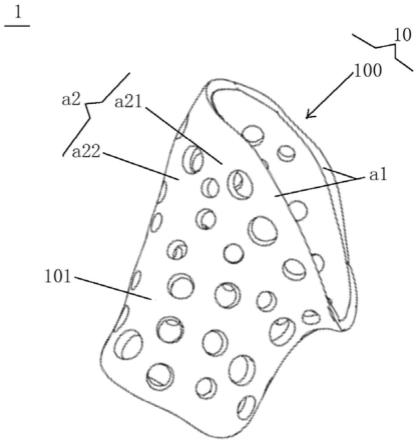
1.本发明属于电子配件领域,具体涉及一种基于高性能复合型晶格构弹性体耳机壳。
背景技术:2.众所周知,耳机包括耳机壳、扬声器、讯号处理器,其中讯号处理器与电子产品(手机、电脑、pad、收音机等)通过有线或无线连通,并通过讯号处理器将获得电讯号传递至扬声器,再通过扬声器的振动输出形成音波。也就是说,耳机是一对转换单元,它接受来自媒体播放器或接收器所发出的电讯号,利用贴近耳朵的扬声器将其转化成可以听到的音波。
3.然而,现有的耳机壳多为硬质材料,使用时间久了以后容易造成耳道不适,严重影响用户的使用体验感。
技术实现要素:4.本发明所要解决的技术问题是克服现有技术的不足,提供一种改进的基于高性能复合型晶格构弹性体耳机壳。
5.为解决上述技术问题,本发明采取如下技术方案:一种基于高性能复合型晶格构弹性体耳机壳,其包括壳本体,壳本体包括晶格点阵结构弹性体和弹性树脂层,晶格点阵结构弹性体为3d打印而成的热塑性弹性体,热塑性弹性体的孔隙率为15%~35%,且热塑性弹性体的密度为0.7-1.1g/cm3,弹性树脂层至少形成在晶格点阵结构弹性体的内部孔隙中并与晶格点阵结构弹性体之间结合。
6.优选地,弹性树脂层还形成在热塑性弹性体的表面。进一步提升壳本体的强度、弹性、抗冲击性能,而且也不会增加整体的厚度。
7.优选地,组成弹性树脂层的弹性树脂的硬度为50a邵氏硬度以上、40d邵氏硬度以下,25℃下的粘度小于12000cp,抗拉强度为5mpa以上,断裂伸长率为120%以上。
8.优选地,弹性树脂层的质量为热塑性弹性体质量的10%~30%。提升壳本体的强度、弹性、抗冲击性能,且保证弹性缓冲能力足够前提下,最佳化的减轻重量。
9.根据本发明的一个具体实施和优选方面,热塑性弹性体包括内塞部分和外塞部分,其中内塞部分塞入外耳道,外塞部分与内塞部分形成容纳腔,且外塞部分中一部分贴合耳廓,另一部分外露于耳外。这样所形成的壳本体,不仅隔音、降噪、承力、透气等功能,给予用户不一样的体验,而且大大提升了入耳的舒适度,同时还能贴合耳道,减少耳机长时间入耳对耳道的伤害。
10.优选地,外塞部分与内塞部分一体成型,且内塞部分被压缩至形变为50%时所需的压力为n1,外塞部分被压缩至形变为50%时所需的压力为n2,其中n2≥n1≥150n。这说明,内塞部分相对于外塞部分更加的柔软。
11.优选地,内塞部分的孔隙率大于外塞部分的孔隙率。这样一来,通过不同位置的接触、以及所提供不同的压缩形变,确保入耳舒适度,而且改善隔音、降噪、承力、透气等功能。
12.根据本发明的又一个具体实施和优选方面,内塞部分包括第一塞体、第二塞体,其中第一塞体能够塞入外耳道,第二塞体包括贴合在耳廓上的贴合部、与贴合部形成容纳空间的外露部。
13.优选地,第一塞体、所述贴合部、及所述外露部分别被压缩至形变为50%时所需的压力依次变大设置。
14.优选地,外塞部分自所述外露部向下延伸且下端部闭合设置,其中所述外塞部分的周向面或/和下端面上均形成有镂空的晶格点阵结构。
15.根据本发明的又一个具体实施和优选方面,壳本体采用包含所述弹性树脂或其原料、固化剂的处理液对所述晶格点阵结构弹性体进行涂覆处理形成。
16.优选地,涂覆处理采用的方法为喷涂、浸涂或电镀,涂覆处理时,使所述处理液渗透进入所述晶格点阵结构弹性体的内部孔隙之中。
17.在一些具体实施方式中,涂覆处理的时间为5-20min,加热处理的时间为3-12h。
18.进一步地,处理液中弹性树脂的质量浓度为30-60%,固化剂的质量浓度为1%-10%。在一些具体实施方式中,处理液中弹性树脂的质量浓度为40-55%,固化剂的质量浓度为2%-5%。
