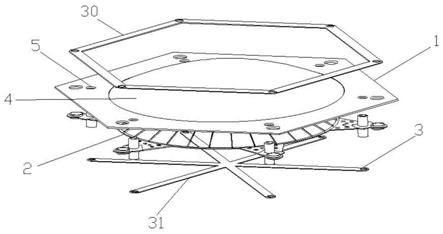
1.本发明涉及汽车车身复合板技术领域,具体是涉及一种轻量化汽车车身复合加强板及其制备方法。
背景技术:2.相对于其他新型材料,碳纤维复合材料车身的减重效果最显著;与传统钢材车身相比,采用碳纤维复合材料的车身可减重一半以上。碳纤维复合材料不仅具有质轻高强的优势、同时具有良好的可设计性。而且,复合材料可以一体化成型,大幅减少了零部件和紧固件数量;此外,碳纤维复合材料应用于汽车车身,能够提高碰撞吸能性、减振性和抗疲劳性。减重的同时,保证车辆碰撞安全性并提升乘坐舒适性。
3.目前,碳纤维复合材料应用于车身及零部件在国外已有量产案例。宝马i8及7系已应用碳纤维于车身。在宝马7系的乘员舱区域,车身由钢部件、铝合金部件和碳纤维部件组合构成,实现了不同材料间性能上的协同互补。其中,碳纤维复合材料作为车身结构加强件,在减轻车身重量的同时提高了整车碰撞安全性。
4.现有技术提供的碳纤维复合材料板件通常采用单一碳纤维材料制成,由于碳纤维属于各向异性材料,因此力学性能不均衡,应用于车辆这种工况较复杂的机械结构上存在一定的技术缺陷,尤其是现有碳纤维复合板件正面抗冲击能力及其弱,要用于车门、车头等常规撞击区存在较大的技术壁垒。
技术实现要素:5.本发明解决的技术问题是:解决现有技术碳纤维复合板力学性能不均衡,正面抗冲击能力弱的问题。
6.本发明的技术方案是:一种轻量化汽车车身复合加强板,包括能够安装在汽车车架上的复合主体壳板,设置在所述复合主体壳板内部的预埋加强结构,以及设置在所述复合主体壳板外部与预埋加强结构连接的外部加强结构;
7.所述复合主体壳板包括外形为弧面壳状的第一主体,以及围设在所述第一主体外围作为翻边结构的第二主体;
8.所述第一主体、第二主体均包括若干层碳纤维布、若干层玻璃纤维布混合铺设组成的基本层,设置在所述基本层上表面由若干层碳纤维、玻璃纤维制成的混合编织布铺设的第一增强层,设置在所述基本层下表面由若干层碳纤维、玻璃纤维混合编织布铺设组成的第二增强层;
9.所述预埋加强结构包括设置在第二主体的基本层内的第一预埋金属环,设置在第一主体的基本层内的第二预埋金属环,一端连接第一预埋金属环、另一端连接第二预埋金属环且位于基本层内的弧状金属条,以及设置在第二主体的基本层内的连接件;
10.所述弧状金属条为多个采用弹簧钢制成的金属条,并且以第一预埋金属环中心均匀分布;
11.所述外部加强结构包括设置在第一增强层上端面且与连接件栓接的外围翻边加固环,以及多个交叉设置在第二增强层下端面与连接件栓接的内部支撑杆。
12.进一步地,所述连接件包括多个以第一预埋金属环中心均匀分布且与第一预埋金属环固定的预埋固定片,设置在所述预埋固定片上与外围翻边加固环、内部支撑杆的第一连接孔,以及设置在所述预埋固定片上与汽车车架连接的第二连接孔。通过预埋固定片、第一连接孔以及第二连接孔的设置能够将复合加强板承受的大部分负载从第一预埋金属环、预埋固定片传递到车架上,能够大大减小在车辆撞击中致使车身复合加强板承受的载荷,有利于车辆安全性能的提升。
13.进一步地,所述第一预埋金属环为钢制圆环。通过弧状金属条将大部分冲击载荷直接传递给第一预埋金属环,通过钢制圆环设计能够保证吸收载荷的均匀性,防止第一预埋金属环内部产生内应力,造成扭曲;因此能够大大提高复合加强板的正面抗冲击能力。
14.进一步地,所述外围翻边加固环、内部支撑杆均采用铝合金材质;并且外围翻边加固环与第一增强层外边沿贴合。通过铝制外围翻边加固环、内部支撑杆的设置能够二次提升复合加强板的力学性能,能够结合内部预埋加强结构对复合加强板实现二次保护,在一定程度上提高复合加强板的使用寿命。
