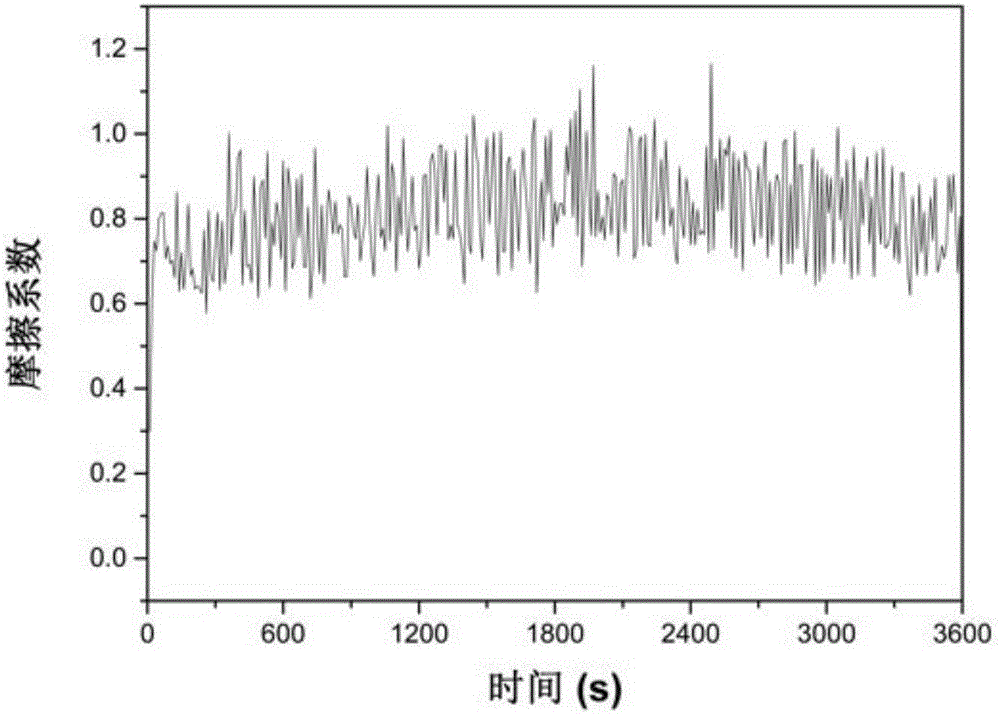
本发明涉及一种铜基复合材料及其制备方法,特别是指一种铜基复合基板、覆铜板及其制备方法。
背景技术:
随着电子器件向大功率、集成化的发展,电子电路基板的散热日趋突出。为了使得电子器件工作稳定,并且保持器件高的效率和增加寿命,因此,覆铜板的散热问题一直是企业需要解决的核心问题之一。而且,铜本身属于高塑性金属材料,很容易磨损,因此在以铜为基板的覆铜板中,提高铜基板的耐磨性也很重要,因为提高铜基板的耐磨性能够对尺寸的稳定性起决定性的作用,而且可以提高覆铜板的寿命。
目前世界各国正积极对覆铜基板进行研发,希望通过改善工艺,或者研发新的材料来提高覆铜板整体的散热效率和耐磨性。如中国专利申请号201220004672.6公开了一种高导热金属基覆铜板,通过增加粘结层的导热性,从而提高覆铜板的导热率的方法。又如中国专利申请号200620032367.2公开了一种高导热的金属基覆铜板,在金属基板上通过掺杂无极填料的树脂介质层,满足大功耗电子器件和部件安装的需要。但是前述两个专利中的粘结层或者树脂介质中的热都无法迅速传到到基板上,因为粘结层或者树脂介质与基板之间会形成热阻,在大功耗下,热阻将成为限制散热的主要因素,所以前述两个专利中提高覆铜板的导热率的方法并不理想,需要继续进行研发。
技术实现要素:
本发明的目的是提供一种导热性能好且耐磨的铜基复合基板及其制备方法。
本发明的另一目的是提供一种采用铜基复合基板制备的覆铜板及其制备方法。
本发明的技术方案是这样实现的:
一种铜基复合基板的制备方法,它以铜粉和纳米石墨烯片粉末为原料,具体包括下述步骤:
(1)按重量比874~891:0.42~4.2称取铜粉和纳米石墨烯片,然后将称取好的铜粉和纳米石墨烯片粉末进行干磨;
(2)将干磨后的混合粉末置于密封模具中,然后进行放电等离子烧结,烧结后得到铜基复合基板。
进一步的,所述铜粉的平均粒度为400~500nm,铜的含量大于99.9wt%;纳米石墨烯片粉末的平均粒度为6~8nm,片层厚度为15~25μm。
进一步的,所述步骤(1)中铜粉和纳米石墨烯片粉末是在球磨罐中以转速为300~500r/min干磨3~5h。
进一步的,所述步骤(2)的烧结过程中,压头压力为30~40MPa,模腔真空度在0.1Pa以下,烧结温度为550~750℃,升温的速率为50~100℃/min从室温加热到烧结温度,待温度到达烧结温度后保持在烧结温度进行烧结5~10min;烧结结束后,取出样坯,得到铜基复合基板。
进一步的,所述步骤(2)中的密封模具的尺寸根据所需要的基板的尺寸进行设计,该密封模具是根据产品形状的需要设计成的能够装载混合粉末并能保持密封状态的模具,所述密封模具具有可拆卸的盖板和底板,模腔内部的尺寸刚好为产品的外部三维尺寸,模具材料为石墨,模腔厚度为0.5~5mm。
本发明还提供了一种由上述铜基复合基板的制备方法制备出的铜基复合基板。
本发明还提供了一种覆铜板,该覆铜板由铜基复合基板、半固态树脂和铜箔依次叠合构成,所述铜基复合基板为上述铜基复合基板制备方法制备的铜基复合基板。
