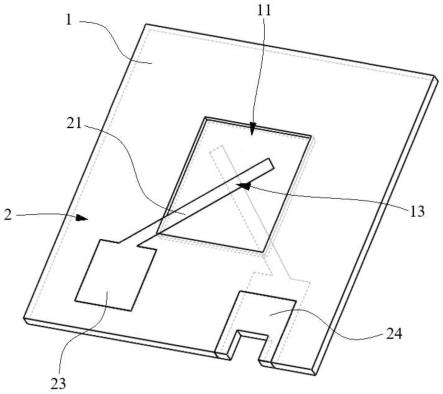
1.本发明涉及石英谐振器技术领域,尤其涉及一种石英谐振器晶片及制造方法。
背景技术:2.近几十年来,随着石英晶体谐振器朝高频化方向迅猛发展,研究学者们发现高基频at切石英谐振器有助于在在高速、大容量通信系统中实现高频率下的稳定性和低抖动。国内迄今为止报道的at切基频石英谐振器为285mhz,这些超高基频石英谐振器也往往应用在基站等大容量通信系统中。
3.at切石英晶体谐振器的厚度剪切振动频率可以通过减小石英振动区域的厚度来提高。例如申请号为:cn202111456065.3的中国发明专利,名称为:一种高基频石英晶体谐振器,包括用于安装石英晶片(11) 的陶瓷基座,石英晶片(11)上有上下对称的上电极(9)和下电极(10),该装置工艺简单,结构新颖,且具有高机电转换效率,超高频率,高品质因数q值,频率范围为50mhz~200mhz。通常石英晶片在设计时应保证上电极和下电极在振动区域上的投影面积重叠,以提高石英晶片的稳定性,但在大批量生产中无法保证每块石英晶片两侧的电极在石英晶片上的投影面积重叠后能完全一致,从而使得大批量生产的石英晶片存在各项电性能参数不一致性的问题。
4.因此,亟需一种石英谐振器晶片及制造方法,用于解决现有技术中因大批量生产中无法保证每块石英晶片两侧的电极在石英晶片上的投影面积重叠后能完全一致,从而导致大批量生产的石英晶片存在各项电性能参数不一致性的问题。
技术实现要素:5.有鉴于此,有必要提供一种石英谐振器晶片及制造方法,解决现有技术中因大批量生产中无法保证每块石英晶片两侧的电极在石英晶片上的投影面积重叠后能完全一致,从而导致大批量生产的石英晶片存在各项电性能参数不一致性的技术问题。
6.为达到上述技术目的,本发明的技术方案提供一种石英谐振器晶片,包括:
7.晶片本体,所述晶片本体开设有第一凹槽和第二凹槽,所述第一凹槽和所述第二凹槽分别相对设置于所述晶片本体的两对侧;
8.电极组件,包括第一电极和第二电极,所述第一电极沿第一方向设置,所述第一电极连接于所述第一凹槽的底部内壁,并延伸连接于所述晶片本体的一侧的外壁,所述第一电极在所述第一凹槽的底部形成有第一投影,所述第二电极沿第二方向设置,所述第二电极连接于所述第二凹槽的底部内壁,并延伸连接于所述晶片本体的另一侧的外壁,所述第二电极在所述第二凹槽的底部形成有第二投影,所述第二方向与所述第一方向相交设置,用于使得所述第一投影和第二投影在所述晶片本体上形成相互重叠且重叠面积不变的振动区域。
9.进一步的,所述第一凹槽和第二凹槽分别镜像设置于所述晶片本体的两对侧,且所述第一电极和第二电极分别相对所述第一凹槽或第二凹槽的中轴线倾斜设置,并设置于
所述第一凹槽或第二凹槽的中轴线的两侧。
10.进一步的,所述第一电极在所述晶片本体的一侧的外壁形成有第一电极激励区,用于将所述第一电极与外部相电性连接。
11.进一步的,所述第二电极在所述晶片本体的外壁形成有第二电极激励区,且所述第二电极激励区经由所述晶片本体的另一侧的外壁延伸连接于所述晶片本体的一侧的外壁,用于将所述第二电极与外部相电性连接。
12.进一步的,所述第一电极、第二电极、第一电极激励区及第二电极激励区的材质均为铝。
13.进一步的,所述晶片本体的长度尺寸为2000~2800μm,宽度尺寸为 1900~2500μm,外形厚度尺寸为50~100μm。
