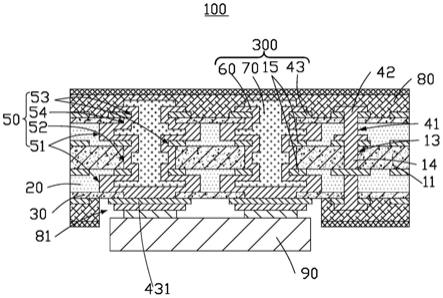
1.本发明涉及一种电路板的制造方法及电路板。
背景技术:2.印刷电路板中,基于承载电流、散热、阻抗匹配等需求,需要电路板中的线路层具有较大的厚度和宽度,从而降低线路层内阻。然而,因为电子产品的轻薄及高密度的要求,没有更多的空间用来增加线路层宽度,所以现有技术中常采用增大线路层厚度的方式。
3.传统制程中常采用在铜箔层上电镀,然后通过曝光显影方式蚀刻电镀层和铜箔层,得到线路层,电镀层的设置可以增加线路层的总厚度。然而,由于曝光显影制程的限制,电镀层厚度有限,得到的线路层中电镀层这一部分的宽度也可能会小于铜箔层的宽度,导致线路层内阻能够降低的程度有限;增厚的线路层在后续填胶过程可能会因为线距和电镀层的厚度出现局部的气泡或填胶不充分,导致产品可靠性受到影响等。
技术实现要素:4.有鉴于此,有必要提供一种在电路板内部空间形成内埋电镀层从而降低导线电阻的电路板的制造方法。
5.另,本发明还提供一种采用上述电路板的制造方法制造的电路板。
6.本发明提供一种电路板的制造方法,包括步骤:
7.提供一电路基板,所述电路基板包括基材层,所述基材层包括相对的两个表面,每一所述表面上依次层叠设置有内层线路层、胶层和外层铜箔层。
8.利用激光于所述电路基板中形成至少一开槽,所述开槽至少贯穿位于所述基材层一侧的所述外层铜箔层、所述胶层和所述内层线路层,所述开槽至少未贯穿另一所述外层铜箔层,所述开槽包括形成于所述胶层中的第一开口、形成于所述基材层中的第二开口和形成于所述内层线路层以及所述外层铜箔层中的第三开口,沿所述电路基板的延伸方向,所述第一开口的尺寸大于所述第二开口的尺寸,所述第一开口的尺寸还大于所述第三开口的尺寸。
9.于所述开槽的内壁形成电镀层,所述电镀层使所述内层线路层与所述外层铜箔层电性连接。
10.蚀刻所述外层铜箔层以形成外层线路层,所述电镀层连通所述内层线路层和所述外层线路层以共同形成导线,沿所述电路基板的延伸方向,所述导线的最大宽度等于所述第一开口的宽度,所述导线的总厚度不小于两所述外层线路层远离所述基材层一侧的表面之间的距离。
11.以及提供一电子元件,将所述电子元件安装于所述导线的所述外层线路层上,从而获得所述电路板。
12.本技术实施方式中,所述基材层的热分解温度大于所述胶层的热分解温度。
13.本技术实施方式中,所述胶层材质为环氧树脂,所述基材层材质为聚酰亚胺。
14.本技术实施方式中,所述“于所述开槽的内壁形成电镀层”之后,还包括:
15.于设置有所述电镀层的所述开槽内形成导电柱,所述导线还包括所述导电柱。
16.本技术实施方式中,所述胶层与所述外层线路层之间还设置有绝缘层,所述开槽贯穿所述基材层、两个所述内层线路层、两个所述胶层、两个所述绝缘层和一所述外层铜箔层。
17.本发明还提供一种电路板,所述电路板包括电路基板以及设置于所述电路基板上的至少一开槽和电子元件。
18.所述电路基板包括基材层,所述基材层包括相对的两个表面,每一所述表面上依次层叠设置有内层线路层、胶层和外层线路层,两所述内层线路层电性连接,所述内层线路层与所述外层线路层电性连接。
19.所述开槽至少贯穿位于所述基材层一侧的所述外层铜箔层、所述胶层和所述内层线路层,所述开槽至少未贯穿另一所述外层线路层,所述开槽包括形成于所述胶层中的第一开口、形成于所述基材层中的第二开口和形成于所述内层线路层以及所述外层线路层中的第三开口,沿所述电路基板的延伸方向,所述第一开口的尺寸大于所述第二开口的尺寸,所述第一开口的尺寸还大于所述第三开口的尺寸,所述开槽的内壁设置有电镀层,所述电镀层连通所述内层线路层与所述外层线路层以形成导线,沿所述电路基板的延伸方向,所述导线的最大宽度等于所述第一开口的宽度,所述导线的总厚度不小于两所述外层线路层远离所述基材层一侧的表面之间的距离。