进一步的,所述半固态树脂是由重量份为40~59份的环氧树脂和聚酰胺固化剂、40~59份的氮化硼和氮化铝、1~3份硅烷偶联剂和1~3份的丙酮混匀制成,其中环氧树脂与聚酰胺固化剂的重量比为100:45,氮化硼和氮化铝的重量比为2.25:3.235~9.705。
进一步的,所述氮化硼的粒度为1~3um,氮化铝的晶须长度为80um以上,直径为1~3um。
本发明还提供了覆铜板的制备方法,制备时先将半固态树脂涂覆到铜基复合基板表面,再与铜箔叠合,然后在100~150℃下压合固化制成覆铜板;所述半固态树脂固化后形成树脂导热绝缘层。
进一步的,所述树脂导热绝缘层的厚度为0.01~0.3mm。
覆铜板的制备具体包括下述步骤:
(1)选取所需厚度和形状的铜基复合基板;
(2)制备半固态树脂,将重量份为40~59份的环氧树脂和聚酰胺固化剂,40~59份的氮化硼和氮化铝,1~3份硅烷偶联剂加入到1~3份丙酮中混合均匀,即得到半固态树脂;其中,所述环氧树脂与聚酰胺固化剂的重量比为100:45;所述氮化硼和氮化铝的重量比为2.25:3.235~9.705;
(3)制备铜箔;先将铜锭去除氧化层;然后在惰性气体环境中,温度为300~350℃下均匀化退火2~4小时,轧制成铜板;再在温度为200~250℃下退火1.5~3小时,冷轧成0.05~0.2mm的铜箔;
(4)制备覆铜板,将半固态树脂涂覆到铜基复合基板表面,再与铜箔叠合,然后在温度为100~150℃下压合固化制成覆铜板;所述半固态树脂固化后形成树脂导热绝缘层。
本发明的有益效果:
(1)本发明中的铜基复合基板具有很好的机械强度,耐磨性与纯铜相比有很大的提升;石墨烯加入铜基体中作为第二相,能起到弥散强化的作用,阻碍晶粒生长和为错的迁移,能细化晶粒,大大改善铜的力学性能,可以明显提高复合材料的硬度,在一定范围内硬度随着石墨烯含量的增加而增加(但超过临界值以后会导致强化效果的弱化);
(2)本发明中的铜基复合基板的导热系数达到了350~412W/(M·K),树脂导热绝缘层的导热系数达到6~8W/(M·K);树脂导热绝缘层的导热系数达到该数值的原因为:按重量比1:1~3添加了氮化铝和氮化硼,而且氮化铝的添加形式为晶须,这种形式能够使热传递进行的更顺利,而单纯的树脂导热绝缘层的导热系数仅为0.8~2.2W/(M·K),因此该方法获得的树脂导热绝缘层的导热系数在原来的基础上有了很大的提升;
(3)石墨烯添加到纯铜中不仅增加了铜的耐磨性和机械强度,而且增加了树脂导热绝缘层与基板的接触面积,从而使得树脂导热绝缘层中的氮化铝和氮化硼能够和基板更有效的连接,有效的降低了接触热阻;
(4)本发明中采用放点等离子烧结的方法获得基板的生产方法操作简单,效率高,材料利用率高,一次成型,能够大大降低成本,而且可以根据基板形状的不同调整模具,简单方便。
附图说明
为了更清楚地说明本发明实施例或现有技术中的技术方案,下面将对实施例或现有技术描述中所需要使用的附图作简单地介绍,显而易见地,下面描述中的附图仅仅是本发明的一些实施例,对于本领域普通技术人员来讲,在不付出创造性劳动性的前提下,还可以根据这些附图获得其他的附图。
图1为实施例1中覆铜板的摩擦系数与时间关系图;
图2为实施例2中覆铜板的摩擦系数与时间关系图;