14.进一步的,所述第一凹槽或第二凹槽的长度尺寸为700~1000μm,宽度尺寸为700~1000μm,厚度为尺寸0.3~1.7μm。
15.进一步的,所述第一电极的长度尺寸为100~200μm,宽度尺寸为 60~150μm,厚度尺寸为50~200nm。
16.进一步的,所述第二电极的长度尺寸为100~200μm,宽度尺寸为 60~150μm,厚度尺寸为50~200nm。
17.本发明的技术方案还提供一种石英谐振器晶片制造方法,其特征在于,包括如上所述的石英谐振器晶片,包括如下步骤:
18.s1、依次在石英基板的表面分别形成厚度均匀的镀金层和第一光刻抗刻蚀保护层er,在第一光刻抗刻蚀保护层er表面形成第一凹槽、第二凹槽及晶片本体的外形通孔;
19.s2、去除石英基板的表面的金掩膜,并在石英基板的表面形成厚度均匀的镀铝层,并在镀铝层的表面形成厚度均匀的第二光刻抗刻蚀保护层er;
20.s3、在第二光刻抗刻蚀保护层er表面形成第一电极、第一电极激励区、第二电极及第二电极激励区的外形,并通过显影、蚀刻方式形成第一电极、第一电极激励区、第二电极及第二电极激励区;
21.s4、去除第二光刻抗刻蚀保护层er,并清洗石英基板;
22.s5、在石英基板上加工切割定位孔,并经切割加工得到晶片本体。
23.与现有技术相比,本发明的有益效果包括:第一电极连接于第一凹槽的底部内壁,第二电极连接于第二凹槽的底部内壁,其中第一电极沿第一方向设置,第二电极沿第二方向设置,且第二方向与第一方向相交设置,使得第一电极在第一凹槽的底部内壁所形成的第一投影与第二电极在第二凹槽的底部内壁所形成的第二投影相重叠,且重叠面积不变的振动区域,相比于现有技术,经批量化生产的石英晶片,即使每一块石英晶片中第一电极和第二电极的安装位置不一样,但由于第一投影和第二投影在晶片本体上形成有重叠面积不变的振动区域,从而使得每个石英晶片的各项电性能参数一致,因此能用于解决因大批量生产所导致的石英晶片存在各项电性能参数不一致性的技术问题。
附图说明
24.图1是本发明实施例所提供的一种石英谐振器晶片的三维结构示意图;
25.图2是本发明实施例所提供的一种石英谐振器晶片的俯视图;
26.图3是本发明实施例所提供的一种石英谐振器晶片的仰视图。
具体实施方式
27.下面结合附图来具体描述本发明的优选实施例,其中,附图构成本技术一部分,并与本发明的实施例一起用于阐释本发明的原理,并非用于限定本发明的范围。
28.请参阅图1,本发明提供了一种石英谐振器晶片,包括:晶片本体1 和电极组件2,晶片本体1开设有第一凹槽11和第二凹槽12,第一凹槽 11和第二凹槽12分别相对设置于晶片本体1的两对侧,电极组件2包括第一电极21和第二电极22,第一电极21沿第一方向设置,第一电极21 连接于第一凹槽11的底部内壁,并延伸连接于晶片本体1的一侧的外壁,第一电极21在第一凹槽11的底部形成有第一投影,第二电极22沿第二方向设置,第二电极22连接于第二凹槽12的底部内壁,并延伸连接于晶片本体1的另一侧的外壁,第二电极22在第二凹槽12的底部形成有第二投影,第二方向与第一方向相交设置,用于使得第一投影和第二投影在晶片本体1上形成相互重叠且重叠面积不变的振动区域13。
