细说明。如图1所示,本发明提供一种线路板盲孔的加工方法的优选实施例。所述线路板依次向下至少包括第一层铜箔10、基材20和第二层铜箔30。所述线路板盲孔的加工方法包括步骤:s10、获取激光切孔处理第一层铜箔10的光斑数;s20、确定处理第一层铜箔10后重点所对应的光斑的位置;s30、减小对应位置光斑的能量对第一层铜箔10进行激光切孔处理;s40、获取激光钻孔处理基材20的光斑数;s50、确定处理基材20后重点所对应的光斑的位置;s60、减小对应位置光斑的能量对基材20进行钻孔处理。通过确定激光切孔处理第一层铜箔10后重点所对应的光斑的位置并减小对应位置光斑的能量对第一层铜箔10进行切孔处理,以及,确定处理基材20后重点所对应的光斑的位置并减小对应位置光斑的能量对基材20进行钻孔处理,实现线路板盲孔的加工,确定并减小光斑叠加部分的光斑的能量解决盲孔加工的重点问题,防止盲孔底部过烧,达到盲孔孔底加工效果的一致性,提高盲孔加工品质。其中,盲孔的形状可以是圆形或者腰形,本实施例中盲孔的形状优选为圆形。本实施例中,参考图2,在步骤s20中,所述确定处理第一层铜箔10后重点所对应的光斑的位置包括步骤:s21、根据获取的光斑数使用小能量的激光加工获取光斑轨迹;s22、将获取的光斑轨迹与实际加工效果进行比较确定重点所对应的光斑的位置。其中,小能量的激光是相对于实际切孔处理第一层铜箔10时的激光能量来说。采用小能量的激光在材料上进行加工,可获取加工的光斑轨迹,在材料上可看到激光的光斑轨迹,看清光斑的个数。将获取的光斑轨迹与实际加工效果比较便可初步确定处理第一层铜箔10后重点是由哪几个光斑造成的,从而确定重点对应的光斑的位置。参考图3,在步骤s30中,包括步骤:s31、减小处理第一层铜箔10后重点对应不同位置光斑的能量获取不同的加工效果;s32、比较不同的加工效果确定需要减小能量的光斑的位置;s33、减小对应位置光斑的能量对第一层铜箔10进行切孔处理。在初步确定重点对应的光斑的位置后,因造成重点的光斑有多个,操作人员可通过减少其中一个、两个或多个光斑的能量获取不同的加工效果,通过比较不同位置光斑能量减小的加工效果,确定减少哪些位置的光斑的能量能更有效地解决切孔处理第一层铜箔10的重点问题,从而进一步地提高盲孔加工品质。本实施例中,参考图4,在步骤s50中,所述确定处理基材20后重点所对应的光斑的位置包括步骤:s51、根据获取的光斑数使用小能量的激光加工获取光斑轨迹;s52、将获取的光斑轨迹与实际加工效果进行比较确定重点所对应的光斑的位置。其中,小能量的激光是相对于实际钻孔处理基材20时的激光能量来说。采用小能量的激光在材料上进行加工,可获取加工的光斑轨迹,在材料上可看到激光的光斑轨迹,看清光斑的个数。将获取的光斑轨迹与实际加工效果比较便可初步确定处理基材20后重点是由哪几个光斑造成的,从而确定重点对应的光斑的位置。参考图5,在步骤s60中,包括步骤:s61、减小处理基材20后重点对应不同位置光斑的能量获取不同的加工效果;s62、比较不同的加工效果确定需要减小能量的光斑的位置;s63、减小对应位置光斑的能量对基材20进行钻孔处理。在初步确定重点对应的光斑的位置后,因造成重点的光斑有多个,操作人员可通过减少其中一个、两个或多个光斑的能量获取不同的加工效果,通过比较不同位置光斑能量减小的加工效果,确定减少哪些位置的光斑的能量能更有效地解决钻孔处理基材20重点问题,从而进一步地提高盲孔加工品质。本实施例中,通过减小光斑的脉宽以减小对应位置光斑的能量。具体地,通过激光能量脉冲控制卡减小对应改善盲孔加工的光斑的能量。以及,减少脉宽的范围为5-10,即减少5-10个脉宽。以及,本实施例中采用紫外激光以圆轨迹对第一层铜箔10进行切孔处理,以螺旋切割轨迹对基材20进行钻孔处理。其中,采用波长为355nm的紫外激光对线路板的盲孔进行加工。进一步地,操作人员可根据激光加工参数获取处理除第一层铜箔10/基材20的光斑数。其中,激光加工参数包括第一激光加工参数和第二激光加工参数。操作人员根据第一激光加工参数获取切孔处理第一层铜箔10的光斑数,根据第二激光加工参数获取钻孔处理基材20的光斑数。具体地,所述第一激光加工参数包括盲孔加工孔径、激光功率、加工速度、加工次数、激光频率和光斑直径。所述第二激光加工参数包括盲孔加工孔径、加工速度、螺旋次数、激光频率、光斑直径、螺旋内圆直径和螺旋圈数。本实施例中,所述线路板包括柔性线路板和pcb板中的一种。本发明的线路板盲孔的加工方法优选应用于柔性线路板中盲孔的加工。以下以加工柔性线路板中孔径为100um的盲孔为例对本发明的线路板盲孔的加工方法作具体说明。其中,参考图6和图7,柔性线路板包括第一层铜箔10、基材20和第二层铜箔30。首先,在激光光斑处于焦点位置时,先将第一层铜箔10打穿将盲孔位于第一层铜箔10的孔切出来,也称之为切圆,切圆大小与盲孔的直径一致,圆的直径为100um。