图3为实施例3中覆铜板的摩擦系数与时间关系图;
图4为对照实施例1中覆铜板的摩擦系数与时间关系图。
具体实施方式
下面对本发明实施例中的技术方案进行清楚、完整地描述,显然,所描述的实施例仅仅是本发明一部分实施例,而不是全部的实施例。基于本发明中的实施例,本领域普通技术人员在没有作出创造性劳动前提下所获得的所有其他实施例,都属于本发明保护的范围。
一、制备实施例:
实施例1:
本实施例中所用的原料:
铜粉:平均粒度为500nm,铜的含量大于99.9wt%;
纳米石墨烯片粉末:平均粒度为6nm,片层厚度约为20μm;
氮化硼:平均粒度为2um;
氮化铝:晶须长度为80um以上,平均直径为2um;
1.1制备铜基复合基板:
(1)称取铜粉889.77Kg,纳米石墨烯片粉末0.525Kg,将称取好的铜粉和纳米石墨烯片粉末在球磨罐中以转速为400r/min干磨4h;
(2)将干磨后的混合粉末置于密封模具中,该密封模具的尺寸根据所需要的基板的尺寸进行设计,模腔厚度为3mm。然后进行放电等离子烧结,在烧结过程中,压头压力为35MPa,模腔真空度在0.1Pa以下,烧结温度为600℃,温度从室温按100℃/min的速率升温至烧结温度,待温度达到烧结温度后保持在烧结温度烧结8min;烧结结束后,取出样坯,得到铜基复合基板。
1.2制备覆铜板:
(1)选取所需厚度和形状的铜基复合基板;
(2)制备半固态树脂:将重量份为49份的环氧树脂和聚酰胺固化剂,49份的氮化硼和氮化铝,1份硅烷偶联剂加入到1份丙酮中混合均匀,即得到半固态树脂;其中,所述环氧树脂与聚酰胺固化剂的重量比为100:45;所述氮化硼和氮化铝的重量比为2.25:3.235;
(3)制备铜箔:先将铜锭去除氧化层;然后在惰性气体的环境中,温度为300℃下均匀化退火3小时,轧制成铜板;再于温度为200℃退火3小时,冷轧成0.1mm的铜箔;
(4)制备覆铜板:将半固态树脂喷涂到铜基复合基板表面,然后再与铜箔叠合,在温度为100℃下压合固化制成覆铜板;其中,半固态树脂固化后形成树脂导热绝缘层,该树脂导热绝缘层的厚度为0.2mm。
实施例2:
本实施例中所用的原料:
铜粉:平均粒度为400nm,铜的含量大于99.9wt%;
纳米石墨烯片粉末:平均粒度为8nm,片层厚度约为15μm;
氮化硼:平均粒度为1um;
氮化铝:晶须长度为80um以上,平均直径为1um;
2.1制备铜基复合基板:
(1)称取铜粉887.54Kg,纳米石墨烯片粉末1.05Kg,将称取好的铜粉和纳米石墨烯片粉末在球磨罐中以转速为400r/min干磨4h;
(2)将干磨后的混合粉末置于密封模具中,该密封模具的尺寸根据所需要的基板的尺寸进行设计,模腔厚度为5mm。然后进行放电等离子烧结,在烧结过程中,压头压力为30MPa,模腔真空度在0.1Pa以下,烧结温度为700℃,温度从室温按50℃/min的速率升温至烧结温度,待温度到达烧结温度后保持在烧结温度进行烧结10min;烧结结束后,取出样坯,得到铜基复合基板。
2.2制备覆铜板:
(1)选取所需厚度和形状的铜基复合基板;