19.在一些具体实施方式中,所述加热固化在温度80~100℃下进行,所述涂覆处理和加热固化为一次,或者在一次结束后,再重复1~3次。
20.此外,组成热塑性弹性体的树脂为选自热塑性聚氨酯树脂、热塑性聚乙烯树脂中的一种或两种的组合。
21.在本发明的一些实施方式中,组成弹性树脂层的弹性树脂为选自聚氨酯树脂、丙烯酸树脂、有机硅树脂中的一种或多种的组合。
22.本发明人通过研究发现,将晶格点阵结构弹性体与包含弹性树脂或形成弹性树脂的原料、树脂固化剂的处理液充分接触,并加热固化,弹性树脂会在晶格点阵结构弹性体的内部孔隙中以及晶格点阵结构弹性体的外表面形成弹性树脂层,弹性树脂与晶格点阵结构弹性体固化、粘接、复合,填充晶格点阵结构弹性体的内部孔隙,进而可以获得优异力学性能的壳本体。在相同的重量下,该壳本体具有更高的抗压缩性能;在达到相同压缩性能的条件下,该材料具有更低的重量。此外,位于晶格点阵结构弹性体外表面的弹性树脂层可以降低材料的表面粗糙度,使得壳本体表面光滑。
23.晶格点阵结构弹性体通过3d打印制备。通过调节3d打印温度和激光能量等参数,可以控制晶格点阵结构弹性体的烧结密度和孔隙率,进而控制弹性树脂渗透的深度和质量。温度和激光功率越低,打印出的晶格点阵结构弹性体的孔隙率越高,壳本体中弹性树脂的含量也就越高,壳本体的抗压缩性能越好。
24.在一些具体实施方式中,采用的参数如下:温度为80-140℃,激光功率为30-100w,扫描速率为4000-15000mm/s,扫描间距为0.1-0.3mm。
25.同时,构成晶格点阵结构弹性体的点阵胞元结构没有特别限制。点阵胞元结构可以是常见的立方体,星形,八角形,六边形,菱形和四面体等。
26.由于以上技术方案的实施,本发明与现有技术相比具有如下优点:
27.本发明将弹性树脂渗入晶格点阵结构弹性体的内部孔隙中并且使二者紧密结合以形成壳本体,不仅满足自重轻、厚度薄,而且也大幅增强壳本体的强度、弹性和抗压缩性
能,也大幅度提升了入耳的舒适度,改善隔音、降噪、承力、透气等功能,此外,贴合耳道,减少耳机长时间入耳对耳道的伤害。
附图说明
28.图1为实施例1中耳机壳结构示意图;
29.图2为实施例2中耳机壳结构示意图;
30.图3为实施例3中耳机壳结构示意图;
31.图4为实施例4中耳机壳结构示意图;
32.其中:1、壳本体;10、晶格点阵结构弹性体;100、内塞部分;a1、第一塞体;a2、第二塞体;a21、贴合部;a22、外露部;101、外塞部分。
具体实施方式
33.为使本技术的上述目的、特征和优点能够更加明显易懂,下面结合附图对本技术的具体实施方式做详细的说明。在下面的描述中阐述了很多具体细节以便于充分理解本技术。但是本技术能够以很多不同于在此描述的其它方式来实施,本领域技术人员可以在不违背本技术内涵的情况下做类似改进,因此本技术不受下面公开的具体实施例的限制。
34.在本技术的描述中,需要理解的是,术语“中心”、“纵向”、“横向”、“长度”、“宽度”、“厚度”、“上”、“下”、“前”、“后”、“左”、“右”、“竖直”、“水平”、“顶”、“底”、“内”、“外”、“顺时针”、“逆时针”、“轴向”、“径向”、“周向”等指示的方位或位置关系为基于附图所示的方位或位置关系,仅是为了便于描述本技术和简化描述,而不是指示或暗示所指的装置或元件必须具有特定的方位、以特定的方位构造和操作,因此不能理解为对本技术的限制。
35.此外,术语“第一”、“第二”仅用于描述目的,而不能理解为指示或暗示相对重要性或者隐含指明所指示的技术特征的数量。由此,限定有“第一”、“第二”的特征可以明示或者隐含地包括至少一个该特征。在本技术的描述中,“多个”的含义是至少两个,例如两个,三个等,除非另有明确具体的限定。
