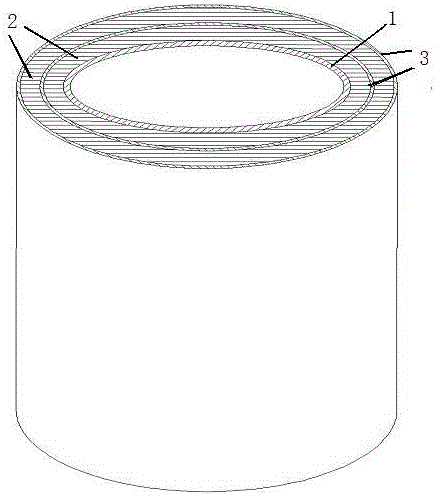
本发明属于属于碳/碳复合材料设备技术领域,具体涉及一种低密度碳/碳复合筒材的制备方法。
背景技术:碳/碳复合材料主要由碳纤维和碳基体组成,它继承了二者优异的结构和热学性能。其中,低密度碳/碳复合材料在高温下具有良好保温绝热功能,一般密度为0.10g/cm3-0.3g/cm3之间,其碳含量高、可挥发性杂质少,在真空或惰性气体保护下,可靠使用温度高达2800℃,并且长时间使用,具有各项性能指标稳定等特点,已经被广泛的应用到真空炉、单晶硅、多晶硅以及各种宝石生产行业中。目前,低密度碳/碳复合材料多采用碳毡、石墨毡等叠层复合而成,层间依靠粘接剂粘接而成。然而,低成本的高温粘接剂粘接效果很不理想,使用过程中碳毡、石墨毡之间很容易分层脱落,严重影响使用性能和寿命;一些粘接效果略好的高温粘接剂成本太高,严重制约低密度碳/碳复合材料的工业化推广。近年来,专利CN102134068A、CN102616767A等提供了几种新工艺制备的低密度泡沫碳/碳复合材料,成本较低,但是其强度很差,稍加碰撞既碎,运输和使用难度很高,不易大规模推广。因此,研究低密度碳/碳复合材料的先进制备方法,对于扩大低密度碳/碳复合材料应用领域、延长使用寿命、降低生产成本有着至关重要的作用。
技术实现要素:鉴于上述,本发明的目的在于提供一种低密度碳/碳复合筒材的制备方法。为实现上述之目的,本发明采取的技术方案为:一种低密度碳/碳复合筒材制备方法,其特征从内侧至外侧结构为:支撑层(1)、碳毡或石墨毡(2)和拉紧层(3)组成的交替缠绕层,其中碳毡或石墨毡(2)和拉紧层(3)可以重复交替缠绕,通过以下步骤实现:a.支撑层(1)采用碳纤维布、碳丝或者为两者的组合缠绕制备支撑层(1);b.涂敷高温粘接剂,然后缠绕碳毡或石墨毡(2),碳毡或石墨毡紧贴支撑层(1),用碳绳缝合接口;c.在步骤b形成碳毡或石墨毡(2)的基础上利用预浸碳丝缠绕形成拉紧层(3),缠绕预浸碳丝的张力为2-6N,缠绕厚度为0.5-3mm;d.根据需要重复步骤b-c;;e.将步骤d形成预成型体放入固化炉内,升温至180℃-230℃,固化8-12小时,随炉至60℃以下取出,固化过程中保持预成型体以25-45转/分钟低速转动;f.将步骤e固化好的预成型体放入氮气保护炭化炉中,升温至450℃-600℃,然后再降温至400℃-500℃,在400℃-500℃碳化2-4小时;g.将步骤f中得到的预成型体脱去心模,再放入氮气保护炭化炉,升温至900℃-930℃碳化2-4小时;h.将步骤g中获得的预成型体放入高温炉,升温至2000℃-2400℃,石墨化处理2-4小时;i.将步骤h中获得的预成型体机加工成所需产品。与现有技术相比,本发明具有以下优点:本发明低密度碳/碳复合筒材制备方法充分利用支撑层和拉紧层结构优势,拉紧层碳丝的缠绕张力增加了层间分层和脱落阻力,筒材整体具有一定的预紧力,增强筒材抵御外力和变形的能力;制备过程使用普通高温粘接剂,在不增加成本的前提下,有效的提高了低密度碳/碳复合筒材的使用寿命,总体提高了材料利用率。附图说明图1为本发明制备低密度碳/碳复合筒材工艺流程图。图2为本发明低密度碳/碳复合筒材结构示意图。具体实施方式为使本领域技术人员更好的理解本发明的技术方案,以下结合附图对本发明的技术方案再作进一步的描述,所举实例只用于解释本发明,并非用于限定本发明的范围。实施例1普通高温粘接剂的制备用工业乙醇溶解对甲苯磺酸,其中工业乙醇和对甲苯磺酸的重量比为100份:12份,然后搅拌20分钟,接着在搅拌下将100份酚醛树脂和6份硼酸逐渐加入,最后将石墨80份加入溶液中,继续搅拌60分钟后即制得高温粘结剂。