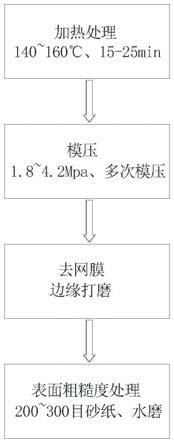
1.本发明涉及复合材料表面改性技术领域,特别涉及一种增强复合材料表面物粘性的工艺。
背景技术:2.复合材料,像碳纤维板和玻璃纤维板等是一种新型非金属材料,有着强度高、规模大、耐疲劳和抗蠕变性能高等优良性能。复合材料增强树脂基复合材料具有高比模量、高比强度和低密度等优异性能,因此被广泛应用于航空航天、建筑和汽车等行业。其中,复合材料是增强体,为主要的承力结构,树脂基体起连接纤维和传递载荷的作用。复合材料的性能不仅取决于其组分材料,同时也很大程度上取决于各组分间界面的质量,复合材料的界面是增强相和基体相的中间相,是增强相和基体相连接的桥梁,也是应力、热量的传递者,良好的界面结合能有效地传递载荷和热量,提高复合材料的热导率及其力学性能。
3.但复合材料表面惰性大,表面能低,缺乏有化学活性的官能团,反应活性低,与基体的粘结性差,现有的复合材料表面在进行处理的时候,通常采用离型剂作为辅助粘连剂,让离型膜粘连到复合材料的表面,但残余的离型剂使得复合材料的表面粗糙度下降,不利于复合材料表面与其他材料相互结合。
技术实现要素:4.本发明旨在至少解决现有技术中存在的“离型剂作为辅助粘连剂,让离型膜粘连到复合材料的表面,但残余的离型剂使得复合材料的表面粗糙度下降,不利于复合材料表面与其他材料相互结合”的技术问题。为此,本发明提出一种增强复合材料表面物粘性的工艺,无需使用离型剂,使离型膜粘附在复合材料的表面上,增大复合材料表面的粗糙度,粘接材料更容易与表面粘接。
5.根据本发明的一些实施例的一种增强复合材料表面物粘性的工艺,包括复合材料板材,所述复合材料板材的表面设置有离型膜,所述离型膜和所述复合材料板材之间设置有复合棉布热熔胶网膜;所述复合材料板材、所述复合棉布热熔胶网膜和所述离型膜经过加热处理、模压、去除网膜和表面粗糙度处理四个处理步骤,所述复合材料板材的表面与所述离型膜粘合,所述离型膜的表面与其他粘接材料结合。
6.根据本发明的一些实施例,加热处理步骤把所述复合材料板材、所述复合棉布热熔胶网膜和所述离型膜放入加热装置中,加热温度140~160℃,加热时间15-25min。
7.根据本发明的一些实施例,模压步骤把加热处理好的所述复合材料板材、所述复合棉布热熔胶网膜和所述离型膜放入模压机的工作台上,模压压力1.8~4.2mpa。
8.根据本发明的一些实施例,模压过程采用反复模压的方式,对所述复合材料板材、所述复合棉布热熔胶网膜和所述离型膜反复模压3~5次。
9.根据本发明的一些实施例,模压过程采用阶梯压力进行模压,每次模压的压力递增0.2~0.5mpa。
10.根据本发明的一些实施例,去网膜步骤把模压后的所述复合材料板材、所述复合棉布热熔胶网膜和所述离型膜取出,切除所述复合材料板材周缘多余的所述复合棉布热熔胶网膜,所述复合材料板材的周缘进行圆滑打磨处理。
11.根据本发明的一些实施例,表面粗糙度处理步骤把所述复合材料板材放置到打磨装置中,采用200~300目的砂纸打磨。
12.根据本发明的一些实施例,打磨过程采用水磨的方式进行打磨。
13.根据本发明的一些实施例,所述复合棉布热熔胶网膜采用tpu热熔胶网膜、eva热熔胶网膜、pa热熔胶网膜和pes热熔胶网膜中的任意一种。
14.根据本发明的一些实施例,所述复合材料板材的正反两面均采用加热处理、模压、去除网膜和表面粗糙度处理四个处理步骤。
15.根据本发明的一些实施例的一种增强复合材料表面物粘性的工艺,至少具有如下有益效果:所述复合材料板材的表面上依次设置所述复合棉布热熔胶网膜和所述离型膜,通过加热处理、模压、去除网膜和表面粗糙度处理四个步骤,使所述离型膜与所述复合材料板材的粘连在一起,避免使用离型剂进行粘连过程中残留的离型剂降低所述复合材料板材的粗糙度,有利于表面与其他材料相互结合。
16.本发明的附加方面和优点将在下面的描述中部分给出,部分将从下面的描述中变得明显,或通过本发明的实践了解到。
附图说明
17.本发明的上述和/或附加的方面和优点从结合下面附图对实施例的描述中将变得明显和容易理解,其中:
18.图1为本发明实施例的复合材料板材表面层次结构示意图;
19.图2为本发明实施例一种增强复合材料表面物粘性的工艺的示意图。
20.附图标记:
21.复合材料板材100、复合棉布热熔胶网膜200、离型膜300。
具体实施方式
