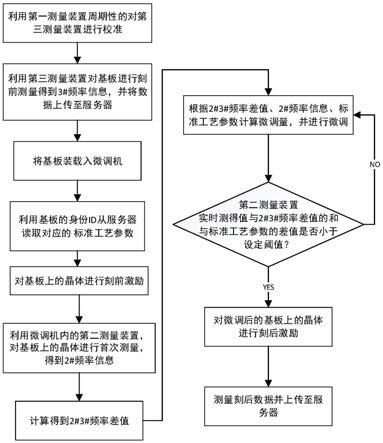
1.本发明涉及晶振生产工艺领域,尤其涉及一种整板晶体微调方法及系统。
背景技术:2.传统的晶振生产过程,是先生产整板的半成品晶体,然后从整板半成品晶体中随机选择其中几颗作为代表,与元级标晶(精度最高的晶体)进行参数对比,确定与元级标晶的差值,利用此差值调整微调机的工作参数,然后将整板半成品晶体放入微调机进行微量的刻蚀调整,简称微调,经微调机微调结束后,再随机取几颗晶体为代表,重新与元级标晶进行参数对比,若差值在允许误差范围内,则认为此板晶体达标,否则对整板晶体进行重新调整或者废弃。
3.由于晶振对制作精度要求很高,所以上述生产过程中,为了确保用于测试晶体频率的测量机本身的准确性,一般在每个监控频点制作五颗标准晶体,每天在每个频点处随机选取三颗标准晶体对测试机进行校准标定,以确保测试机本身状态的稳定性,确保其测出的数值是准确的,现有技术这一步均是人工测量校准,工作效率低,容易出错。若需要更换生产规格,则需要用新规格的标晶对测试机、微调机等设备进行重新校准调整,耗时较长,所以传统的生产方法中,单条产线难以适应多种规格共线生产的情况。
4.另外,上述过程中,在对整板晶体进行测量时,由于是人工测量,故是采用随机采样的方式选择几颗作为代表,我们将此时被选中的这几颗晶体命名为“刻前代表晶体”,以这几颗刻前代表晶体的数值代表整板晶体的状态对微调机进行调节,经微调机调整后,再次随机抽取几颗进行测量,我们将此时被选中的这几颗晶体命名为“刻后代表晶体”,以这几颗刻后代表晶体的数值作为整板晶体的状态,来判断整板晶体是否达标。显然上述过程中,绝大部分的晶体都“被代表”了,上述生产过程中的数据是基于统计学理论得出的理论值,具体每一颗晶体的实际情况如何,无法精准的掌控,在竞争越来越激烈的当下,上述生产工艺已经无法满足精益求精的生产要求。
5.还有,传统微调过程中,对单个晶体的微调往往是分两次进行,第一次刻蚀是粗调,第二次刻蚀是微调,即整个微调过程中探针会分两次接触到晶体,这也会导致测量出现系统的误差。
6.综上,传统的晶体微调过程,以下缺点:
7.1、一台设备一次只能生产一种频率、负载的产品。
8.2、每次更换生产规格型号,必须要用标准晶体对机和试刻。
9.3、产品测试环节抽样少,不能保证所有出厂的产品都合格。
10.4、刻蚀机由于工作环境、工作方式带来系统误差和随机误差,影响测量准确性和一致性,实际出厂的产品与标准参数之间的误差无法100%做到
±
3ppm 以内。
11.5、对标晶、换号耗时较久,设备稼动率在85%以下,已不能适应多品种生产。
技术实现要素:12.本发明所要解决的技术问题是:如何在不降低生产效率的前提下,提高测量数量,实现所有晶体的全面测量,精准掌控生产过程中的真实数据,以及如何提高产线上设备的嫁动率。
13.为解决上述技术问题,本发明所采用的技术方案是:
14.一种整板晶体微调方法,基于整板晶体微调系统,所述整板晶体微调系统包括微调机、服务器、第三测量装置,所述微调机内设有第二测量装置,所述服务器内预先存储有各种规格晶体的标准工艺参数;每一块基板都具有唯一的身份id,基于此身份id,可以确定基板上晶体的规格;微调步骤如下:
15.s1、进行刻前测量,获取本序基板的身份id,利用第三测量装置对本序基板进行测量,获得本序基板上各晶体的位置信息和对应的3#频率信息,将晶体的位置信息、对应的各晶体的3#频率信息以及本序基板的身份id绑定上传至服务器;