20.所述电子元件安装于所述导线的所述外层线路层上。
21.本技术实施方式中,所述基材层的热分解温度均大于所述胶层的热分解温度。
22.本技术实施方式中,所述胶层的材质为环氧树脂,所述基材层的材质为聚酰亚胺。
23.本技术实施方式中,设置有所述电镀层的所述开槽内还设置有导电柱,所述导线还包括所述导电柱。
24.本技术实施方式中,所述胶层与所述外层线路层之间还设置有绝缘层。
25.本技术实施方式中,所述胶层与所述外层线路层之间还设置有绝缘层。
26.本发明提供的线路板的制造方法具有以下优点:通过开槽使内层线路层与外层线路层形成了贯通的网络结构,然后在开槽的内表面形成电镀层导通内外层线路层,得到内埋的导线,由于围绕开槽的胶层内缩,因此增加了导线的截面积,有效降低了导线的电阻。由于本案不需要单独增加内层或外层线路层的宽度,因此可以节省布线空间,满足高密度电路板技术发展需求。内埋式设计不存在断层现象,后续填充覆盖层的过程不会因为线距和铜厚等因素出现局部气泡或填胶不充分等问题。
附图说明
27.图1为本发明实施例提供的覆铜板的示意图。
28.图2为图1所示的覆铜板设置第一盲孔后的示意图。
29.图3为图2所示的覆铜板中第一盲孔内设置第一电连接部的示意图
30.图4为图3所示的覆铜板上形成内层线路层的示意图。
31.图5为本发明一实施例提供的电路基板的示意图。
32.图6为图5所示的电路基板上设置开槽和第二盲孔的示意图。
33.图7为图6所示的电路基板上在开槽内形成电镀层的示意图。
34.图8为图7所示的电路基板上在开槽内形成导电柱的示意图。
35.图9为图8所示的电路基板上形成外层线路层的示意图。
36.图10为图9所示的外层线路层上形成覆盖层的示意图。
37.图11为本发明一实施例提供的电路板的示意图。
38.主要元件符号说明
39.电路板
ꢀꢀꢀꢀꢀꢀꢀꢀꢀꢀꢀꢀꢀꢀꢀꢀꢀꢀꢀꢀ
100
40.电路基板
ꢀꢀꢀꢀꢀꢀꢀꢀꢀꢀꢀꢀꢀꢀꢀꢀꢀꢀ
200
41.覆铜板
ꢀꢀꢀꢀꢀꢀꢀꢀꢀꢀꢀꢀꢀꢀꢀꢀꢀꢀꢀꢀ
10
42.基材层
ꢀꢀꢀꢀꢀꢀꢀꢀꢀꢀꢀꢀꢀꢀꢀꢀꢀꢀꢀꢀ
11
43.内层铜箔层
ꢀꢀꢀꢀꢀꢀꢀꢀꢀꢀꢀꢀꢀꢀꢀꢀ
12
44.第一盲孔
ꢀꢀꢀꢀꢀꢀꢀꢀꢀꢀꢀꢀꢀꢀꢀꢀꢀꢀ
13
45.第一电连接部
ꢀꢀꢀꢀꢀꢀꢀꢀꢀꢀꢀꢀꢀꢀ
14
46.内层线路层
ꢀꢀꢀꢀꢀꢀꢀꢀꢀꢀꢀꢀꢀꢀꢀꢀ
15
47.胶层
ꢀꢀꢀꢀꢀꢀꢀꢀꢀꢀꢀꢀꢀꢀꢀꢀꢀꢀꢀꢀꢀꢀ
20
48.绝缘层
ꢀꢀꢀꢀꢀꢀꢀꢀꢀꢀꢀꢀꢀꢀꢀꢀꢀꢀꢀꢀ
30
49.外层铜箔层
ꢀꢀꢀꢀꢀꢀꢀꢀꢀꢀꢀꢀꢀꢀꢀꢀ
40
50.第二盲孔
ꢀꢀꢀꢀꢀꢀꢀꢀꢀꢀꢀꢀꢀꢀꢀꢀꢀꢀ
41
51.第二电连接部
ꢀꢀꢀꢀꢀꢀꢀꢀꢀꢀꢀꢀꢀꢀ
42
52.外层线路层
ꢀꢀꢀꢀꢀꢀꢀꢀꢀꢀꢀꢀꢀꢀꢀꢀ
43
53.开槽
ꢀꢀꢀꢀꢀꢀꢀꢀꢀꢀꢀꢀꢀꢀꢀꢀꢀꢀꢀꢀꢀꢀ
50
54.第一开口
ꢀꢀꢀꢀꢀꢀꢀꢀꢀꢀꢀꢀꢀꢀꢀꢀꢀꢀ
51
55.第二开口
ꢀꢀꢀꢀꢀꢀꢀꢀꢀꢀꢀꢀꢀꢀꢀꢀꢀꢀ
52
56.第三开口
ꢀꢀꢀꢀꢀꢀꢀꢀꢀꢀꢀꢀꢀꢀꢀꢀꢀꢀ
53
57.电镀层
ꢀꢀꢀꢀꢀꢀꢀꢀꢀꢀꢀꢀꢀꢀꢀꢀꢀꢀꢀꢀ
60
58.导电柱
ꢀꢀꢀꢀꢀꢀꢀꢀꢀꢀꢀꢀꢀꢀꢀꢀꢀꢀꢀꢀ
70
59.覆盖层
ꢀꢀꢀꢀꢀꢀꢀꢀꢀꢀꢀꢀꢀꢀꢀꢀꢀꢀꢀꢀ
80
60.开窗
ꢀꢀꢀꢀꢀꢀꢀꢀꢀꢀꢀꢀꢀꢀꢀꢀꢀꢀꢀꢀꢀꢀ
81