15.一种轻量化汽车车身复合加强板的制备方法,包括以下步骤:
16.步骤一:制造预埋加强结构
17.首先机加工制造第一预埋金属环、预埋固定片、第二预埋金属环以及弧状金属条;然后将弧状金属条两端分别与第一预埋金属环、第二预埋金属环焊接固定;预埋固定片与第一预埋金属环由一整块厚度为0.6~1.4mm的钢板经过慢走丝切割得到;
18.其中,根据复合加强板整体面积确定第一预埋金属环的大小及形状;
19.步骤二:制造混合编织布以及准备模具
20.准备碳纤维丝束、玻璃纤维丝束;将准备好的碳纤维丝束、玻璃纤维丝束按照比例3~5:1排列设置作为编织纬线;并且编织纬线中的玻璃纤维丝束间隔均匀;将准备好的碳纤维丝束经向排列作为编织经线;将编织纬线、编织经线上下交错编织得到混合编织布;
21.准备rtm工艺模具;
22.步骤三:铺设复合加强板
23.首先对混合编织布、碳纤维布以及玻璃纤维布进行裁剪,将裁剪好的材料放入复合环氧树脂中在130℃条件下浸泡20~30min;
24.然后,在准备好的rtm工艺模具上均匀涂抹脱模剂,再将浸泡好的混合编织布取出在rtm工艺模具上铺设第二增强层;在第二增强层上放置预埋加强结构,再将浸泡好的碳纤维布、玻璃纤维布取出继续铺设形成基本层;然后,再将浸泡好的混合编织布取出铺设在基本层的上表面形成第一增强层;
25.最后,rtm工艺模具合模,加热至130~160℃,同时抽负压至5~20kpa,保持5~8h,降温后得到复合加强板。
26.进一步地,步骤三铺设的基本层包括8层从下至上依次铺设的碳纤维布,2层夹设在碳纤维布中的玻璃纤维布;
27.其中,8层碳纤维布按照碳纤维丝编排方向铺设角度依次为120
°
、+60
°
、90
°
、0
°
、0
°
、90
°
、
‑
60
°
、120
°
;第一层玻璃纤维布夹设在+60
°
与90
°
之间,第二层玻璃纤维布夹设在
90
°
与
‑
60
°
之间。
28.在90
°
、0
°
垂直设计的基础上通过120
°
、+60
°
、
‑
60
°
、120
°
的设置能够大大提高基本层的抗剪切能力;由于碳纤维材质属于各向异性材质,通过大角度的交叉设计能够弥补复合加强板在侧向上的力学性能,使复合加强板板件成型后在各个方向上能够承受载荷的能力相对均衡。
29.进一步地,步骤二所述编织经线为12k碳纤维丝束;所述编织纬线为1200tex玻璃纤维丝束,以及与1200tex玻璃纤维丝束比例为3:1的12k碳纤维丝束。相比小丝束碳纤维原丝来说,24k以上的大丝束碳纤维原丝在制作板材等结构时,丝束不宜展开,导致单层厚度增加,不利于结构设计;并且小丝束的碳纤维不容易粘连、断丝少,对制造的复合板件强度影响小。
30.进一步地,步骤三所述第一增强层包括8层碳纤维、玻璃纤维组成的混合编织布;其中,8层混合编织布按照碳纤维丝编排方向从下至上铺设角度依次为+45
°
、
‑
45
°
、90
°
、0
°
、90
°
、0
°
、
‑
45
°
、+45
°
;
31.所述第二增强层与第一增强层层数相同且关于基本层中心对称铺设。
32.因为碳纤维存在热膨胀现象,均衡对称的铺层设计可以有效避免耦合,从而防止层合板发生翘曲变形;并且
±
45
°
铺层靠近复合板表面铺设,可以提高复合板的屈服强度;最外层
±
45
°
铺层方向还具有承受剪切载荷的能力,同时提高材料的抗冲击性能。