36.在本技术中,除非另有明确的规定和限定,术语“安装”、“相连”、“连接”、“固定”等术语应做广义理解,例如,可以是固定连接,也可以是可拆卸连接,或成一体;可以是机械连接,也可以是电连接;可以是直接相连,也可以通过中间媒介间接相连,可以是两个元件内部的连通或两个元件的相互作用关系,除非另有明确的限定。对于本领域的普通技术人员而言,可以根据具体情况理解上述术语在本技术中的具体含义。
37.在本技术中,除非另有明确的规定和限定,第一特征在第二特征“上”或“下”可以是第一和第二特征直接接触,或第一和第二特征通过中间媒介间接接触。而且,第一特征在第二特征“之上”、“上方”和“上面”可是第一特征在第二特征正上方或斜上方,或仅仅表示第一特征水平高度高于第二特征。第一特征在第二特征“之下”、“下方”和“下面”可以是第一特征在第二特征正下方或斜下方,或仅仅表示第一特征水平高度小于第二特征。需要说明的是,当元件被称为“固定于”或“设置于”另一个元件,它可以直接在另一个元件上或者也可以存在居中的元件。当一个元件被认为是“连接”另一个元件,它可以是直接连接到另一个元件或者可能同时存在居中元件。本文所使用的术语“垂直的”、“水平的”、“上”、“下”、“左”、“右”以及类似的表述只是为了说明的目的,并不表示是唯一的实施方式。
38.实施例1
39.如图1所示,本实施例所涉及的基于高性能复合型晶格构弹性体耳机壳,其包括壳本体1。
40.壳本体1包括晶格点阵结构弹性体10和弹性树脂层,其中晶格点阵结构弹性体10以热塑性聚氨酯tpu为原料,通过粉末烧结成型3d打印出晶格点阵结构弹性体,其工艺参数为主温100-120℃,激光功率50w,扫描速率4000-8000mm/s,扫描间距0.2mm。
41.弹性树脂层形成在晶格点阵结构弹性体10的内部孔隙中并与晶格点阵结构弹性体10之间结合。
42.晶格点阵结构弹性体10为3d打印而成的热塑性弹性体,热塑性弹性体的孔隙率为15%~35%,且热塑性弹性体的密度为0.7-1.1g/cm3。
43.组成弹性树脂层的弹性树脂的硬度为50a邵氏硬度以上、40d邵氏硬度以下,25℃下的粘度小于12000cp,抗拉强度为5mpa以上,断裂伸长率为120%以上。
44.弹性树脂层的质量为热塑性弹性体质量的10%~30%。提升壳本体的强度、弹性、抗冲击性能,且保证弹性缓冲能力足够前提下,最佳化的减轻重量。
45.热塑性弹性体10包括内塞部分100和外塞部分101,其中内塞部分100塞入外耳道,外塞部分101与内塞部分100形成容纳腔,且外塞部分101中一部分贴合耳廓,另一部分外露于耳外。这样所形成的壳本体,不仅隔音、降噪、承力、透气等功能,给予用户不一样的体验,而且大大提升了入耳的舒适度,同时还能贴合耳道,减少耳机长时间入耳对耳道的伤害。
46.内塞部分100包括第一塞体a1、第二塞体a2,其中第一塞体a1能够塞入外耳道,第二塞体a2包括贴合在耳廓上的贴合部a21、与贴合部a21形成容纳空间的外露部a22。
47.第一塞体a1、贴合部a21、及外露部a22分别被压缩至形变为50%时所需的压力依次变大设置。
48.外塞部分101自外露部a22向下延伸且下端部闭合设置,其中外塞部分101的周向面或/和下端面上均形成有镂空的晶格点阵结构。
49.外塞部分101与内塞部分100一体成型,且内塞部分100被压缩至形变为50%时所需的压力为n1,外塞部分101被压缩至形变为50%时所需的压力为n2,其中n2≥n1≥150n。这说明,内塞部分相对于外塞部分更加的柔软。
50.内塞部分100的孔隙率大于外塞部分101的孔隙率。这样一来,通过不同位置的接触、以及所提供不同的压缩形变,确保入耳舒适度,而且改善隔音、降噪、承力、透气等功能。
51.此外,壳本体1采用包含所述弹性树脂或其原料、固化剂的处理液对所述晶格点阵结构弹性体进行涂覆处理形成。