61.电子元件
ꢀꢀꢀꢀꢀꢀꢀꢀꢀꢀꢀꢀꢀꢀꢀꢀꢀꢀ
90
62.导线
ꢀꢀꢀꢀꢀꢀꢀꢀꢀꢀꢀꢀꢀꢀꢀꢀꢀꢀꢀꢀꢀꢀ
300
63.宽度
ꢀꢀꢀꢀꢀꢀꢀꢀꢀꢀꢀꢀꢀꢀꢀꢀꢀꢀ
d1,d2,x
64.总厚度
ꢀꢀꢀꢀꢀꢀꢀꢀꢀꢀꢀꢀꢀꢀꢀꢀꢀꢀꢀꢀy65.如下具体实施方式将结合上述附图进一步说明本发明。
具体实施方式
66.下面将结合本发明实施例中的附图,对本发明实施例中的技术方案进行清楚、完整地描述,显然,所描述的实施例仅仅是本发明一部分实施例,而不是全部的实施例。基于本发明中的实施例,本领域普通技术人员在没有做出创造性劳动前提下所获得的所有其他实施例,都属于本发明保护的范围。
67.除非另有定义,本文所使用的所有的技术和科学术语与属于本发明的技术领域的技术人员通常理解的含义相同。本文中在本发明的说明书中所使用的术语只是为了描述具体的实施例的目的,不是旨在于限制本发明。
68.本发明实施例提供一种电路板的制造方法,包括步骤:
69.步骤s1,请参阅图1,提供一覆铜板10,所述覆铜板10包括基材层11及设置于所述基材层11相对的两表面上的内层铜箔层12。
70.本实施方式中,所述基材层11的材质包括但不局限于聚酰亚胺。
71.步骤s2,请参阅图2和图3,于所述覆铜板10上形成一第一盲孔13,于所述第一盲孔13内形成第一电连接部14,使得两所述内层铜箔层12通过所述第一电连接部14电性连接。
72.本实施方式中,可采用激光开孔的方式在所述覆铜板10上形成所述第一盲孔13。
73.本实施方式中,所述第一盲孔13未贯穿一所述内层铜箔层12,通过在所述第一盲孔13内镀铜以形成所述第一电连接部14,从而实现两所述内层铜箔层12的电性连接。可以理解的是,所述第一盲孔13也可以贯穿整个覆铜板。
74.步骤s3,请参阅图4,蚀刻所述内层铜箔层12以形成内层线路层15,以及所述基材层11露出于所述第一内层线路层15的表面。
75.本实施方式中,所述内层线路层15通过减成法(subtractive)工艺制得。具体地,可通过压膜曝光显影蚀刻去膜等制程得到所述内层线路层15。
76.步骤s4,请参阅图5,于每一所述内层线路层15的表面形成胶层20,所述胶层20包覆所述内层线路层15。
77.可以理解的是,也可以在所述基材层11露出于所述第一内层线路层15的表面形成所述胶层20,即,使所述胶层20填充于所述内层线路层15的间隙中。
78.本实施方式中,所述胶层20的材质包括但不局限于环氧树脂。
79.步骤s5,请参阅图5,于所述胶层20的表面形成外层铜箔层40,以形成一电路基板200。
80.本实施方式中,为双面增层,即在每一所述胶层20的表面均形成一所述外层铜箔层40。可以理解的是,当所述胶层20只设置于所述基材层11的一侧表面时,也可以选择单面增层。
81.本实施方式中,所述胶层20与所述外层铜箔层40之间还设置有一绝缘层30,所述绝缘层30的材质可以与所述基材层11相同,可以为聚酰亚胺。
82.步骤s6,请参阅图6,利用激光于所述电路基板200中形成至少一开槽50,所述开槽50至少贯穿所述基材层11和设置于所述基材层11同侧的所述内层线路层15、所述胶层20以及所述外层铜箔层40。
83.所述开槽50包括形成于所述胶层20中的第一开口51、形成于所述基材层11中的第二开口52以及形成于所述内层线路层15和所述外层铜箔层40中的第三开口53,沿所述电路基板200的延伸方向,所述第一开口51的宽度大于所述第二开口52的宽度,所述第一开口51的宽度大于所述第三开口53的宽度。
84.本实施方式中,所述第二开口52的宽度大于所述第三开口53的宽度。
