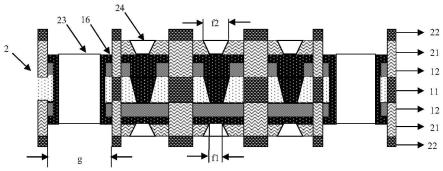
1.本发明涉及印刷线路板加工工艺技术领域,尤其是指一种提升印刷线路板对位精度的加工工艺。
背景技术:2.随着电子产品的多功能化,产品呈轻、薄、短、小方向发展,其要求在更小尺寸的印刷线路板上能够布局更多的元器件,要求对产品的线路越来越细、导通孔越来越小,同时线路和导通孔之间的间距也相应减少,特别是高密度互联多层线路板盲孔各层之间的对位要求越来越高,现有技术中多层线路板盲孔各层之间的对位难以精确控制。
技术实现要素:3.为此,本发明所要解决的技术问题在于克服现有技术中高密度互联多层线路板盲孔各层之间的对位难以控制,提供一种提升印刷线路板对位精度的加工工艺,从而提升印刷线路软硬结合板对位精度。
4.按照本发明提供的技术方案,一种提升印刷线路板对位精度的加工工艺,包括如下步骤:s1:准备印刷线路板的内层芯板:所述内层芯板包括绝缘层,所述绝缘层的上表面和下表面分别设有第一铜箔;s2:制作第一盲孔和第一通孔:在内层芯板上制作第一盲孔和第一通孔,所述第一盲孔贯穿内层芯板其中一面的第一铜箔及绝缘层,所述第一通孔以内层芯板为中心对称分布于内层芯板的四个角位置;s3:填孔电镀:对内层芯板进行电镀,使得第一盲孔内填满铺铜,并在内层芯板的上表面和下表面分别形成第一铺铜层以及在第一通孔的内壁形成第二铺铜层;s4:影像转移:利用四个第一通孔对位进行影像转移,得到第一线路基板,所述第一线路基板包括去除部分第一铺铜层以及第一铜箔后的非铜区域,并在每个第一通孔位于第一线路基板上表面及下表面的孔边缘处保留预留铺铜;s5:压合:利用半固化片和铜箔在第一线路基板上表面和下表面均进行压合,使得第一线路基板上表面和下表面均依次形成半固化层和第二铜箔,得到第二线路基板,所述半固化层覆盖所述第一通孔;s6:制作第二盲孔和第二通孔:利用激光将第一通孔位置处的半固化层和第二铜箔去除,并使所述预留铺铜和第一通孔露出,得到第二通孔,再次以四个第一通孔对位在第二线路基板上表面和下表面制作第二盲孔,所述第二盲孔贯穿第二铜箔及半固化层;s7:根据印刷线路板所需层数不断重复步骤s3至s6。
5.在本发明的一种实施方式中,所述绝缘层的厚度在0.025mm-0.15mm。
6.在本发明的一种实施方式中,所述第一铜箔和第二铜箔的厚度均在1/8 oz
–ꢀ
1 oz。
7.在本发明的一种实施方式中,所述第一盲孔和所述第二盲孔的形状和尺寸均形同。
8.在本发明的一种实施方式中,所述第一盲孔为圆形孔或锥形孔,所述第一盲孔的截面的直径在0.025mm-0.25mm。
9.在本发明的一种实施方式中,所述第一盲孔和所述第二盲孔同轴设置。
10.在本发明的一种实施方式中,所述第一通孔为圆形孔,其截面直径不小于0.5mm,所述预留铺铜的外形包括正方形或圆形,所述预留铺铜的中轴线与所述第一通孔的中轴线相同。
11.在本发明的一种实施方式中,所述预留铺铜的边或外圆周距离第二铺铜层内圆周的最小距离不小于.mm。
12.在本发明的一种实施方式中,所述第二通孔的截面为圆形,所述第一通孔包含于第二通孔内且与所述第二通孔同轴设置,所述第二通孔的截面的最大半径不大于预留铺铜的边长或直径。
13.在本发明的一种实施方式中,步骤s5之前,还对第一线路基板进行包括蚀刻、自动光学检验和棕化的操作。
14.本发明的上述技术方案相比现有技术具有以下优点:本发明所述的一种提升印刷线路板对位精度的加工工艺,在第一次制作盲孔的同时预留四个用于对位的第一通孔,在制作第一次线路及增层的盲孔和增层线路时,依旧使用此四个第一通孔进行对位,即不管做多少次增层压合,始终选用第一次制作盲孔时预留的第一通孔对位,打破传统的印刷线路板的对位原理。本发明能够有效解决高密度互联印刷线路板层间对位差异,提升对位精度。
