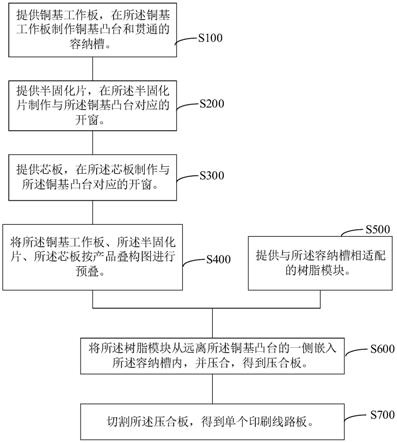
1.本发明涉及印刷电路板技术领域,尤其是涉及一种印刷线路板的制作方法及印刷线路板。
背景技术:2.随着电子通讯行业及车载电子不断发展,相关的pcb产品(printed circuit board,印刷电路板,又称印刷线路板)要求趋向于小型化,多功能化,可立体组装,散热性能要求越来越高。
3.现行业内高散热性能的pcb产品以埋嵌铜块的pcb为主,此类埋铜基凸台的pcb产品制作时,通常采用在fr
‑
4基板上埋嵌铜块,并露出铜块的凸台,依次放入均具有开窗的半固化片和柔性芯板,铆合对位,压合,得到压合板。
4.此种制作工艺仍然存在良品率低的技术问题,具体地,压合预叠铜块凸台与柔性芯板开窗及半固化片开窗容易偏位,导致铜块凸台不能与芯板开窗及半固化片开窗对位,铜块凸台位置无法嵌入在芯板开窗及半固化片开窗内,造成压合板报废。
技术实现要素:5.本发明的目的在于提供一种印刷线路板的制作方法及印刷线路板,旨在解决现有的印刷线路板制作良品率低的技术问题。
6.为实现上述目的,本发明采用的技术方案是:一种印刷线路板的制作方法,包括:
7.s100:提供铜基工作板,在所述铜基工作板制作铜基凸台和贯通的容纳槽;
8.s200:提供半固化片,在所述半固化片制作与所述铜基凸台对应的开窗;
9.s300:提供芯板,在所述芯板制作与所述铜基凸台对应的开窗;
10.s400:将所述铜基工作板、所述半固化片、所述芯板按产品叠构图进行预叠;
11.s500:提供与所述容纳槽相适配的树脂模块;
12.s600:将所述树脂模块从远离所述铜基凸台的一侧嵌入所述容纳槽内,并压合,得到压合板;
13.s700:切割所述压合板,得到单个印刷线路板。
14.在其中一个实施例中,在步骤s100中,所述铜基工作板在蚀刻缸内的传送速度控制在2m/min
‑
2.2m/min、上下压力控制在2kg/cm2‑
2.2kg/cm2,酸性蚀刻所述铜基工作板2次,每次蚀刻深度为0.1mm
‑
0.11mm;再继续以传送速度控制在3.5m/min
‑
3.7m/min、上下压力控制在2kg/cm2‑
2.2kg/cm2,酸性蚀刻所述铜基工作板一次,蚀刻深度为0.05mm
‑
0.052mm,得到所述铜基凸台。
15.在其中一个实施例中,在步骤s100中,在所述铜基工作板上锣出比所述树脂模块的尺寸单边大0.05mm
‑
0.075mm的所述容纳槽。
16.在其中一个实施例中,在步骤s100之后,将所述铜基工作板整板放置在磨板线,清理所述容纳槽的边缘残留披锋。
17.在其中一个实施例中,在步骤s400之前,在所述铜基工作板、所述半固化片和所述芯板的中间非单元区域均设置位置相互对应的第一铆合孔;
18.在步骤s400时,通过所述第一铆合孔将预叠后的所述铜基工作板、所述半固化片和所述芯板进行铆合。
19.在其中一个实施例中,步骤s300具体为:使用镭射钻孔机在所述芯板制作镭射孔;清理所述镭射孔的边缘残胶;清洗所述芯板;将所述镭射孔的孔壁导体化;利用vcp技术填充所述镭射孔;在所述芯板制作外层线路;使用通断测试检查所述外层线路是否存在短路;切割出所述芯板的开窗。
20.在其中一个实施例中,步骤s500具体为:裁切覆铜板;蚀刻所述覆铜板成树脂光板;在所述树脂光板的一面贴第一高温保护膜;将所述树脂光板锣成单个所述树脂模块;在所述树脂模块的另一面贴第二高温保护膜,并撕下所述第一高温保护膜;棕化。
21.在其中一个实施例中,在步骤s600之后,还包括:将所述压合板进行通断测试,以检测所述压合板的线路是否存在短路;
