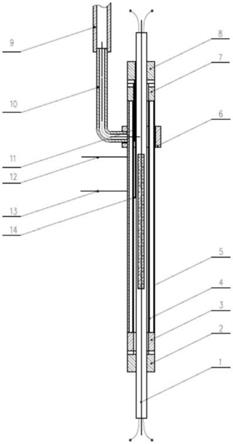
1.本实用新型属于核燃料组件试验装置技术领域,具体涉及一种内外同时加热的环形燃料包壳试验件。
背景技术:2.核电站反应堆运行过程中,核燃料的性能是影响反应堆安全性和经济性的重要因素。因此国际上一直将燃料元件的研究放在十分突出的地位,通过优化燃料元件设计、采用先进结构材料、改进元件制造工艺等方法,不断提高核燃料元件的各种性能,促使核电向更安全和更经济的方向发展。
3.全性和经济性是核电发展的基础,几乎所有的核电技术发展都以增加核电安全性和经济性为目标。燃料元件作为核电厂反应堆核心部件,其性能是核电安全性和经济性最主要影响因素之一,因此国际上一直将燃料元件的研究放在十分突出的地位,通过优化燃料元件设计、采用先进结构材料、改进元件制造工艺等方法,不断提高核燃料元件的各种性能,促使核电向更安全和更经济的方向发展。
4.目前压水堆核电厂普遍采用棒状燃料,可通过加深组件卸料燃耗、延长换料周期,降低电厂运营成本,提高核电经济性。压水堆燃料组件的平均设计燃耗从早期的10~15gwd/tu逐步提高,至今已达到60~70gwd/tu,换料周期也相应地从12个月延长至现在的18或24个月。燃料组件燃耗加深也带来诸如裂变气体释放量增大、包壳腐蚀和吸氢增加、燃料芯块肿胀、燃料元件和组件辐照生长加剧等一系列问题。如何解决这些问题,一直是国际压水堆燃料元件研究的重要任务,例如,研发抗腐蚀性能好的先进包壳,采用低裂变气体释放率的芯块。此外,通过改进定位格架设计,增加组件临界热流密度等途径,也提升了反应堆堆芯的整体安全性。总的来说,棒状燃料组件结构和参数是近50年发展不断优化的结果,以棒状燃料为基础的技术改进对于提升核电经济性和安全性的潜力已非常有限,因此,近些年来,采用其他几何结构的燃料元件成为一种新的发展思路。
5.对于新型几何结构的燃料元件至少满足以下五个基本要求:1)能提高燃料的“表面积/体积”比;2)能减小芯块厚度;3)有足够的刚度;4)能降低堆芯压降;5)组件要有开式栅格设计。美国麻省理工学院最早提出的轻水堆用环形燃料元件的概念,很好地满足了上述5个要求。所谓环形燃料是将燃料芯块制成环状,在芯块内、外表面加装包壳管,使得冷却剂可以从内、外两个流道同时对元件进行冷却与传统的实心圆柱状燃料相比,环形燃料的好处是在很高的线性密度下,燃料中心的温度仍然很低,燃料内的储能较少,裂变气体释放较少。可预期正常运行和瞬态条件下燃料性能较好。
6.环形燃料作为一种结构上完全革新的先进燃料元件,可大幅度提高燃料元件的传热效率,降低燃料芯块温度,能显著提升反应堆的安全性和经济性,已成为压水堆先进燃料组件的重要发展趋势之一,受到国际上业界的重点关注。美、韩等国相继进行了环形燃料的研发,研究表明环形燃料具有很好的应用前景。
7.环形燃料组件设计过程中,亟需开展爆破试验性能测试研究,目前有没有类似的
技术,新的结构也面临着新的问题,首先,外包壳这种大直径的薄壁包壳在核电站从未有过使用经验,因此对于外包壳的外压失稳问题,需要重新计算;其次,根据以往压水堆的运行经验,即使在相同组件中,不同的燃料棒也会有不同的轴向生长。所以,可以推断,双包壳的环形燃料,也可能发生的不同的轴向生长。
技术实现要素:8.本实用新型的目的在于研制设计一种内外同时加热的环形燃料包壳试验件,解决环形燃料内外包壳整体堆外性能实验研究的问题。