33.进一步地,步骤三铺设时第一增强层与第二增强层混合编织布的边缘处逐层向内收缩,使边缘呈三角形;其中,第一增强层厚度与三角形高的比值不大于1:10。通过三角形实现复合加强板边缘的过渡设计能够防止边缘产生裂纹,导致复合加强板存在安全隐患,有效改善复合加强板边缘的成型质量,提高使用寿命。
34.进一步地,所述复合环氧树脂由28份双酚a型环氧树脂、15份高温韧性环氧树脂以及8份氨基四官能团环氧树脂在90℃条件下混合搅拌20~30min得到。通过复合改性后的环氧树脂粘度大大增加,并且能够扩展树脂体系高温粘度区间延长,可有效改善固化树脂的力学性能,增强复合加强板的拉伸强度和冲击强度。
35.本发明的有益效果是:本发明提供的轻量化汽车车身复合加强板,将碳纤维、玻璃纤维等复合材料与金属材质结合,将金属材质制成与车架直接连接的金属骨架预埋在复合材料中心,能够大大提高复合加强板改善复合加强板的力学性能;相对与传统复合碳纤维板,能够大大改善复合加强板的正面抗冲击能力,能够大幅提高车辆车身承受冲击载荷的能力;当正面撞击突破复合加强板承担载荷的能力时,由于金属预埋结构的设计导致复合加强板发生溃缩,吸收大部分冲击,且复合材料破裂后碎片少,穿透能力弱;因此能够在很大程度上提升车辆的安全性能。
36.本发明提供的轻量化汽车车身复合加强板的制备方法,通过对碳纤维布、玻璃纤维布铺层的设计以及对碳纤维丝束、玻璃纤维丝束混合编织布的设计能够在一定程度改善纯碳纤维布的机械强度,提高复合加强板的抗冲击能力,改善成型复合加强板的耐热性、耐腐蚀性。
附图说明
37.图1是本发明实施例1整体的结构示意图;
38.图2是本发明实施例1复合主体壳板剖面的示意图;
39.图3是本发明实施例1预埋加强结构的结构示意图;
40.其中,1
‑
复合主体壳板、10
‑
基本层、11
‑
第一增强层、12
‑
第二增强层、2
‑
预埋加强结构、20
‑
第一预埋金属环、21
‑
第二预埋金属环、22
‑
弧状金属条、23
‑
连接件、230
‑
预埋固定片、231
‑
第一连接孔、232
‑
第二连接孔、3
‑
外部加强结构、30
‑
外围翻边加固环、31
‑
内部支撑杆、4
‑
第一主体、5
‑
第二主体。
具体实施方式
41.实施例1:
42.如图1所示的一种轻量化汽车车身复合加强板,包括能够安装在汽车车架上的复合主体壳板1,设置在复合主体壳板1内部的预埋加强结构2,以及设置在复合主体壳板1外部与预埋加强结构2连接的外部加强结构3;
43.复合主体壳板1包括外形为弧面壳状的第一主体4,以及围设在第一主体4外围作为翻边结构的第二主体5;
44.第一主体4、第二主体5均包括8层碳纤维布、2层玻璃纤维布混合铺设组成的基本层10,设置在基本层10上表面由若干层碳纤维、玻璃纤维制成的混合编织布铺设的第一增强层11,设置在基本层10下表面由若干层碳纤维、玻璃纤维混合编织布铺设组成的第二增强层12;
45.预埋加强结构2包括设置在第二主体5的基本层10内的第一预埋金属环20,设置在第一主体4的基本层10内的第二预埋金属环21,一端连接第一预埋金属环20、另一端连接第二预埋金属环21且位于基本层10内的弧状金属条22,以及设置在第二主体5的基本层10内的连接件23;
46.弧状金属条22为36个采用弹簧钢制成的金属条,并且以第一预埋金属环20中心均匀分布;
47.外部加强结构3包括设置在第一增强层11上端面且与连接件23栓接的外围翻边加固环30,以及3个交叉设置在第二增强层12下端面与连接件23栓接的内部支撑杆31。