22.和/或,在步骤s600之后,还包括:将所述压合板进行四端子测试,以检测所述压合板的线路是否存在缺口或残铜。
23.在其中一个实施例中,所述芯板为柔性芯板,在步骤s600之后,在所述压合板的弯折区域进行控深锣,控深余厚为0.30mm
‑
0.35mm。
24.本发明还提供一种印刷线路板,该印刷线路板按照上述任意一项所述的印刷线路板的制作方法制成。
25.本发明提供的印刷线路板的制作方法及印刷线路板的有益效果是:采用在铜基工作板嵌树脂模块,铜基工作板、半固化片和芯板共用一套定位系统,保证铜基凸台与半固化片及芯板的开窗完全对准,避免铜基凸台和半固化片及芯板的开窗因容易偏位而报废,解决现有的印刷线路板制作良品率低的技术问题,从而提高了印刷线路板的良品率。
附图说明
26.为了更清楚地说明本发明实施例中的技术方案,下面将对实施例或现有技术描述中所需要使用的附图作简单地介绍,显而易见地,下面描述中的附图仅仅是本发明的一些实施例,对于本领域普通技术人员来讲,在不付出创造性劳动性的前提下,还可以根据这些附图获得其他的附图。
27.图1为本发明实施例提供的印刷线路板的制作方法中的凸台位置示意图;
28.图2为本发明实施例提供的印刷线路板的制作方法中的成品示意图;
29.图3为图2中的压合板的平面图;
30.图4为本发明实施例提供的印刷线路板的制作方法的流程图;
31.图5为图4中步骤s100的具体流程示意图;
32.图6为图4中步骤s200的具体流程示意图
33.图7为图4中步骤s300的具体流程示意图;
34.图8为图4中步骤s500的具体流程示意图。
35.其中,图中各附图标记:
36.10、第一铆合孔;20、弯折区域;30、第二铆合孔;
37.100、铜基工作板;110、铜基凸台;120、容纳槽;
38.200、半固化片;
39.300、芯板;310、介质层;320、芯板线路层;
40.400、树脂模块。
具体实施方式
41.下面详细描述本发明的实施例,所述实施例的示例在附图中示出,其中自始至终相同或类似的标号表示相同或类似的元件或具有相同或类似功能的元件。下面通过参考附图描述的实施例是示例性的,旨在用于解释本发明,而不能理解为对本发明的限制。
42.在本发明的描述中,需要理解的是,术语“长度”、“宽度”、“上”、“下”、“前”、“后”、“左”、“右”、“竖直”、“水平”、“顶”、“底”“内”、“外”等指示的方位或位置关系为基于附图所示的方位或位置关系,仅是为了便于描述本发明和简化描述,而不是指示或暗示所指的装置或元件必须具有特定的方位、以特定的方位构造和操作,因此不能理解为对本发明的限制。
43.此外,术语“第一”、“第二”仅用于描述目的,而不能理解为指示或暗示相对重要性或者隐含指明所指示的技术特征的数量。由此,限定有“第一”、“第二”的特征可以明示或者隐含地包括一个或者更多个该特征。在本发明的描述中,“多个”的含义是两个或两个以上,除非另有明确具体的限定。
44.在本发明中,除非另有明确的规定和限定,术语“安装”、“相连”、“连接”、“固定”等术语应做广义理解,例如,可以是固定连接,也可以是可拆卸连接,或成一体;可以是机械连接,也可以是电连接;可以是直接相连,也可以通过中间媒介间接相连,可以是两个元件内部的连通或两个元件的相互作用关系。对于本领域的普通技术人员而言,可以根据具体情况理解上述术语在本发明中的具体含义。
45.请参考图1至图4,一种印刷线路板的制作方法,包括:
46.s100:提供铜基工作板100,在铜基工作板100制作铜基凸台110和贯通的容纳槽120。其中,铜基凸台110的数量为若干个,比如一个、两个或多个。一般地,铜基凸台110的数量为多个。容纳槽120的数量为若干个,比如一个、两个或多个。
