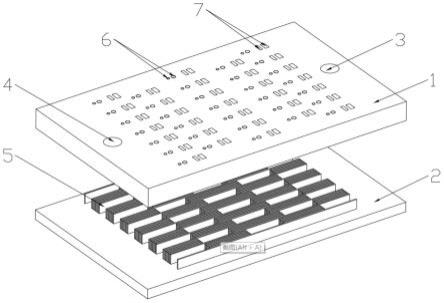
1.本发明属于电子器件技术领域,更进一步涉及电子散热器件技术领域一种泵与散热器一体的微通道散热器。本发明可应用于高功率、高热流密度电子元器件的热管理。
背景技术:2.随着摩尔定律逐渐接近极限,单位面积上电子元件的数量成倍增长,电子器件的功耗逐渐提高,以至于在有限的封装体积内元器件的热流密度急剧上升,导致元器件失效的可能性大幅提高,因此需要一种换热能力较强的热管理方案。微通道散热技术作为一种新型的液冷换热技术,基于该技术设计的微通道散热器具有更高的换热系数、更小的尺寸以及更轻的重量,是目前高热流密度电子元器件的首选散热方式,然而微通道散热器内部流体工质的流动特性一般无法被精准控制,因此流体工体的流动均匀性很难保证,另外微通道散热器的回路中往往需要泵来为流体工质提供动力,泵的设计、选型、安装、维护等方面大大增加了液冷散热回路的设计难度和成本。
3.中国科学院理化技术研究所在其申请的专利文献“一种基于压电泵的微通道相变换热冷却系统”(申请号cn201721624733.8,公开号cn207519054u)中公开了一种微通道相变换热冷却的微通道散热器。该散热系统包括压电泵、微通道散热器以及换热器,该微通道冷却系统采用压电泵驱动技术结合微通道相变换热技术。压电泵的出水口通过连接管路与微通道散热器连接,压电泵的进水口通过连接管路与换热器连接,微通道散热器与换热器通过连接管路连接。该散热器存在的不足之处是,将压电泵是液冷回路中唯一为流体提供动力的部件,压电泵的结构不仅复杂,而且其稳定性和可靠性最低,出现失效的可能性较大。因此,在该冷却系统的设计和使用过程中需要详细考虑压电泵的选型、维护、安装形式、安装位置等因素,不仅提升了系统的设计难度和复杂程度,而且降低了系统的可靠性。
4.毫厘机电(苏州)有限公司在其申请的专利文献“一种用于医疗器械的冷板”(申请号cn201920334714.4,公开号cn209691743u)中公开了一种用于医疗器械的微通道散热器。该散热器包括:上基板和下基板,该微通道散热器采用双层冷却结构。上基板下表面、下基板上表面均设有流道以及若干翅片安装槽,翅片安装槽内安装有散热翅片,上基板端部设有进水管道、下基板端部设有出水管道,由进水管道流入的液体可分流进入上基板、下基板的流道中,在流道中依次经过对应的散热翅片,最终汇流后通过下基板的出水管道流出。该散热器存在的不足之处在于,由于该微通道散热器采取单流体入口、单流体出口的结构,虽然在其上下基板表面设有复杂形状的流道和翅片,但是依然无法精准控制各个流道内流体工质的流速,因此很可能出现微通道散热器内部流体工质流动不均匀的情况,从而导致不同区域的散热能力相差较大,最终降散热器的低换热性能。
技术实现要素:5.本发明的目的是针对上述已有技术的不足,提出一种泵与散热器一体的微通道散热器,用于改善目前微通道散热系统设计过程中,泵的设计难度大、使用和维护复杂的情
况,并解决微通道散热器内部流体工质流动不均匀的问题。
