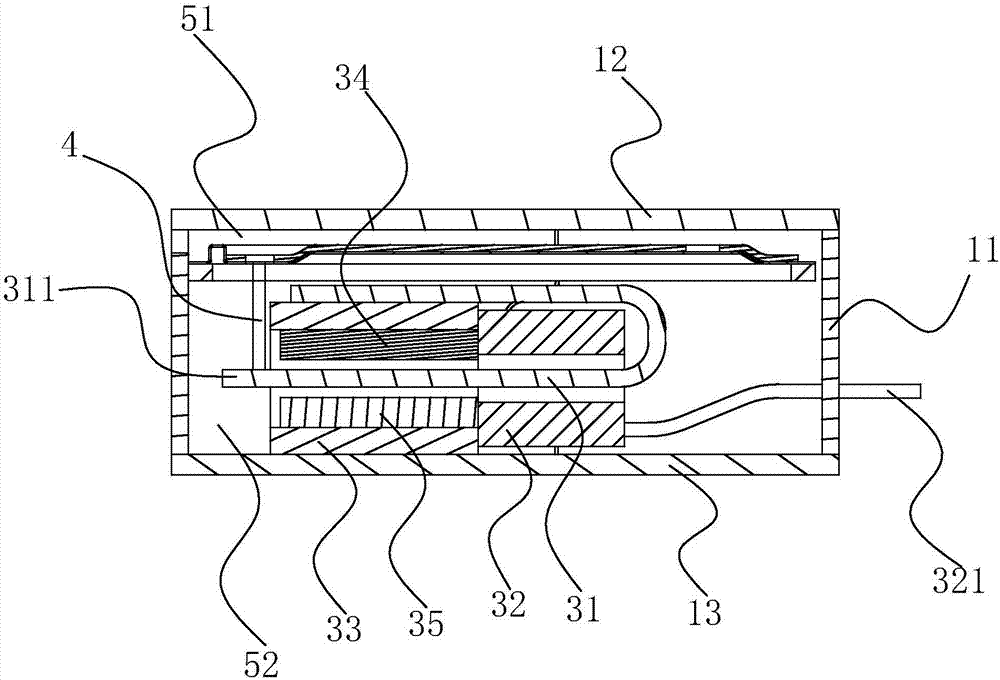
本发明属于受话器领域,更具体涉及一种适用于自动化生产的受话器。
背景技术
现有的受话器的壳体一般为上盒体和下盒体的分体结构,有深度的下盒体无法以带料的形式进行装配,使其装配过程较为繁琐,无法适应自动化装配工艺,浪费了大量的时间在装配上,生产效率极其低下。
技术实现要素:
本发明的目的是提供一种适用于自动化装配的受话器。
根据本发明的一个方面,提供了一种受话器,包括壳体以及位于所述壳体的腔体中的马达组件和膜片组件,所述马达组件和所述膜片组件通过连接杆连接,
所述壳体包括盒体以及分别与所述盒体连接的第一盖板和第二盖板,所述盒体顶部和底部分别为开口状,所述第一盖板覆盖所述盒体顶部的开口,所述第二盖板覆盖所述盒体底部的开口,
所述马达组件包括电枢、线圈、磁铁框以及位于所述磁铁框内的第一磁铁和第二磁铁,所述电枢为u型,所述线圈具有通道,所述第一磁铁和第二磁铁位于所述磁铁框内,所述第一磁铁和第二磁铁相对设置且不接触,所述电枢的一端与所述磁铁框的外壁连接,所述电枢的另一端穿过所述线圈位于所述第一磁铁和第二磁铁之间,所述线圈的两根引出线穿过所述盒体延伸至所述盒体的外部。
在一些实施方式中,所述磁铁框为闭合框体,所述磁铁框的外底部与所述第二盖板连接,所述电枢和所述磁铁框构成工作磁路。
在一些实施方式中,所述第一磁铁与所述磁铁框的内顶部连接,所述第二磁铁与所述磁铁框的内底部连接。
在一些实施方式中,所述磁铁框为设有开口的u型框体,所述磁铁框的开口朝向所述第二盖板,所述磁铁框与所述第二盖板连接,所述第一磁铁与所述磁铁框的内顶部连接,所述第二磁铁与所述第二盖板连接,所述第二盖板的材质为高导磁合金,所述电枢、所述磁铁框和所述第二盖板构成工作磁路。
在一些实施方式中,所述第二盖板设有朝向所述磁铁框的凸起,所述第二磁铁与所述第二盖板的凸起连接。
在一些实施方式中,所述第二盖板包括覆盖板和折返板,所述覆盖板的端部向相反方向延伸有折返板,所述覆盖板和所述折返板平行设置,所述第二磁铁与所述折返板连接。
在一些实施方式中,所述电枢位于所述第一磁铁和所述第二磁铁之间的一端部设有连接块,所述连接杆的一端与所述连接块连接,所述连接杆的另一端与所述膜片组件连接。
其有益效果为:本发明在装配时,先在第二盖板上装配受话器的马达组件,然后放置盒体,再放置膜片组件,最后再焊接第一盖板,本发明使得第二盖板实现了带料的方式进行装配,实现了受话器装配过程的自动化,提高了装配效率。
附图说明
图1是本发明实施例一的一种受话器的结构示意图;
图2是图1的爆炸示意图;
图3是本发明实施例二的一种受话器的结构示意图;
图4是图3的爆炸示意图;
图5是本发明实施例三的一种受话器的结构示意图;
图6是图5的爆炸示意图。
具体实施方式
实施例一
图1和图2示意性地表示了本发明实施例一的受话器。如图1和图2所示,该受话器包括壳体以及位于壳体的腔体中的马达组件和膜片组件。马达组件和膜片组件通过连接杆4连接。壳体包括盒体11以及分别与盒体11连接的第一盖板12和第二盖板13。盒体11为立方体。盒体11顶部和底部为开口。由于无法通过冲压和拉伸工艺形成一个具有上开口和下开口的结构,盒体11通过折弯工艺形成。