48.连接件23包括6个以第一预埋金属环20中心均匀分布且与第一预埋金属环20固定的预埋固定片230,设置在预埋固定片230上与外围翻边加固环30、内部支撑杆31的第一连接孔231,以及设置在预埋固定片230上与汽车车架连接的第二连接孔232。
49.第一预埋金属环20为钢制圆环,厚度为0.6mm。
50.外围翻边加固环30、内部支撑杆31均采用铝合金材质;并且外围翻边加固环30与第一增强层11外边沿贴合。
51.其中,复合加强板通过第二连接孔232与外部汽车车架螺栓连接。
52.实施例2:
53.本实施例是针对实施例1的轻量化汽车车身复合加强板的制备方法进行阐述,包括以下步骤:
54.步骤一:制造预埋加强结构
55.首先机加工制造第一预埋金属环20、预埋固定片230、第二预埋金属环21以及弧状金属条22;然后将弧状金属条22两端分别与第一预埋金属环20、第二预埋金属环21焊接固
定;预埋固定片230与第一预埋金属环20由一整块厚度为0.6mm的钢板经过慢走丝切割得到;
56.其中,第一预埋金属环20为直径63cm的钢制圆环;
57.步骤二:制造混合编织布以及准备模具
58.准备12k碳纤维丝束、1200tex玻璃纤维丝束;将准备好的碳纤维丝束、玻璃纤维丝束按照比例3:1排列设置作为编织纬线;并且编织纬线中的玻璃纤维丝束间隔均匀;将准备好的碳纤维丝束经向排列作为编织经线;将编织纬线、编织经线上下交错编织得到混合编织布;
59.准备rtm工艺模具;
60.步骤三:铺设复合加强板
61.首先对混合编织布、碳纤维布以及玻璃纤维布进行裁剪,将裁剪好的材料放入复合环氧树脂中在130℃条件下浸泡20min;复合环氧树脂由28份双酚a型环氧树脂、15份高温韧性环氧树脂以及8份氨基四官能团环氧树脂在90℃条件下混合搅拌20min得到;
62.然后,在准备好的rtm工艺模具上均匀涂抹脱模剂,再将浸泡好的混合编织布取出在rtm工艺模具上铺设第二增强层12;在第二增强层12上放置预埋加强结构2,再将浸泡好的碳纤维布、玻璃纤维布取出继续铺设形成基本层10;然后,再将浸泡好的混合编织布取出铺设在基本层10的上表面形成第一增强层11;
63.最后,rtm工艺模具合模,加热至130℃,同时抽负压至20kpa,保持5h,降温后得到复合加强板。
64.其中,步骤三铺设的基本层10包括8层从下至上依次铺设的碳纤维布,2层夹设在碳纤维布中的玻璃纤维布;8层碳纤维布按照碳纤维丝编排方向铺设角度依次为120
°
、+60
°
、90
°
、0
°
、0
°
、90
°
、
‑
60
°
、120
°
;第一层玻璃纤维布夹设在+60
°
与90
°
之间,第二层玻璃纤维布夹设在90
°
与
‑
60
°
之间。
65.步骤三铺设的第一增强层11包括8层碳纤维、玻璃纤维组成的混合编织布;其中,8层混合编织布按照碳纤维丝编排方向从下至上铺设角度依次为+45
°
、
‑
45
°
、90
°
、0
°
、90
°
、0
°
、
‑
45
°
、+45
°
;
66.第二增强层12与第一增强层11层数相同且关于基本层10中心对称铺设;并且第一增强层11与第二增强层12混合编织布的边缘处逐层向内收缩,使边缘呈三角形;其中,第一增强层11厚度与三角形高的比值为0.08。
67.实施例3:
68.与实施例2不同的是:在步骤一中预埋固定片230与第一预埋金属环20由一整块厚度为1.2mm的钢板经过慢走丝切割得到;
69.其中,第一预埋金属环20为边长为55cm的矩形钢环;
