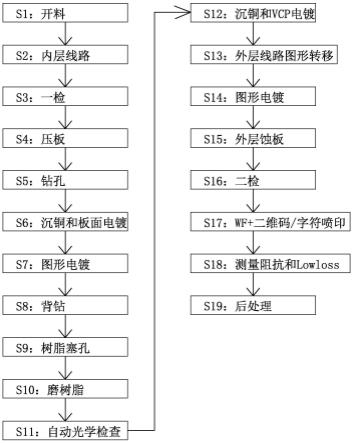
5g线路板pcb制作方法
1.本技术是分案申请,原申请的申请号为202110464268.0,申请日为2021年04月28日,发明名称为“5g主板线路板的生产方法”。
【技术领域】
2.本发明涉及线路板领域,具体涉及5g线路板pcb制作方法。
背景技术:3.伴随着通信技术的快速发展及5g的商用推广,作为5g产业链中最核心的材料,电子线路板(pcb)的设计和制造向高频高速化发展的趋势将不可阻挡,高频高速线路板pcb在5g通信领域的应用将进一步深化。5g在给pcb产业带来机遇的同时,也对技术提出了更高、更严苛的要求,其在信号传输速度、集成度、散热、多层化方面的指标均比4g提升了很多。现有5g线路板pcb制作方法为:开料、内层一检、压板、钻孔+首锣、沉铜/板面电镀、图形电镀(镀铜镀锡)、背钻、蚀刻、背钻测试、树脂塞孔、磨树脂、自动光学检查aoi、沉铜/vcp、外层线路、图电(镀锡)、外层蚀板)、二检(过ir炉)、wf+二维码、阻抗+low loss、高压测试、沉金、字符、锣板、et、fqc、pk。现有5g线路板pcb制作技术仍存在生产流程繁琐的缺陷,导致生产效率难以提高,以及难以降低生产成本。
技术实现要素:4.本发明解决了针对现有5g线路板pcb制作方法上存在生产流程繁琐的技术问题,本发明提供了结构简单、设计合理的5g线路板pcb制作方法。
5.本发明是通过以下技术方案实现的:
6.5g线路板pcb制作方法,包括以下步骤:
7.s1:开料,对覆铜板进行切割,以形成内层覆铜板;
8.s2:内层线路,在内层覆铜板板面铜箔贴上一层感光材料,蚀刻显影后形成内层线路图形;
9.s3:一检,对经过步骤s2后的内层覆铜板进行质量检测;
10.s4:压板,将通过质量检测的内层覆铜板与树脂胶片按预设排列方式进行排列,然后进行压合处理,以形成层压线路板;
11.s5:钻孔,在层压线路板进行钻出通孔;
12.s6:沉铜和板面电镀,其中沉铜为通过沉铜的方法在通孔内沉积出一层导通层压线路板中各层的铜层,以使通孔形成导通孔;板面电镀为采用全板电镀的方法对层压线路板进行电镀,以在层压线路板的导通孔和板面上形成导电铜层;
13.s7:图形电镀,使导电铜层达到预设的厚度;
14.s8:背钻,使用机械钻孔以使导通孔达到预设深度;
15.s9:树脂塞孔,使用真空树脂塞孔,导通孔分为树脂塞孔的孔和非树脂塞孔的孔;
16.s10:磨树脂,磨平树脂塞孔后多余的树脂;
17.s11:自动光学检查,检查塞孔饱满度;
18.s12:沉铜和vcp电镀,对树脂塞孔后的孔进行电镀填平,通过vcp电镀使非树脂塞孔的孔和板面上的铜厚达到预设成品铜层厚度;
19.s13:外层线路图形转移;在层压线路板的铜箔表面上贴上一层干膜感光材料,然后通过激光直接成像技术进行对位曝光,显影后形成线路图形;
20.s14:图形电镀,在线路图形镀上一层锡作为线路的防蚀刻保护层;
21.s15:外层蚀板,形成外层线路图形;
22.s16:二检,即过回流焊炉;
23.s17:wf+二维码/字符喷印,线路板上印上一层均匀的感光阻焊油墨;
24.s18:测量阻抗和lowloss,测量生产板中的阻抗模块及lowloss;
25.s19:后处理。
26.如上所述的5g线路板pcb制作方法,在步骤s4中,采用塑料铆钉进行压合处理。
27.如上所述的5g线路板pcb制作方法,在步骤s5中,通孔为一次性钻出,期间采用酚醛垫板生产,蜜胺垫板作盖板,盖板先钻好管位孔。
28.如上所述的5g线路板pcb制作方法,在步骤s8中,还包括以下步骤:
29.s801:使用机械钻孔以使导通孔达到预设深度;
30.s802:将无连接或者传输作用的通孔段钻掉;
31.s803:背钻后采用高压水洗;
32.s804:过数孔机全检铝片盖板防漏钻孔。
33.如上所述的5g线路板pcb制作方法,在步骤s10中,多余的树脂包括塞孔后孔口凸的树脂,以及板面上树脂。
34.如上所述的5g线路板pcb制作方法,在步骤s15中,还包括以下步骤:
35.s1501:退膜;
36.s1502:蚀刻;
37.s1503:一次褪锡;
38.s1504:褪干膜;
39.s1505:将干膜下方未受锡保护的部分铜蚀刻;
