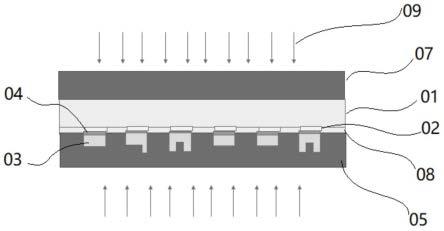
1.本发明涉及厚铜电路板技术领域,具体涉及一种在无机基材表面制作厚铜电路的方法。
背景技术:2.厚铜电路一般用于大电流高电压的高功率能源器件所需陶瓷基电路板中,一些瞬时功率较大的电路板,铜的厚度超过200μm以上,甚至达到400μm。这类电路目前主要采用dbc或amb技术方案生产陶瓷基覆铜板,然后通过蚀刻制造。dbc是将铜在高温下通过热熔结合的方法直接与al2o3和aln陶瓷表面结合而成的复合基板,在覆铜表面上,可以根据电路设计或产品结构蚀刻相应的图案,已经广泛用于智能电源模块和电动汽车电源模块的封装。amb技术是dbc技术的进一步发展,是利用焊料中的活性金属元素(如ti/ag/zr/cu)实现陶瓷与金属结合的方法,陶瓷形成可被液态焊料润湿的反应层。但dbc和amb工艺过程都是在800℃以上进行,属于高能耗的制造方法。同时,蚀刻的方案,也属于水体污染严重的制造模式。
3.因此,仍需一种低能耗低污染的高功率器件用厚铜陶瓷基载板的绿色制造方法。
技术实现要素:4.为解决现有技术存在的问题,本发明提供一种在无机基材表面制作厚铜电路的方法,采用微纳米复合浆料,能够在300℃以下,实现厚铜电路与陶瓷基板的低温粘结,实现低能耗低污染的高功率器件陶瓷基载板的绿色制造。
5.为实现以上发明目的,本发明采用如下的技术方案:
6.一种在无机基材表面制作厚铜电路的方法,包括以下步骤:
7.1)在无机基材表面预置一层金属种子层;
8.2)制备厚金属箔;
9.3)在金属种子层或厚金属箔的至少任一表面涂覆微纳米复合浆料;
10.4)涂覆后的微纳米复合浆料预干燥;
11.5)将厚金属箔和金属种子层基板对应图形位置面对面压在一起,并在真空压机中压合制成厚铜电路。
12.在一个具体的实施方案中,所述步骤1)中所述无机基材选自无机非金属材料、热变形温度在压合温度以上的绝缘材料或带有绝缘表层的材料(如表面有氧化铝层的铝板,硅片、水泥)中的任一种,优选为玻璃、陶瓷;优选地,所述金属种子层通过溅射、化学镀、真空气相沉积、电镀、印刷烧结、冷喷或活性焊料的方法预置而成;更优选地,所述金属种子层的厚度为0.1μm-10μm,所述金属种子层带有电路图案或不带有电路图案;进一步优选地,当金属种子层不带有电路图案时,需将金属种子层进一步加工做成电路图形;加工方法选自图形化学蚀刻或激光烧蚀、印刷、掩膜溅射、掩膜化学镀中的任一种。
13.在一个具体的实施方案中,所述步骤2)中的厚金属箔采用延压或者电镀成型的方
法制成整张金属箔,通过模具冲压成所需电路图形。
14.在一个具体的实施方案中,所述步骤3)中所述微纳米复合浆料由80-95%金属粉体、0.5-10%树脂、0.5-15%的溶剂、0.5-5%的活性剂组成;优选地,所述金属粉体中微米金属粉体与纳米金属粉体的质量比为9:1~5:5,所述金属粉体与树脂的质量比不低于9:1;更优选地,所述微米金属粉体选自铜、银、金、锡、铋、铝、铅或其合金粉体中的任一种或多种组合,粒径在0.5至100μm;所述纳米金属粉体选自为铜、银、锡、铋、铅或其合金粉体中的任一种或多种组合,粒径在10至200nm。
15.在一个具体的实施方案中,所述树脂为tg点在压合温度以下的热塑性树脂,优选为热塑性丙烯酸酯树脂、聚酯树脂、聚氨酯树脂、聚乙酸乙烯酯、纤维素、聚氯乙烯、氯醋树脂中的任一种。
16.在一个具体的实施方案中,所述溶剂为沸点在60至200℃的醇、醚、酯、酮类溶剂,优选沸点在80至120℃;优选地,所述溶剂选自异丙醇、乙二醇、乙二醇丁醚、醋酸丁酯、丁酮中的至少任一种。
17.在一个具体的实施方案中,所述活性剂为有机酸或无机酸;优选地,所述有机酸选自柠檬酸、苹果酸、酒石酸、乙酸、丁二酸、戊二酸、衣康酸、邻羟基苯甲酸、葵二酸、庚二酸、草酸或活性松香类中的任一种,所述无机酸选自盐酸、硝酸、硼酸、硫酸、碳酸、磷酸中的任一种。
