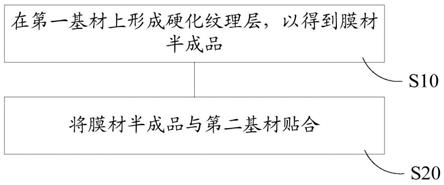
1.本发明涉及电子设备的技术领域,具体是涉及一种电子设备、壳体组件、膜材及其制备方法。
背景技术:2.为了在塑胶产品上达到现有蚀刻玻璃的触感及外观效果,常规技术通过uv转印或者打印的方案在pc/pmma复合板材上实现具有爽滑触感或闪点效果的纹理,并通过高压热弯成型出需要的外观形态。目前该工艺方案被广泛应用于手机板材后盖上,以提升用户体验及外观效果。但该方案使用的pc/pmma厚度至少需要0.64mm,已无法满足行业追求轻薄的需求。
技术实现要素:3.本技术实施例第一方面提供了一种膜材的制备方法,所述制备方法包括:
4.在第一基材上形成硬化纹理层,以得到膜材半成品;
5.将所述膜材半成品与第二基材贴合;
6.其中,所述第二基材的材质为透明玻纤环氧树脂;所述第一基材夹设于所述硬化纹理层与所述第二基材之间。
7.第二方面,本技术实施例提供一种用于电子设备壳体上的膜材,所述膜材包括:依次层叠设置的第二基材、第一基材以及硬化纹理层;其中,所述第二基材的材质为透明玻纤环氧树脂,所述第一基材的材质为柔性透明树脂;所述第二基材的厚度不大于0.4mm。
8.另外,本技术实施例又提供一种壳体组件,所述壳体组件包括透明壳体以及上述实施例中任一项所述的膜材,所述透明壳体与所述膜材贴合。
9.进一步地,本技术实施例还提供一种电子设备,所述电子设备包括控制电路板、显示屏模组以及上述实施例中所述的壳体组件,所述显示屏模组与所述壳体组件配合形成容置空间,所述控制电路板设于所述容置空间内,并与所述显示屏模组电连接。
10.本技术实施例提供的膜材的制备方法,可以使用较薄的明玻纤环氧树脂材料,进而使得膜材整体更加轻薄(膜材整体厚度可以做到0.4mm以内),另外,该制备方法得到的膜材具有与常规技术中采用pc/pmma复合板材或玻璃相似的外观以及触感效果。
附图说明
11.为了更清楚地说明本发明实施例中的技术方案,下面将对实施例描述中所需要使用的附图作简单地介绍,显而易见地,下面描述中的附图仅仅是本发明的一些实施例,对于本领域普通技术人员来讲,在不付出创造性劳动的前提下,还可以根据这些附图获得其他的附图。
12.图1是本技术膜材的制备方法一实施例的流程示意图;
13.图2是膜材半成品一实施例的结构示意图;
14.图3是在第一基材上形成硬化纹理层,以得到膜材半成品一实施例的流程示意图;
15.图4是在第一基材上形成硬化纹理层,以得到膜材半成品另一实施例的流程示意图;
16.图5是膜材半成品又一实施例的结构示意图;
17.图6是本技术膜材一实施例的结构示意图;
18.图7是本技术膜材另一实施例的结构示意图;
19.图8是膜材半成品与玻纤环氧树脂子基材叠放的结构示意图;
20.图9是本技术膜材的制备方法还一实施例的流程示意图;
21.图10是本技术膜材还一实施例的结构示意图;
22.图11是本技术膜材再一实施例的结构示意图;
23.图12是本技术壳体组件一实施例的结构断面示意图;
24.图13是本技术电子设备一实施例的结构示意图;
25.图14是图13实施例中电子设备在a
‑
a处的结构剖视示意图;
26.图15是本技术电子设备一实施例的结构组成框图示意图。
具体实施方式
27.下面结合附图和实施例,对本发明作进一步的详细描述。特别指出的是,以下实施例仅用于说明本发明,但不对本发明的范围进行限定。同样的,以下实施例仅为本发明的部分实施例而非全部实施例,本领域普通技术人员在没有做出创造性劳动前提下所获得的所有其它实施例,都属于本发明保护的范围。