22.下面详细描述本发明的实施例,实施例的示例在附图中示出,其中自始至终相同或类似的标号表示相同或类似的元件或具有相同或类似功能的元件。下面通过参考附图描述的实施例是示例性的,仅用于解释本发明,而不能理解为对本发明的限制。
23.在本发明的描述中,需要理解的是,涉及到方位描述,例如上、下、前、后、左、右、顶、底等指示的方位或位置关系为基于附图所示的方位或位置关系,仅是为了便于描述本发明和简化描述,而不是指示或暗示所指的装置或元件必须具有特定的方位、以特定的方位构造和操作,因此不能理解为对本发明的限制。
24.在本发明的描述中,若干的含义是一个或者多个,多个的含义是两个以上,大于、小于、超过等理解为不包括本数,以上、以下、以内等理解为包括本数。如果有描述到第一、第二只是用于区分技术特征为目的,而不能理解为指示或暗示相对重要性或者隐含指明所指示的技术特征的数量或者隐含指明所指示的技术特征的先后关系。
25.本发明的描述中,除非另有明确的限定,设置、安装、连接等词语应做广义理解,所
属技术领域技术人员可以结合技术方案的具体内容合理确定上述词语在本发明中的具体含义。
26.下面参考图1-图2描述根据本发明实施例的一种增强复合材料表面物粘性的工艺,本发明中所提及的复合材料主要涉及碳纤维板材和玻璃纤维板材。
27.如图1-图2所示,一种增强复合材料表面物粘性的工艺,包括复合材料板材100,在复合材料板材100的表面设置有离型膜300,离型膜300能够增加复合材料板材100的表面附着能力,使粘接板材粘贴到复合材料板材100的表面。在复合材料板材100和离型膜300之间设置有复合棉布热熔胶网膜200,复合材料板材100、复合棉布热熔胶网膜200和离型膜300通过加热处理、模压、取出网膜和表面粗糙度处理四个处理步骤,使复合材料板材100的表面与离型膜300粘合,离型膜300的表面与其他粘接材料结合。
28.现有的碳纤维板材或玻璃纤维板材表面处理工艺一般采用离型剂辅助复合材料板材100和离型膜300之间粘连,离型剂在粘合过程中会有局部残留胶体附着在离型膜300的表面,导致复合材料板材100表面的粗糙度降低,离型剂胶体填充在复合材料板材100的缝隙中,即使通过打磨,也无法把离型剂完全去除,导致复合材料板材100的表面无法很好地与其他粘接材料结合,并且在日常使用过程中,粘接材料存在脱落风险。
29.而本发明采用的复合棉布热熔胶网膜200,为片状胶膜,加热后呈现粘性,相比于离型剂,合棉布热熔胶网膜的稳定性更高,能够有效避免粘合剂残留或渗到复合材料板材100的表面。复合棉布热熔胶网膜200采用加热处理、模压、取出网膜的步骤工艺,使离型膜300粘连到复合材料板材100的表面,再对复合材料板材100的表面进行粗糙度打磨处理。
30.在本发明的一些实施例中,如图1和图2所示,加热步骤中,工作人员或机械手把叠好的复合材料板材100、复合棉布热熔胶网膜200和离型膜300放入加热装置中,加热温度140~160℃,加热时间15-25min。具体地,在本实施例中,加热温度为145℃,加热时间根据复合材料板材100和离型膜300的厚度来选择加热时间。加热装置在对复合材料板材100、复合棉布热熔胶网膜200和离型膜300加热前,先进行预热,达到指定温度后再放入复合材料板材100、复合棉布热熔胶网膜200和离型膜300进行加热。
31.在本发明的一些实施例中,如图1和图2所示,在模压步骤中,把加热处理好的复合材料板材100、复合棉布热熔胶网膜200和离型膜300从加热装置中取出,工作人员通过机械手把板材吸取到魔牙机的工作台上,模压压力1.8~4.2mpa。持续施压,使处于熔融状的复合棉布热熔胶网膜200的上下两面分别与离型膜300和复合材料板材100粘合,通过施加压力的方式让复合棉布热熔胶网膜200充分展开并降低其厚度,使离型膜300和复合材料板材100之间的连接更紧密。模压压力根据实际加工的复合材料板材100和离型膜300的厚度进行调整,应理解,在不脱离本发明基本构思的前提下,1.8~4.2mpa范围内的模压压力数值,均应视为在本发明限定的保护范围之内。
32.具体地,模压过程采用反复模压的方式,在一轮完整的模压过程中,对复合材料板材100、复合棉布热熔胶网膜200和离型膜300反复模压3~5次,通过对板材反复模压。单次模压后,模压分离,使复合材料板材100的内部应力消退,再进行模压,避免复合材料板材100的应力集中导致板材出现裂痕。