18.在一个具体的实施方案中,所述步骤4)中涂覆后的微纳米复合浆料在100℃以下干燥挥发掉溶剂成分。
19.在一个具体的实施方案中,所述步骤5)中通过销钉、槽、视觉mark点中的任一种方式实现厚金属箔和金属种子层基板对应图形位置面对面压在一起;优选地,压合界面无图形位置设有1-50μm厚的软性垫板,所述软性垫板的材料选自硅胶、聚四氟、橡胶、聚氨酯中的任一种高温无粘性的材料;更优选地,真空压机中压合温度为100-300℃,优选220-250℃;压合压力1-10mpa,压合时间》10min。
20.在一个具体的实施方案中,通过反复压合实现台阶状的立体厚铜结构;或者冲压或切削成下表面平整的立体厚铜结构,然后压合在基板金属种子层表面,实现立体结构电路。
21.与现有技术相比,本发明具有以下有益效果:
22.本发明采用微纳米复合浆料,能够在300℃以下,实现厚铜电路与陶瓷基板的低温粘结,实现低能耗低污染的高功率器件陶瓷基载板的绿色制造。其中厚铜电路图形是通过冲裁金属或金属块形成,无蚀刻无化学污染,不仅环保,而且减少了水体污染处理费用,边角料可回收,降低综合制造成本。
23.本发明较低的工艺键合温度,除了能实现陶瓷基表面的金属基电路,还能进一步将带有电路图形的陶瓷基电路板直接连接在铝、铜或者其他金属热沉上,取代硅脂等导热性能低下的热界面材料,提升导热能力100倍以上。
附图说明
24.图1为本发明的方法步骤1)预置有金属种子层的基板示意图。
25.图2为本发明的方法步骤3)表面涂覆微纳复合金属浆料的厚金属箔示意图。
26.图3为本发明的方法步骤5)真空压合示意图。
27.图4为本发明的方法制成的厚铜电路示意图。
28.图5为本发明的方法多次压合台阶示意图。
29.图6为本发明的方法制成的立体结构电路示意图。
30.其中,01为基板、02带有图形的金属种子层、03厚金属箔、04微纳米复合浆料、05下模冲、06烘干、07上模冲、08软性垫板、09真空热压、10立体结构电路。
具体实施方式
31.为了使本发明要解决的技术问题,技术方案及有益效果更加清楚明白,以下结合附图,对本发明进行进一步详细说明。应当理解,此处所描述的具体实施仅仅用于解释本发明,并不用于限定本发明。
32.一种在无机基材表面制作厚铜电路的方法,包括以下步骤:
33.1)在无机基材表面预置一层金属种子层;
34.2)制备厚金属箔;
35.3)在金属种子层或厚金属箔的至少任一表面涂覆微纳米复合浆料;
36.4)涂覆后的微纳米复合浆料预干燥;
37.5)将厚金属箔和金属种子层基板对应图形位置面对面压在一起,并在真空压机中压合制成厚铜电路。
38.其中,步骤1)如图1所示,在基板01的表面预置一层结合力较强的金属种子层02,其中,基板可以是玻璃、陶瓷或其他基板,通常为陶瓷基板,金属种子层的厚度在0.1μm-10μm范围内。金属种子层可以带有电路图案或不带有电路图案,优选金属种子层带有电路图案。其中,不带有电路图案的整面金属种子层需要通过进一步加工,做成电路图形,加工方法包括但不限于图形化学蚀刻、激光烧蚀等。金属种子层可以通过溅射、化学镀、真空气相沉积、电镀、印刷烧结、冷喷、活性焊料等方法制作,使其与陶瓷基板形成较强的结合力。其中,金属种子层的金属包括但不限于铜、铝、钽、银、金、铅、锡等。
39.如图2所示,其中的厚金属箔03一般采用延压或者电镀成型的方法制成整张金属箔,通过模具冲压成所需电路图形。对于不相连接的电路图形,冲压后的金属箔要预置在模具内或固定平台表面,以保持其实际图形与设计图形的一致性。
