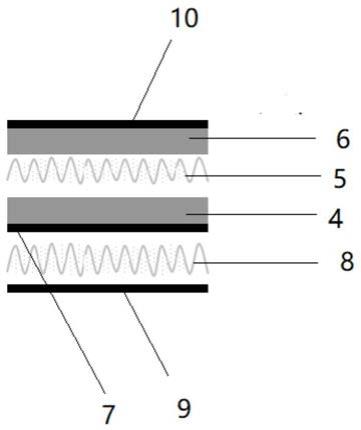
1.本发明涉及电路板技术领域,尤其涉及一种改善高密度互联电路板弯翘的方法。
背景技术:2.随着汽车、家电、通讯、航空航天等产品的可靠性、信号完整性需求越来越严格,普通的覆铜板材料已不能满足客户需求,针对有高频高速信号要求的层次,需要使用高速或高频材料,其加工方法和工艺也要随着提升。
3.传统的电路板产品,一般采用普通的材料加工即可满足客户需求;但随着产品小型化、薄型化、高频化,普通的材料和传统工艺已很难加工出合格产品,这就使得电路板为满足高频高速需求,需要更好的材料和加工工艺,考虑到成本的因素,针对高频高速的层次会采用高频高速材料,同时由于设计和板厚要求,越来越多采用不对称叠构,使得板弯翘严重,超出客户规范,导致产品无法正常上件,无法满足客户产品的需求,随着电子产品的更新换代,尤其5g时代的到来,对电路板产品的信号完整性要求更高,为了保证信号完整性,许多设计采用了不对称叠构,使得电路板产品在层压后会发生翘曲,尤其薄层的缩量大,导致电路板产品弯翘超出常规管控规格(<0.75%),给产品制作、管控、出货和客户端的装配带来了极大困扰,因此提供一种不改变电路板产品不对称结构且能改善电路板弯翘的方法成为当前急需解决的技术问题。
技术实现要素:4.本发明的目的是在于克服、补充现有技术中存在的不足,提供一种改善高密度互联电路板弯翘的方法,达到产品的高频高速、平整度的要求。本发明采用的技术方案是:一种改善高密度互联电路板弯翘的方法,其中,包括以下步骤:s1.提供基板、第一半固化片和铜箔,将基板、第一半固化片和铜箔从下至上依次叠合;s2.将叠合后的铜箔、基板、第一半固化片压合,制成第一子板;s3.将第一子板冷却后不用打靶,直接再压合一次或烘烤一次;s4.将步骤s3的第一子板经过钻孔、电镀、图形制作后,在第一子板上放置第二半固化片,然后再与第二子板压合,形成多层高密度互联电路板。
5.优选的是,所述的改善高密度互联电路板弯翘的方法,其中,所述步骤s1基板包括两层铜箔和设置于两层铜箔之间的环氧树脂基材。
6.优选的是,所述的改善高密度互联电路板弯翘的方法,其中,所述步骤s3烘烤温度为180℃~185℃,烘烤时间为2~2.5h。
7.优选的是,所述的改善高密度互联电路板弯翘的方法,其中,所述步骤s4第二子板>3mil>第一子板时,所述第二子板远离第一子板的一面放置第一离型膜,所述第一离型膜下方设置第三半固化片,所述第三半固化片下方设置第二离型膜,所述第二子板上方设置铜箔。
8.优选的是,所述的改善高密度互联电路板弯翘的方法,其中,所述步骤s4第一子板、第二半固化片和第二子板压合后,还进行拆除第三半固化片、铜箔、第一离型膜和第二离型膜的步骤,形成多层高密度互联电路板。
9.本发明的优点:(1)本发明改善高密度互联电路板弯翘的方法,需要对第一子板和第二子板的内层芯板涨缩给予一定的补偿,以满足经过多次压合后,层偏、涨缩等都达到厂内要求,最终平整度和可靠性达到客户规范的目的。
10.(2)本发明改善高密度互联电路板弯翘的方法,实现了高频高速且不对称结构产品的平整性要求,可以降低由于板弯翘原因导致客户上件不良而产生的报废;本发明既大大提升了产品良率,又满足了客户高频高速产品功能的平整性要求。
附图说明
11.图1为本发明基板的结构示意图。
12.图2为本发明基板和第一半固化片的结构示意图。
13.图3为本发明第一子板与第二子板压合的结构示意图。
14.图4为本发明多层高密度互联电路板的结构示意图。
具体实施方式
15.下面结合具体实施例对本发明作进一步说明。
16.实施例1一种改善高密度互联电路板弯翘的方法,其中,包括以下步骤:一种改善高密度互联电路板弯翘的方法,其中,包括以下步骤:s1.提供基板、第一半固化片和铜箔,将基板、第一半固化片和铜箔从下至上依次叠合;如图1所示,基板包括两层铜箔1和设置于两层铜箔之间的环氧树脂基材2,图2为基板上放置了第一半固化片的结构图。
