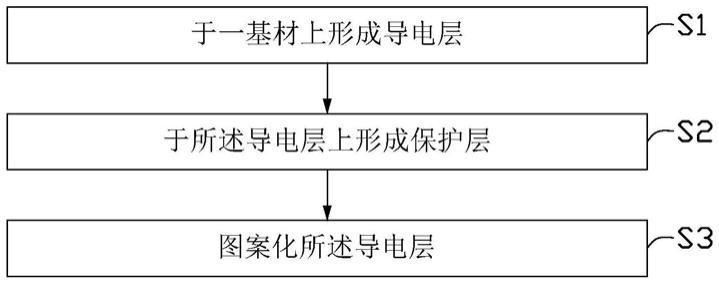
1.本发明涉及线路板技术领域,尤其涉及一种线路板及其制备方法。
背景技术:2.线路板(尤其是厚度小于等于40微米的超薄型线路板)在其线路层制备过程中,位于基材层上的导电层经压膜、曝光、显影及蚀刻等步骤后,位于基材层边缘的导电层会被蚀刻去除掉而暴露出基材层。因此,线路板容易因板边刚性不足,在后续制程中,存在板裂、板破的问题。另,线路板的板边暴露出的基材层容易产生碎屑,该碎屑掉落后,还会造成线路污染和刮伤等问题,损失整体良率。
技术实现要素:3.本发明一方面提供一种线路板的制备方法,其包括以下步骤:
4.于一基材上形成导电层,所述基材定义有线路区以及围绕所述线路区的周边区,所述基材具有连接并环绕所述周边区的侧面,所述导电层位于所述侧面、所述周边区以及所述线路区;
5.于所述导电层上形成保护层,所述保护层位于所述侧面以及所述周边区;以及
6.图案化所述导电层,使位于所述线路区的所述导电层被图案化形成线路层,位于所述侧面以及所述周边区的所述导电层由于被所述保护层覆盖而未被图案化且仍留在所述基材上形成一强化层;
7.其中,图案化所述导电层的步骤包括压干膜、曝光、显影、蚀刻以及去干膜,所述保护层在所述去干膜步骤中一并移除。
8.该线路板的制备方法,通过在基材的侧面及周边区形成导电层,且在图案化所述导电层之前,于基材的边缘涂布保护层,使得获得的线路板在板边及侧面仍保留有导电层(即,强化层),提高了线路板板边刚性,解决了线路板(尤其是厚度小于等于40微米的超薄型线路板)在制程中存在的板裂、板破的问题,进而避免了板边暴露出的基材产生的碎屑碎屑掉落后,造成的线路污染和刮伤等问题,提高了整体良率。
9.本发明另一方面还提供一种线路板,其包括:
10.基材,所述基材定义有线路区以及围绕所述线路区的周边区,所述基材具有连接并环绕所述周边区的侧面;
11.线路层,位于所述线路区,以及
12.强化层,位于所述侧面以及所述周边区。
13.该线路板,其基材的侧面及周边具有强化层,提高了线路板板边刚性,解决了线路板(尤其是厚度小于等于40微米的超薄型线路板)在制程中存在的板裂、板破的问题,进而避免了板边暴露出的基材产生的碎屑碎屑掉落后,造成的线路污染和刮伤等问题,提高了整体良率。
附图说明
14.图1为本发明一实施例提供的线路板的制备方法的流程示意图。
15.图2为图1中步骤s1之于一基材上形成导电层的示意图。
16.图3为图1中步骤s2之于所述导电层上形成保护层的示意图。
17.图4为图1中步骤s3之图案化所述导电层中,压干膜的示意图。
18.图5为图1中步骤s3之图案化所述导电层中,曝光的示意图。
19.图6为图1中步骤s3之图案化所述导电层中,显影的示意图。
20.图7为图1中步骤s3之图案化所述导电层中,蚀刻的示意图。
21.图8为图1中步骤s3之图案化所述导电层中,去干膜以及去保护层后的示意图。
22.图9为本发明一实施例的线路板的平面示意图。
23.图10为本发明另一实施例的线路板的制备方法中,形成贯穿第一导电层和基材的开孔的剖面示意图。
24.图11为于图10中第一导电层和第二导电层上形成保护层的剖面示意图。
25.图12为于图11中形成第三导电层并图案化所述第一导电层、所述第二导电层及所述第三导电层后的剖面示意图。
26.主要元件符号说明
27.线路板
ꢀꢀꢀꢀꢀꢀꢀꢀꢀꢀꢀꢀꢀꢀꢀꢀꢀꢀꢀ
100
28.基材
ꢀꢀꢀꢀꢀꢀꢀꢀꢀꢀꢀꢀꢀꢀꢀꢀꢀꢀꢀꢀꢀ
10
29.线路区