40.然后在在图形化的厚金属箔03的表面涂覆微纳米复合浆料04,涂覆方法包括但不限于丝印、移印、喷涂、涂布、浸涂等。本领域技术人员可以理解的是,也可以在金属种子层表面涂覆微纳米复合浆料,或者在金属种子层和厚金属箔的表面同时都涂覆有微纳米复合浆料。
41.其中的微纳米复合浆料,由80-95%金属粉体、0.5-10%树脂、0.5-15%的溶剂、0.5-5%的活性剂组成。其中的微米金属粉:纳米金属粉的质量比例为9:1-5:5。金属粉体和树脂的比例不应低于9:1,否则过量的树脂会影响浆料对陶瓷基金属种子层和厚铜电路之间的冶金焊接。微米金属粉可以为铜、银、金、锡、铋、铝、铅或其合金粉体其中的一种或多种组合,粒径在0.5至100μm,过小不易分散,过大会形成焊层较厚、施工不均匀的问题。纳米金属粉可以为铜、银、锡、铋、铅或其合金粉体其中的一种或多种组合,粒径在10至200nm,过小表面稳定性差,过大影响结合强度。树脂为热塑性树脂,如热塑性丙烯酸酯树脂、聚酯树脂、
聚氨酯树脂等固体树脂,其tg点在压合温度以下,能促进压合过程中的粉体流动。溶剂为沸点在60至200℃区间的醇、醚、酯、酮类溶剂,进一步优选在80至120℃,如异丙醇、乙二醇、乙二醇丁醚、醋酸丁酯、丁酮,沸点过低不易于存储和长期施工,沸点过高干燥时间过长,会引起铜皮氧化。活性剂一般为有机或无机酸,用于在施工过程中同时去除金属种子层、厚铜电路、微米金属粉、纳米金属粉表面的氧化层或钝化层,使前三者能够在通过纳米金属粉烧结在一起。
42.涂覆后的微纳米复合浆料在100℃以下烘干06以挥发掉溶剂成分,该过程相当于预固化。
43.如图3所示,在上冲模07和下冲模05的辅助下,将图形化厚金属箔03和图形化金属种子层02基板01对应图形位置,面对面压在一起。对位方式包括但不限于通过销钉、槽、视觉mark点等方式实现。优选情况下,压合界面无图形的位置,有软性垫板08,软性垫板的材料可以为硅胶、聚四氟、橡胶等高温无粘性的材料,其到抑制微纳米复合浆料扩散,可局部缓冲的目的。软性垫板厚度一般在1-50μm。产品在真空压机中真空热压09,在100-300℃温度下压合,优选220-250℃。压合压力1-10mpa,压合时间》10min。
44.将厚金属箔和金属种子层基板对应图形位置面对面压在一起,并在真空压机中压合制成的厚铜电路如图4所示。
45.如图5所示,本发明的一个优选方案中进行反复多次压合,即重复步骤3)~5),涂覆一层微纳米复合浆料再压合,用于金属台阶间的键合,从而实现台阶状的立体厚铜结构,如图6所示。特别地,因为压合面必须平整,所以不管其他部位立体结构如何设计,在压合的界面需要表面平整,从而保证紧密压合形成立体结构。因此,需要冲压或切削成下表面平整的立体厚铜结构,然后压合在基板种子层表面,实现立体结构。
46.本发明的在无机基材表面制作厚铜电路的方法,实现了陶瓷基表面的金属基电路,从而可将带有电路图形的陶瓷基电路板直接连接在铝、铜或者其他金属热沉上,取代硅脂等导热性能低下的热界面材料,提升导热能力100倍以上。
47.而现有技术中,由于制造经济性的原因,电路基板和金属热沉是分开独立制作和采购的两种物料,然后在通过热界面材料(如硅脂)来连接两者,实现将电路基板上元器件生成的热能导向比热容较大的热沉上,保证元器件不会超温烧坏。硅脂作为热界面材料,是目前最常见的工艺方法,用于连接电路基板和金属热沉。硅脂的热导率在4w/m
·
k以下。而本发明直接将电路基板与金属热沉通过微纳米复合浆料连接在一起,热导率可以达到200-400w/m
·
k范围。
48.以上所述实施例仅表达了本发明的几种实施方式,其描述较为具体和详细,但并不能因此而理解为对发明专利范围的限制。应当指出的是,对于本领域的普通技术人员来说,在不脱离本发明构思的前提下,还可以做出若干变形和改进,这些都属于本发明的保护范围。因此,本发明专利的保护范围应以所附权利要求为准。