16.s2、获取本序基板的身份id,将本序基板装载入微调机;并将此步骤信息上传至服务器;
17.s3、微调机根据本序基板的身份id,从服务器中读取与本序基板对应的标准工艺参数,所述标准工艺参数包括标准频率信息;
18.s4、利用微调机内的第二测量装置,对本序基板进行测量,获得本序基板上晶体的位置信息及各晶体对应的2#频率信息;
19.s5、微调机根据本序基板的身份id,从服务器读取步骤s1中获取的与本序基板对应的3#频率信息,与步骤s4中获取的2#频率信息进行比较计算,获得本序基板上同一位置晶体的2#3#频率差值;
20.s6、微调机根据2#频率信息、2#3#频率差值及标准工艺参数,对本序基板上的晶体进行刻蚀微调,直至微调机内第二测量装置实时测得频率与2#3#频率差值的和与标准频率之间的差值小于设定阈值为止;将微调完后第二测量装置的实时测得频率上传至服务器。
21.与现有技术相比,具有如下有益的效果:
22.利用第三测量装置的测得的3#频率信息、微调机初次测得的2#频率信息、微调机实时测得值和服务器中记载的标准工艺参数对微调机的微调量进行调整,不再需要在微调机上对标晶,提高刻蚀频率准确性和离散性,解决了微调机工作环境对测试的系统误差问题,从而提高生产效率。
23.待加工的基板进入微调机后,探针接触晶体后不再分离,直至微调结束,解决了探针两次接触带来的测试随机偏差问题,采用探针一次完成刻蚀,保证测量准确性、一致性。
24.在上述基础上,本发明还可以做如下改进:
25.进一步地,对于连续的生产过程,当对前序基板进行步骤s2-s6操作时,对本序基板进行步骤s1的操作。充分利用了步骤s2-s6过程等待的时间,大幅度提高了连续加工的工作效率。
26.进一步地,在步骤s6之后还包括步骤s7,所述步骤s7为:在步骤s6 之后还包括步骤s7,所述步骤s7为:进行刻后激励,对经微调机刻蚀微调后的本序基板进行刻后激励。
27.进一步地,第三测量装置在生产过程中周期性的进行频率校准,具体地,对机基板是指承载着产线标晶的一块基板,所述产线标晶是以元级标晶为基准制作的次级标准晶
体,用做校对生产设备的基准,所述元级标晶是用来校准标准测量装置的晶体,用外部信号对作为标准测量装置的第一测量装置进行时钟校准,利用校准时钟后的第一测量装置测量元级标晶,根据测得值与元级标晶的理论值,设置第一测量装置的补偿值,确保第一测量装置的准确性,第三测量装置的周期性校准过程如下:
28.首先、读取对机基板的身份id,用设置好补偿值后的第一测量装置对对机基板进行测量,得到对机基板的标准负载频率;将对机基板的身份id与测得的标准负载频率绑定上传至服务器;
29.其次、读取对机基板的身份id,用一块第三测量装置对对机基板进行测量,得到与本块第三测量装置、对机基板匹配的测量负载频率,将本块第三测量装置的身份信息、对机基板的身份id及对应的测量负载频率绑定后上传至服务器;
30.最后、服务器计算对机基板上相同位置晶体的标准负载频率和测量负载频率的差值,设置本块第三测量装置的补偿值,完成对第三测量装置的校准;
31.对机基板在生产过程中不断地在第一测量装置和第三测量装置之间循环测量,实现对第三测量装置的周期性校准。
32.采用上述进一步方案的有益效果是基于整板测试方式,借助服务器存储对机基板的数据,实现了对第三测量装置的持续校准,由于用于校准的基础数据是整个对机基板上所有的晶体,数据量大,校准效果更好。