85.其中,通过所述激光形成所述开槽50时,因激光形成开槽过程中会产生大量的热量,这一热量将被围绕所述开槽50的所述胶层20、所述基材层11和所述绝缘层30吸收,进而
使所述胶层20、所述基材层11和所述绝缘层30的材料发生降解,降解后,围绕所述开槽50的所述胶层20、所述基材层11和所述绝缘层30会发生沿所述电路基板200延伸方向上的内缩。使所述开槽50各处的宽度增加。而且,通过选择所述胶层20、所述基材层11和所述绝缘层30的材质,以及控制激光光束能量等,可以使不同层降解的程度不同,从而使所述开槽50各部分的宽度不同。
86.本实施方式中,所述胶层20的材质为环氧树脂,所述基材层11与所述绝缘层30的材质均为聚酰亚胺(pi)。
87.在经过激光照射后,高分子材料会吸收激光热量进而发生汽化或分解,材料汽化或分解的量与材料本身的性质有关。本实施方式中,环氧树脂和聚酰亚胺的内缩实际上是因为材料的受热分解,受热分解的程度与材料本身的热分解温度有关系:在受热情况下,大分子开始裂解的温度称之为热分解温度(thermal decomposition)。对于全芳香聚酰亚胺(pi),热分解温度一般在400℃~500℃,由联苯二酐和对苯二胺合成的聚酰亚胺,热分解温度达到600℃,环氧树脂的热分解温度在300℃以上。按照两种材料热分解温度规格可知,环氧树脂内缩宽度d1大于聚酰亚胺的内缩宽度d2,d2:d1=1:1.5,也就是说在两种材料接收同样的激光热量时,环氧树脂的内缩量比聚酰亚胺的内缩量大1.5倍。
88.所述基材层11用于承载内层线路层15,所述绝缘层30用于承载外层铜箔层40,内缩量太大的话会影响其表面的线路层,所以本技术中设置所述基材层11的内缩量相对较小。所述胶层20的宽度不受线路层的限制,所以在选择所述胶层20的材料时,可以选择热分解温度较低的材料,从而提高所述胶层20的内缩量。
89.本实施方式中,所述开槽50贯穿所述基材层11、两所述内层线路层15、两所述胶层20以及一所述外层铜箔层40。所述开槽50的底部为另一所述外层铜箔层40。
90.本实施方式中,所述开槽50还贯穿两所述绝缘层30,所述开槽50对应所述绝缘层30形成有第四开口54,所述绝缘层30与所述基材层11的材质相同,则所述开槽50对应所述绝缘层30形成的第四开口54与所述第二开口52的尺寸一致。
91.本实施方式中,所述制造方法还包括于所述绝缘层30以及所述外层铜箔层40中形成第二盲孔41,所述第二盲孔41对应所述第一电连接部14。
92.步骤s7,请参阅图7,于所述开槽50的内壁形成电镀层60,使所述内层线路层15与所述外层铜箔层40电性连接。
93.本实施方式中,所述电镀层60为镀铜层。具体地,所述电镀层60形成在第一开口51、第二开口52、第三开口53的内表面以及未被所述开槽50贯穿的所述外层铜箔层40靠近所述开槽50的表面,进而形成阶梯型镀铜层。
94.本实施方式中,所述制造方法还包括于所述第二盲孔41内形成第二电连接部42,使得所述外层铜箔层40与所述内层线路层15通过所述第二电连接部42实现电性连接。
95.本实施方式中,所述电镀层60未将所述开槽50镀满,可以理解的是,所述电镀层60仅镀于所述开槽50的内侧壁,所述电镀层60远离所述开槽50内侧壁的表面围成与原开槽50形状大致一样,尺寸略小的开槽。
96.另一实施方式中,所述电镀层60充满所述开槽50。
97.步骤s8,请参阅图8,于形成有所述电镀层60的所述开槽50内形成导电柱70。
98.本实施方式中,所述导电柱70是通过向形成有所述电镀层60的所述开槽50内填充
导电金属膏(例如铜膏或锡膏),再经过固化而形成。