47.s200:提供半固化片200,在半固化片200制作与铜基凸台110对应的开窗。
48.s300:提供芯板300,在芯板300制作与铜基凸台110对应的开窗。
49.s400:将铜基工作板100、半固化片200、芯板300按产品叠构图进行预叠。产品叠构图是指印刷线路板的叠构图,包括芯板300的数量,可以为两个以上。芯板300可选为双面板,芯板300两面的芯板线路层320之间通过介质层310连接。介质层310一般选用半固化片200。
50.s500:提供与容纳槽120相适配的树脂模块400。
51.其中,树脂模块400可以是环氧树脂的热固性树脂模块、聚酰亚胺的热塑性树脂模块、浸有增强材料的热固性树脂模块、或浸有增强材料的热塑性树脂模块。具体地,树脂模块400为fr
‑
4模块、abf模块、bt树脂模块。
52.s600:将树脂模块400从远离铜基凸台110的一侧嵌入容纳槽120内,并压合,得到压合板。
53.s700:切割压合板,得到单个印刷线路板。
54.传统的印刷线路板的制作方法中,铜块活动嵌在树脂板的开槽内,由于铜基凸台110的数量多、尺寸小,铜基凸台110的尺寸存在机器加工误差,将如此多的铜块人工嵌入树脂板中,极易导致铜基凸台110的位置跑偏。半固化片200及芯板300和树脂板共用一套定位系统,半固化片200及芯板300根据定位系统定位叠放在树脂板上,而不是参考铜基凸台110的位置定位叠放在树脂板上,导致半固化片200及芯板300的开窗与铜块的铜基凸台110容易偏位,产品报废。而且,由于在树脂板上设置嵌铜块的开槽,芯板300、半固化片200和树脂板在压合过程中,熔融状态的半固化片200会挤入树脂板用于嵌铜块的开槽内,消耗半固化片200,导致压合后铜基凸台110位置因填胶不足出现压合空洞,进而导致后续蚀刻线路时药水进入印刷线路板的内层而造成产品报废。
55.本实施例介绍的印刷线路板的制作方法中,采用在铜基工作板100上嵌树脂模块400,铜基工作板100及铜基凸台110的位置固定,铜基工作板100、半固化片200和芯板300共用一套定位系统,保证铜基凸台110与半固化片200及芯板300的开窗完全对准,避免铜基凸台110和半固化片200及芯板300的开窗因容易偏位而报废,解决现有的印刷线路板制作良品率低的技术问题,从而提高了印刷线路板的良品率。
56.此外,采用上述印刷线路板的制作方法制作印刷线路板,无需在树脂板上设置嵌铜块的开槽,在铜基工作板100、半固化片200、芯板300按产品叠构图进行预叠并压合过程中,无需消耗熔融状态的半固化片200,避免铜基凸台110位置因填胶不足而造成的产品报废。
57.在其中一个实施例中,可参考图5中的步骤s104,在步骤s100中,铜基工作板100在蚀刻缸内的传送速度控制在2m/min
‑
2.2m/min、上下压力控制在2kg/cm2‑
2.2kg/cm2,酸性蚀刻铜基工作板1002次,每次蚀刻深度为0.1mm
‑
0.11mm;再继续以传送速度控制在3.5m/min
‑
3.7m/min、上下压力控制在2kg/cm2‑
2.2kg/cm2,酸性蚀刻铜基工作板100一次,蚀刻深度为0.05mm
‑
0.052mm,得到铜基凸台110。
58.相比在小铜块上加工铜基凸台110,通过多次蚀刻去除材料的方式,在铜基工作板100形成该铜基凸台110,能够批量化得到尺寸稳定的铜基凸台110,自动化水平高、良品率高。
59.其中,铜基凸台110的深度为0.25mm
‑
0.26mm。铜基凸台110的形状不限于方形凸台,也可以是圆形凸台、或其他异形凸台。