29.本装置中,第一电极21连接于第一凹槽11的底部内壁,第二电极 22连接于第二凹槽12的底部内壁,其中第一电极21沿第一方向设置,第二电极22沿第二方向设置,且第二方向与第一方向相交设置,使得第一电极21在第一凹槽11的底部内壁所形成的第一投影与第二电极22在第二凹槽12的底部内壁所形成的第二投影相重叠,且重叠面积不变的振动区域13,相比于现有技术,经批量化生产的石英晶片,即使每一块石英晶片中第一电极21和第二电极22的安装位置不一样,但由于第一投影和第二投影在晶片本体1上形成有重叠面积不变的振动区域13,从而使得每个石英晶片的各项电性能参数一致。
30.可以理解,本发明利用石英晶片内凹槽的设计一方面实现凹槽内高基频的厚度剪切振动,另一方面又通过凹槽四周的外形部分提高了晶片的强度,提高其在加工制造过程中的良率。
31.进一步地,本发明利用湿法腐蚀工艺结合光刻工艺制作掩膜实现了高基频石英晶片的结构设计,使腐蚀后凹槽内部的表面形貌良好,有助于提高谐振器的谐振性能。
32.进一步地,本发明使用的上下电极的交叉结构,其交叉部分形成的振动区域13面积不会随着电极位置的偏移而产生变化,这能有效保证包括电阻在内的各项电性能参数的稳定。
33.进一步地,为了方便将每个晶片本体1从石英基板上进行分割,晶体本体1上开设有外形通孔,此处为本领域技术人员所公知的常规设置,不作过多阐述。
34.如图1至图3所示,第一凹槽11和第二凹槽12分别镜像设置于晶片本体的两对侧,且第一电极21和第二电极22分别相对第一凹槽11或第二凹槽12的中轴线倾斜设置,并设置于第一凹槽11或第二凹槽12的中轴线的两侧。
35.可以理解,为了更好的保证各项电性能参数的一致性,第一凹槽11 和第二凹槽12相同,并镜像设置于晶片本体1的两对侧。
36.其中,如图1、图2所示,第一电极21在晶片本体1的一侧的外壁形成有第一电极激励区23,用于将第一电极21与外部相电性连接。
37.其中作为一种实施方式,如图1、图3所示,第二电极22在晶片本体1的外壁形成有第二电极激励区24,且第二电极激励区24经由晶片本体1的另一侧的外壁延伸连接于晶片
本体1的一侧的外壁,用于将第二电极22与外部相电性连接。
38.可以理解,第一电极激励区23和第二电极激励区24设置于晶片本体1的同一侧,用于方便使用者选择不同的外部电连接方式,扩大本装置的适用范围。
39.其中作为一种较佳的实施方式,第一电极21、第二电极22、第一电极激励区23及第二电极激励区24的材质均为铝。
40.可以理解,本发明使用铝电极,相较于通常使用的金电极能极大地减轻凹槽的质量负载效应,减小晶片制作过程中的返回量。
41.进一步地,第一电极激励区23和第二电极激励区24的设置为本领域技术人员所公知的常规设置,此处不作过多阐述。
42.进一步地,晶片本体1的长度尺寸为2000~2800μm,宽度尺寸为 1900~2500μm,外形厚度尺寸为50~100μm。
43.进一步地,第一凹槽11或第二凹槽12的长度尺寸为700~1000μm,宽度尺寸为700~1000μm,厚度为尺寸0.3~1.7μm。
44.进一步地,第一电极21的长度尺寸为100~200μm,宽度尺寸为 60~150μm,厚度尺寸为50~200nm。
45.进一步地,第二电极22的长度尺寸为100~200μm,宽度尺寸为 60~150μm,厚度尺寸为50~200nm。
46.本发明还提供一种石英谐振器晶片制造方法,包括如上述的石英谐振器晶片,包括如下步骤:
47.s1、首先取出一定规格的石英基板,并对石英基板的上、下表面进行研磨、抛光处理,接着通过溅射或蒸镀方式在石英基板两侧表面形成厚度均匀的镀金层,通过旋涂或喷淋方式在石英基板表面形成厚度均匀的第一光刻抗刻蚀保护层er,然后使用光刻曝光在第一光刻抗刻蚀保护层er上,在表面形成待刻蚀图形,最后通过显影、蚀刻和腐蚀方式在石英基板上形成第一凹槽11和第二凹槽12及外形通孔;
48.s2、去除石英基板上的金掩膜并通过溅射或蒸镀方式在石英基板两侧表面形成厚度均匀的镀铝层,通过旋涂或喷淋方式在石英基板表面形成厚度均匀的第二光刻抗刻蚀保护层er,然后使用光刻曝光在第二光刻抗刻蚀保护层er上,在表面形成待刻蚀图形;
49.s3、通过显影、蚀刻方式在石英基板上形成第一电极21、第一电极激励区23、第二电极22及第二电极激励区24;
50.s4、去除第二光刻抗刻蚀保护层er并将石英基板表面清洗干净,从而制得具有铝电极结构的压电石英晶片;
51.s5、在石英基板上加工出切割定位孔,使用激光切割或刀片切割沿着切割定位孔对石英基板进行切割分离,从而实现了石英晶片的加工。
52.本发明的具体工作流程,第一电极21连接于第一凹槽11的底部内壁,第二电极22连接于第二凹槽12的底部内壁,其中第一电极21沿第一方向设置,第二电极22沿第二方向设置,且第二方向与第一方向相交设置,使得第一电极21在第一凹槽11的底部内壁所形成的第一投影与第二电极22在第二凹槽12的底部内壁所形成的第二投影相重叠,且重叠面积不变的振动区域13,相比于现有技术,经批量化生产的石英晶片,即使每一块石英晶片中第一电极21和第二电极22的安装位置不一样,但由于第一投影和第二投影在晶片本体1上形
成有重叠面积不变的振动区域13,从而使得每个石英晶片的各项电性能参数一致,因此能用于解决因大批量生产所导致的石英晶片存在各项电性能参数不一致性的技术问题。
53.使用者在得到本发明中的石英晶片时,首先取出一定规格的石英基板,并对石英基板的上、下表面进行研磨、抛光处理,接着通过溅射或蒸镀方式在石英基板两侧表面形成厚度均匀的镀金层,通过旋涂或喷淋方式在石英基板表面形成厚度均匀的第一光刻抗刻蚀保护层er,然后使用光刻曝光在第一光刻抗刻蚀保护层er上,在表面形成待刻蚀图形,最后通过显影、蚀刻和腐蚀方式在石英基板上形成第一凹槽11和第二凹槽 12及外形通孔;
54.进一步地,去除石英基板上的金掩膜并通过溅射或蒸镀方式在石英基板两侧表面形成厚度均匀的镀铝层,通过旋涂或喷淋方式在石英基板表面形成厚度均匀的第二光刻抗刻蚀保护层er,然后使用光刻曝光在第二光刻抗刻蚀保护层er上,在表面形成待刻蚀图形;
55.进一步地,通过显影、蚀刻方式在石英基板上形成第一电极21、第一电极激励区23、第二电极22及第二电极激励区24;
56.进一步地,去除第二光刻抗刻蚀保护层er并将石英基板表面清洗干净,从而制得具有铝电极结构的压电石英晶片;
57.进一步地,在石英基板上加工出切割定位孔,使用激光切割或刀片切割沿着切割定位孔对石英基板进行切割分离,从而实现了石英晶片的加工。
58.通过上述结构,能解决现有技术中因大批量生产中无法保证每块石英晶片两侧的电极在石英晶片上的投影面积重叠后能完全一致,从而导致大批量生产的石英晶片存在各项电性能参数不一致性的技术问题。
59.以上所述,仅为本发明较佳的具体实施方式,但本发明的保护范围并不局限于此,任何熟悉本技术领域的技术人员在本发明揭露的技术范围内,可轻易想到的变化或替换,都应涵盖在本发明的保护范围之内。