17.s2.将叠合后的铜箔、基板、第一半固化片3压合,制成第一子板6;s3.将第一子板6冷却后不用打靶,直接再压合一次或烘烤一次,步骤s3烘烤温度为180℃,烘烤时间为2.5h;s4.将步骤s3的第一子板6经过钻孔、电镀、图形制作后,在第一子板4上放置第二半固化片5,然后再与第二子板4压合,如图3所示,第二子板4>3mil>第一子板6时,所述第二子板4远离第一子板6的一面放置第一离型膜7,所述第一离型膜7下方设置第三半固化片8,所述第三半固化片8下方设置第二离型膜9,所述第二子板上方设置铜箔10,第一子板4、第二半固化片5和第二子板6压合后,如图4所示,还进行拆除第三半固化片8、铜箔10、第一离型膜7和第二离型膜9的步骤,形成多层高密度互联电路板。
18.实施例2一种改善高密度互联电路板弯翘的方法,其中,包括以下步骤:s1.提供基板、第一半固化片和铜箔,将基板、第一半固化片和铜箔从下至上依次叠合;如图1所示,基板包括两层铜箔1和设置于两层铜箔之间的环氧树脂基材2,图2为基板上放置了第一半固化片的结构图。
19.s2.将叠合后的铜箔、基板、第一半固化片3压合,制成第一子板6;s3.将第一子板6冷却后不用打靶,直接再压合一次或烘烤一次,步骤s3烘烤温度为182℃,烘烤时间为2.2h;s4.将步骤s3的第一子板6经过钻孔、电镀、图形制作后,在第一子板4上放置第二半固化片5,然后再与第二子板4压合,如图3所示,第二子板4>3mil>第一子板6时,所述第二子板4远离第一子板6的一面放置第一离型膜7,所述第一离型膜7下方设置第三半固化片8,所述第三半固化片8下方设置第二离型膜9,所述第二子板上方设置铜箔10,第一子板4、第二半固化片5和第二子板6压合后,如图4所示,还进行拆除第三半固化片8、铜箔10、第一离型膜7和第二离型膜9的步骤,形成多层高密度互联电路板。
20.实施例3一种改善高密度互联电路板弯翘的方法,其中,包括以下步骤:s1.提供基板、第一半固化片和铜箔,将基板、第一半固化片和铜箔从下至上依次叠合;如图1所示,基板包括两层铜箔1和设置于两层铜箔之间的环氧树脂基材2,图2为基板上放置了第一半固化片的结构图。
21.s2.将叠合后的铜箔、基板、第一半固化片3压合,制成第一子板6;s3.将第一子板6冷却后不用打靶,直接再压合一次或烘烤一次,步骤s3烘烤温度为185℃,烘烤时间为2h;s4.将步骤s3的第一子板6经过钻孔、电镀、图形制作后,在第一子板4上放置第二半固化片5,然后再与第二子板4压合,如图3所示,第二子板4>3mil>第一子板6时,所述第二子板4远离第一子板6的一面放置第一离型膜7,所述第一离型膜7下方设置第三半固化片8,所述第三半固化片8下方设置第二离型膜9,所述第二子板上方设置铜箔10,第一子板4、第二半固化片5和第二子板6压合后,如图4所示,还进行拆除第三半固化片8、铜箔10、第一离型膜7和第二离型膜9的步骤,形成多层高密度互联电路板。
22.本发明改善高密度互联电路板弯翘的方法,需要对第一子板和第二子板的内层芯板涨缩给予一定的补偿,以满足经过多次压合后,层偏、涨缩等都达到厂内要求,最终平整度和可靠性达到客户规范的目的。
23.本发明改善高密度互联电路板弯翘的方法,实现了高频高速且不对称结构产品的平整性要求,可以降低由于板弯翘原因导致客户上件不良而产生的报废;本发明既大大提升了产品良率,又满足了客户高频高速产品功能的平整性要求。
24.最后所应说明的是,以上具体实施方式仅用以说明本发明的技术方案而非限制,尽管参照实例对本发明进行了详细说明,本领域的普通技术人员应当理解,可以对本发明的技术方案进行修改或者等同替换,而不脱离本发明技术方案的精神和范围,其均应涵盖在本发明的权利要求范围当中。