60.在其中一个实施例中,在步骤s100中,在铜基工作板100上锣出比树脂模块400的尺寸单边大0.05mm
‑
0.075mm的容纳槽120,便于树脂模块400能够顺畅地装入容纳槽120内,且树脂模块400与容纳槽120的槽壁之间的间隙合适。
61.其中,单边是指每一条边,即容纳槽120的形状与树脂模块400的形状相同,且容纳槽120的每一条边都比树脂模块400的每一条边的尺寸大0.05mm
‑
0.075mm。
62.具体地,可参考图5中的步骤s106,在步骤s100之后,将铜基工作板100整板放置在磨板线,清理容纳槽120的边缘残留披锋。
63.传统的制作方法需要制作多个、小单元尺寸的铜块,还需要对多个、小单元尺寸的铜块进行披锋处理,生产部门还需要制作专用载具辅助处理单个铜块披锋、并需要使用专用棕化载具辅助单个铜块制作铜块棕化流程。
64.本实施例介绍的印刷线路板的制作方法中,单个大尺寸的铜基工作板100磨板,无需制作磨板载具及棕化治具,利用水平磨板线即可,同时树脂模块400无需像铜块一样需要磨披锋及棕化。因此,上述印刷线路板的制作方法可减少因单个铜块需要过水平线磨披锋及过棕化线时的载具的投入,只需正常的整板过磨板线及棕化线即可完成铜基工作板100磨板,无需载具,同时也取消人工放铜块至载具上以及磨披锋后及棕化后从载具上取铜块的工作,大大提高了生产效率。
65.其中,披锋,又可称之为飞边、毛刺或溢边。
66.在其中一个实施例中,请参考图5,步骤s100具体为:
67.s101、开料。选取合适厚度的铜基板裁切成合适尺寸的铜基工作板100。比如,铜基板的厚度为1mm、1.5mm或2mm,铜基工作板100的尺寸为450mm
×
200mm、468mm
×
250mm或500mm
×
300mm。
68.s102、铜基钻孔。在铜基工作板100钻出的ldi定位孔、锣板定位孔、第一铆合孔10和第二铆合孔30。其中,ldi(laser direct imaging)是指激光直接成像技术。第一铆合孔10和第二铆合孔30是用于后续与芯板300及半固化片200铆合,相应地芯板300及半固化片200具有位置相应的第一铆合孔10和第二铆合孔30。
69.s103、外层线路。铜基工作板100利用ldi定位孔定位,然后采用ldi曝光在铜基工作板100做出铜基凸台110图形及保护菲林层图形。
70.s104、蚀刻凸台。
71.s105、锣板。根据所设定的树脂模块400的外形尺寸加工出容纳槽120。容纳槽120的尺寸比树脂模块400的单边尺寸大0.05mm
‑
0.075mm。
72.s106、磨板。可选地,使用不织布磨板线生产,只需将容纳槽120的边缘残留披锋清理干净即可。
73.s107、棕化。可选地,按照1.5m/min
‑
2.0m/min的棕化速度生产制作。此时,铜基工作板100整板过棕化线,不需要增加过棕化载具,简化生产工序,提高生产效率。
74.s108、烤板。烘烤棕化后铜基工作板100上残留水汽。
75.在其中一个实施例中,请参考图6,步骤s200具体为:
76.s201、开料。具体地,工作人员使用裁切机自动裁切出尺寸与铜基工作板100的尺寸相同的半固化片200。
77.s202、镭射开窗及钻孔。具体地,工作人员使用uv激光切割机生产,半固化片200的开窗尺寸比铜基凸台110的尺寸单边大0.075mm。同时,在半固化片200加工出第一铆合孔10和第二铆合孔30。
78.在其中一个实施例中,请参考图7,步骤s300具体为:
79.s301、开料。其中,工作人员使用自动剪切机裁出尺寸为与铜基工作板100的尺寸相同的芯板300。可选地,可以直接采购与铜基工作板100尺寸相同的芯板300,此步骤可省略。