6.实现本发明的思路是,采用电流体材料作为微通道散热器内部的流体工质。电流体作为新型智能材料,是一种含有自由电子的单极性荷电流体或极化流体,在存在强电场的情况下,电流体会受到电场和流场耦合作用,从而产生定向流动,该现象的机理是:在无外加电场或弱电场作用下,介电液体整体呈电中性,其中电中性分子的解离和结合过程保持平衡,当施加较强的电场时,以上平衡不再保持,一方面,电中性分子的解离速度会随着电场的增强而增加,从而产生更多的自由电荷,即昂萨格维恩效应;另一方面,电场排斥与电极极性相同的离子,形成异号电荷层,当作用于异号电荷层的库仑力不能相互平衡时,电流体将产生流动。因此本发明直接在微通道散热器内部对电流体施加强电场,控制电流体的流动,不再需要液冷回路中的泵作为流体工质动力源,从而实现泵与散热器的一体化,简化在设计和使用泵的过程中存在的复杂问题。通过对微通道散热器内部各个流道中的电极施加电流的方式,实现对微通道散热器的各个流道中电流体的快速、准确的控制,从而大幅提升微通道散热器内流体工质的流动均匀性,进而获得更高的换热能力。并采用规整且密集的散热鳍片,形成拥有较小水力直径的微通道,从而提升微通道散热器单位面积上的对流换热系数,最终实现对高功率电子元器件的高效散热的目的。
7.本发明中的泵与散热器一体的微通道散热器,包括上底板1、下底板2、流体入口3、流体出口4、散热鳍片5、棒状金属电极6、网状金属电极7;所述上底板1沿平行于电流体流动方向,至少成型有两两交错的33对通孔,每对电极通过导热胶分别粘结于上底板1的相应通孔内,每对电极的上表面均与上底板1的上表面重合;每对电极中包括一对棒状金属电极6和一对网状金属电极7,其材料均采用导电性能好、抗腐蚀的材料;每对电极中,均有一个电极接直流电源正极,另一个电极接直流电源负极,且可以单独控制每对电极上施加的电流大小;在上底板2的上表面沿平行于电流体流动的方向,均匀设置有多条整齐且密集的散热鳍片5。
8.本发明与现有技术相比具有如下优点:
9.第一,由于本发明采用直接对微通道散热器内部的电流体施加强电场的方式,达到了微通道散热器直接为电流体提供动力的效果,从而实现了泵与散热器的一体化,克服了现有技术中泵与散热器分开设计所带来的可靠性低、设计难度大、成本高等不足,使得本发明降低了散热器的设计难度,并使本发明设计的结构具有更高的可靠性和更长的工作寿命。
10.第二,由于本发明采用微通道散热器内部电极直接控制电流体流动的方式,克服了现有结构中各个流道中流体工质无法快速准确控制的缺陷,由此使得本发明结构内部流体工质的流动均匀性更好,从而提升本发明结构整体的换热能力。
11.第三,由于本发明采用整齐且密集的散热鳍片,克服了现有结构在单位面积上对流换热系数过小、散热能力低、阻力和压降大的不足,由此使得本发明结构具有更小的水力直径,更低的阻力和压降,并在单位面积上具有更强的换热能力。
附图说明
12.图1是本发明整体结构示意图;
13.图2是本发明中装配有电极的上底板结构示意图;
14.图3是本发明中上底板尺寸图;
15.图4是本发明中下底板结构示意图;
16.图5是本发明中下底板尺寸图;
17.图6是本发明棒状金属电极主视和俯视图;
18.图7是本发明网状金属电极主视和俯视图;
19.图8是本发明整体结构俯视图及a-a截面全剖视图;
20.图9是本发明整体结构主视图及b-b截面全剖视图。
具体实施方式
21.下面结合附图和实施例,对本发明做进一步的描述。
22.参照图1和实施例,对本发明的整体结构做进一步的描述。
23.本发明包括上底板1、下底板2、流体入口3、流体出口4、散热鳍片5、棒状金属电极6、网状金属电极7。
24.参照图2装配有电极的上底板结构示意图、图3上底板尺寸图和实施例,对本发明上底板的结构做进一步的描述。
