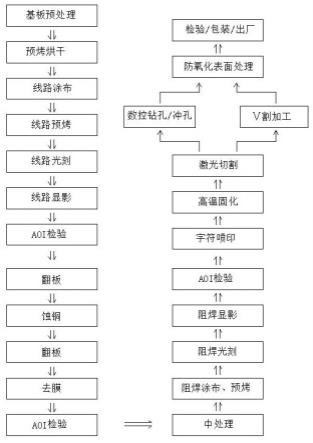
1.本发明属于线路板加工技术领域,尤其涉及一种基于光刻工艺的大尺寸单面线路板制备方法。
背景技术:2.线路板又称印制电路板或印刷电路板,简称pcb(printed circuit board),是电子元器件之间电气连接的载体,是电子工业的重要部件之一。单面线路板具有低成本的优势,在很多技术领域都有着广泛的应用。随着电子产品应用技术的不断进步,对高精度、大尺寸单面线路板的需求不断提升。
3.现有技术中,单面线路板制备工艺的自动化程度不高,目前,还没有全自动化的单面线路板生产线,导致生产效率较低以及生产成本相对较高,同时也使线路板的精度和尺寸均存在瓶颈;现有单面板工艺中,通常只能制备小尺寸线路板,主要原因在于,现有线路层制备采用曝光工艺,大尺寸的菲林容易发生形变,在曝光过程中由于光线的折射,造成线路图形线宽减少,使线路存在线宽不足、开路等风险,无法制备大尺寸的精密线路板。为此,现有工艺首先需要将标准基板材切割为相应尺寸的小板,这不仅增加了工艺的复杂度,同时在一定程度上,也造成了板材的浪费。如果能够采用大尺寸线路板,就能通过图形拼接,最大限度的利用板材空间,进一步降低生产成本。
4.故,本领域急需一种自动化大尺寸线路板的制备技术,以解决现有技术存在的技术问题。
技术实现要素:5.针对现有技术存在的问题,本发明提供的一种基于光刻工艺的大尺寸单面线路板生产工艺,采用光刻工艺实现线路转印,从而无需受限于菲林尺寸的限制,能够非常方便的实现高精度大尺寸线路层的制备;同时,为了适应大尺寸线路板的生产需求,对现有生产线的诸多环节作出了改进,最终实现了全自动化大尺寸高精密线路板生产线。
6.本发明解决其技术问题所采用的技术方案是: 一种基于光刻工艺的大尺寸单面线路板生产工艺,包括以下步骤:(1)基板预处理:使用机械臂把待加工的基板板直接移送至传送带上,对标准基板进行抛刷及水洗及风干,去除板面污渍;(2)线路涂布、光刻:涂布机在覆铜板面上均匀在涂一层线路油墨,并使用光刻机进行光刻;(3)线路显影:将基板置于显影机中进行显影处理,把没有光刻到的油墨进行去除处理;(4)蚀铜:把没有油墨保护的铜面用强酸或者强碱进行化学反应去除掉,只保留下有油墨保护的图形;(5)去膜:把基板上保护铜线的线路油墨去除,将铜线全部显露出来;
(6)阻焊涂布、预烤:使用涂布机将基板上铜线面的整面涂覆阻焊油墨,并进行烘烤;(7)阻焊光刻:通过光刻机对基板进行光刻;(8)阻焊显影:将烘烤后的基板置于显影机中进行显影处理,把没有光刻到的油墨进行去除处理,留下光刻后的图形;(9)高温固化:将基板传送至高温固化炉,进行高温固化后,使阻焊油墨彻底固化,增加与基板间的粘合力;(10)切割:使用激光切割机将大尺寸的pcb板切割成相应的小板或成品。
7.优选的,相邻工序间的传送装置采用伸缩式传送装置。
8.优选的,所述步骤2和步骤7的工序中采用采用双层传输。
9.优选的,相邻工序间设置有暂存装置。
10.优选的,所述步骤1至步骤10中,基板进入下一道工序前进行归中处理。
11.优选的,所述步骤2、步骤7和步骤9完成后分别对基本进行冷却处理。
12.优选的,所述步骤5中,在完成去膜后,对基板进行抛刷、水洗及风干,去基板表面的污渍。
13.优选的,所述基板清洗后进行粘尘处理。
14.优选的,所述步骤4中,在基板蚀铜前将基板翻转180度,从下方下喷涂腐蚀液,提高腐蚀的效果,蚀铜完成后将基板翻转180度,使覆铜面向上,满足上刷洗去膜的需要。
15.优选的,所述步骤2和步骤7中光刻均采用光刻机进行光刻。