ꢀꢀꢀꢀꢀꢀꢀꢀꢀꢀꢀꢀꢀꢀꢀꢀꢀꢀꢀ
101
30.周边区
ꢀꢀꢀꢀꢀꢀꢀꢀꢀꢀꢀꢀꢀꢀꢀꢀꢀꢀꢀ
102
31.第一表面
ꢀꢀꢀꢀꢀꢀꢀꢀꢀꢀꢀꢀꢀꢀꢀꢀꢀ
11
32.第二表面
ꢀꢀꢀꢀꢀꢀꢀꢀꢀꢀꢀꢀꢀꢀꢀꢀꢀ
12
33.侧面
ꢀꢀꢀꢀꢀꢀꢀꢀꢀꢀꢀꢀꢀꢀꢀꢀꢀꢀꢀꢀꢀ
13
34.开孔
ꢀꢀꢀꢀꢀꢀꢀꢀꢀꢀꢀꢀꢀꢀꢀꢀꢀꢀꢀꢀꢀ
14
35.过孔
ꢀꢀꢀꢀꢀꢀꢀꢀꢀꢀꢀꢀꢀꢀꢀꢀꢀꢀꢀꢀꢀ
15
36.导电层
ꢀꢀꢀꢀꢀꢀꢀꢀꢀꢀꢀꢀꢀꢀꢀꢀꢀꢀꢀ
20
37.第一导电层
ꢀꢀꢀꢀꢀꢀꢀꢀꢀꢀꢀꢀꢀꢀꢀ
22
38.第二导电层
ꢀꢀꢀꢀꢀꢀꢀꢀꢀꢀꢀꢀꢀꢀꢀ
24
39.第三导电层
ꢀꢀꢀꢀꢀꢀꢀꢀꢀꢀꢀꢀꢀꢀꢀ
26
40.保护层
ꢀꢀꢀꢀꢀꢀꢀꢀꢀꢀꢀꢀꢀꢀꢀꢀꢀꢀꢀ
30
41.线路层
ꢀꢀꢀꢀꢀꢀꢀꢀꢀꢀꢀꢀꢀꢀꢀꢀꢀꢀꢀ
40
42.第一线路层
ꢀꢀꢀꢀꢀꢀꢀꢀꢀꢀꢀꢀꢀꢀꢀ
42
43.第二线路层
ꢀꢀꢀꢀꢀꢀꢀꢀꢀꢀꢀꢀꢀꢀꢀ
44
44.强化层
ꢀꢀꢀꢀꢀꢀꢀꢀꢀꢀꢀꢀꢀꢀꢀꢀꢀꢀꢀ
50
45.干膜
ꢀꢀꢀꢀꢀꢀꢀꢀꢀꢀꢀꢀꢀꢀꢀꢀꢀꢀꢀꢀꢀ
60
46.图案化的干膜
ꢀꢀꢀꢀꢀꢀꢀꢀꢀꢀꢀꢀꢀ
62
47.如下具体实施方式将结合上述附图进一步说明本发明。
具体实施方式
48.下面将结合本发明实施例中的附图,对本发明实施例中的技术方案进行清楚、完整地描述,显然,所描述的实施例是本发明一部分实施例,而不是全部的实施例。
49.除非另有定义,本文所使用的所有的技术和科学术语与属于本发明的技术领域的技术人员通常理解的含义相同。本文中在本发明的说明书中所使用的术语只是为了描述具体的实施例的目的,不是旨在于限制本发明。
50.为能进一步阐述本发明达成预定目的所采取的技术手段及功效,以下结合附图及较佳实施方式,对本发明作出如下详细说明。
51.图1为本发明一实施例提供的线路板的制备方法的流程示意图。如图1所示,该线路板的制备方法包括以下步骤:
52.步骤s1:于一基材上形成导电层;
53.步骤s2:于所述导电层上形成保护层;
54.步骤s3:图案化所述导电层。
55.以下结合附图具体说明该线路板的制备方法。
56.步骤s1:于一基材上形成导电层。
57.如图2所示,在步骤s1中,提供基材10,于基材10上形成导电层20。所述基材10定义有线路区101以及围绕所述线路区101的周边区102。基材10包括相对的第一表面11和第二表面12以及连接所述第一表面11和第二表面12的侧面13。图2中,侧面13连接并环绕所述周边区102。所述导电层20位于所述侧面13、第一表面11的所述周边区102以及第一表面11的所述线路区101。即,导电层20覆盖第一表面11并延伸覆盖基材10的侧面13。
58.于一实施例中,基材10大致呈矩形,导电层20覆盖基材10的整个第一表面11并延伸覆盖基材10的四个侧面13。
59.于一实施例中,基材10的材质为聚对苯二甲酸乙二醇酯、聚萘二甲酸乙二醇酯、聚酰亚胺、液晶聚合物及聚酰胺树脂中的任意一种。
60.于一实施例中,导电层20的材质为溅射铜、电镀铜或压延铜箔中的任意一种。
61.步骤s2:于所述导电层上形成保护层;
62.如图3所示,在步骤s2中,于所述导电层20上形成保护层30。所述保护层30位于所述侧面13以及所述周边区102。保护层30部分覆盖位于第一表面11上的导电层20并延伸覆盖位于侧面13上的导电层20。在沿基材10的厚度方向上的剖面图中,保护层30大致呈l型。