25.所述上底板1为长方体底板,四周成型有凸台,中间设置有圆角矩形的腔体,上底板1上沿平行于电流体流动方向交错设置有13行5列,共33对通孔,所述每对通孔是由一对圆形通孔与一对矩形通孔组成的,每对圆形通孔是由一个粗圆形通孔和一个细圆形通孔组成的,每对矩形通孔是由一个宽矩形通孔和一个窄矩形通孔组成的,上底板1采用陶瓷材料。
26.本发明实施例中上底板1为长方体底板,其长度为100mm、宽度为60mm、高度为7mm,材料为抗腐蚀性好、绝缘性好的si3n4。所述上底板1四周成型有凸台,中间设置有圆角矩形的腔体,凸台高度3.5mm,凸台四周宽度为4mm,圆角矩形腔体四角的圆弧半径为10mm;所述上底板1沿如图2所示的平行于电流体流动的方向,交错设置有13行5列共33对通孔。其中,相邻且距离为2.5mm的一个宽矩形通孔与一个窄矩形通孔组成一对矩形通孔,相邻且距离为2mm的一个粗圆形通孔与一个细圆形通孔组成一对圆形通孔。所述上底板1中位于同一行中左右相邻且距离为7.5mm的一对圆形通孔与一对矩形通孔组成一对通孔,上底板1的圆形通孔和矩形通孔的作用是固定棒状金属电极6和网状金属电极7。本发明为了防止相邻电极释放的强电场互相干扰,所以将上底板的通孔交错排布,并且每对通孔间距离不能过近,因此不同行中相邻通孔间的距离不同。另一方面,要保证本发明结构对流体工质的阻力不能过大,因此棒状金属电极6和网状金属电极7要平行于电流体流动方向排布,所以同一列中相邻通孔间的距离相同。由于不同行中相邻通孔间的距离不同,不同列中通孔间的距离相同,所以将行按通孔间距离是否相同分为奇数行和偶数行,对不同列不进行区分。其中,同一奇数行中相邻通孔间的距离为29mm,同一偶数行中相邻通孔间的距离为33mm,全部列中相邻通孔间的距离相同,距离均为8mm。窄矩形通孔尺寸长为3mm、宽为1mm,宽矩形通孔尺寸长为3mm、宽为1.5mm,细圆形通孔直径为1mm,粗圆形通孔直径为1.5mm。
27.所述流体入口3、流体出口4为直径相同的圆形通孔,流体入口3位于上底板1的左侧,流体出口4位于上底板1的右侧,流体入口3和流体出口4位于上底板1的短边的中心线两侧,且二者关于上底板1长边的中心线对称。
28.本发明实施例中,上底板1的长边两侧设置有直径相等的两个圆形通孔,二者关于长边中心线对称。两圆形通孔中左侧为流体入口3,右侧为流体出口4,二者的直径均为6mm。流体入口3的圆心距上底板1的下边缘30mm,左边缘8mm,流体出口4的圆心距上底板1的下边缘30mm,距右边缘8mm。
29.参照图4下底板结构示意图、图5下底板尺寸图和实施例,对本发明下底板的结构做进一步的描述。
30.所述下底板2为长方体底板,其长度和宽度与上底板1对应相等,其上表面与上底板1的下表面通过导热胶进行粘结,二者共同形成了供电流体流动的圆角矩形的密封腔体,下底板2采用半导体材料。
31.本发明实施例中下底板2为长方体底板,其长度和宽度与上底板1对应相等,长度为100mm、宽度为60mm、高度为7mm,材料为与电子元器件兼容性好的si。所述下底板2的上表面沿如图4所示的平行于电流体流动方向,通过反应离子刻蚀法,均匀刻蚀多条薄长方体形状的散热鳍片5。下底板2的所有散热鳍片5高度相同,散热鳍片5分为长散热鳍片5.1和短散热鳍片5.2两种。下底板2上的全部长散热鳍片5.1有8行
×
1列共8条,每条长散热鳍片5.1长度为60mm、宽度为0.4mm、高度为3.5mm,同一列中相邻长散热鳍片5.1间的距离为3.6mm,长散热鳍片5.1按行分为8行,按从上到下的顺序依次为第1至第8行,其中第1行与下底板2的上边缘距离为5mm,与左右边缘距离为15mm。每条短散热鳍片5.2宽度均为0.45mm,高度均为3.5mm,4条相邻的长度相同的短散热鳍片5.2组成一组短散热鳍片组,同一组中相邻短散热鳍片5.2间的距离为0.35mm,下底板2上的所有短散热鳍片组有13行