第一盖板12覆盖盒体11顶部的开口。第二盖板13覆盖盒体11底部的开口。膜片组件包括膜片框21、膜片22和振板23。膜片框21设有内孔。膜片22与膜片框21粘贴连接并覆盖膜片框21的内孔。振板23与膜片22粘贴连接。振板23的中部设有第一凸起231。可增加振板23的劲度,提高受话器的本振频率。振板23的一边与膜片框21内孔的一边重叠,振板23的其余边与膜片框21的内孔之间设有空隙。便于振板23沿着该重叠边进行往返振动。膜片22位于振板23与膜片框21的内孔之间的部分为第二凸起221。为振板23的振动提供空间,保证振板23具有一定的振幅。振板23与膜片框21位于膜片22的两侧。使膜片22对振板23起到支撑的作用。膜片组件的外边缘与盒体11的内侧壁连接。具体地为膜片框21的外边缘与盒体11的内侧壁粘贴连接。膜片组件将壳体的空腔隔为前腔51和后腔52。膜片组件、盒体11和第一盖板12为前腔51。膜片组件、盒体11和第二盖板13为后腔52。前腔的壳体的侧壁上开设有出音口,通过出音口将声压传递出去。马达组件位于后腔52中。
马达组件包括电枢31、线圈32、磁铁框33以及位于磁铁框33内的第一磁铁34和第二磁铁35。电枢31为u型。线圈32具有通道。磁铁框33为闭合框体。第一磁铁34和第二磁铁35位于磁铁框33内。第一磁铁34与磁铁框33的内顶部连接,第二磁铁35与磁铁框33的内底部连接。第一磁铁34和第二磁铁35相对设置且不接触。磁铁框33的外底部与第二盖板13连接。第二盖板13可以以带料的形式应用于受话器的马达组件的自动装配,提高受话器的马达组件的装配效率。电枢31的一端与磁铁框33的外壁连接,电枢31的另一端穿过线圈32位于第一磁铁34和第二磁铁35之间。电枢31和磁铁框33的材质均为高导磁性合金,第一磁铁34和第二磁铁35的材质均为铝镍钴材料,电枢31、磁铁框33、第一磁铁34和第二磁铁35构成工作磁路。线圈32的两根引出线321穿过盒体11延伸至盒体11的外部。
电枢31位于第一磁铁24和第二磁铁25之间的一端部设有连接块311。连接杆4的一端与连接块311连接,连接杆4的另一端与振板23连接。
电信号通过两根引出线321输入线圈32,电枢31在输入电信号的作用下做上下往复运动,振板23在连接杆4的带动下,与电枢31做同频率的往复运动,使得前腔51的气体呈现疏密相间的体积变化,产生声压,由此,受话器完成了从电信号到声能量的转换。
实施例二
图3和图4示意性地显示了本发明实施例二的受话器。如图3和图4所示的受话器在实施例一的基础上对马达组件和第二盖板14做了改动。