99.在形成所述电镀层60时,所述电镀层60并未将所述开槽50填充满,本实施方式中,采用填充导电铜膏的方式进一步将所述开槽50填充满,在形成有电镀层60的所述开槽50内填充铜膏,填充效果好,不会在所述开槽50的内部形成空隙或气泡等不良。
100.步骤s9,请参阅图9,蚀刻所述外层铜箔层40以形成外层线路层43,所述电镀层60连通所述内层线路层15和所述外层线路层43以共同形成导线300,沿所述电路基板200的延伸方向,所述导线300的最外侧宽度x等于所述第一开口51的宽度,所述导线300的总厚度y不小于两所述外层线路层43远离所述基材层11一侧的表面之间的距离。
101.通过在电路基板200内部开槽,并通过所述胶层20、基材层11以及绝缘层30的内缩使得所述电镀层60形成内置于所述电路基板200的阶梯式结构,从而有效降低所述导线300的电阻。通过在形成所述电镀层60的所述开槽50内填充铜膏形成所述导电柱70,进一步降低了所述导线300的电阻。
102.所述胶层20内缩形成所述第一开口51,后续在所述开槽50内形成的所述电镀层60的最外侧的宽度与所述第一开口51的宽度相等,使得所述导线300的最外侧的宽度(最大宽度)x等于所述第一开口51的宽度,通过选择所述胶层20的材质以及激光的能量可以控制所述第一开口51的宽度,从而根据实际需求控制所述导线300的最大宽度x。再者导电柱70的设置可以使得开槽50内结构一体化,也可进一步降低所述导线300的电阻。电阻的降低有利信号的传输及阻抗匹配,另外也可以使电子元件快速散热。
103.本实施方式中,为了增加所述导线300的截面积,还可以将所述开槽50开口周围的所述外层线路层43的表面也形成所述电镀层60。同时,还可以将所述导电柱70的表面超出所述开槽50的开口,进一步增加所述导线300的截面积,所以,所述导线300的总厚度y可以进一步增加至所述导电柱70远离所述基材层11的表面,使得所述导线的总厚度y等于未被所述开槽50贯穿的所述外层线路层43远离所述基材层11的表面之间的距离,显著降低了所述导线300的电阻。
104.本实施方式中,沿所述电路基板200的延伸方向,所述导线300的最小截面积=2
×
第一开口51的截面积+第二开口52的截面积+3
×
第三开口53的截面积+2
×
第四开口54的截面积+2
×
所述导线300对应的内层线路层15的截面积+2
×
所述导线300对应的外层线路层43的截面积,由此可知,通过开设开槽50并在开槽50内表面形成电镀层60,使所述内层线路层15与所述外层线路层43形成了贯通的网络结构,然后将所述导电柱70填充在所述开槽50内,增加了所述导线300的截面积,有效降低了所述导线300的电阻。
105.本实施方式中,所述外层线路层43通过减成法(subtractive)工艺制得。具体地,可通过压膜曝光显影蚀刻去膜等制程得到所述外层线路层43。
106.步骤s10,请参阅图10,于所述外层线路层43的表面形成覆盖层80,未被所述开槽50贯穿的所述外层线路层43的一侧的所述覆盖层80上形成有一开窗81,所述开窗81对应所述开槽50设置,未被所述开槽50贯穿的所述外层线路层43由所述开窗81露出以形成焊垫431。
107.步骤s11,请参阅图11,提供一电子元件90,将所述电子元件90安装于所述焊垫431上,从而获得所述电路板100。
108.本实施方式中,将所述电子元件90焊接在所述焊垫431上。