×
5列共32组,用于提高对流换热系数。由于不同行中相邻短散热翅片组间的数量不同,所以将短散热翅片组按行分为13行,按从上到下的顺序以此为1行、2行~12行、13行,其中奇数行中有两组短散热翅片组,偶数行中有3组短散热翅片组,每行中相邻的短散热鳍片组之间距离均为13mm,第1行与下底板2的上边缘距离为5.4mm,与左右边缘距离为28mm,第2行与下底板2的上边缘距离为9.75mm,与左右边缘距离为15mm,其他行依此类推。将短散热翅片组按列分为5列,按从左向右的顺序依次为第1至第5列,其中第1、第5列的短散热翅片组长度为13mm,第2、第4列的短散热翅片组长度为16mm,第3列的短散热翅片组长度为20mm,每列中相邻短散热鳍片组之间的距离为5.15mm。下底板2的中央区域刻蚀有散热鳍片5,该区域长70mm、宽52.4mm,与下底板2的上下边缘的距离为5mm,与下底板2的左右边缘距离为15mm。所述下底板2的上表面无散热鳍片5的区域,与涂抹有导热胶的上底板1四周的凸台的下表面进行紧密粘结,使上底板1和下底板2共同形成供电流体流动的圆角矩形的密封腔体。
32.所述散热鳍片5形状为薄长方体,通过反应离子刻蚀法,均匀刻蚀于下底板2的上表面,所有散热鳍片5的长边均严格平行于电流体流动方向,相邻两条散热鳍片5之间的距离不超过0.5mm;下底板2的中央区域设置有散热鳍片5,所有的散热鳍片5的高度相等;散热鳍片5分为长散热鳍片5.1和短散热鳍片5.2两种,下底板2的长度至少是每条短散热鳍片5.2的长度的5倍,每条长散热鳍片5.1的长度至少是每条短散热鳍片5.2长度的3倍,相邻两条长散热鳍片5.1之间设置有2~3组短散热鳍片组;下底板2上共设置8行
×
1列共8条的长散热鳍片5.1,共设置13行
×
5列共32组的短散热鳍片组,4条相邻的长度相同的短散热鳍片5.2组成一组短散热鳍片组。
33.参照图6棒状金属电极主视和俯视图和实施例,对本发明棒状金属电极的结构做
进一步的描述。
34.所述每对棒状金属电极6均由形状为圆柱体的一个粗棒状金属电极和一个细棒状金属电极组成,二者高度相等,半径不同,一粗一细,每对棒状金属电极6均采用金属材料;每个粗棒状金属电极均通过导热胶粘结于上底板1的粗圆形通孔内,每个细棒状金属电极均通过导热胶粘结于上底板1的细圆形通孔内,每对棒状金属电极6的上表面均与上底板1的上表面重合;每个粗棒状金属电极接直流电源正极,每个细棒状金属电极接直流电源负极。
35.本发明实施例中共有33对粘结在上底板1上的棒状金属电极6。每对棒状金属电极6中包括一个粗棒状金属电极和一个细棒状金属电极,粗棒状金属电极和细棒状金属电极的形状均为圆柱体,安装在同一对圆形通孔中的一个粗棒状金属电极和一个细棒状金属电极称为一对棒状金属电极6。如图3所示,每个粗棒状金属电极通过导热胶粘结于上底板1的每个粗圆形通孔内,每个细棒状金属电极通过导热胶粘结于上底板1的每个细圆形通孔内,每对棒状金属电极6的上表面均与上底板1的上表面重合。本发明实施例中的细棒状金属电极直径为1mm,高度均为6.5mm,粗棒状金属电极直径为1.5mm,高度为6.5mm,每对棒状金属电极6材料均为不锈钢。