9.本实用新型的技术方案如下所述:
10.一种内外同时加热的环形燃料包壳试验件,包括电加热芯体组件、内外包壳组合试验件、进气接管组件和定位组件;
11.一、电加热芯体组件
12.电加热丝芯体组件整体是棒状结构,其中有效发热段位于整个电加热芯体的中部位置;
13.电加热丝芯体组件中包括两根电加热丝;两根电加热丝的电加热功率可以分别控制;
14.二、内外包壳组合试验件包括内包壳、外包壳、上端塞、下端塞和四个热电偶;
15.内包壳和外包壳都是管状结构;
16.内包壳和外包壳同轴套设,组成套管结构;
17.在外包壳上端开设圆孔;
18.分别在内包壳和外包壳上端和下端设置上端塞和下端塞,通过上端塞和下端塞将内包壳和外包壳之间的环状套管空间封闭;
19.上端塞和下端塞的结构相同,外径与外包壳外径一致,内径与内包壳内径一致;
20.分别在上端塞和下端塞中设置上定位凸起、下定位凸起;
21.在内包壳长度中心位置的内壁处设置内包壳中部热电偶;
22.在内包壳长度上部位置的内壁处设置内包壳上部热电偶;
23.在外包壳长度中心位置的外壁处设置外包壳中部热电偶;
24.在外包壳长度上部位置的外壁处设置外包壳上部热电偶;
25.三、进气接管组件包括气回路连接管、试验件连接管和方形进气连接块;
26.气回路连接管的一端与外部供气系统连接,另一端与试验件连接管连接;
27.外部供气系统为进气接管组件提供气体,气体的种类为氦气、氮气中的一种;
28.试验件连接管的外径与气回路连接管的内径相配合并焊接固定;
29.试验件连接管通过方形进气连接块与外包壳连接;
30.方形进气连接块为长方体结构,中间开有圆形孔道作为进气口,侧面开有圆形孔,试验件连接管插入该侧面圆孔内并焊接连接;
31.试验件连接管插入方形进气连接块侧面圆孔后,进气口与外包壳上端开设的圆孔相连,通过进气口向内外包壳组合试验件内部进气充压;
32.四、定位组件包括上定位块和下定位块;
33.上定位块和下定位块的结构相同,外径与外包壳外径一致,内径与电加热芯体组
件内径一致;
34.在上定位块的一侧断面中心位置开有上定位凹槽,在下定位块的一侧断面中心位置开有下定位凹槽;
35.上定位凹槽与上端塞中设置的上定位凸起相互配合、下定位凹槽与下端塞中设置的下定位凸起相互配合。
36.进一步的,如上所述的一种内外同时加热的环形燃料包壳试验件,电加热丝芯体组件整体是一个长度为800-1000mm、直径为6mm的棒状结构,其中有效发热段的长度为600mm。
37.进一步的,如上所述的一种内外同时加热的环形燃料包壳试验件,电加热丝芯体组件中,两根电加热丝规格一致,材料采用镍镉电热合金,材料牌号为cr20ni80、cr15ni60、gh140、cr20ni35之一;电加热丝的最高使用温度为1100℃-1200℃,加热功率最高为10kw/m。
38.进一步的,如上所述的一种内外同时加热的环形燃料包壳试验件,内包壳是长度为650mm,内径为8.2mm,厚度为0.57mm的管状结构;外包壳是长度为650mm,外径为15.7mm,厚度为0.74mm的管状结构;在外包壳上端距离顶端30-50mm位置处,开设直径为1-2mm的圆孔。
39.进一步的,如上所述的一种内外同时加热的环形燃料包壳试验件,上端塞通过焊接方式封闭内包壳和外包壳的上端,焊缝的承压能力为10-15mpa;下端塞通过焊接方式封闭内包壳和外包壳的下端,焊缝的承压能力为10-15mpa。