33.进一步地,每隔设定时间或第三测量装置累计测量设定数额的待刻蚀基板后,用第一测量装置、对机基板对第三测量装置进行校对,若第三测量装置或第一测量装置中同一测试通道少于5%的位置的晶体新测得的数值与上一次测量值差异超过1.5ppm,判定晶体测试接触不良;若同一测试通道超过 20%位置晶体频率测量值与上一次频率测量值超过1.5ppm,则判定第三测量装置或第一测量装置故障。
34.采用上述进一步方案的有益效果是用对机基板循环对第三测量装置进行校准,及时发现第三测量装置可能发生的故障,避免影响产品的品控结果。
35.进一步地,第一测量装置、测试板卡与服务器的数据交换是通过网络传输实现的。
36.进一步地,在微调机对本序基板进行首次测量之前,还包括对本序基板进行刻前激励的过程。
37.采用上述进一步方案的有益效果是刻前对基板进行激励,可以使基板上的晶体更接近使用状态,避免微小的虚焊等情况导致测量误差。
38.一种对整板晶体微调的系统,其特征在于,包括元级标晶、对机基板、微调机、第一测量装置、第三测量装置、服务器;
39.所述元级标晶是用来校准第一测量装置的标准晶体;
40.所述对机基板是指承载着产线标晶的一块基板,所述产线标晶是以元级标晶为基准制作的次级标准晶体,用做产线校对设备的基准;
41.所述第一测量装置是标准测量装置,用于测量对机基板的参数,形成基准测量数据;
42.所述第三测量装置测量对机基板获得第三测量数据,或者对待刻蚀基板进行测量,得到对应的3#频率信息;并上传至服务器;
43.所述微调机内设有第二测量装置,所述第二测量装置对本序基板进行刻前测量,
获得与本序基板身份id对应的2#频率信息,在刻蚀中对本序基板进行实时测量,得到刻中数据,在刻蚀后对本序基板进行测量得到刻后参数,所述微调机根据微调参数对晶体进行逐一刻蚀微调;
44.所述服务器用于接收、存储第一测量装置测得的基准测量数据、第二测量装置测得的2#频率信息和刻后参数、第三测量装置测得的第三测量数据、与基板身份id对应的3#频率信息及本序基板的理论频率信息;
45.所述服务器根据第三测量数据和基准测量数据之间的差值,生成第三测量装置的校准补偿参数并传递给第三测量装置;
46.所述微调机从所述服务器读取本序基板的3#频率信息、2#频率信息、理论频率信息,计算确定微调机针对本序基板的微调参数并对本序基板进行刻蚀微调。
47.进一步地,所述第三测量装置独立于生产线存在。
48.首先利用第三测量装置对待刻蚀基板上所有位置的晶体产品进行频率测量,得到该基板的3#频率信息,利用网络协议将待刻蚀基板上每只晶体的数据 (包括其位置和频率)传至服务器;然后微调机读取待刻蚀基板的身份id,获得此待刻蚀基板上产品的理论数据,理论数据包括理论频率信息,同时读取存储在服务器中该基板的3#频率信息,微调机测量该待刻蚀基板上所有位置的晶体产品的频率,得到2#频率信息,将3#频率信息和2#频率信息之差记为2#3# 频率差值,2#3#频率差值就是第三测量装置与微调机内置的第二测量装置之间的测量误差,微调机内第二测量装置实时测得的频率与2#3#频率误差的和与理论数据的差值就是微调机的微调量;微调机根据微调量对晶体进行刻蚀,一般微调1s,再实时测试一次(每次测试耗时为毫秒级),更新一次微调量,直至第二测量装置实时测得的频率与2#3#频率误差的和与理论频率之间的差值小于设定阈值,即认为已经将晶体的频率调整至目标频率,再进行下一颗晶体的调整,保证了晶体频率的准确性。