制备低密度碳/碳复合筒材尺寸为:D=1100mm,d=990mm,L=1800mm,厚度55mm。低密度碳/碳复合筒材制备方法,其步骤是a.利用预浸碳纤维布制备支撑层1,缠绕厚度为3mm;b.在步骤a制备的支撑层1上涂刷高温粘接剂,采用12mm石墨毡在支撑层1上缠绕一层,缠绕时注意压紧,再使碳毡紧贴石墨毡,不能松动,碳毡在石墨毡上的缝用碳绳缝合接口;c.在步骤b基础上利用预浸碳丝缠绕拉紧层3,缠绕单丝张力3N,缠绕厚度0.5mm;d.在步骤c拉紧层3上,再涂刷高温粘接剂,缠绕石墨毡,石墨毡紧贴拉紧层3,拉紧层3厚度为2.3mm,形成预成型体;e.将步骤d预成型体放入固化炉内,升温至220℃固化12小时,随炉至60℃以下取出,固化过程中保持预成型体以45转/分钟低速转动;f.将步骤e固化好的预成型体放入氮气保护炭化炉中,升温至600℃,600℃,500℃低温碳化3小时;g.将步骤f中得到的预成型体脱去心模,再放入氮气保护炭化炉,升温至930℃,碳化4小时;h.将步骤g中获得的预成型体放入高温炉,升温至2400℃,石墨化处理4小时;i.将步骤h中获得的预成型体机加工成所需产品,整体密度0.23g/cm3。实施例2制备低密度碳/碳复合筒材尺寸为:D=596mm,d=460mm,L=1400mm,厚度68mm:a.利用预浸碳丝缠绕制备支撑层1,缠绕厚度为3mm;b.在步骤a制备的支撑层1上涂刷高温粘接剂,然后,在支撑层1上缠绕10mm厚碳毡二层,缠绕时碳毡紧贴支撑层1,不能松动,利用碳绳缝合接口;c.在步骤b基础上利用预浸碳丝缠绕拉紧层,缠绕碳丝张力5N,缠绕厚度1mm;d.在步骤c拉紧层3上,再涂刷高温粘接剂,缠绕碳毡,碳毡紧贴拉紧层3,拉紧层3缠绕碳丝厚度为3mm,形成预成型体;e.将步骤d预成型体放入固化炉内,升温至230℃固化12小时,随炉至60℃以下取出,固化过程中保持预成型体以40转/分钟低速转动;f.将步骤e固化好的预成型体放入氮气保护炭化炉中,升温至600℃,450℃低温碳化4小时;g.将步骤f中得到的预成型体脱去心模,再放入氮气保护炭化炉,升温至930℃碳化4小时;h.将步骤g中获得的预成型体放入高温炉,升温至2400℃,石墨化处理4小时;i.将步骤h中获得的预成型体机加工成所需产品,整体密度0.24g/cm3。实施例3制备低密度碳/碳复合筒材尺寸为:D=1423mm,d=1260mm,L=1800mm,厚度82mm:a.利用预浸碳纤维布缠绕制备支撑层,缠绕厚度为4mm;b.在步骤a支撑层1上涂刷高温粘接剂,然后,在支撑层1上缠绕14mm厚碳毡一层,缠绕时注意压紧保证碳毡紧贴支撑层1,不能松动,利用碳绳缝合接口;c.在步骤b碳毡基础上缠绕一层石墨纸,厚度1mm;d.在步骤c石墨纸基础上利用预浸碳丝缠绕拉紧层3,缠绕单丝张力5N,缠绕厚度1mm;e.在步骤d拉紧层3上,再涂刷高温粘接剂,缠绕石墨毡3层,石墨毡紧贴拉紧层3,拉紧层3缠绕碳丝厚度为2mm,形成预成型体;f.将步骤e预成型体放入固化炉内,升温至230℃固化12小时,随炉至60℃以下取出,固化过程中保持预成型体以35转/分钟低速转动;g.将步骤f固化好的预成型体放入氮气保护炭化炉中,升温至600℃,400℃低温碳化4小时;h.将步骤g中得到的预成型体脱去心模,再放入氮气保护炭化炉,升温至930℃碳化4小时;i.将步骤h中获得的预成型体放入高温炉,升温至2400℃,石墨化处理4小时;j.将步骤i中获得的预成型体机加工成所需产品,整体密度0.27g/cm3。