33.并且为了提升模压的效果,减少复合材料板材100和离型膜300之间的缝隙,模压过程中采用阶梯压力进行模压,每次模压的压力值递增0.2~0.5mpa。在其他实施例中,第
一次模压时采用1.8mpa作为起始压力值,第二次模压时,压力值递增0.2mpa,即第二次模压压力值为2.0mpa,以此类推,一轮模压过程中,每次递增的压力值相等。一轮模压过程中,通过每次增加压力值,来使离型膜300与复合材料板材100之间的缝隙逐渐减少,能够逐步试探出当前厚度的复合材料板材100的加工极限。
34.应理解,本实施例所采用的加热和模压分开操作的装置并非唯一实施方式,在其他一些实施例中,还可以根据实际生产需求采用带加热功能的模压装置进行加工,板材通过机械手放到加工台上,模压装置的压板在达到指定温度后靠近板材,并与板材表面接触,加热一定时间后压板对板材进行阶梯施压。本发明对实施步骤的组合方式不一一赘述,应理解,在不脱离本发明基本构思的前提下,实施步骤的组合方式灵活变换,均应视为在本发明限定的保护范围之内。
35.在本发明的一些实施例中,如图1和图2所示,复合材料板材100、复合棉布热熔胶网膜200和离型膜300取出模压完成后,工作人员通过机械手把板材吸取到去网膜步骤的工作台上,通过切割刀具切除复合材料板材100周缘多余的复合棉布热熔胶网膜200,再采用磨盘对复合材料板材100的周缘进行圆滑打磨处理。复合材料板材100边缘打磨后,能够减少边缘的毛刺,更加平滑。
36.在本发明的一些实施例中,如图1和图2所示,切除多余的复合棉布热熔胶网膜200,到表面粗糙度处理步骤,机械手把复合材料板材100放置到打磨装置中,采用200~300目的砂纸进行打磨,打磨过程采用单一目数砂纸进行打磨。在本实施例中,采用240目的砂纸进行打磨,对复合材料板材100的表面进行粗糙度处理,具体地,为了保证打磨质量和安全性,打磨过程采用水磨的方式进行打磨,无需再细化打磨,240目的砂纸水磨能够给后续其他粘接材料提供更好的粘结力。采用水磨打磨的方式,能够防止干磨的碳纤维板材或玻璃纤维板材粉尘进入板材表面细小的缝隙中,干磨所产生的粉尘进入缝隙后极不容易清理,水洗也难以清理。在缝隙残留粉尘的前提下直接粘贴其他粘接材料,会导致粘接力下降,长期使用后,复合材料板材100表面容易出现气泡、粘接材料脱落等风险,降低良品率。水磨处理,能够保证碳纤维板材或玻璃纤维板材粉尘不会四处飞扬,保护工作人员的身体健康,更加安全,并且产生的粉尘立刻随流水冲去,不会堆积在碳纤维板材或玻璃纤维板材表面的缝隙中。
37.应理解,本实施例所采用的240目砂纸水磨并非唯一实施方式,在其他一些实施例中,还可以根据实际生产采用的复合材料板材100的厚度和离型膜300的材质选用200~300目中的任意目数的砂纸。本发明对砂纸目数的选用不一一赘述,应理解,在不脱离本发明基本构思的前提下,砂纸目数的选用灵活变换,均应视为在本发明限定的保护范围之内。
38.在本发明的一些实施例中,如图1和图2所示,复合棉布热熔胶网膜200采用tpu热熔胶网膜、eva热熔胶网膜、pa热熔胶网膜和pes热熔胶网膜中的任意一种。
39.应理解,本实施例所提及的复合棉布热熔胶网膜200种类并非唯一实施方式,在其他一些实施例中,还可以根据实际生产采用不同种类的复合棉布热熔胶网膜200。本发明对复合棉布热熔胶网膜200的种类不一一赘述,应理解,在不脱离本发明基本构思的前提下,复合棉布热熔胶网膜200种类的选用灵活变换,均应视为在本发明限定的保护范围之内。
40.在本发明的一些实施例中,如图1和图2所示,复合材料板材100的正反两面均采用加热处理、模压、去除网膜和表面粗糙度处理四个处理步骤,根据所加工的复合材料板材
100用途决定其加工面数。
41.在本说明书的描述中,参考术语“一个实施例”、“一些实施例”、“示意性实施例”、“示例”、“具体示例”、或“一些示例”等的描述意指结合该实施例或示例描述的具体特征、结构、材料或者特点包含于本发明的至少一个实施例或示例中。在本说明书中,对上述术语的示意性表述不一定指的是相同的实施例或示例。而且,描述的具体特征、结构、材料或者特点可以在任何的一个或多个实施例或示例中以合适的方式结合。
42.尽管已经示出和描述了本发明的实施例,本领域的普通技术人员可以理解:在不脱离本发明的原理和宗旨的情况下可以对这些实施例进行多种变化、修改、替换和变型,本发明的范围由权利要求及其等同物限定。