49.与现有技术相比,本方案具有如下有益的效果:
50.1、可以柔性化生产,一台设备同时加工不同频率、负载晶体;
51.2、待刻蚀基板进入微调机后,直接通过第三测量装置测得的3#频率信息与微调机初次测得频率(即2#频率信息)的差值和微调机实时测试值,给出微调量,探针一次完成刻蚀,保证测量准确性、一致性,解决了传统加工模式下探针两次接触带来的测试随机偏差问题。
52.3、由于第三测量装置独立与生产线存在,其测量结果不受微调机工作环境的变化而变化,直接通过第三测量装置与微调机初次频率测试差值和微调机实时测试值,给出微调量,解决了微调机工作环境对测试的系统误差问题,提高刻蚀频率准确性和离散性;
53.4、利用服务器记录对机基板的数据,借助独立与微调机存在的第三测量装置的独立测量,可以间接确认微调机测量结果的准确性,不需要在微调机上对标晶,从而提高生产效率。
附图说明
54.图1为本发明的整板晶体微调方法的流程图;
55.图2为本发明的整板晶体微调系统的结构示意图。
具体实施方式
56.以下结合附图对本发明的原理和特征进行描述,所举实例只用于解释本发明,并非用于限定本发明的范围。
57.实施例1:
58.如图1所示,一种整板晶体微调方法,基于整板晶体微调系统,所述整板晶体微调系统包括微调机、服务器、第三测量装置,所述微调机内设有第二测量装置,所述服务器内预先存储有各种规格晶体的标准工艺参数;每一块基板都具有唯一的身份id,基于此身份id,可以确定该基板上晶体的理论规格;
59.首先对第三测量装置进行频率校准,步骤如下:
60.j1、用铷原子钟对作为标准测量装置的第一测量装置进行校准,同时进行0欧姆、50欧姆和开路校准,再用50欧姆验证合格后,利用校准后的第一测量装置测量元级标晶-具体是镀金标晶,根据测得值与镀金标晶的理论值,设置第一测量装置的补偿值;确保第一测量装置测量的结果是准确的。
61.j2、读取对机基板的身份id,用设置好补偿值后的第一测量装置对对机基板进行测量,得到此对机基板的标准负载频率;将对机基板的身份id与测得的标准负载频率绑定上传至服务器,由此,当外部装置向服务器提供对机基板的身份id时,服务器可以对外提供此对机基板的标准负载频率;
62.j3、读取对机基板的身份id,用一块第三测量装置对此对机基板进行测量,得到与本块第三测量装置、本块对机基板对应的测量负载频率,将本块第三测量装置的身份信息、对机基板的身份id及对应的测量负载频率绑定后上传至服务器;数据上传到服务器后,服务器会将第三测量装置的身份信息与对应的测量负载频率、对机基板的身份id进行绑定,其记录了用此块第三测量装置测量此块对机基板得到的测量结果。
63.j4、服务器计算此对机基板上相同位置晶体的标准负载频率与测量负载频率的差值,设置为此块第三测量装置的补偿值,对第三测量装置进行校准,确保第三测量装置测得的数据是准确的。
64.按照上述方式,对所有的第三测量装置进行校准。
65.完成上述校准工作之后,就可以开始对待加工的整板晶体进行微调了,具体步骤如下:
66.s1、进行刻前测量,第三测量装置读取本序基板的身份id,利用第三测量装置对本序基板进行测量,获得本序基板上各晶体的位置信息和对应的3#频率信息,将晶体的位置信息、对应的各晶体的3#频率信息以及本序基板的身份id 绑定上传至服务器;服务器记录下对应这个本序基板身份id的2#频率信息。此处“本序基板”是指当前正处在加工工序的整板基板,其上携带着待刻蚀的晶体,“本序基板”的定义是为了与连续生产作业过程中的“前序基板”“后序基板”进行区分。