40.进一步的,如上所述的一种内外同时加热的环形燃料包壳试验件,在内包壳长度上部距内包壳顶端200mm位置的内壁处设置内包壳上部热电偶;在外包壳长度上部距外包壳顶端200mm位置的内壁处设置外包壳上部热电偶;热电偶通过点焊的方式固定,焊点直径不超过热电偶直径的2倍。
41.进一步的,如上所述的一种内外同时加热的环形燃料包壳试验件,气回路连接管的外径为10mm,厚度为2mm,材料为s30408不锈钢;方形进气连接块为长方体结构,长度为21.5mm,宽度为21.5mm,高度为12mm,中间开有15.48mm的圆形孔道,侧面开有直径为6.2mm的圆形孔;直径为6mm的试验件连接管插入该侧面圆孔内3mm并焊接连接。
42.进一步的,如上所述的一种内外同时加热的环形燃料包壳试验件,上定位块和下定位块的长度均为10mm;上定位凹槽和下定位凹槽的宽度均为2mm。
43.进一步的,如上所述的一种内外同时加热的环形燃料包壳试验件,该内外同时加热的环形燃料包壳试验件应用于压水堆、沸水堆、重水堆、快堆、动力堆、船用动力堆中的一种。
44.本实用新型技术方案的有益效果是:
45.1.通过每根电加热丝的电加热功率可以分别控制的环形电加热芯体组件可对内包壳进行可控加热;并且线功率密度大,可以满足试验要求,并可达较高升温速率。
46.2.通过上述结构的设置及其中各部件的连接,可以在环形燃料棒内包壳周向可形成较大温差,以更好的模拟试验所需要的温度环境,并完全模拟材料自外向内的传热工况。
47.3.通过上述结构的设置及其中各部件的连接,可以达到环形燃料棒内包壳各种试验时对内部承压的要求;并且其中的气腔容积可调,可以更好的模拟各种试验环境。
附图说明
48.图1是本实用新型一种内外同时加热的环形燃料包壳试验件结构示意图;
49.图2是电加热芯体组件结构示意图;
50.图3是上端塞结构示意图(下端塞结构与其一致);
51.图4是上定位块结构示意图(下定位块结构与其一致);
52.图5是内包壳、外包壳结构示意图;
53.图6是方形进气连接块结构示意图;
54.图7是试验件连接管结构示意图;
55.图8是气路连接管结构示意图。
56.图中:1:电加热芯体组件;2:下端塞;3:下定位块;4:内包壳;5:外包壳;6:方形进气连接块;7:上端塞;8:上定位块;9:气路连接管;10:试验件连接管;11:内包壳上部热电偶;12:外包壳上部热电偶;13:外包壳中间热电偶;14:内包壳中间热电偶。
具体实施方式
57.下面结合附图和实施例对本实用新型进行进一步描述。
58.如图1所示,本实用新型一种内外同时加热的环形燃料包壳试验件,包括电加热芯体组件、内外包壳组合试验件、进气接管组件和定位组件;
59.一、电加热芯体组件
60.如图2所示,电加热丝芯体组件整体是一个长度为800-1000mm、直径为6mm的棒状结构,其中有效发热段位于整个电加热芯体的中部位置,长度为600mm;
61.电加热丝芯体组件中包括两根电加热丝;两根电加热丝的电加热功率可以分别控制;
62.电加热丝芯体组件中,两根电加热丝规格一致,材料采用镍镉电热合金,材料牌号为cr20ni80、cr15ni60、gh140、cr20ni35之一;电加热丝的最高使用温度为1100℃-1200℃,加热功率最高为10kw/m。