马达组件包括电枢61、线圈62、磁铁框63以及位于磁铁框63内的第一磁铁64和第二磁铁65。电枢61为u型。线圈62具有通道。磁铁框63为设有开口的u型框体。第一磁铁64和第二磁铁65位于磁铁框63内。磁铁框63设有开口的一端朝向第二盖板14,并与第二盖板14连接。第二盖板14设有朝向磁铁框63的凸起141,为形成工作磁路提供一定的厚度。第一磁铁64与磁铁框63的内顶部连接,第二磁铁65与第二盖板14的凸起131连接。第一磁铁64和第二磁铁65相对设置且不接触。磁铁框63的外底部与第二盖板14连接。第二盖板13可以以带料的形式应用于受话器的马达组件的自动装配,提高受话器的马达组件的装配效率。电枢61的一端与磁铁框63的外壁连接,电枢61的另一端穿过线圈62位于第一磁铁64和第二磁铁65之间。电枢61、磁铁框63和第二盖板13的材质均为高导磁性合金,第一磁铁64和第二磁铁65的材质均为铝镍钴材料,电枢61、磁铁框63、第二盖板13、第一磁铁64和第二磁铁65构成工作磁路。线圈62的两根引出线621穿过盒体11延伸至盒体11的外部。
电信号通过两根引出线621输入线圈62,电枢61在输入电信号的作用下做上下往复运动,振板23在连接杆4的带动下,与电枢61做同频率的往复运动,使得前腔51的气体呈现疏密相间的体积变化,产生声压,由此,受话器完成了从电信号到声能量的转换。
实施例三
图5和图6示意性地显示了本发明实施例三的受话器。如图5和图6所示的受话器在实施例一的基础上对马达组件和第二盖板15做了改动。
马达组件包括电枢71、线圈72、磁铁框73以及位于磁铁框73内的第一磁铁74和第二磁铁75。电枢71为u型。线圈72具有通道。磁铁框73为设有开口的u型框体。第一磁铁74和第二磁铁75位于磁铁框73内。磁铁框73设有开口的一端朝向第二盖板15,并与第二盖板15连接。第二盖板15包括覆盖板151和折返板152。覆盖板151的端部向相反方向延伸有折返板152,为形成工作磁路提供一定的厚度。第二盖板13与折返板131为一体结构,便于制造。折返板521与第二盖板13平行设置,便于放置马达组件。第二盖板15可以以带料的形式应用于受话器的马达组件的自动装配,提高受话器的马达组件的装配效率。第一磁铁74与磁铁框73的内顶部连接,第二磁铁75与第二盖板15的折返板152连接。第一磁铁74和第二磁铁75相对设置且不接触。磁铁框73的外底部与第二盖板15连接。电枢71的一端与磁铁框73的外壁连接,电枢71的另一端穿过线圈72位于第一磁铁74和第二磁铁75之间。电枢71、磁铁框73和第二盖板15的材质均为高导磁性合金,第一磁铁74和第二磁铁75的材质均为铝镍钴材料,电枢71、磁铁框73、第二盖板15、第一磁铁74和第二磁铁75构成工作磁路。线圈72的两根引出线721穿过盒体11延伸至盒体11的外部。
电信号通过两根引出线721输入线圈72,电枢71在输入电信号的作用下做上下往复运动,振板23在连接杆4的带动下,与电枢71做同频率的往复运动,使得前腔51的气体呈现疏密相间的体积变化,产生声压,由此,受话器完成了从电信号到声能量的转换。
以上所述的仅是本发明的一些实施方式。对于本领域普通技术人员来讲,在不脱离本发明创造构思的前提下,还可以做出若干变形和改进,这些都属于本发明的保护范围。