附图说明
15.为了使本发明的内容更容易被清楚的理解,下面根据本发明的具体实施例并结合附图,对本发明作进一步详细的说明,其中图1是本发明的内层芯板结构示意图。
16.图2是本发明的在内层芯板上制作第一盲孔和第一通孔的示意图。
17.图3是第一盲孔和第一通孔在内层芯板上分布示意图。
18.图4是对内层芯板填孔电镀的示意图。
19.图5是对内层芯板填孔电镀后第一盲孔和第一通孔在内层芯板上分布示意图。
20.图6是第一线路基板的示意图。
21.图7是第一线路基板上预留铺铜示意图。
22.图8是第二线路基板示意图。
23.图9是在第二线路基板制作第二盲孔和第二通孔后的示意图。
24.说明书附图标记说明:1、内层芯板;11、绝缘层;12、第一铜箔;13、第一盲孔;14、第一通孔;15、第一铺铜层;16、第二铺铜层;17、预留铺铜;18、非铜区域;100、第一线路基板;2、第二线路基板;21、半固化层;22、第二铜箔;23、第二通孔;24、第二盲孔。
具体实施方式
25.下面结合附图和具体实施例对本发明作进一步说明,以使本领域的技术人员可以更好地理解本发明并能予以实施,但所举实施例不作为对本发明的限定。
26.参照图1至如9所示,本发明的一种提升印刷线路板对位精度的加工工艺,包括如下步骤:s1:准备印刷线路板的内层芯板1:所述内层芯板1包括绝缘层11,所述绝缘层11的上表面和下表面分别设有第一铜箔12;s2:制作第一盲孔13和第一通孔14:在内层芯板1上制作第一盲孔13和第一通孔14,所述第一盲孔13贯穿内层芯板1其中一面的第一铜箔12及绝缘层11,所述第一通孔14以内层芯板1为中心对称分布于内层芯板1的四个角位置;s3:填孔电镀:对内层芯板1进行电镀,使得第一盲孔13内填满铺铜,并在内层芯板1的上表面和下表面分别形成第一铺铜层15(如图3所示,其厚度为c2)以及在第一通孔14的内壁形成第二铺铜层17(如图3所示,其厚度为c1);s4:影像转移:利用四个第一通孔14对位进行影像转移,得到第一线路基板100,所述第一线路基板100包括去除部分第一铺铜层15以及第一铜箔12后的非铜区域18,并在每个第一通孔14位于第一线路基板100上表面及下表面的孔边缘处保留预留铺铜17;s5:压合:利用半固化片和铜箔在第一线路基板100上表面和下表面均进行压合,使得第一线路基板100上表面和下表面均依次形成半固化层21和第二铜箔22,得到第二线路基板2,所述半固化层21覆盖所述第一通孔14;s6:制作第二盲孔24和第二通孔23:利用激光将第一通孔14位置处的半固化层21和第二铜箔22去除,并使所述预留铺铜16和第一通孔14露出,得到第二通孔23,再次以四个第一通孔14对位在第二线路基板2上表面和下表面制作第二盲孔24,所述第二盲孔24贯穿第二铜箔22及半固化层21;s7:根据印刷线路板所需层数不断重复步骤s3至s6。通过在制作盲孔的同时预留四个用于对位的第一通孔16,在制作第一次线路及增层的盲孔和增层线路时,依旧使用此四个第一通孔16进行对位,即不管做多少次增层压合,始终选用第一次制作盲孔时预留的第一通孔16对位,解决了高密度互联印刷线路板层间对位差异,提升对位精度。
27.具体地,所述绝缘层11的厚度在0.025mm-0.15mm,所述绝缘层11材料包括树脂。
28.具体地,所述第一铜箔12和第二铜箔22的厚度均在1/8 oz
–ꢀ
1 oz。
29.具体地,所述第一盲孔13和所述第二盲孔24的形状和尺寸均形同。
