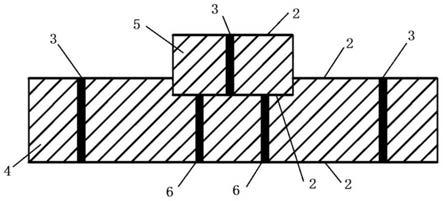
1.本发明属于电子元器件领域,进一步来说涉及多层共烧陶瓷(ltcc及htcc)领域,具体来说,涉及一种多层孤岛陶瓷电路基板的制备方法。
背景技术:2.在电子电路中,多层共烧陶瓷(包含ltcc和htcc)技术是于1982年由美国休斯公司开始发展起来的令人瞩目的3d集成技术,目前该技术已经成为无源集成的主流技术,成为无源元件领域的发展方向和新的元件产业的经济增长点。该技术是将陶瓷粉制成厚度精确而且致密的生瓷带,在生瓷带上利用激光打孔、微孔注浆、精密导体浆料印刷等工艺制出所需要的电路图形,并将多个被动元器件(如低容值电容、电阻、滤波器、阻抗转换器、耦合器等)埋入多层陶瓷基板中,然后通过高精度对位系统,将多层生瓷片进行叠压在一起,其中内外电极可分别使用银、铜、金、钨等金属,通过高温烧结后,制成三维空间互不干扰的高密度互联电路,也可制成内置无源元件的组件基板,在其表面可贴装ic和有源器件,制成无源/有源集成的功能模块,可进一步将电路小型化与高密度化,特别适合于高频通讯用组件。因此,采用ltcc和htcc技术,可以制备多层结构的小型化叠层陶瓷元器件、组件模块等高性能产品。
3.尽管多层共烧陶瓷制备的产品具有体积小的优势,但是由于陶瓷基板核心工艺都是一层层生瓷片(可带过金属孔及电路)进行精确对位堆叠制备而成,加工工程中,只能在生瓷片上打腔体(腔体面积通常要求不超过生瓷片总体面积的1/2),且要求腔体的边缘是与生瓷片有连接,以实现对位叠层。因此,现阶段,基于ltcc/htcc工艺平台所加工的多层陶瓷基板只能具备腔体,孤岛凸台一直存在无法对位堆叠的问题、如果额外放置上去,存在孤岛凸台的位置精度完全不可控的问题。总之,ltcc/htcc电路基板产品无法制备陶瓷孤岛问题,在目前电子信息技术高速发展的时代,已经成为一个明显的技术瓶颈,亟待解决。
4.有鉴于此,特提出本发明。
技术实现要素:5.本发明的目的是:解决现有多层陶瓷基板ltcc/htcc工艺平台中无法对具有孤岛凸台的多层生瓷片进行对位堆叠的问题。
6.为此,本发明提供一种含多层孤岛陶瓷电路的主体电路,所述主体电路的组成包括具有盲腔结构的a基板和b孤岛。
7.所述b孤岛是通过在生瓷片上打孔、填孔、印刷、叠层、小压力预等静压、切割等步骤制备出的b孤岛电路生坯体,在b孤岛底面制作有互联焊盘;
8.所述a基板是通过在生瓷片上打孔、填孔、印刷、打腔、叠层、小压力预等静压等步骤进行制备,a基板的上面带有盲腔结构及腔底互联焊盘,盲腔的形状与b孤岛的形状一致,盲腔的平面尺寸略大于b孤岛的平面尺寸,b孤岛的厚度需大于a部分的盲腔深度,用于将b孤岛精确定位并嵌套于盲腔中。
9.本发明提供一种多层孤岛陶瓷电路的制备方法,工艺步骤如下:
10.(1)通过在生瓷片上打孔、填孔、印刷、叠层、小压力预等静压、切割等步骤制备出b孤岛电路生坯体,其中b孤岛底面含互联焊盘;
11.(2)通过在生瓷片上打孔、填孔、印刷、打腔、叠层、小压力预等静压等步骤制备出a基板,a基板的上面带有盲腔结构及腔底互联焊盘,盲腔的形状与b孤岛的形状一致,腔体高度(深度)范围0.1mm~0.5mm,优选0.2mm~0.3mm,腔底互联焊盘与b基板上底面焊盘一一对应;
12.(3)在a基板盲腔中通过高压喷雾等方式喷涂薄层粘合胶,粘合胶成分为20%质量分数的乙基纤维素溶于丁基咔吡醇、松油醇溶液(丁基咔吡醇40%、松油醇40%),再将切割得到的b孤岛生坯体塞入a基板盲腔中进行贴合;
13.(4)根据b孤岛高度、形状等特性,选用合适的保护模具,对a+b多层电路基板生坯体进行真空封装、大压力等静压、热切、排胶烧结得到带有孤岛结构的多层陶瓷电路板;
14.所述a基板为主体电路的基板部分,厚度通常在1mm~5mm,大小尺寸通常与ltcc/htcc工艺平台相适应,一般为152.4mm或203mm;
15.所述b孤岛为a基板上需要制备的孤岛电路部分,尺寸大小由设计决定,通常在1mm~50mm,形状多样化,包含正方形、长方形、圆形及异形结构,厚度通常在0.5mm~3mm。
16.所述a基板的电路图形、盲腔的加工具体原理是通过识别机械或激光加工的定位孔和金属过孔,再通过常规的过孔填充、厚膜印刷、激光打腔、叠层及预等静压工艺步骤制备;
17.所述b孤岛的电路图形、外观结构的加工具体原理是通过识别机械或激光加工的定位孔,再通过常规的过孔填充、厚膜印刷、叠层、预等静压及切割工艺步骤制备。