52.涂覆处理采用的方法为喷涂、浸涂或电镀,涂覆处理时,使所述处理液渗透进入所述晶格点阵结构弹性体的内部孔隙之中。
53.同时,本例中,壳本体1包括晶格点阵结构弹性体和弹性树脂层,且成型过程包括如下步骤:
54.1)以热塑性聚氨酯tpu为原料,通过粉末烧结成型3d打印出晶格点阵结构弹性体,其工艺参数为主温100-120℃,激光功率50w,扫描速率4000-8000mm/s,扫描间距0.2mm。
55.2)将商购的质量浓度为45%的聚氨酯树脂溶液94质量份、异氰酸酯类固化剂6质量份,用高速搅拌器混合分散均匀得到浸渍处理液,其中聚氨酯树脂的硬度为60a,25℃下
的粘度为8000cp,抗拉强度为10mpa,断裂伸长率为200%。
56.3)将打印出的晶格点阵结构弹性体浸泡于步骤2)制备的浸渍处理液中8min,取出后甩干,然后放入80
±
2℃真空烘箱中固化2.5h,得到复合材料样品。
57.在不同扫描速率下得到的晶格点阵结构弹性体的烧结密度和孔隙率,以及晶格点阵结构弹性体在聚氨酯树脂处理前和处理后的重量、压缩形变50%时的压力如下表1所示:
58.表1
[0059][0060]
由上表1可知,通过控制3d打印的工艺参数,可以调整晶格点阵结构弹性体的烧结密度和孔隙率,孔隙率越大,壳本体中聚氨酯树脂的含量越多,复合弹性体材料的抗压缩性能提升越多。
[0061]
实施例2
[0062]
如图2所示,本实施例所涉及的基于高性能复合型晶格构弹性体耳机壳,其包括壳本体1,且壳本体1的结构与实施例1基本相同,不同之处在于。
[0063]
晶格点阵结构弹性体10所构成晶格点阵结构弹性体的点阵胞元结构不同。
[0064]
同时,本例中,晶格点阵结构弹性体10和弹性树脂层的成型过程包括如下步骤:
[0065]
1)以热塑性聚氨酯tpu为原料,通过粉末烧结成型3d打印出晶格点阵结构弹性体,其工艺参数为主温100-120℃,激光功率55w,扫描速率4000mm/s,扫描间距0.3mm;
[0066]
2)将商购质量浓度为约55%的丙烯酸树脂溶液98质量份、固化剂4,4'-亚甲基双(2-甲基环己基胺)2质量份,用高速搅拌器混合分散均匀得到浸渍处理液,其中,丙烯酸树脂的硬度为70a,25℃下的粘度为10000cp,抗拉强度为12mpa,断裂伸长率为180%;
[0067]
3)将打印出的tpu晶格点阵结构弹性体浸泡于浸渍处理液中10min,取出后甩干,然后放入80℃真空烘箱中固化5h,得到壳本体样品;
[0068]
4)将固化后的样品再次置于浸渍处理液中,浸泡10min、甩干、固化,所形成的壳本体1中晶格点阵结构弹性体表面形成有一层弹性树脂层。
[0069]
此时,将壳本体1的重量由处理前的0.61g增加至0.86g,材料压缩形变50%时压力由处理前的135.2n增加至215.4n。制备的壳本体的密度为0.981g/cm3。
[0070]
实施例3
[0071]
结合图3所示,本实施例所涉及的基于高性能复合型晶格构弹性体耳机壳,其包括壳本体1,且壳本体1的结构与实施例2基本相同,不同之处在于。
[0072]
晶格点阵结构弹性体10所构成晶格点阵结构弹性体的点阵胞元结构不同。
[0073]
同时,本例中,晶格点阵结构弹性体10和弹性树脂层的成型过程包括如下步骤:
[0074]
1)以热塑性聚氨酯tpu为原料,通过粉末烧结成型3d打印出晶格点阵结构弹性体,其工艺参数为主温100-120℃,激光功率80w,扫描速率4000mm/s,扫描间距0.2mm;
[0075]
2)将商购质量浓度为约55%的丙烯酸树脂溶液98质量份、固化剂4,4'-亚甲基双(2-甲基环己基胺)2质量份,用高速搅拌器混合分散均匀得到浸渍处理液,其中,丙烯酸树脂的硬度为70a,25℃下的粘度为10000cp,抗拉强度为12mpa,断裂伸长率为180%;