30.具体地,参考图2与图9,所述第一盲孔13为圆形孔或锥形孔,所述第一盲孔13的截面的直径在0.025mm-0.25mm。如图所示,当第一盲孔13为锥形孔时,锥形孔截面的最大直径为a1,a1不大于0.25mm;最小直径为a2,a2不小于0.025mm。当第二盲孔24也为锥形孔时,第二盲孔24截面的最大直径为f2并与a1相等,第二盲孔24截面的最小直径为f1并与a2相等;所述第一盲孔13和所述第二盲孔24同轴设置。
31.参考图3,本实施例中,所述内层芯板1的外形为矩形,每个第一通孔16距离所述内层芯板1的长边距离b1和距离所述内层芯板1的短边距离b2均相等。
32.具体地,所述第一通孔14为圆形孔,其截面直径不小于0.5mm,所述预留铺铜17的外形包括正方形或圆形,所述预留铺铜17的中轴线与所述第一通孔14的中轴线相同。
33.具体地,参考图6和图7,所述预留铺铜16的边或外圆周距离第二铺铜层16内圆周的最小距离d不小于0.2mm。
34.具体地,参考图9,所述第二通孔23的截面为圆形,所述第一通孔包含于第二通孔内且与所述第二通孔23同轴设置,所述第二通孔23的截面的最大半径g不大于预留铺铜17的边长或直径。
35.具体地,所述第一盲孔13和第二盲孔24的制作过程包括镭射激光打盲孔、盲孔除胶、盲孔光学检验和盲孔电镀。
36.具体地,步骤s5之前,还对第一线路基板100进行包括蚀刻、自动光学检验和棕化的操作。
37.实施例2以型号为0.004
″
h/h oz的内层芯板1为例,本实施例提供一种提升印刷线路板对位精度的加工工艺,包括如下步骤:s1:准备印刷线路板的内层芯板1:所述内层芯板1包括绝缘层11,所述绝缘层11的上表面和下表面分别设有第一铜箔12;s2:制作第一盲孔13和第一通孔14:在内层芯板1上制作第一盲孔13和第一通孔14,所述第一盲孔13贯穿内层芯板1其中一面的第一铜箔12及绝缘层11,所述第一通孔14以内层芯板1为中心对称分布于内层芯板1的四个角位置,所述第一通孔14的直径为3mm;s3:填孔电镀:对内层芯板1进行电镀,使得第一盲孔13内填满铺铜,并在内层芯板1的上表面和下表面分别形成第一铺铜层15以及在第一通孔14的内壁形成第二铺铜层17;s4:影像转移:利用四个第一通孔14对位进行影像转移,得到第一线路基板100,所述第一线路基板100包括去除部分第一铺铜层15以及第一铜箔12后的非铜区域18,并在每个第一通孔14位于第一线路基板100上表面及下表面的孔边缘处保留预留铺铜17,所述预留铺铜17的外形为正方形,所述预留铺铜17的中轴线与所述第一通孔14的中轴线相同,所述预留铺铜16的边距离第二铺铜层16内圆周的距离d为3mm;s5:压合:利用半固化片和铜箔在第一线路基板100上表面和下表面均进行压合,使得第一线路基板100上表面和下表面均依次形成半固化层21和第二铜箔22,得到第二线路基板2,所述半固化层21覆盖所述第一通孔14;s6:制作第二盲孔24和第二通孔23:利用激光将第一通孔14位置处的半固化层21和第二铜箔22去除,并使所述预留铺铜16和第一通孔14露出,得到第二通孔23,再次以四个第一通孔14对位在第二线路基板2上表面和下表面制作第二盲孔24,所述第二盲孔24贯穿第二铜箔22及半固化层21,如图7所示;s7:再次重复步骤s3至s6,再次制作第三盲孔后,依流程生产到成品,完成高精度印刷线路板生产。
38.最后所应说明的是,以上具体实施方式仅用以说明本发明的技术方案而非限制,尽管参照实例对本发明进行了详细说明,本领域的普通技术人员应当理解,可以对本发明的技术方案进行修改或者等同替换,而不脱离本发明技术方案的精神和范围,其均应涵盖在本发明的权利要求范围当中。