18.所述a基板、b孤岛的预等静压工艺参数为,水温60℃~80℃、压力500psi~1500psi,保压时间2min~10min。
19.所述a基板加工时,需要在上表面(需要制备孤岛面)叠一张打有盲腔图形的pet膜,该膜叠在a基板上时,只露出a基板的盲腔部分,a基板的其他部分被pet膜保护盖住。
20.所述b孤岛的切割加工,可以通过铣刀机械切割、激光切割、刀片机械切割等方式进行,制备的b孤岛外形尺寸比a基板的盲腔小0.05mm,b孤岛的厚度需大于a部分的盲腔深度。
21.所述a基板为一体化基板,a基板上可以有多种盲腔,所述b孤岛可以是多种孤岛,如b1、b2、b3等,每种孤岛的形状或高度可以有差异,a基板上的盲腔与b孤岛一一对应。
22.所述a基板、b孤岛(简称ab)之间粘合叠层方法为:在pet膜的保护作用下,可以在a基板盲腔中通过喷雾等方式喷涂薄层粘合剂,粘合剂的厚度要求小于50μm,喷涂了粘合剂后,在60秒时间范围内,撕去pet膜,将切割得到的所有b孤岛(包含b1、b2、b3
…
)逐一对应塞入a基板的盲腔中。
23.a基板+b孤岛(简称a+b)的最终等静压工艺参数为,水温60℃~80℃、压力2500psi~6000psi,保压时间10min~60min。
24.所述多层孤岛陶瓷电路排胶烧结按ltcc和htcc区分,通常ltcc产品的烧结温度800℃~920℃,htcc产品的烧结温度1550℃~1800℃。将a和b烧结成为一个整体,两者之间有电路互联,通过a盲腔内部与b孤岛底面一一对应的互联导体pad等进行电气连接。
25.与现有技术相比,本发明的有益效果为:
26.本发明中,通过ltcc/htcc基板上加工高位置精度和高尺寸精度的盲腔,以及凹凸腔体堆叠转化技术,解决了目前多层共烧陶瓷技术难以制备孤岛多层陶瓷电路的问题,制备的陶瓷孤岛与主体ltcc/htcc电路基板电气互联,具有互联位置精度高、尺寸范围可调等优势。
27.本发明所述的技术方案,广泛应用于将电路小型化与高密度化,特别是高频通讯用组件领域。
附图说明
28.图1为常规ltcc/htcc产品电路基板结构示意图。
29.图2为常规多层共烧陶瓷电路加工效果示意图。
30.图3为本发明带凸台多层共烧陶瓷电路基板结构示意图。
31.图4为本发明带凸台多层共烧陶瓷电路基板效果示意图。
32.图中:1为ltcc/htcc陶瓷体基板,2为表面金属化层,3为金属化通孔,4为盲腔结构陶瓷基板,5为多层孤岛陶瓷体;6为金属化盲孔。
具体实施方式
33.结合图1~图4,下面对本发明实施例做更进一步说明:a基板+b孤岛
34.(1)b孤岛ltcc电路生坯制备
35.选用203mm*203mm*0.127mm钙硼硅体系ltcc生瓷片10张(每张烧结后0.1mm),在生瓷片上打孔、填孔、印刷、叠层、小压力预等静压、切割等步骤,制备出30mm*30mm大小的多层陶瓷电路生坯体;预等静压工艺参数为,水温70℃、压力1200psi,保压时间5min。
36.(2)a基板ltcc电路生坯制备
37.选用203mm*203mm*0.127mm钙硼硅体系ltcc生瓷片20张(每张烧结后0.1mm),在生瓷片上打孔、填孔、印刷、打腔、叠层、小压力预等静压制备出203mm*203mm大小的多层陶瓷电路生坯体;盲腔大小30.05mm*30.05mm,腔体深度为3张生瓷片厚度(约0.35mm,烧结后0.3mm);预等静压工艺参数为,水温70℃、压力1200psi,保压时间5min。
38.(3)a与b组合叠层
39.在a基板盲腔中通过高压喷雾等方式喷涂薄层粘合胶,粘合胶为乙基纤维素溶液,喷雾厚度约30μm,60秒内将切割得到的b孤岛生坯体塞入a基板盲腔中进行贴合,然后等静压,工艺参数为,水温70℃、压力5000psi,保压时间40min。
40.(4)排胶烧结
41.将a+b组合好的生坯体切割成60mm*60mm的方片,设置烧结曲线:室温到450℃用6h,450℃保温2h,升温至860℃用1h,860℃保温15min后自然降温,得到带孤岛电路结构的多层共烧陶瓷电路基板。
42.以上内容是结合最佳实施方案对本发明说做的进一步详细说明,不能认定本发明的具体实施只限于这些说明。本领域的技术人员应该理解,在不脱离由所附权利要求书限定的情况下,可以在细节上进行各种修改,都应当视为属于本发明的保护范围。