16.本发明的有益效果是:本技术技术方案提出了一种全自动大尺寸单面线路板的生产线,从而能够进一步提升单面线路板的性能和生产效率,进一步降低了单面线路板的生产成本;本技术工艺中采用光刻工艺实现线路转印,从而无需受限于菲林尺寸的限制,能够非常方便的实现高精度大尺寸线路层的制备;同时,为了适应大尺寸线路板的生产需求,对现有生产线的诸多环节作出了改进,其中,通过设置有伸缩式传送装置,伸缩式传送装置实现全自动转向,进而方便生产线的布置与规划以及传动装置的移动,提高设备的利用率;通过设置有双层传输装置,双层传输装置配合机械手提高生产效率,同时方便管理进料和出料;通过暂存装置可以短暂的存储一定量的基板;当下一道工序设备出现问题时,可以通过控制器给暂存装置发送信号,暂存装置接受到信号后上开始存储基板,进而方便线路板的加工;在基板蚀铜前通过翻板机将基板翻转180度,从下方下喷涂腐蚀液,提高腐蚀的效果。
附图说明
17.图1为本发明中伸缩式传动送装置的结构示意图;图2为图1中固定架结构示意图;图3为图2中移动组件结构示意图;图4为本发明中双层传输装置的结构示意图;图5为图4的俯视示意图;图6为本发明中暂存装置的结构示意图;图7为本发明的工艺流程图;图8为蚀刻装置结构示意图。
具体实施方式
18.下面结合实施例对本发明做进一步的详细描述,但本发明的保护范围并不限于此。
19.参见图7,所示为本发明涉及一种基于光刻工艺的大尺寸单面线路板制备方法的流程框图,包括以下步骤:(1)基板预处理:使用机械臂把待加工的基板板直接移送至传送带上,对标准基板进行抛刷及水洗及风干,去除板面污渍;现有技术工艺通常先将标准基板切割为相应尺寸的小板后再进行加工,而本技术直接对标准基板(通常是1.2m*1.2m)进行处理。由于本技术工艺是基于标准基板直接进行制备,能够省去对板材进行切割的步骤,一定程度上简化了制备工艺,同时大尺寸线路板有助于线路层的拼接,能够充分利用基板尺寸。
20.(2)线路涂布、光刻:涂布机在覆铜板面上均匀在涂一层厚度为0.01mm线路油墨,并使用光刻机进行光刻;由于本技术采用光刻工艺制备线路层,能够进一步提升线路精度,同时,能够非常方便的实现线路拼板并省去了菲林的制备,使线路层尺寸不受限于菲林的瓶颈,能够非常方便的实现大尺寸线路板的制备。
21.在一种优选实施方式中,线路光刻采用多台光刻机同时进行光刻,提升线路光刻速度,以满足整个自动化生产线的需求。
22.(3)线路显影:将基板置于显影机中进行显影处理,把没有光刻到的油墨进行去除处理;(4)蚀铜:把没有油墨保护的铜面用强酸或者强碱进行化学反应去除掉,只保留下有油墨保护的图形;(5)去膜:把基板上保护铜线的线路油墨去除,将铜线全部显露出来;(6)阻焊涂布、预烤:使用涂布机将基板上铜线面的整面涂覆阻焊油墨,并进行烘烤;(7)阻焊光刻:通过光刻机对基板进行光刻;在本技术中,阻焊层的制备也采用光刻工艺,能够进一步提升生产线的自动化程度以及阻焊层的精度;(8)阻焊显影:将烘烤后的基板置于显影机中进行显影处理,把没有光刻到的油墨进行去除处理,留下光刻后的图形;(9)高温固化:将基板传送至高温固化炉,进行高温固化后,使阻焊油墨彻底固化,增加与基板间的粘合力;(10)切割:使用激光切割机将大尺寸的pcb板切割成相应的小板或成品。
23.在本实施方式中,使用大尺寸的基板,一次加工若干个小的线路板,加工完成后对基板进行切割,进而一次加工若干的线路板。本技术通过线路拼板能够进一步充分利用基板空间,进一步降低了线路板的生产成本,同时也提升了生产效率。
24.现有单面线路板工艺都是基于小尺寸线路板的制备,为了适应大尺寸线路板的生产需求,实现了全自动化大尺寸高精密线路板生产线,本技术对现有生产线的诸多环节均作出了相应改进,具体参见以下描述。
25.现有蚀刻机均是基于小尺寸线路板,在大尺寸线路板制备中,会导致蚀刻不均匀进而导致线路板性能下降。为此,本技术对现有蚀刻工艺作出了相应的改进。首先,本发明采用多台蚀刻机级联工作,线路板在蚀刻流程中将经过多台蚀刻机,从而能够保证大尺寸
线路板充分蚀刻,同时,多台蚀刻机通过同一个容器提供蚀刻液,从而保证不同蚀刻机中溶液浓度的一致性、以及进料量保持一致,进而大大提高线路板的性能。
26.如图8所示,4台蚀刻机连接在一起,通过对pcb板进行蚀刻,四个蚀刻机的一侧连接有容器1201,容器内盛放有蚀刻液,容器内部连接有搅拌装置1202,通过搅拌装置对蚀刻液进行搅拌,防止蚀刻液出现沉淀,影响pcb板的质量;容器上连接有泵1203,泵上连接有四根连接管1204,四个连接管分别连接至蚀刻机1205,进而使每台蚀刻机1205内的蚀刻液的浓度保持一致,提高pcb板的质量。