将第一层铜箔10打穿以将盲孔位于第一层铜箔10的圆切出来称为开窗。与步骤s10对应,操作人员根据钻孔孔径、加工速度、加工次数以及激光频率计算盲孔开窗切圆时的光斑数。在加工100um盲孔时第一步开窗切圆时使用的第一激光加工参数为:钻孔孔径激光功率加工速度加工次数激光频率光斑直径100um4.5w300mm/s1次40khz20um根据第一激光加工参数计算获取开窗的光斑数的公式为:n1=s1/d1,其中,n1为开窗的光斑数,s1为钻孔周长,d1为第一光斑间距。钻孔周长s1=2*π*3.14*(100-20)/2=251.2um,其中,r为钻孔孔径与光斑直径的差值得一半;第一光斑间距d1=v1/f1=(300mm/s)/(40khz)=7.5um,其中,v1为加工速度,f1为激光频率;因此,开窗的光斑数n1=s1/d1=251.2/7.5um=33.49个。根据上述第一激光加工参数可计算开窗的激光的光斑数为33个。接下来,与步骤s20对应,确定哪几个光斑的能量需要减小:根据上一步获取的第一激光加工参数和获取的光斑数,使用较小的能量如0.8w-1w左右的功率在材料上进行加工,小能量打在材料上可以看到激光的光斑痕迹,光斑痕迹的直径在3um左右,而光斑间距为7.5um,因此,比较容易看清光斑个数,用此小能量打出的光斑轨迹与实际的加工效果进行比较初步确定不良位置即开窗重点是由哪几个光斑造成的。初步估计大概是最后1-3个光斑即33、32、31此3个光斑造成的重点,通过激光能量脉冲控制卡依次减小最后1个光斑、2个光斑、3个光斑的脉宽并获取这三种方案的光斑轨迹,将其与实际加工效果进行比较,确定改善开窗重点所要减小能量光斑的位置,具体如下表所示:光斑数第33个第33、32个第33、32、31个更改前脉宽242424更改后脉宽181818加工效果仍然有重点无重点无重点根据比较结果可确定是第32与33个光斑打的比较深,因此,在激光能量脉冲控制卡控制界面将最后两个光斑即32和33两个光斑的脉宽由24改为18,减小最后两个光斑的能量,以此解决加工开窗重点的问题,达到避免伤到底铜的方法,提高盲孔加工品质。在以螺旋切割轨迹加工清除基材20时,设定离焦高度、激光能量以及螺旋圈数对盲孔内基材20进行钻孔处理,由于离焦后光斑能量比较分散不容易伤到底铜,所以可以用比较大的能量和较快的加工速度进行加工,因此只需要螺旋一次便可以直接将盲孔内的基材20全部清除干净,但由于螺旋轨迹的中间位置的光斑较密,所以在螺旋钻孔处理中间基材20的时候孔底中间部分也会打的比较重,看上去清扫效果不均匀,造成外观不良。与步骤s40对应,操作人员根据第二激光加工参数计算螺旋轨迹的光斑数。在使用螺旋切割钻孔处理基材20时使用的的第二激光加工参数为:根据第二激光加工参数计算获取螺旋切割的光斑数的公式为:n2=s2/d2,其中n2为螺旋切割的光斑数,s2为螺旋周长,d2为第二光斑间距。如图8所示,两圈螺旋相当于八个四分之一圆组成,最大螺旋四分之一圆的直径为螺旋孔径与光斑直径的差,其余七个四分之一圆的直径一次减小7.5um,其中,7.5um为螺旋外圆直径与內圆直径的差值的八分之一。因此,螺旋周长的计算公式为:s2=π*d1/4+π*d2/4+π*d3/4+π*d4/4+π*d5/4+π*d6/4+π*d7/4+π*d8/4,其中,d1,d2,d3,…,d8分别为组成螺旋轨迹的八个四分之一圆的直径。计算可得螺旋周长为430um。第二光斑间距d2=v2/f2=(300mm/s)/(40khz)=7.5um,其中,v2为加工速度,f2为激光频率;因此,螺旋切割的光斑数n2=s2/d2=300/7.5um=57.33个。根据上述第二激光加工参数可计算螺旋切割的激光的光斑数为57个,接下来,与步骤对应,确定哪几个光斑的能量需要减小;根据上一步获取的第二激光加工参数和获取的螺旋切割的光斑数,同样采用小能量在材料上打出螺旋的光斑轨迹与实际加工效果进行比较,初步估计大概是最后10个光斑即48-57个光斑造成的重点,通过激光能量脉冲控制卡依次减小最后5个、6个、7个、8个、9个、10个光斑的脉宽,比较其螺旋轨迹与实际加工效果,确定改善螺旋切割中重点所要减小能量光斑的位置,具体如下表所示:光斑数最后5个最后6个最后7个最后8个更改前脉宽24242424更改后脉宽18181818加工效果仍然有重点仍然有重点无重点无重点根据比较结果可确定是第51-57个光斑打的比较重,在激光能量脉冲控制卡控制界面将最后7个光斑即51-57此7个光斑的脉宽由24改为18,减小最后几个光斑的能量,解决加工螺旋切割重点的问题,达到孔底加工效果的一致性,避免伤到底铜,提高盲孔加工品质。应当理解的是,以上实施例仅用以说明本发明的技术方案,而非对其限制,对本领域技术人员来说,可以对上述实施例所记载的技术方案进行修改,或者对其中部分技术特征进行等同替换;而所有这些修改和替换,都应属于本发明所附权利要求的保护范围。当前第1页12