109.其中,所述电镀层60连通对应所述开槽50处的所述外层线路层43与所述内层线路层15,从而共同形成所述导线300,本实施方式中,所述开槽50为两个,两个所述开槽50对应两根所述导线300,两根所述导线300的所述外层线路层43连接所述电子元件90,这两根所述导线300可以是电源线或信号线等。
110.请参阅图11,为本发明实施例提供的一种采用上述电路板制造方法制造的电路板100,所述电路板100包括电路基板200以及设置于所述电路基板200上的开槽50和电子元件90。
111.所述电路基板200包括基材层11,所述基材层11包括相对设置的两个表面,每一所述表面层叠设置有内层线路层15、胶层20以及外层线路层43,两所述内层线路层15电性连接,同侧的所述内层线路层15与所述外层线路层43电性连接。
112.请一并参阅图9,所述开槽50至少未贯穿一所述外层线路层43,所述开槽50包括形成于所述胶层20中的第一开口51、形成于所述基材层11中的第二开口52和形成于所述内层线路层15以及所述外层线路层43中的第三开口53,沿所述电路基板200的延伸方向,所述第一开口51的尺寸大于所述第二开口52的尺寸,所述第一开口51的尺寸还大于所述第三开口53的尺寸。所述开槽50的内壁设置有电镀层60,所述电镀层60连通所述内层线路层15与所述外层线路层43以形成导线300,沿所述电路基板200的延伸方向,所述导线300的最大宽度x等于所述第一开口51的宽度,所述导线300的总厚度y至少等于两所述外层线路层43远离所述基材层11一侧的表面之间的距离。
113.所述电子元件90固定且电性连接于所述开槽50未贯穿的所述外层线路层43远离所述开槽50一侧的表面。
114.本实施方式中,所述基材层11以及所述绝缘层30的热分解温度均大于所述胶层20的热分解温度。
115.本实施方式中,所述胶层20为环氧树脂,所述基材层11为聚酰亚胺。
116.本实施方式中,形成有所述电镀层60的所述开槽50内还设置有导电柱70,所述导电柱70能够进一步增加所述导线300的截面积,从而进一步降低所述导线300的电阻。所述导电柱70为导电金属膏(例如铜膏或锡膏)经固化形成。
117.本实施方式中,所述电路板100还包括覆盖层80,所述覆盖层80设置于所述外层线路层43的表面,所述覆盖层80对应所述电子元件90设置有一开窗81,未被所述开槽50贯穿的所述外层线路层43于所述开窗81露出,所述外层线路层43由所述开窗81露出以形成焊垫431。所述电子元件90安装于所述焊垫431上。
118.本实施方式中,所述胶层20与所述外层线路层43之间还设置有绝缘层30。所述开槽50对应所述绝缘层30形成有第四开口54,所述绝缘层30与所述基材层11的材质相同,则所述开槽50对应所述绝缘层30形成的第四开口54与所述第二开口52的尺寸一致。
119.本实施方式中,两个所述开槽50对应两根所述导线300,两根所述导线300的所述外层线路层43连接所述电子元件90,这两根所述导线300可以是电源线或信号线等。
120.本发明通过开设所述开槽50并在所述开槽50内形成电镀层60,使所述内层线路层15与所述外层线路层43形成了贯通的网络结构,从而在所述电路板100内部形成内埋式的导线300,由于围绕开槽50的胶层20内缩,因此增加了所述导线300截面积,从而有效降低了导线300的电阻。同时不影响所述内层线路层15和所述外层线路层43的布线设计,所述外层
线路层43不存在断层现象,因此增厚的部分在后续填充所述覆盖层80的过程不会因为线距和铜厚等因素出现局部气泡或填胶不充分等问题。
121.另外,对于本领域的普通技术人员来说,可以根据本发明的技术构思做出其它各种相应的改变与变形,而所有这些改变与变形都应属于本发明的保护范围。