80.s302、使用镭射钻孔机在芯板300制作镭射孔。其中,镭射孔的孔径可选为0.12mm、0.125mm或0.13mm。
81.s303、清理镭射孔的边缘残胶。具体地,使用等离子清理残胶。
82.s304、清洗芯板300。
83.s305、将镭射孔的孔壁导体化。
84.s306、利用vcp(vertical conveyor plating,连续垂直电镀)技术填充镭射孔。其中,填孔空洞≤25%,保证焊盘平整,焊盘凹陷深度≤25μm。
85.s307、在芯板300制作外层线路。其中,使用常规生产参数制作,不允许有干膜气泡、折皱、露铜等不良现象发生,曝光上下层不允许错位,显影后全检是否有开短路、曝光不良及显影不净等现象。
86.s308、外层酸性蚀刻。其中,当采用外层线路可以采用非酸性蚀刻方式制成,此步骤可省略。
87.s309、使用通断测试检查外层线路是否存在短路。其中,若使用aoi(automated optical inspection,自动光学扫描)检查外层线路是否存在短路,由于aoi扫描至镭射孔位置时,机器会出现无数个虚假报错,导致该流程无法正常生产。本实施例中,使用通断测试检查外层线路是否存在短路,能避免因大量虚假报错带来的繁重的工作量,同时通断路测试也能准确地找出不良位置,方便后续的修理及报废,提高了工作效率。
88.s310、切割出芯板300的开窗。具体地,利用uv切割机切割出开窗,开窗的尺寸比铜基凸台110的尺寸单边大0.075mm。同时,在芯板300切割出第一铆合孔10和第二铆合孔30。
89.s311、棕化。具体地,板厚0.05mm、两面铜厚1oz的柔性芯板,由于厚度偏薄,棕化需使用牵引板辅助生产。
90.在其中一个实施例中,请参考图8,步骤s500具体为:
91.s501、裁切覆铜板。
92.s502、蚀刻覆铜板成树脂光板。具体地,采用双面蚀刻,直接将覆铜板通过酸性蚀刻水平线蚀刻至树脂光板。
93.s503、在树脂光板的一面贴第一高温保护膜。可选地,利用自动贴膜机实现自动贴膜。
94.s504、将树脂光板锣成单个树脂模块400。可选地,利用使用可控深锣机生产。
95.s505、在树脂模块400的另一面贴第二高温保护膜,并撕下第一高温保护膜。
96.s506、棕化。棕化参数设定为3.5m/min生产,主要作用是清洗树脂模块400。
97.如此,采用上述步骤能够批量化、快速生产得到多个、小单元尺寸的树脂模块400。
98.在其中一个实施例中,请参考图3,在步骤s400之前,在铜基工作板100、半固化片200和芯板300的中间非单元区域均设置位置相互对应的第一铆合孔10。
99.在步骤s400时,通过第一铆合孔10将预叠后的铜基工作板100、半固化片200和芯板300进行铆合。
100.如此,铜基工作板100、半固化片200和芯板300的中间非单元区域通过第一铆合孔10铆合定位,芯板300能更牢固地与半固化片200及铜基工作板100或与其余各层芯板300结合在一起,在贴膜过程中不易被贴膜机拉扯、挤压而造成局部变形、移位、褶皱,从而大幅提高压合良率。因此,在步骤s400时,将铜基工作板100、半固化片200和芯板300进行铆合,能够有效地改善了芯板300在贴膜过程中导致局部变形而造成压合过程偏位及褶皱的问题,提高了产品良率。
101.此外,在铜基工作板100、半固化片200和芯板300的边缘位置还设置有位置相应的第二铆合孔30,使得铜基工作板100、半固化片200和芯板300铆合更加牢固。
102.其中,铜基工作板100、半固化片200和芯板300同时通过第一铆合孔10和第二铆合孔30铆合定位。