36.参照图7网状金属电极主视和俯视图和实施例,对本发明网状金属电极的结构做进一步的描述。
37.所述每对网状金属电极7均由形状为长方体的一个宽网状金属电极和一个窄网状金属电极组成,二者的长度和高度相等,宽度不同,一宽一窄,在金属网状电极7的一半部分均匀设置有3行3列共9个圆形通孔,每个圆形通孔的直径均相等,每对网状金属电极7均采用金属材料;每个宽网状金属电极均通过导热胶粘结于上底板1的宽矩形通孔内,每个窄网状金属电极均通过导热胶粘结于上底板1的窄矩形通孔内,每对网状金属电极7的上表面均与上底板1的上表面重合;每个宽网状金属电极接直流电源正极,每个窄网状金属电极接直流电源负极。
38.本发明实施例中的共有33对粘结在上底板1上的网状金属电极7,棒状金属电极6和网状金属电极7的数量相同,一对棒状金属电极6和一对网状金属电极7粘结同一对通孔中,组成一对电极,本发明实施例中共有33对电极。每对网状金属电极7中包括一个宽网状金属电极和一个窄网状金属电极,宽网状金属电极和窄网状金属电极的形状均为长方体。安装在同一对矩形通孔中的网状金属电极7称为一对网状金属电极。如图3所示,每个宽网状金属电极通过导热胶粘结于上底板1的每个宽矩形通孔内,每个窄网状金属电极通过导热胶粘结于上底板1的每个窄矩形通孔内,每对网状金属电极7的上表面均与上底板1的上表面重合。本发明实施例中的窄网状金属电极长3.5mm、宽1mm、高6.5mm,宽窄网状金属电极长3.5mm、宽2mm、高6.5mm,每对网状金属电极7材料均为不锈钢。本发明实施例为了减小阻力,以保证电流体能顺利在流道中流动,在每个网状金属电极的一半部分均匀设置有3行3列共9个圆形通孔,每个圆形通孔的直径都相等,均为0.75mm,每行中相邻的圆形通孔的距离为0.9mm,每列中相邻圆形通孔的距离为1mm,9个圆形通孔中,最左下端的圆形通孔距离网状金属电极下表面的距离为0.5mm,距离左边缘的距离为0.6mm。
39.参照图8的a-a截面剖视图、图9的b-b截面剖视图和实施例,对本发明实施例的结构做进一步的描述。
40.因为本发明实施例的上底板1与下底板2需要装配在一起使用,所以粘接在上底板1上的棒状金属电极6和网状金属电极7不能和下底板2的全部散热鳍片干涉,因此下底板2的全部散热鳍片5需要交错排布。本发明实施例中的每对棒状金属电极6中的粗棒状金属电极接直流电源正极,细棒状金属电极接直流电源负极,每对网状金属电极7中的宽网状金属电极接直流电源正极,窄网状金属电极接直流电源负极。
41.本发明所述的一种泵与散热器一体的微通道散热器工作过程如下:
42.在使用本发明实施例之前,应先将流体入口3和流体出口4与外部流体循环系统连接起来,使电流体充满本发明实施例的整个腔体内。由于电流体是一种流体,所以其具有流体的基本特性,并且在强电场的作用下电流体会随电场线的方向流动,因此可直流电源直接与棒状金属电极6和网状金属电极7接通,使每对棒状金属电极6和网状金属电极7之间产生强电场,从而在本发明实施例内部流动的电流体中产生库仑力,最终利用电液动力效应驱使电流体流动,直接在本发明实施例的内部腔体中产生泵送效果。
43.当本发明实施例出现局部热流密度过高,或者内部电流体流速不均匀等情况,可以单独提升加载在某几个通道内的棒状电极6和网状金属电极7上的电流,提升相应通道内电流体的流动速度,由此使得本发明实施例内部流动的电流体获得良好的流动特性,从而提升本发明实施例局部的对流换热系数,最终达到在整体上达到提升本发明实施例换热能力的目的。