28.在本文中提及“实施例”意味着,结合实施例描述的特定特征、结构或特性可以包含在本发明的至少一个实施例中。在说明书中的各个位置出现该短语并不一定均是指相同的实施例,也不是与其它实施例互斥的独立的或备选的实施例。本领域技术人员显式地和隐式地理解的是,本文所描述的实施例可以与其它实施例相结合。
29.作为在此使用的“电子设备”(或简称为“终端”)包括,但不限于被设置成经由有线线路连接(如经由公共交换电话网络(pstn)、数字用户线路(dsl)、数字电缆、直接电缆连接,以及/或另一数据连接/网络)和/或经由(例如,针对蜂窝网络、无线局域网(wlan)、诸如dvb
‑
h网络的数字电视网络、卫星网络、am
‑
fm广播发送器,以及/或另一通信终端的)无线接口接收/发送通信信号的装置。被设置成通过无线接口通信的通信终端可以被称为“无线通信终端”、“无线终端”或“移动终端”。移动终端的示例包括,但不限于卫星或蜂窝电话;可以组合蜂窝无线电电话与数据处理、传真以及数据通信能力的个人通信系统(pcs)终端;可以包括无线电电话、寻呼机、因特网/内联网接入、web浏览器、记事簿、日历以及/或全球定位系统(gps)接收器的pda;以及常规膝上型和/或掌上型接收器或包括无线电电话收发器的其它电子装置。手机即为配置有蜂窝通信模块的电子设备。
30.常规技术中有在透明玻纤板材一侧转印具有装饰效果的纹理涂层,热弯成型后,在另一侧涂布硬化液涂层作为耐磨保护层;该方案需要先通过转印颜色及纹理效果在透明玻纤板材上再进行高压热弯,热弯温度及压力均较高,在树脂软化状态下,玻纤布纹浮现到产品表面,对印刷及纹理层造成一定破坏和干扰,最终实现效果不佳。
31.另外,还有一种常规技术是在pc/pmma复合板材表面打印哑面油墨,背面转印纹理
电镀层,该方案可实现外纹理触感及闪点炫彩效果。但缺点是打印油墨的精细度不高,出来的纹理效果粗糙,手感效果不佳。
32.其中,常规技术中还有在pc/pmma复合板材正面先淋涂一层硬化层,再转印一层uv纹理层,起到提升手感及外观的作用;但缺点是pc/pmma材料厚度胶厚,总体厚度达到0.6~0.65mm,且uv硬化纹理层跟随pc/pmma一起热弯的过程中容易开裂,且硬化层硬度(铅笔硬度又称涂膜硬度铅笔测定法。是一种标定涂膜硬度的测试方法和量度体系。按工业标准,铅笔笔芯的硬度分为13级)只有3~5h。
33.有鉴于此,本技术实施例提供一种膜材的制备方法,请参阅图1,图1是本技术膜材的制备方法一实施例的流程示意图;需要说明的是,本技术实施例中的膜材可以是用于电子设备的外壳上,而电子设备可以包括手机、平板电脑、笔记本电脑、可穿戴设备等。该膜材的制备方法包括但不限于以下步骤。本技术实施例中的术语“包括”和“具有”以及它们任何变形,意图在于覆盖不排他的包含。例如包含了一系列步骤或单元的过程、方法、系统、产品或设备没有限定于已列出的步骤或单元,而是可选地还包括没有列出的步骤或单元,或可选地还包括对于这些过程、方法、产品或设备固有的其它步骤或组件。
34.步骤s10,在第一基材上形成硬化纹理层,以得到膜材半成品。
35.其中,请参阅图2,图2是膜材半成品一实施例的结构示意图。可选地,第一基材110的材质可以为pet(polyethylene terephthalate简称pet或peit,俗称涤纶树脂,对苯二甲酸与乙二醇的缩聚物)、pmma(聚甲基丙烯酸甲酯(poly(methyl methacrylate)),简称pmma),又称做压克力、亚克力(英文acrylic)或有机玻璃)、pc(polycarbonate,聚碳酸酯(英文简称pc)是分子链中含有碳酸酯基的高分子聚合物)、pi(聚酰亚胺(polyimide))等。第一基材110的厚度可以是小于0.2mm,具体可以为0.05mm、0.06mm、0.1mm以及0.15mm等。关于第一基材110的详细厚度值此处不做具体限定。硬化纹理层120则是具有纹理的硬化层,具体的材料组成将在后续实施例中进行详述。