40.s1506:二次褪锡,直至露出锡下面的线路,即形成外层线路图形。
41.如上所述的5g线路板pcb制作方法,在步骤s16中,还包括以下步骤:
42.s1601:用光学检查设备检查外层线路;
43.s1602:将通过检测的线路板,过回流焊炉。
44.如上所述的5g线路板pcb制作方法,在步骤s19中,还包括以下步骤:
45.s1901:沉金;
46.s1902:锣板;
47.s1903:et;
48.s1904:fqc;
49.s1905:fqc。
50.如上所述的5g线路板pcb制作方法,在步骤s9中,还包括以下步骤:
51.s901:树脂塞孔前增加磨板;
52.s902:粗化铜面。
53.与现有技术相比,本发明的有如下优点:
54.本发明提供了5g线路板pcb制作方法,通过在步骤s7中取消镀锡流程和蚀刻流程,优化两道工序,解决现有生产技术流程繁琐问题。达到提供生产效率,降低生产成本的目的。
【附图说明】
55.为了更清楚地说明本发明实施例中的技术方案,下面将对实施例描述中所需要使用的附图作简单地介绍,显而易见地,下面描述中的附图仅仅是本发明的一些实施例,对于本领域普通技术人员来讲,在不付出创造性劳动的前提下,还可以根据这些附图获得其他的附图。
56.图1是本发明的工艺流程图。
【具体实施方式】
57.为了使本发明所解决的技术问题技术方案及有益效果更加清楚明白,以下结合附图及实施例,对本发明进行进一步详细说明。应当理解,此处所描述的具体实施例仅仅用以解释本发明,并不用于限定本发明。
58.当本发明实施例提及“第一”“第二”等序数词时,除非根据上下文其确实表达顺序之意,应当理解为仅仅是起区分之用。
59.在本发明的描述中,需要说明的是,除非另有明确的规定和限定,术语“安装”“相连”“连接”应做广义理解,例如,可以是固定连接,也可以是可拆卸连接,或一体地连接;可以是机械连接,也可以是电连接;可以是直接相连,也可以通过中间媒介间接相连,可以是两个元件内部的连通。对于本领域的普通技术人员而言,可以具体情况理解上述术语在本发明中的具体含义。
60.5g线路板pcb制作方法,包括以下步骤:
61.s1:开料,对覆铜板进行切割,以形成内层覆铜板;本实施例中采用高频高速覆铜板,切割完成后还对其表面进行清洗处理和烘干处理。
62.s2:内层线路,在内层覆铜板板面铜箔贴上一层感光材料,蚀刻显影后形成内层线路图形;在此步骤中采用黑菲林进行对位曝光的方法,蚀刻显影后形成内层线路图形。
63.s3:一检,对经过步骤s2后的内层覆铜板进行质量检测;
64.s4:压板,将通过质量检测的内层覆铜板与树脂胶片按预设排列方式进行排列,然后进行压合处理,以形成层压线路板;
65.s5:钻孔,在层压线路板进行钻出通孔;
66.s6:沉铜和板面电镀,其中沉铜为通过沉铜的方法在通孔内沉积出一层导通层压线路板中各层的铜层,以使通孔形成导通孔;板面电镀为采用全板电镀的方法对层压线路板进行电镀,以在层压线路板的导通孔和板面上形成导电铜层;
67.s7:图形电镀,使导电铜层达到预设的厚度;镀铜为了加厚孔内及线路铜层,提高镀层质量。
68.s8:背钻,使用机械钻孔以使导通孔达到预设深度;
69.s9:树脂塞孔,使用真空树脂塞孔,导通孔分为树脂塞孔的孔和非树脂塞孔的孔;
70.s10:磨树脂,磨平树脂塞孔后多余的树脂;
71.s11:自动光学检查,检查塞孔饱满度;本实施例中采用树脂塞孔专用自动光学检查机,100%检查塞孔饱满度;
72.s12:沉铜和vcp电镀,对树脂塞孔后的孔进行电镀填平,通过vcp电镀使非树脂塞孔的孔和板面上的铜厚达到预设成品铜层厚度;
73.s13:外层线路图形转移;在层压线路板的铜箔表面上贴上一层干膜感光材料,然后通过激光直接成像技术进行对位曝光,显影后形成线路图形;
74.s14:图形电镀,在线路图形镀上一层锡作为线路的防蚀刻保护层;
75.s15:外层蚀板,形成外层线路图形;
76.s16:二检,即过回流焊炉;采用光学检查设备检查外层线路开短路及外观不良等品质缺陷,检查完后,过回流焊炉,这样可以减少热应力,提高高频高速5g主板线路板尺寸稳定性。