63.二、内外包壳组合试验件包括内包壳、外包壳、上端塞、下端塞和四个热电偶;
64.如图5所示,内包壳是长度为650mm,内径为8.2mm,厚度为0.57mm的管状结构;
65.外包壳是长度为650mm,外径为15.7mm,厚度为0.74mm的管状结构;
66.在外包壳上端距离顶端30-50mm位置处,开设直径为1-2mm的圆孔。
67.分别在内包壳和外包壳上端和下端设置上端塞和下端塞,通过上端塞和下端塞将内包壳和外包壳之间的环状套管空间封闭;
68.如图3所示,上端塞和下端塞的结构相同,外径与外包壳外径一致,内径与内包壳内径一致;
69.分别在上端塞和下端塞中设置上定位凸起、下定位凸起;
70.在内包壳长度中心位置的内壁处设置内包壳中部热电偶;
71.在内包壳长度上部距内包壳顶端200mm位置的内壁处设置内包壳上部热电偶;
72.在外包壳长度中心位置的外壁处设置外包壳中部热电偶;
73.在外包壳长度上部距外包壳顶端200mm位置的内壁处设置外包壳上部热电偶;
74.热电偶通过点焊的方式固定,焊点直径不超过热电偶直径的2倍。
75.上端塞通过焊接方式封闭内包壳和外包壳的上端,焊缝的承压能力为10-15mpa;
76.下端塞通过焊接方式封闭内包壳和外包壳的下端,焊缝的承压能力为10-15mpa。
77.三、进气接管组件包括气回路连接管、试验件连接管和方形进气连接块;
78.如图8所示,气回路连接管的外径为10mm,厚度为2mm,材料为s30408不锈钢;
79.气回路连接管的一端与外部供气系统连接,另一端与试验件连接管连接;
80.外部供气系统为进气接管组件提供气体,气体的种类为氦气、氮气中的一种;
81.如图7所示,试验件连接管的外径与气回路连接管的内径相配合并焊接固定;
82.试验件连接管通过方形进气连接块与外包壳连接;
83.如图6所示,方形进气连接块为长方体结构,长度为21.5mm,宽度为21.5mm,高度为12mm,中间开有15.48mm的圆形孔道,侧面开有直径为6.2mm的圆形孔;直径为6mm的试验件连接管插入该侧面圆孔内3mm并焊接连接。
84.试验件连接管插入方形进气连接块侧面圆孔后,进气口与外包壳上端开设的圆孔相连,通过进气口向内外包壳组合试验件内部进气充压;
85.四、定位组件包括上定位块和下定位块;
86.如图4所示,上定位块和下定位块的结构相同,外径与外包壳外径一致,内径与电加热芯体组件内径一致;
87.上定位块和下定位块的长度均为10mm;
88.上定位凹槽和下定位凹槽的宽度均为2mm;
89.上定位凹槽与上端塞中设置的上定位凸起相互配合、下定位凹槽与下端塞中设置的下定位凸起相互配合。
90.组装时先将下定位凹槽位置朝上,将下定位块与电加热芯体组件中下端塞的下定位凸起焊接连接,从而将包壳组合试验件在下部径向定位;
91.再将上定位凹槽朝下与试验件组装,然后将上定位块与电加热芯体组件中上端塞的上定位凸起焊接连接,从而将包壳组合试验件在上部固定定位。
92.该内外同时加热的环形燃料包壳试验件应用于压水堆、沸水堆、重水堆、快堆、动力堆、船用动力堆中的一种。
93.上面结合实施例对本实用新型的实施方法作了详细说明,但是本实用新型并不限于上述实施例,在本领域普通技术人员所具备的知识范围内,还可以在不脱离本实用新型宗旨的前提下作出各种变化。本实用新型说明书中未作详细描述的内容均可以采用现有技术。