27.由于本技术线路层制备采用光刻工艺,单台光刻机的光刻效率无法满足全自动化生产线工艺的要求,因此,在实际光刻流程中,采用多台光刻机配合机械手协同进行光刻,为了保证光刻流程有序进行,本技术对生产线进行了改进,提出了一种双层传输装置,进料和出料分别设置在上层和下层,从而保证生产流程有序,方便自动化生产线的管理。
28.进一步的,在步骤2和步骤7的工序中采用采用双层传输。
29.如图4、5所示,图4为双层传输装置的结构示意图,在步骤2和步骤3中,为了提高企业的生产效率,从而多台光刻机同时工作,为了机器手与多台光刻机交互的时候有序的进料和出料,机器手从下层拿取线路板,光刻机加工完毕后,放到上层进入下一工序,这样能够方便管理进料和出料,大大提高了企业的生产效率。
30.在本实施方式中,第一固定架91的顶端连接有第一传送装置92,第一传送装置92的顶端连接有第二传送装置93,第一传送装置92的一端或者两个连接若干置料架94,置料架94的数量可以根据下移到工序的产线确定数量,第一传送装置92上对应置料架4的位置设置有转向装置95,通过转向装置95可以将第一转运装置92上的pcb板转送至置料架94上,进而使pcb自动转向至置料架94上,第一传送装置92用于进料,第二传送装置93用于出料,进而减少传送装置占地面积,充分利用有限的空间;通过双层物料传输架以及置料架实现物料快速自动运输,大大提高物料输送的效率,进而大大提高生产效率。
31.在本实施方式中,双层传输装置的控制方法如下:(1)pcb板在第一传送装置传送,第一传感器记录第一传送装置上pcb板的数量,并向控制器发送第一传送装置上有待加工的pcb板的信号;(2)任一第二传感器判断相应的置物上是否有待加工的pcb板,并将信号传送至转向装置和光刻机,当第二传感器发送需要pcb板的信号时,转向装置将第一传送装置上的pcb板分流至置物架上;(3)置物架输送pcb板,并向光刻机发送信号,光刻机判断是否需要pcb板,当光刻机需要pcb板时,光刻机给机械手发送信号;(4)机械手接受到信号,机械手将置物架上的pcb板移动至相应的光刻机上;(5)待光刻机完成pcb板加工后,光刻机给第二传送装置上的第一传感器发送信号,当第二传送装置上没有pcb板传输时,机械手将pcb移动至第二传送装置上,pcb板通过第二传送装置输送至下一道工序。
32.在本实施方式中,上一工序的基板进入双层传送的第一层传送时,双层传送的第一层传送开启,滚筒转动,基板再经过转角传送进入取料区并发给机械臂可取料信号;光刻机开启加工进入待料信号,光刻机给机械臂发出要料信号,机械臂确认取料区有料可以抓取,机械臂到取料区进行取料,然后把基板放在光刻机加工台面上,光刻机开启真空吸住板
料后机械臂离开完成放料动作,光刻机开启加工,光刻机加工完成后,发取料信号给机械臂,机械臂将光刻机台面上加工完成的基板取走,机械臂发信号给双层传送确认是否可以放板料在双层传送的第二层出料放板区,确认第二层出料放板区没有板料的情况下,确认机械臂可以把板料放在第二层出料放板区;机械臂放料完成后给双层传送一个放板完成信号,双层传送出料滚筒转动,将板料传送到下一个工位。
33.在本实施方式中,pcb板在第一传送装置,第一传送架上的pcb板移动至相应的置料架的一侧时,第一传感器和第二传感器同时检测到pcb板以及控制器的信号时,相应的传送架上的驱动装置停止工作,转向装置开始工作,进而将pcb板输送置料架上,当置料架上第三传感器检测到pcb板时,相应的置料架上的驱动装置开始工作,对pcb板进行运输,当pcb板输送至相应的位置时,机械手将pcb板转移至对应的生产线上,当pcb加工完成后,机械手将pcb板移动至第二传送装置3上,进而输送下一生产工序。
34.进一步的,为了适应全自动大尺寸线路板生产线的要求,相邻工序间的传送装置采用伸缩式传送装置。