70.在步骤二中准备8k碳纤维丝束、800tex玻璃纤维丝束;将准备好的碳纤维丝束、玻璃纤维丝束按照比例5:1排列设置作为编织纬线;将编织纬线、编织经线上下交错编织得到混合编织布;
71.在步骤三中将裁剪好的材料放入复合环氧树脂中在130℃条件下浸泡30min;复合环氧树脂由28份双酚a型环氧树脂、15份高温韧性环氧树脂以及8份氨基四官能团环氧树脂在90℃条件下混合搅拌30min得到;
72.在rtm工艺模具合模中,加热至160℃,同时抽负压至12kpa,保持6.5h,降温后得到复合加强板。
73.其中,步骤三铺设的基本层10包括7层从下至上依次铺设的碳纤维布,2层夹设在碳纤维布中的玻璃纤维布;7层碳纤维布按照碳纤维丝编排方向铺设角度依次为120
°
、+60
°
、90
°
、0
°
、90
°
、
‑
60
°
、120
°
;第一层玻璃纤维布夹设在+60
°
与90
°
之间,第二层玻璃纤维布夹设在90
°
与
‑
60
°
之间。
74.步骤三铺设的第一增强层11包括7层碳纤维、玻璃纤维组成的混合编织布;其中,7层混合编织布按照碳纤维丝编排方向从下至上铺设角度依次为+45
°
、
‑
45
°
、90
°
、0
°
、90
°
、
‑
45
°
、+45
°
;
75.实施例4:与实施例2不同的是:在步骤一中预埋固定片230与第一预埋金属环20由一整块厚度为0.8mm的钢板经过慢走丝切割得到;
76.其中,第一预埋金属环20为直径为55cm的钢制圆环;
77.在步骤二中准备10k碳纤维丝束、800tex玻璃纤维丝束;将准备好的碳纤维丝束、玻璃纤维丝束按照比例4:1排列设置作为编织纬线;将编织纬线、编织经线上下交错编织得到混合编织布;
78.在步骤三中将裁剪好的材料放入复合环氧树脂中在130℃条件下浸泡25min;复合环氧树脂由28份双酚a型环氧树脂、15份高温韧性环氧树脂以及8份氨基四官能团环氧树脂在90℃条件下混合搅拌25min得到;
79.在rtm工艺模具合模中,加热至145℃,同时抽负压至5kpa,保持8h,降温后得到复合加强板。
80.其中,步骤三铺设的基本层10包括9层从下至上依次铺设的碳纤维布,2层夹设在碳纤维布中的玻璃纤维布;9层碳纤维布按照碳纤维丝编排方向铺设角度依次为120
°
、+60
°
、+45
°
、0
°
、90
°
、0
°
、
‑
45
°
、
‑
60
°
、120
°
;第一层玻璃纤维布夹设在+60
°
与+45
°
之间,第二层玻璃纤维布夹设在
‑
45
°
与
‑
60
°
之间。
81.步骤三铺设的第一增强层11包括9层碳纤维、玻璃纤维组成的混合编织布;其中,8层混合编织布按照碳纤维丝编排方向从下至上铺设角度依次为+45
°
、
‑
45
°
、0
°
、90
°
、0
°
、90
°
、0
°
、
‑
45
°
、+45
°
。
82.试验例:按照上述实施例2、实施例3以及实施例4的方法制备能够与汽车车架连接的复合加强板,并对得到的复合加强板进行实验检测,得到如下数据:
83.表1:复合加强板与钢制车身板件力学参数对比
[0084][0085]
需要说明的是,与车架连接的钢制车身板件在需要加强处通常采用厚度在1.8mm以上的钢板;上述方法得到的复合加强板厚度为5~6mm;通过表1中的数据能够得到实施例3为上述方法中的最佳实施方案,其抗拉强度能达到2895mpa。
[0086]
结合表1中的密度、抗拉强度以及弹性模量数据,不仅能够在很大程度上提高车辆应用板材的强度,提高车辆的安全性能,还能够实现车辆减重,有质量轻、强度高的优点,在汽车车身复合板技术领域具有显著进步。