36.其中,在第一基材上形成硬化纹理层,以得到膜材半成品的步骤具体包括如下步骤,请参阅图3,图3是在第一基材上形成硬化纹理层,以得到膜材半成品一实施例的流程示意图,在本实施例中,在第一基材上形成硬化纹理层,以得到膜材半成品的步骤包括步骤s10a:在带有纹理的离型纸上涂布或淋涂形成硬化液层。其中,硬化液层采用的材料可以为双固化型硬化液。双固化型硬化液的组成可以为:聚氨酯丙烯酸酯(pua)含量35
‑
45%,单体(可以为但不限于为1、6
‑
己二醇二丙烯酸酯(hdda)、丙烯酸异冰片酯(iboa)、双季戊四醇六丙烯酸酯(dpha)、丙烯酸四氢糠基酯(thfa)、n
‑
乙烯基吡咯烷酮(nvp)、三羟甲基环己基丙烯酸酯(tmcha)、新戊二醇二丙烯酸酯(npgda)、季戊四醇三丙烯酸酯(peta)、三羟甲基丙烷三丙烯酸酯(tmpta)中的一种或多种)10
‑
15%,稀释剂45
‑
55%,光引发剂3
‑
5%,助剂(流平剂、消泡剂)0.5
‑
1%,固化剂(譬如芳香族异氰酸酯
──
tdi/mdi/ndi/todi;脂肪族异氰酸酯
──
hdi(六亚甲基二异氰酸酯)/tmdi/xdi以及脂环族异氰酸酯
──
ipdi(六亚甲基二异氰酸酯)/hmdi(异氟尔酮二异氰酸酯)/htdi(二环己基甲烷
‑
4,4'
‑
二异氰酸酯)等)3
‑
10%,其中,上述百分比的含量均为质量分数。
37.步骤s10b,对硬化液层进行加热,以使得硬化液层半固化。
38.在涂覆硬化液层后,可以是在60
‑
85℃下烘烤3
‑
5min使硬化液层烘干,硬化液层在固化剂的作用下烘烤得到初步固化。
39.步骤s10c:将第一基材与半固化的硬化液层贴合并加热,使得硬化液层完全固化形成硬化纹理层并与第一基材粘接。
40.在该步骤中,可以是将第一基材通过滚轮,辊压在离型纸内侧硬化液层上,再通过另一个滚轮绕卷实现纹理的卷对卷转印。撕去离型纸,将第一基材110带有硬化纹理层120的一侧通过汞灯照射,汞灯固化能量800
‑
1200mj/cm2,实现硬化纹理层120的完全固化。
41.请参阅图4,图4是在第一基材上形成硬化纹理层,以得到膜材半成品另一实施例的流程示意图,在本实施例中,在第一基材上形成硬化纹理层,以得到膜材半成品的步骤包括步骤s10d:在带有纹理的离型纸上涂布或淋涂形成硬化液层。其中,硬化液层采用的材料可以为双固化型硬化液。双固化型硬化液的组成可以为:聚氨酯丙烯酸酯(pua)含量35
‑
45%,单体(可以为但不限于为1、6
‑
己二醇二丙烯酸酯(hdda)、丙烯酸异冰片酯(iboa)、双季戊四醇六丙烯酸酯(dpha)、丙烯酸四氢糠基酯(thfa)、n
‑
乙烯基吡咯烷酮(nvp)、三羟甲基环己基丙烯酸酯(tmcha)、新戊二醇二丙烯酸酯(npgda)、季戊四醇三丙烯酸酯(peta)、三羟甲基丙烷三丙烯酸酯(tmpta)中的一种或多种)10
‑
15%,稀释剂45
‑
55%,光引发剂3
‑
5%,助剂(流平剂、消泡剂)0.5
‑
1%,固化剂(譬如芳香族异氰酸酯
──
tdi/mdi/ndi/todi;脂肪族异氰酸酯
──
hdi(六亚甲基二异氰酸酯)/tmdi/xdi以及脂环族异氰酸酯
──
ipdi(六亚甲基二异氰酸酯)/hmdi(异氟尔酮二异氰酸酯)/htdi(二环己基甲烷