67.s2、将本序基板装载入微调机,微调机获取本序基板的身份id,对本序基板进行刻前激励,将此步骤信息上传至服务器;由此,服务器得知,接下来此台微调机测得的数据将是对应此身份id的基板的数据;另外刻前为基板上的晶体施加激励,可以使本序基板上的晶体处于工作状态,可以解决微小的虚焊等各种情况,使其接近使用状态,进一步测量时才能获得最贴近使用状态的数据;
68.s3、微调机同时根据本序基板的身份id,从服务器中读取与此本序基板对应的标准工艺参数,所述标准工艺参数包括标准频率信息;
69.s4、利用微调机内的第二测量装置,对本序基板进行测量,获得本序基板上晶体的位置信息及各晶体对应的2#频率信息;此时还没有对本序基板上的晶体进行微调,所以此时测得的2#频率信息,是微调机初次测得的频率,理论上其应该跟此本序基板对应的3#频率信息是完全一致的,但是由于第二测量装置和第三测量装置本身之间的差异,导致3#频率信息和2#频率信息实际上会有微小的差异。
70.s5、根据本序基板的身份id,从服务器读取步骤s1中获取的与本序基板对应的3#频率信息,与步骤s4中获取的2#频率信息进行比较计算,获得本序基板上同一位置晶体的2#3#频率差值,即2#3#频率差值体现了第二测量装置和第三测量装置本身之间的误差;第二测量装置对本序基板的实时测量值加2#3#频率差值获得的和,与标准工艺参数中的理论频率信息之间的差值即为微调机的微调量。
71.s6、微调机根据第二测量装置实时测得的频率值、2#3#频率差值及标准工艺参数不断调整微调量,对本序基板上的晶体进行刻蚀微调,一般是每隔1s 左右更新一次微调量,直至微调机内第二测量装置实时测得频率与2#3#频率差值的和与标准频率之间的差值小于设定阈值时,认为此颗晶体已经达到设计的理论频率;切换到下一颗晶体,依次循环直至本序基板上所有需要微调的晶体都刻蚀调整完毕,将微调完后第二测量装置的实时测得频率上传至服务器。
72.步骤s7为:对本序基板进行刻后激励,刻后激励意味着先对微调后的基板上的晶体施加激励信号,使得基板上各晶体处于工作状态一定时间,这样可以解决微调过程中可能产生的微粒等对策测量结果产生的影响。
73.本例中,设有一个第一测量装置,9个第三测量装置,若干个微调机。
74.为了保证独立存在的第三测量装置的测量准确性,对机基板会在唯一的第一测量装置与9块第三测量装置之间循环测量,相当于对于任意一个第三测量装置或第一测量装置而言,其每测量9块待刻蚀的基板之后,就会测量一次对机基板,所有数据都会上传至服务器,服务器利用第一测量装置、第三测量装置对对机基板测量的差值,设置对应第三测量装置的补偿值,使得所有第三测量装置不断的以第一测量装置为标准进行校准,确保测量结果的准确性。
75.对机基板仅在第一测量装置和第三测量装置之间循环,不会进入微调机内,由于微调机内第二测量装置并没有用第一测量装置进行校准,所以其测得的2# 频率信息并非待刻蚀基板的真实频率信息,对于同一块待刻蚀基板而言,第二测量装置与第三测量装置之间会存在与此待刻蚀基板对应的测量误差2#3#频率差值,理论上,2#频率信息加上2#3#频率差值即为此待刻蚀基板的实际频率。
76.测量过程中,若同一测试通道中少于5%的位置的晶体新测得的数值与上一次测量值差异超过1.5ppm,判定晶体测试接触不良;若同一测试通道超过 20%位置晶体频率测量值与上一次频率测量值超过1.5ppm,则判定第三测量装置故障,需要停机检修查找原因,或者重新校准。