(2)制备半固态树脂:将重量份为40份的环氧树脂和聚酰胺固化剂,59份的氮化硼和氮化铝,1份硅烷偶联剂加入到3份丙酮中混合均匀,即得到半固态树脂;其中,所述环氧树脂与聚酰胺固化剂的重量比为100:45;所述氮化硼和氮化铝的重量比为2.25:6.47;
(3)制备铜箔:先将铜锭去除氧化层,然后在惰性气体环境中,温度为350℃下均匀化退火4小时,轧制成铜板;再于250℃退火1.5小时,冷轧成0.05mm的铜箔;
(4)制备覆铜板:将半固态树脂刷涂到铜基复合基板表面,然后再与铜箔叠合,在温度为150℃下压合固化制成覆铜板,其中,半固态树脂固化后形成树脂导热绝缘层,该树脂导热绝缘层的厚度为0.3mm。
实施例3:
本实施例中所用的原料:
铜粉:平均粒度为500nm,铜的含量大于99.9wt%;
纳米石墨烯片粉末:平均粒度为6nm,片层厚度约为25μm;
氮化硼:平均粒度为3um;
氮化铝:晶须长度为80um以上,平均直径为3um;
3.1制备铜基复合基板:
(1)称取铜粉878.62Kg,纳米石墨烯片粉末2.52Kg,将称取好的铜粉和纳米石墨烯片粉末在球磨罐中以转速为500r/min干磨3h;
(2)将干磨后的混合粉末置于密封模具中,该密封模具的尺寸根据所需要的基板的尺寸进行设计,模腔厚度为0.5mm。然后进行放电等离子烧结,在烧结过程中,压头压力为40MPa,模腔真空度在0.1Pa以下,烧结温度为550℃,温度从室温按80℃/min的速率升温至烧结温度,待温度到达烧结温度后保持在烧结温度进行烧结5min;烧结结束后,取出样坯,得到铜基复合基板。
3.2制备覆铜板:
(1)选取所需厚度和形状的铜基复合基板;
(2)制备半固态树脂:将重量份为48份的环氧树脂和聚酰胺固化剂,48份的氮化硼和氮化铝,2份硅烷偶联剂加入到2份丙酮中混合均匀,即得到半固态树脂;其中,所述环氧树脂与聚酰胺固化剂的重量比为100:45;所述氮化硼和氮化铝的重量比为2.25:9.705;
(3)制备铜箔:先将铜锭去除氧化层;然后在惰性气体的环境中,在温度为320℃下均匀化退火2小时,轧制成铜板;再在温度为220℃下退火1.5小时,冷轧成0.2mm的铜箔;
(4)制备覆铜板:将半固态树脂刮涂到铜基复合基板表面,然后再与铜箔叠合,在温度为120℃下压合固化制成覆铜板,其中,半固态树脂固化后形成树脂导热绝缘层,该树脂导热绝缘层的厚度为0.01mm。
对照实施例1:
制备铜基复合基板所用的原料只有铜粉,没有纳米石墨烯片粉末,其余同实施例1。
二、实验例:
1、上述实施例1~3以及对照实施例1中所得的铜基复合基板的导热系数、树脂导热绝缘层的导热系数、击穿电压如下表1所示,并同时将现有技术中的一些基板和绝缘层的导热系数列出同本发明实施例中所得铜基复合基板和树脂导热绝缘层的导热系数做出对比:
表1
由上表1中可以看出本发明实施例1~3中所得的铜基复合基板均具有优异的导热性能,优于现有技术中的金属陶瓷复合基板和镁基合金基板的导热性能,且其树脂导热绝缘层的导热性能也优于现有技术中常常作为绝缘层的高导热少胶粉云母带、氮化硅填充的聚乙烯和氧化铝复合材料的导热性能。
2、将上述实施例1~3以及对照实施例1中所得的覆铜板进行耐摩擦测试,测试结果如图1~图4所示,从图1~图4中可以看出本发明实施例1~3中的覆铜板的耐磨性明显优于对照实施例1中所得的覆铜板。