103.在其中一个实施例中,上述印刷线路板的制作方法中,在步骤s400之后,在步骤s600之前,在具有铜基凸台110的表面贴耐高温膜,以保护柔性芯板300。具体地,使用手动贴膜机自动贴膜,贴膜过程中需控制贴膜速度及贴膜压力,防止因贴膜速度过快,压力太大而导致柔性芯板300变形错位。
104.步骤s600具体包括:
105.步骤s601,将树脂模块400从远离铜基凸台110的一侧嵌入容纳槽120内。
106.步骤s602,在压合板的远离铜基凸台110的表面贴耐高温膜,以固定树脂模块400。
107.步骤s603,压合压合板。
108.步骤s604,撕下压合板的两侧的耐高温膜,削去铜基凸台110上的溢胶。具体地,使用陶瓷及不织布磨板打磨干净铜基凸台110上的溢胶。
109.步骤s605,钻孔,按常规pcb钻孔要求生产。其中,若钻铜基工作板100上的孔需分段钻孔,孔径大于3.0mm的孔需盖硬纸板生产,不允许偏孔及孔口披锋。
110.步骤s606,沉铜板电。
111.步骤s607,全板加厚。
112.步骤s608,外层线路。
113.步骤s609,外层蚀刻。蚀刻后aoi全检开路,短路及其他不良现象。
114.步骤s610,防焊。使用可弯折油墨生产,使用36t白网印刷一次,注意按客户要求管控油墨厚度,白色油墨需严格管控显影油墨侧蚀及板面外观不良。
115.步骤s611,文字。按常规pcb生产要求制作。
116.步骤s612,沉金。按常规pcb生产要求制作,金厚、镍厚需满足客户要求,为防止擦花大金面,沉金后需隔白纸。
117.在其中一个实施例中,上述印刷线路板的制作方法中,在步骤s600之后,还包括:将压合板进行通断测试,以检测压合板的线路是否存在短路,替代使用aoi测试,可减少报错假点确认的大量工作时间,提高生产效率。
118.在其中一个实施例中,上述印刷线路板的制作方法中,在步骤s600之后,还包括:将压合板进行四端子测试,以检测压合板的线路是否存在缺口或残铜。其中,四端子测试即按四端子电阻测量原理,根据电阻的阻值判断线路是否存在缺口或残铜。
119.在其中一个实施例中,上述印刷线路板的制作方法中,在步骤s600之后,在控深之前,使用手动贴膜机在压合板的具有铜基凸台110的表面贴上高温保护膜,以保证印刷线路板上的通孔保持密封状态。
120.在其中一个实施例中,芯板300为柔性芯板300,上述印刷线路板的制作方法中,在步骤s600之后,在压合板的弯折区域20进行控深锣,控深余厚为0.30mm
‑
0.35mm。如此,制得的印刷线路板具有弯折区域20,能够弯折,具有软硬结合、高散热的特点。
121.具体地,使用控深锣机生产,使用平底锣刀加工。首先,检查锣机吸气能力是否正常,然后按设定程序测算各个主轴台面高度,接着将印刷线路板的具有铜基凸台110的表面朝下摆放安装在控深锣机台面。打开吸气功能让印刷线路板紧密的与台面贴合,然后按照设定程序测算pcb的厚度,最后控深锣机程序内设定所需余厚。每个主轴先加工首件,首件
余厚测量合格后方可大批量生产。加工过程中不允许擦花板面。
122.可以理解,在其他实施例中,在压合板的弯折区域20进行控深锣的步骤可以省略,此时,印刷线路板为硬板。
123.本发明还提供一种印刷线路板,该印刷线路板按照上述任意一项的印刷线路板的制作方法制成。
124.上述印刷线路板具有铜基凸台110,具有高散热的特点,且制作成本低、良品率高。
125.以上所述仅为本发明的较佳实施例而已,并不用以限制本发明,凡在本发明的精神和原则之内所作的任何修改、等同替换和改进等,均应包含在本发明的保护范围之内。