[0076]
3)将打印出的tpu晶格点阵结构弹性体浸泡于浸渍处理液中10min,取出后甩干,然后放入80℃真空烘箱中固化5h,得到壳本体样品;
[0077]
4)将固化后的样品重复两次置于浸渍处理液中,浸泡10min、甩干、固化,得到两层聚氨酯树脂的复合弹性体材料样品。
[0078]
此时,将壳本体1的重量由处理前的0.61g增加至0.96g,材料压缩形变50%时压力由处理前的135.2n增加至235.2n。制备的壳本体的密度为0.997g/cm3。
[0079]
实施例4
[0080]
结合图4所示,本实施例所涉及的坐垫,其结构与实施例1基本相同,不同之处,具体如下。
[0081]
晶格点阵结构弹性体10所构成晶格点阵结构弹性体的点阵胞元结构不同。
[0082]
同时,本例中,晶格点阵结构弹性体10和弹性树脂层的成型过程包括如下步骤:
[0083]
1)以热塑性聚氨酯tpu为原料,通过粉末烧结成型3d打印出晶格点阵结构弹性体,其工艺参数为主温100-120℃,激光功率50w,扫描速率4000-8000mm/s,扫描间距0.2mm。
[0084]
2)将商购的质量浓度为45%的聚氨酯树脂溶液94质量份、异氰酸酯类固化剂6质量份,用高速搅拌器混合分散均匀得到浸渍处理液,其中聚氨酯树脂的硬度为60a,25℃下的粘度为8000cp,抗拉强度为10mpa,断裂伸长率为200%。
[0085]
3)将打印出的晶格点阵结构弹性体浸泡于步骤2)制备的浸渍处理液中8min,取出后甩干,然后放入80
±
2℃真空烘箱中固化2.5h,得到复合材料样品;
[0086]
4)将固化后的样品重复三次置于浸渍处理液中,浸泡10min、甩干、固化,得到三层聚氨酯树脂的复合弹性体材料样品。
[0087]
此时,将壳本体1的重量由处理前的0.61g增加至1.11g,材料压缩形变50%时压力由处理前的135.2n增加至269.9n。制备的壳本体的密度为1.091g/cm3。
[0088]
因此,本发明具有以下优势:
[0089]
1、本技术通过晶格点阵结构弹性体与弹性树脂涂层的复合,使弹性树脂渗入晶格点阵结构弹性体的内部孔隙中并且使二者紧密结合,出乎意料地,在不影响晶格点阵结构弹性体优势性能的前提下,显著提高了材料的抗压缩性能,而同时材料的体积不变,重量仅有微小的增加。相比未复合弹性树脂涂层的晶格点阵结构弹性体,在达到相同的抗压缩性能时,本发明的壳本体的体积显著更小、重量显著更轻;在重量相同时,本技术的壳本体的抗压缩性能显著更高。
[0090]
2、本技术的壳本体的制备工艺,采用3d打印制备晶格点阵结构弹性体,并采用涂覆处理和固化工艺,一方面,通过调节3d打印温度和激光功率等参数,可以控制晶格点阵结构弹性体的烧结密度和孔隙率,进而控制弹性树脂渗透的深度和质量,最终控制壳本体压缩性能改善的程度,因此,可以灵活制备各种性能的壳本体,以满足各种应用场景下的个性化需求。另一方面,采用涂覆处理和固化工艺,晶格点阵结构弹性体与弹性树脂涂层之间结合更加充分和紧密,有助于提升壳本体的强度和使用寿命。
[0091]
3、不仅满足自重轻、厚度薄,而且也大幅增强壳本体的强度、弹性和抗压缩性能,
也大幅度提升了入耳的舒适度,改善隔音、降噪、承力、透气等功能,此外,贴合耳道,减少耳机长时间入耳对耳道的伤害。
[0092]
在本文中所披露的范围的端点和任何值都不限于该精确的范围或值,这些范围或值应当理解为包含接近这些范围或值的值。对于数值范围来说,各个范围的端点值之间、各个范围的端点值和单独的点值之间,以及单独的点值之间可以彼此组合而得到一个或多个新的数值范围,这些数值范围应被视为在本文中具体公开。