‑
4,4'
‑
二异氰酸酯)等)3
‑
10%,其中,上述百分比的含量均为质量分数。
42.步骤s10e:对硬化液层进行加热,以使得硬化液层固化形成硬化纹理层。
43.在该步骤中,可以是利用烤箱烘烤涂布后的得硬化液层,具体可以是在60
‑
95℃下烘烤5
‑
10min。还可以是利用汞灯照射,汞灯固化能量可以是800
‑
1200mj/cm2,实现硬化纹理层120的完全固化。
44.步骤s10f:将硬化纹理层通过胶膜粘接于第一基材。
45.请参阅图5,图5是膜材半成品又一实施例的结构示意图,其中,胶膜130的厚度可以为0.03~0.05mm。胶膜130的材质为透明光学胶。第一基材110的厚度可以是小于0.2mm,具体可以为0.05mm、0.06mm、0.1mm以及0.15mm等。
46.请继续参阅图1,膜材制备方法的步骤s20为:将膜材半成品与第二基材贴合。
47.在该步骤中,请一并参阅图6和图7,其中,图6是本技术膜材一实施例的结构示意图,图7是本技术膜材另一实施例的结构示意图。图6实施例中为采用图3方法制备形成膜材半成品的结构示意图,而图7实施例中则是采用图4方法制备形成膜材半成品的结构示意图。在图6实施例中膜材100的第二基材140的材质为透明玻纤环氧树脂;所述第一基材110夹设于所述硬化纹理层120与所述第二基材140之间。在图7实施例中,所述第一基材110夹设于所述胶膜130与所述第二基材140之间。需要说明的是,本技术实施例中的术语“第一”、“第二”、“第三”仅用于描述目的,而不能理解为指示或暗示相对重要性或者隐含指明所指示的技术特征的数量。由此,限定有“第一”、“第二”、“第三”的特征可以明示或者隐含地包括至少一个该特征。本发明的描述中,“多个”的含义是至少两个,例如两个,三个等,除非另有明确具体的限定。
48.玻纤环氧树脂材料可以将电子设备壳体的厚度做最薄0.2mm,在不减弱强度的基础之上,也可以将玻纤板材(第二基材140)的厚度做到0.4mm以下,在本实施例中,第二基材140具体可以是采用0.3mm的厚度,这就使透明玻纤板材替代传统的pc/pmma板成为了趋势。
49.可选地,将膜材半成品与第二基材贴合的步骤可以是包括:将膜材半成品与第二基材通过热压的方式一体成型。具体而言,可以是将膜材半成品与第二基材放置于热压成型模具当中热弯成型,获得目标弧度和弧高的背盖。成型压力可以为30kg~80kg,覆合温度可以为120℃~170℃,成型时间可以为100~150min,成型时间过短则树脂固化不完全,时间过长影响生产效率。成型完成后膜材的整体厚度t在0.3~0.4mm。相较于传统技术采用pc/pmma复合板材正面先淋涂一层硬化层,再转印一层uv纹理层的方式形成的膜材厚度在0.6~0.65mm,大幅降低了膜材的厚度。
50.可选地,在将膜材半成品与第二基材通过热压的方式一体成型的步骤之前还可以包括将膜材半成品与多片子基材呈预设错位角度堆叠预浸料的步骤;其中,所述多片子基材热压后形成第二基材。具体可以为将膜材半成品101与三层玻纤环氧树脂(子基材141)预浸料成45
°
角叠放(当然,在一些其他实施例中还可以是30度、60度等其他角度叠放),膜材半成品的厚度0.05~0.1mm,单层玻纤环氧树脂(子基材)的厚度可以为0.1mm。呈预设角度叠放的好处是,提高热弯成型过程中的变形能力,以及使得内部应力可以得到更好的释放。请参阅图8,图8是膜材半成品与玻纤环氧树脂子基材叠放的结构示意图。
51.在该步骤之后还可以包括将膜材半成品和玻纤预浸料(多个玻纤环氧树脂子基材)裁切成等大的长方形,以备后续的热弯成型过程使用。
