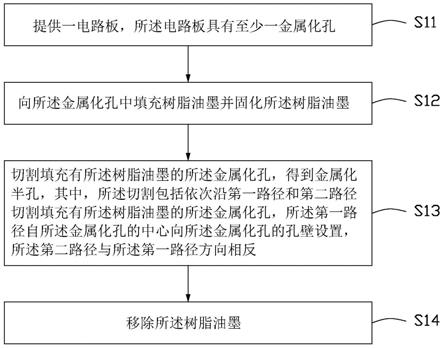
[0001]
本发明涉及电路板制作技术领域,尤其涉及一种电路板金属化半孔的制作方法。
背景技术:[0002]
印刷电路板(pcb)的板边位置通常设有金属化半孔,此印刷电路板通常称为pcb半孔板。现有的板边金属化半孔通常通过数控机床制作,该制作方式在切断金属化孔时,可能会在孔内以及孔表面形成铜丝(毛刺)。后续当pcb半孔板与母板连接时,铜丝会造成短路问题,降低产品良率。因此需要耗费巨大人力去检修铜丝,这无疑又耗费人力,提高生产成本。
技术实现要素:[0003]
有鉴于此,本发明提供一种能够提高良率的电路板金属化半孔的制作方法,避免人力检测导致的生产成本高的问题。
[0004]
本发明提供一种电路板金属化半孔的制作方法,包括以下步骤:
[0005]
提供一电路板,所述电路板具有至少一金属化孔;
[0006]
向所述金属化孔中填充树脂油墨并固化所述树脂油墨;
[0007]
切割填充有所述树脂油墨的所述金属化孔,得到金属化半孔;以及
[0008]
移除所述树脂油墨。
[0009]
本发明通过在所述金属化半孔中填充树脂油墨,避免切割金属化孔的过程中容易出现的铜丝毛刺,提高产品良率,从而避免人工检修铜丝所导致的生产成本高的问题。
附图说明
[0010]
图1是本发明较佳实施例中的电路板金属化半孔的制作方法的流程图。
[0011]
图2是图1所示的制作方法所提供的电路板的结构示意图。
[0012]
图3是在图2所示的电路板的金属化孔中填充树脂油墨后的结构示意图。
[0013]
图4是切割图3所示的金属化孔得到金属化半孔的切割路径示意图。
[0014]
图5是移除图4所示的金属化半孔中的树脂油墨后的电路板的结构示意图。
[0015]
主要元件符号说明
[0016]
电路板100金属化孔10孔环20金属化半孔30第一路径40第二路径50
具体实施方式
[0017]
下面将结合本发明实施例中的附图,对本发明实施例中的技术方案进行清楚、完
整地描述,显然,所描述的实施例仅仅是本发明一部分实施例,而不是全部的实施例。基于本发明中的实施例,本领域普通技术人员在没有做出创造性劳动前提下所获得的所有其他实施例,都属于本发明保护的范围。
[0018]
除非另有定义,本文所使用的所有的技术和科学术语与属于本发明的技术领域的技术人员通常理解的含义相同。本文中在本发明的说明书中所使用的术语只是为了描述具体的实施例的目的,不是旨在于限制本发明。
[0019]
请参阅图1,本发明较佳实施方式提供一种电路板金属化半孔的制作方法,包括以下步骤:
[0020]
s11、请参阅图2,提供一电路板100,所述电路板100具有至少一金属化孔10。
[0021]
在本实施方式中,所述电路板100为印刷电路板(pcb)。在图2中仅示出了两个所述金属化孔10。实际情况是,所述金属化孔10的数量不局限于两个,所述金属化孔10的数量还可以根据实际情况进行变更。
[0022]
所述电路板100还具有围绕所述金属化孔10设置的孔环20。
[0023]
s12、请参阅图3,向所述金属化孔10中填充树脂油墨并固化所述树脂油墨。
[0024]
所述树脂油墨为液态,并可以移除。所述树脂油墨具有耐酸性的特点。在本实施方式中,所述树脂油墨的粘度为240~280dpa.s。优选地,所述树脂油墨的粘度为260dpa.s。
[0025]
本发明只向所述电路板100的所述金属化孔10填充所述树脂油墨,同时所述树脂油墨还形成于所述孔环20的表面。由于本发明只向所述金属化孔10填充所述树脂油墨,因此所述树脂油墨的使用量少,生产成本低,且只需要填充一次,填充次数少,有利于提高生产效率。
[0026]
在本实施方式中,所述树脂油墨采用烘烤的方式进行固化,所述烘烤的温度为130~140℃,所述烘烤的时间为70~90min。优选地,所述烘烤的温度为130℃,所述烘烤的时间为90min。
[0027]
s13、请参阅图4及图5,切割填充有所述树脂油墨的所述金属化孔10,得到金属化半孔30,其中,所述切割包括依次沿第一路径40和第二路径50切割填充有所述树脂油墨的所述金属化孔10,所述第一路径40自所述金属化孔10的中心向所述金属化孔10的孔壁设置,所述第二路径50与所述第一路径40方向相反。
[0028]
在本实施方式中,所述切割通过一正/反转成型机(图未示)进行。所述正/反转成型机具有一主轴以及一铣刀。
[0029]
具体地,切割填充有所述树脂油墨的所述金属化孔10包括:
[0030]
所述正/反转成型机的主轴沿第一路径40正转切割填充有所述树脂油墨的所述金属化孔10(即主轴正转,铣刀从所述金属化孔10中心下刀,沿第一路径40切割所述金属化孔10的左侧),所述第一路径40自所述金属化孔10的中心向所述金属化孔10的孔壁设置;以及
[0031]
所述正/反转成型机的主轴沿第二路径50反转切割填充有所述树脂油墨的所述金属化孔10(即主轴反转,铣刀从所述金属化孔10中心下刀,沿第二路径50切割所述金属化孔10的右侧),所述第二路径50与所述第一路径40方向相反。
[0032]
此切割方式可以阻止所述金属化孔10内铜皮卷起,不需要人工检修等后制程,且生产中不需要反转所述电路板100,节省上下料时间,提高了切割效率。其中,所述正/反转成型机的主轴可在指令控制下进行正转或反转,搭配成型路径,进而克服所述金属化半孔
30孔内毛刺不良等问题。
[0033]
此外,由于在向所述金属化孔10中填充所述树脂油墨后,所述树脂油墨可将围绕所述金属化孔10设置的所述孔环20覆盖,因而可以阻止所述孔环20在切割时产生形变,从而避免所述金属化半孔30孔内毛刺的产生。
[0034]
s14、移除所述树脂油墨。
[0035]
在本实施方式中,所述树脂油墨通过一氢氧化钠溶液移除,所述氢氧化钠溶液的浓度为2%~5%。优选地,所述氢氧化钠溶液的浓度为3%。移除一次即可将所述树脂油墨完全清除,移除后,并不影响所述金属化半孔30的质量。
[0036]
本发明通过在所述金属化半孔30中填充所述树脂油墨,避免切割所述金属化孔10的过程中容易出现的铜丝毛刺,提高产品良率,从而避免人工检修铜丝所导致的生产成本高的问题。
[0037]
以上实施方式仅用以说明本发明实施例的技术方案而非限制,尽管参照以上较佳实施方式对本发明实施例进行了详细说明,本领域的普通技术人员应当理解,可以对本发明实施例的技术方案进行修改或等同替换都不应脱离本发明实施例的技术方案的精神和范围。