77.s17:wf+二维码/字符喷印,线路板上印上一层均匀的感光阻焊油墨;将5g主板线路板字符的制作方式由丝印更改为喷印,与二维码追溯信息同时喷印:丝印字符制作,需要待pcb防焊油固化后,再经过网板丝印字符,最后再次经过高温烘烤字符,喷印字符是pcb在防焊油高温固化前喷印字符,喷印字符后随防焊油一起高温固化.与丝印相比,喷印制作方式减少一次高温流程,同时不再需要网板工具,生产效率极大提升。在线路板上印上一层均匀的感光阻焊油墨,以达到防焊、绝缘的目的,在阻焊油墨高温固化前做喷墨二维码追溯信息和标记字符。
78.s18:测量阻抗和lowloss,测量生产板中的阻抗模块及lowloss;
79.s19:后处理。
80.本发明提供了5g线路板pcb制作方法,通过在步骤s7中取消镀锡流程和蚀刻流程,优化两道工序,解决现有生产技术流程繁琐问题。达到提供生产效率,降低生产成本的目的。图电后背钻减少蚀刻工序,可以有效解决因蚀刻造成的咬蚀
‑‑‑
改善背钻stub值小,原流程设计是在外层线路、图形电镀、背钻和蚀刻,按此流程,背钻的stub为2.67mil,在做蚀刻时,背钻面露铜在蚀刻时没有锡保护,在蚀刻时stub被咬蚀后为0mil,导致5g信号测试失效;通过调整流程,取消背钻后蚀刻工序,可以有效解决因蚀刻造成的咬蚀,可以解决stub不良的问题。
81.进一步地,作为本方案的优选实施方式而非限定,在步骤s4中,采用塑料铆钉进行压合处理。主板高层线路板次外层设计要求3张p片构成,三张pp无法使用dis融合块,需从内层干菲林对位开始管控,用熔合+10头铆钉生产;压合工序采用塑料铆钉解决传统金属铆钉铆合过程产生的铆钉屑引起内层短路问题,调整铆钉长度,开花面朝上,解决打钉位铜箔皱折问题
82.进一步地,作为本方案的优选实施方式而非限定,在步骤s5中,通孔为一次性钻出,期间采用酚醛垫板生产,蜜胺垫板作盖板,盖板先钻好管位孔。钻孔时采用蜜胺垫板作底板及盖板,1.4mm以上的孔加盖板生产,盖板需钻管位孔,能够有效解决5g高频高速板材钻孔披锋的问题。
83.进一步地,作为本方案的优选实施方式而非限定,在步骤s8中,还包括以下步骤:
84.s801:使用机械钻孔以使导通孔达到预设深度;
85.s802:将无连接或者传输作用的通孔段钻掉;
86.s803:背钻后采用高压水洗;
87.s804:过数孔机全检铝片盖板防漏钻孔。
88.利用机械钻机的深度控制功能,在导通孔上用较大直径的钻刀钻具有一定深度要求的孔,钻掉没有起到任何的连接或者传输作用的通孔段,避免造成5g信号传输的反射、散射、延迟等,给信号带来“失真”,双面背钻,背钻后全部高压水洗,过数孔机全检铝片盖板防漏钻孔。
89.进一步地,作为本方案的优选实施方式而非限定,在步骤s10中,多余的树脂包括塞孔后孔口凸的树脂,以及板面上树脂。
90.进一步地,作为本方案的优选实施方式而非限定,在步骤s15中,还包括以下步骤:
91.s1501:退膜;
92.s1502:蚀刻;
93.s1503:一次褪锡;
94.s1504:褪干膜;
95.s1505:将干膜下方未受锡保护的部分铜蚀刻;
96.s1506:二次褪锡,直至露出锡下面的线路,即形成外层线路图形。
97.进一步地,作为本方案的优选实施方式而非限定,在步骤s16中,还包括以下步骤:
98.s1601:用光学检查设备检查外层线路;
99.s1602:将通过检测的线路板,过回流焊炉。
100.进一步地,作为本方案的优选实施方式而非限定,在步骤s19中,还包括以下步骤:
101.s1901:沉金;
102.s1902:锣板;
103.s1903:et;
104.s1904:fqc;
105.s1905:pk。
106.进一步地,作为本方案的优选实施方式而非限定,在步骤s9中,还包括以下步骤:
107.s901:树脂塞孔前增加磨板;
108.s902:粗化铜面。这样可以增强铜面与树脂结合力。针对5g主板线路板设计要求“5次回流焊后,树脂不分离”。因此为增加铜面的粗糙度,主板型号增加步骤s9处理”109.本实施例的工作原理如下:
110.本发明提供了5g线路板pcb制作方法,通过在步骤s7中取消镀锡流程和蚀刻流程,优化两道工序,解决现有生产技术流程繁琐问题。达到提供生产效率,降低生产成本的目的。
111.如上是结合具体内容提供的实施方式,并不认定本技术的具体实施只局限于这些说明。凡与本技术的方法结构等近似雷同,或是对于本技术构思前提下做出若干技术推演或替换,都应当视为本技术的保护范围。