52.在步骤s20之后还可以包括cnc加工的步骤,具体可以为通过cnc铣去边角料,获得尺寸大小一致的膜材成品。
53.本技术实施例提供的膜材制备方法,可以在透明玻纤表面实现传统技术中在pmma/pc复合板材外纹理效果的方案。首先将0.05mm带纹理(硬化层)的pet膜材与0.3mm的透明玻纤环氧树脂板材在热压模具中一体成型出来,得到约0.35mm厚度的带纹理的透明玻纤环氧树脂板材,得到与常规技术中pc/pmma复合板材或玻璃相似效果的电子设备后盖产品。对比传统技术中pc/pmma成品后盖厚度0.7mm,本技术技术方案中的膜材可以将厚度减薄至0.4mm以下;由于pet膜材在成型热弯过程树脂固化之前不完全跟随玻纤环氧树脂板材同步拉伸,因此可以预留足够的长宽尺寸可以确保表面硬化纹理层不被过度拉伸开裂,因此硬化层硬度超过传统pc/pmma复合板材表面硬化涂层,可以达到铅笔硬度5~6h;pet膜材与玻纤板材之间可以直接通过环氧树脂联结,不需要通过额外的胶水层(当然,如前述图4实施例中的技术方案,也可以是先将硬化纹理层完全固化,然后利用胶膜与玻纤板材(第二基材)粘接)。耐磨测试得到显著提升,钢丝绒#0000可以完成2000次实验ok通过,而传统技术方案中的pc/pmma复合板材外纹理钢丝绒#0000不会超过500次。
54.请参阅图9,图9是本技术膜材的制备方法还一实施例的流程示意图;该膜材的制备方法包括但不限于以下步骤。
55.步骤s10,在第一基材上形成硬化纹理层,以得到膜材半成品。
56.步骤s20,将膜材半成品与第二基材贴合。
57.其中,关于步骤s10和步骤s20的详细过程,请参阅前述实施例中的相关描述,此处亦不再详述。
58.与前述实施例不同的是,本实施例中的制备方法还包括步骤s30,在第二基材背离第一基材的表面形成外观膜层。请一并参阅图10和图11,图10是本技术膜材还一实施例的结构示意图,图11是本技术膜材再一实施例的结构示意图。其中,外观膜层150包括颜色层、
uv纹理层、电镀层以及盖底油墨层中的至少一种。外观膜层150可以是颜色层、uv纹理层、电镀层以及盖底油墨层中的任意一种,也可以是上述两种或者多种的组合。另外,还可以包括喷涂补边的步骤:对于膜材上膜片未遮盖到的边缘区域进行对应颜色的喷涂补边。图中标注160表示为补边区域。需要说明的是,本技术实施例中所有方向性指示(诸如上、下、左、右、前、后
……
)仅用于解释在某一特定姿态(如附图所示)下各部件之间的相对位置关系、运动情况等,如果该特定姿态发生改变时,则该方向性指示也相应地随之改变。
59.本技术实施例提供的膜材,可以针对市面上包含触感纹理(如磨砂)的电子设备背盖(主要为pmma/pc复合板材)做较大幅度减薄,如上述工艺介绍,该方案可将整体后盖减薄至0.4mm以内,而且相对pc/pmma复合板材其刚度提升30%以上。请参阅下表,下表是本技术技术方案与pc/pmma复合板材形成的膜材结构刚度测试的比较结果。
[0060][0061]
相对与传统技术中的pmma/pc板材表面硬化纹理层需要在高压成型后再进行二次固化,需要兼顾硬化层的断裂延伸率,本技术实施例中的技术方案可以降低对硬化层锻炼延伸率的要求,从而提升硬化层本身的硬度。pc/pmma复合板材硬化层断裂延伸率50%~200%,硬度3h
‑
5h,本技术实施例中使用的硬化层材料断裂延伸率要求在20%~50%即可满足要求,因此表面硬度可以做的更大,具体可以做到5h
‑
6h。
[0062]