63.于一实施例中,基材10大致呈矩形,保护层30覆盖基材10的第一表面11上靠近四个边缘的导电层20以及基材10的四个侧面13的导电层20。
64.于一实施例中,保护层30的材质为热塑性可剥离胶,形成所述保护层30的步骤包括于所述导电层20上涂布所述可剥离胶并对所述可剥离胶进行紫外光固化。
65.于一实施例中,可采用3d涂布机,对基材10的边缘进行3d立体涂布保护层30,且涂布的保护层30的宽度及厚度可以根据需要进行控制。另,可采用紫外光(uv)固化机,对涂布的可剥离胶进行阶段性固化。
66.步骤s3:图案化所述导电层。
67.于一实施例中,图案化所述导电层20包括压干膜60、曝光、显影、蚀刻以及去干膜60。
68.如图4所示,干膜60形成于导电层20远离基材10的表面,至少位于线路区101。图4中,干膜60部分覆盖位于周边区102的保护层30。于其他实施例中,干膜60也可以不覆盖保护层30。
69.如图5所示,在干膜60远离基材10的一侧进行曝光。如图6所示,显影步骤后,得到图案化的干膜62。
70.如图7所示,蚀刻步骤后,导电层20的未被所述图案化的干膜62覆盖的部分以及未被所述保护层30覆盖的部分被移除。
71.如图8所示,去除所述图案化的干膜62以及保护层30。即,所述保护层30在所述去干膜60步骤中一并移除。其中,位于所述线路区101的所述导电层20被图案化后形成线路层40,而位于所述侧面13以及第一表面11的所述周边区102的导电层20由于被所述保护层30覆盖而未被图案化且仍留在所述基材10上形成一强化层50。所述线路层40和所述强化层50间隔并绝缘设置。图8中,强化层50覆盖基材10的第一表面11的周边区102,并延伸覆盖基材10的侧面13,以增强线路板100在板边的强度。
72.如图9所示,线路板100中,在线路区101,线路层40具有多条导线;在周边区102,基材10的四个边缘仍保留有导电层20构成的强化层50。如此,通过在基材10的侧面13及周边区102形成导电层20,且在图案化所述导电层20之前,于基材10的边缘涂布保护层30,使得获得的线路板100在板边及侧面13仍保留有导电层20,提高了线路板100板边刚性,解决了线路板100(尤其是厚度小于等于40微米的超薄型线路板)在制程中存在的板裂、板破的问题,进而避免了板边暴露出的基材10产生的碎屑掉落后,造成的线路污染和刮伤等问题,提高了整体良率。
73.于另一实施例中,如图10所示,形成所述导电层20的步骤中,所述导电层20还自所述侧面13延伸覆盖至所述第二表面12的所述周边区102以及所述第二表面12的所述线路区101。即,导电层20形成于基材10的第一表面11、第二表面12及侧面13。定义位于所述第一表面11上的所述导电层20为第一导电层22,位于所述第二表面12上的导电层20为第二导电层24。位于线路区101的第一导电层22用于后续图案化后形成第一线路层42,位于线路区101的第二导电层24用于后续图案化后形成第二线路层44。
74.请继续参阅图10,在图案化所述导电层20之前,还包括于所述线路区101形成贯穿所述第一导电层22和所述基材10的开孔14。开孔14的形状不作限制,其可以为圆孔、椭圆孔等。
75.于一实施例中,通过激光成孔的方式形成所述开孔14。于其他实施例中,可通过其他方式形成所述开孔14,如机械钻孔、冲压成型等。