77.本例中,第一测量装置、第二测量装置、第三测量装置与服务器的数据交换均是通过网络传输实现的。
78.另外,对于连续的生产过程,为了提高工作效率,可以在对前序基板进行步骤s2-s6操作时,对本序基板进行步骤s1的操作,在对后续基板做步骤s2-s6 操作时,执行步骤s7,充分利用微调机微调的时间实现对前后序基板的刻前测量和刻后测量工作。
79.实施例2:
80.一种对整板晶体微调的系统,如图2所示,包括整板测试机、微调产线、元级标晶、对机基板、服务器,所述产线上并排分布有若干个微调机,所述整板测试机内包括1个第一测量装置和9个第三测量装置;
81.所述元级标晶是用来校准第一测量装置的标准晶体;
82.所述对机基板是指承载着产线标晶的一块基板,所述产线标晶是以元级标晶为基准制作的次级标准晶体,用做产线校对设备的基准;
83.所述第一测量装置是标准测量装置,用于测量对机基板的参数,形成基准测量数据;并上传至服务器;
84.所述第三测量装置测量对机基板获得第三测量数据,或者对待刻蚀基板进行测量,得到与待刻蚀基板对应的3#频率信息;并上传至服务器;为了区分不同次序的待加工基板,定义本序基板为当前正在加工的、承载着待加工晶体的基板;排在本序基板前面加工的叫前序基板,排在本序基板后面加工的叫后序基板。
85.所述微调机内设有第二测量装置,所述第二测量装置对本序基板进行刻前测量,获得与本序基板身份id对应的2#频率信息,在刻蚀中对本序基板进行实时测量,得到刻中数据,在刻蚀后对本序基板进行测量得到刻后参数,所述微调机根据微调参数对晶体进行逐一刻蚀微调;
86.所述服务器用于接收、存储第一测量装置测得的基准测量数据、第二测量装置测得的2#频率信息和刻后参数、第三测量装置测得的第三测量数据、与基板身份id对应的3#频率信息及本序基板的理论频率信息;
87.所述服务器根据第三测量数据和基准测量数据之间的差值,生成第三测量装置的校准补偿参数并传递给第三测量装置;
88.所述微调机从所述服务器读取本序基板的3#频率信息、2#频率信息、理论频率信息,计算确定微调机针对本序基板的微调参数并对本序基板进行刻蚀微调。
89.所述对机基板在整板测试机内循环测量,即如图2所示,对机基板在第一测量装置和9个第三测量装置之间循环测量,用于周期性的以第一测量装置为基准,校对第三测量装置。
90.如,对于一块包含300颗晶体的基板,对整个基板上的300颗晶体逐个进行微调需要12-15分钟,但是利用第三测量装置对300颗晶体进行一次测量仅需2分钟左右(第三测量装置仅测量,不刻蚀,所以速度很快),因此对3# 频率信息的测量,完全可以利用微调机对前序基板或后续基板进行微调、本序基板在排队等待的时间间隙中进行,不影响正常的生产节奏。
91.本系统可以实现对晶体的100%测量,大幅度提高了质量监控的精度,有利于工艺优化,实现微调、压封、老化后测试的大数据闭环分析,提高产品品质一致性。
92.由于对应不同生产规格的对机板的参数事先测试好并存储在服务器中,且利用服务器对比第二测量频率、第三测量频率并与标称频率进行对比,即可得到校准数据,实现了
微调机的自动化校准,速度快,因此可以实现一条产线的混频生产,满足了多规格,小批量生产的需求。
93.以上所述仅为本发明的较佳实施例,并不用以限制本发明,凡在本发明的精神和原则之内,所作的任何修改、等同替换、改进等,均应包含在本发明的保护范围之内。