另外,本技术实施例还提供一种壳体组件,请参阅图12,图12是本技术壳体组件一实施例的结构断面示意图;需要说明的是,本技术中的壳体组件可以用于电子设备,而电子设备可以包括手机、平板电脑、笔记本电脑、可穿戴设备等。本实施例中的壳体组件10包括透明壳体200以及前述实施例中的膜材100。所述透明壳体200与所述膜材100贴合。
[0063]
本实施例中的壳体组件,其膜材使用较薄的明玻纤环氧树脂材料,进而使得膜材整体更加轻薄(膜材整体厚度可以做到0.4mm以内),另外,得到的膜材具有与常规技术中采用pc/pmma复合板材或玻璃相似的外观以及触感效果。
[0064]
进一步地,本技术实施例还提供一种电子设备,请一并参阅图13和图14,图13是本技术电子设备一实施例的结构示意图,图14是图13实施例中电子设备在a
‑
a处的结构剖视示意图,本实施例中的电子设备可以包括显示屏模组30、壳体组件10以及控制电路板20。其中,壳体组件10可以包括膜材100、透明壳体200以及中框400。这里需要说明的是,本技术实施例仅以电子设备包括中框的结构进行说明,在一起其他实施例中,电子设备可以不包括中框结构,即壳体组件的后盖板(透明壳体200)直接与显示屏模组30配合的结构,此处不做具体限定。
[0065]
可选地,所述显示屏模组30与所述壳体组件10的膜材100以及透明壳体200分别设于所述中框400的相对两侧。显示屏模组30与所述透明壳体200配合形成容置空间1000,所述控制电路板20以及所述膜材100设于所述容置空间1000内,所述膜材100贴设于所述透明壳体200的内表面。控制电路板20与显示屏模组30电连接,控制电路板20用于控制所述显示
屏模组30。关于电子设备其他部分结构的详细技术特征在本领域技术人员的理解范围内,此处亦不再赘述。
[0066]
请参阅图15,图15是本技术电子设备一实施例的结构组成框图示意图,该电子设备可以为手机、平板电脑、笔记本电脑以及可穿戴设备等,本实施例图示以手机为例。该电子设备的结构可以包括rf电路910、存储器920、输入单元930、显示单元940(即上述实施例中的显示屏模组30)、传感器950、音频电路960、wifi模块970、处理器980(可以为前述实施例中的控制电路板20)以及电源990等。其中,rf电路910、存储器920、输入单元930、显示单元940、传感器950、音频电路960以及wifi模块970分别与处理器980连接;电源990用于为整个电子设备提供电能。
[0067]
具体而言,rf电路910用于接发信号;存储器920用于存储数据指令信息;输入单元930用于输入信息,具体可以包括触控面板931以及操作按键等其他输入设备932;显示单元940则可以包括显示面板941等;传感器950包括红外传感器、激光传感器等,用于检测用户接近信号、距离信号等;扬声器961以及传声器(或者麦克风)962通过音频电路960与处理器980连接,用于接发声音信号;wifi模块970则用于接收和发射wifi信号,处理器980用于处理电子设备的数据信息。关于电子设备具体的结构特征,请参阅上述实施例的相关描述,此处不再进行详细介绍。
[0068]
本实施例中的电子设备,其壳体组件的膜材使用较薄的明玻纤环氧树脂材料,进而使得膜材整体更加轻薄(膜材整体厚度可以做到0.4mm以内),另外,得到的膜材具有与常规技术中采用pc/pmma复合板材或玻璃相似的外观以及触感效果。
[0069]
以上所述仅为本发明的部分实施例,并非因此限制本发明的保护范围,凡是利用本发明说明书及附图内容所作的等效装置或等效流程变换,或直接或间接运用在其他相关的技术领域,均同理包括在本发明的专利保护范围内。