76.如图11所示,在形成开孔14后,图案化导电层20之前,于导电层20上形成保护层30。保护层30部分覆盖第一导电层22、延伸覆盖基材10的侧面13上的导电层20以及部分覆盖第二导电层24。在沿基材10的厚度方向上的剖面图中,保护层30大致呈“c”型。其中,若基材10大致呈矩形,则保护层30覆盖基材10的第一表面11的四个边缘、四个侧面13以及第二表面12的四个边缘。
77.于一实施例中,在图案化导电层20之前,还包括于所述线路区101形成覆盖所述第一导电层22、填充所述开孔14且连接所述第二导电层24的第三导电层26。即,开孔14处通过填充第三导电层26形成过孔15,以电性连接第一导电层22和第二导电层24。其中,第三导电
层26的材质为电镀铜,也可以为其他金属合金。即,第三导电层26的材质可以与第一导电层22、第二导电层24的材料相同,也可以不同。
78.如图12所示,所述第一导电层22、所述第二导电层24以及所述第三导电层26被图案化。其中,基材10的第一表面11上的第一导电层22和所述第三导电层26经图案化后形成第一线路层42。基材10的第二表面12上的第二导电层24经图案化后形成第二线路层44,所述第一线路层42和所述第二线路层44通过过孔15电性连接。
79.由于基材10的侧面13及周边区102的导电层20在图案化步骤中,被保护层30覆盖,使得获得的线路板100在板边及侧面13仍保留有导电层20(即,强化层50),提高了线路板100板边刚性,解决了线路板100(尤其是厚度小于等于40微米的超薄型线路板)在制程中存在的板裂、板破的问题,进而避免了板边暴露出的基材10产生的碎屑掉落后,造成的线路污染和刮伤等问题,提高了整体良率。
80.另外,在形成开孔14后于基材10的边缘及侧面13形成了保护层30,除了加强基材10边缘的韧性,降低传送过程中碰撞造成基材10破裂的风险外,同时还使得后续图案化过程中,能够保留基材10的边缘及侧面13的导电层20,避免露出基材10的边缘,进而避免了在后续工段中因碰撞造成的基材10污染和刮伤问题,大幅改善了线路板100(尤其是超薄线路板100)的生成可行性,提升良率。
81.本发明一实施例还提供上述方法制得的所述线路板100。如图9所示,线路板100包括基材10、线路层40以及强化层50。所述基材10定义有线路区101以及围绕所述线路区101的周边区102。如图8所示,所述基材10具有连接并环绕所述周边区102的侧面13。所述基材10具有相对的第一表面11及第二表面12,所述侧面13连接所述第一表面11及所述第二表面12。线路层40位于所述线路区101强化层50位于所述侧面13以及所述周边区102。所述线路层40位于所述第一表面11,所述强化层50自所述第一表面11延伸覆盖所述侧面13。于另一实施例中,如图12所示,所述线路层40包括位于所述第一表面11的第一线路层42以及位于所述第二表面12的第二线路层44,所述第一线路层42和所述第二线路层44通过形成在所述基材10上的过孔15进行电性连接。所述强化层50自所述第一表面11延伸覆盖所述侧面13以及所述第二表面12。
82.该线路板100,其基材10的侧面13及周边具有强化层50,提高了线路板100板边刚性,解决了线路板100(尤其是厚度小于等于40微米的超薄型线路板)在制程中存在的板裂、板破的问题,进而避免了板边暴露出的基材10产生的碎屑掉落后,造成的线路污染和刮伤等问题,提高了整体良率。
83.以上实施方式仅用以说明本发明的技术方案而非限制,尽管参照较佳实施方式对本发明进行了详细说明,本领域的普通技术人员应当理解,可以对本发明的技术方案进行修改或等同替换,而不脱离本发明技术方案的精神和范围。