35.如图1、2、3所示,图1为伸缩式传动送装置,相邻的工序间通过伸缩式传送装置进行连接,可以为后续生产线改造留有空间,同时方便的移除,从而有空间增加新的工序;当后一道生产工序的设备故障时,可快速的将传输线断开,方便进行人工操作。
36.在本实施方式中,伸缩式传送装置采用独立电滚筒转动,多个电滚筒一起形成传送带;同时伸缩式传送装置实现全自动转向,进而方便产线的布置与规划以及传动装置的移动,提高设备的利用率。
37.在本实施方式中,相邻位置的固定架1间连接有活动架4,任一固定架1上连接有第一连接杆3,活动架4上连接有第二连接杆5,第一连接杆4与第二连接杆5间连接有支撑组件6,通过支撑组件6方便固定架1和活动架4的移动,进而方便传动装置的伸缩,任一固定架1的底端连接有移动组件2,通过移动组件2,进而方便通过控制器控制传动装置的调节,大大提高传动装置调节的精度,降低人工操作时的误差,固定架1和活动架4的顶端分别连接有传动组件7,通过传动组件7方便pcb板的移动;固定架4底部连接有移动组件2,进而固定架1可以移动且可以进行伸缩,传送装置可以实现转向传送,进而方便产线的布置与规划以及传动装置的移动,提高设备的利用率;伸缩式传送装置可以方便的移除,从而有空间增加新的工序;同时当后级设备故障时,可快速的将传输线断开,方便进行人工操作。
38.在本实施方式中,固定架1的下部内侧连接有第一驱动电机21,第一驱动电机21的输出端连接有转动杆22,转动杆22的底端连接有壳体23,壳体23上转动连接有滚轮24,通过第一驱动电机21带动滚轮24转动方向,从而方便调节传动装置,壳体23的内侧壁上连接有第二驱动电机25,第二驱动电机25的输出端连接有齿轮26,滚轮24一侧的支杆上开设有槽齿27,槽齿27与齿轮26齿合,进而通过第二驱动电机25可以带动滚轮转动,进而方便固定架1的移动;转动杆22的外侧壁上连接支撑块28,支撑块28与固定架1滑动连接,进而在转动杆22转动时提供支撑作用;转动杆22的上部侧壁上连接有角度传感器29,通过角度传感器29检测转动杆22转动的角度,进而可以精确调节滚轮24的转动角度。
39.在本实施方式中,任一传动组件7包括滚筒71,滚筒71的一端固定架1或活动架4转动连接,滚筒71的另一端连接有第三驱动电机72,第三驱动电机72固定在固定架1或活动架4上,第三驱动电机72连接至控制器。
40.进一步的,为了适应全自动大尺寸线路板生产线的要求,相邻工序间设置有暂存装置。
41.如图6所示,图6为暂存装置的结构示意图, 相邻工序间都连接有暂存装置,通过暂存装置可以短暂的存储一定量的基板;当下一道工序设备出现问题时,可以通过控制器给暂存装置发送信号,暂存装置接受到信号后上开始存储基板,进而方便线路板的加工。
42.在本实施方式中,在步骤1至步骤10中,基板进入下一道工序前进行归中处理,归中装置将基板的位置纠正在传送装置的中部,方便人工目测检查基板的情况和及时对板料进行合理处理,同时方便基板的加工,在本实施方式中,所述步骤2、步骤6和步骤9完成后分别对基本进行冷却处理,冷却时通过冷却料架对基板进行冷却,冷却料架上可以容纳若干基板,冷却料架位于密封的空间中,空间内部通过空调对空间内输出冷气,通过冷却料架上安装有散热风扇,加速基板的散热效率,通过对基板进行散热,方便下一道工序的加工,快速完成基板的散热,提高基板加工的精度,进而提高基板加工的良品率。
43.在本实施方式中,步骤5中,在完成去膜后,对基板进行抛刷、水洗及风干,去基板表面的污渍。
44.在本实施方式中,基板清洗后使用粘尘机把板面进行粘尘处理,防止表面残留粉尘等,为涂覆阻焊油墨做表面清洁保护处理。
45.在本实施方式中,步骤4中,在基板蚀铜前通过翻板机将基板翻转180度,从下方下喷涂腐蚀液,提高腐蚀的效果,蚀铜完成后将基板翻转180度,使覆铜面向上,满足上刷洗去膜的需要。
46.在本实施方式中,所述步骤2和步骤7中均采用光刻机进行光刻。
47.以上所述的实施例只是本发明的一种基于光刻工艺的大尺寸单面线路板制备方法较佳的方案,并非对本发明作任何形式上的限制,在不超出权利要求所记载的技术方案的前提下还有其它的变体及改型。