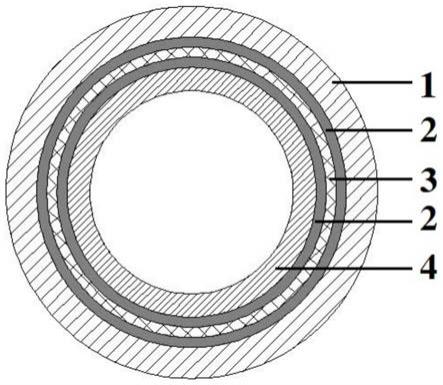
一种阻氧、防垢型pp-rct管材及其制备方法
技术领域
1.本发明属于塑料管道技术领域,具体涉及一种阻氧、防垢型pp-rct管材及其制备方法。
背景技术:2.pp-rct作为pp-r系列材料的升级产品,通过聚集态晶型转变,形成带交叉点的网络结晶结构,较传统的pp-r管在耐热、耐压、韧性等方面得以进一步提升,pp-rct表现出高耐热、高耐压、高韧性等特性。pp-rct能在温度90℃、压强1.0mpa下使用50年,比pp-r使用温度高出20℃;优异的耐压性能,可节约原料15%~20%,已成为ppr管材专用料的主要发展方向。
3.pp-rct管道具有耐酸、耐碱性,使其适于作为工业级、食品级管道,另外,其高耐压、高韧性等性能,使其亦适于对管道性能要求苛刻的场合,如商业高层建筑中的压力管道,另外,pp-rct管道还可以通过热熔合进行拼接,使用极为方便,使得pp-rct的适用范围极广。
4.然而由于塑料本身极易附着并滋生微生物,为了防止在长期使用的管道内滋生细菌、绿藻、污垢等造成管材的使用性能下降,有必要提升pp-rct管道的阻氧、防垢性能。
技术实现要素:5.针对现有技术存在的问题,本技术旨在提供一种阻氧、防垢型pp-rct管材及其制备方法,本技术提供的阻氧、防垢型pp-rct管材不仅具有良好的阻氧性能和耐压性能,并极大改善了管材的防结垢性能。
6.基于上述目的,本技术采用的技术方案如下:
7.第一方面,本技术提供一种阻氧、防垢型pp-rct管材,所述管材由外至里依次包括pp-rct层、阻氧层和防垢层;所述防垢层的材料为添加1wt%~5wt%防垢母粒的pp-rct;所述防垢母粒中含有硅氧烷改性纳米二氧化硅。
8.本技术管材的防垢层以pp-rct材料为基材,向其中添加1wt%~5wt%防垢母粒,防垢母粒中含有硅氧烷改性纳米二氧化硅,经试验发现,随着基材中防垢母粒添加量的增加,管材内层的防垢性能提升,而管材的力学性能呈下降趋势,故而选择于pp-rct中添加1wt%~5wt%防垢母粒,能够在不降低管材整体力学性能的前提下,使得管材的内表面粗糙度低至0.01μm,表面接触角高达119.5
°
,极大改善管材内层的防垢性能。
9.另外,本技术所述管材还具有良好的阻氧性能,管材透氧率低至0.10mg/(m2·
d)。
10.进一步地,防垢母粒中硅氧烷改性纳米二氧化硅的含量为30wt%~60wt%。
11.防垢母粒中硅氧烷改性纳米二氧化硅含量为30wt%~60wt%,以确保防垢母粒具有适宜的防污性能,当防垢母粒用于制备防垢层时,能够在相对较低的添加量下达到较好的防结垢性能,并尽可能降低防垢母粒对管材耐压性能产生负面影响。
12.本发明通过将硅氧烷改性纳米二氧化硅预先分散于pp-rct材料中制得防垢母粒,
再将防垢母粒分散于pp-rct材料中制得管材内层,经过两次分散,提高硅氧烷改性纳米二氧化硅于pp-rct材料中的分散均匀性,有助于提高防垢层的防垢性能均匀性。
13.进一步地,所述阻氧层的材料为乙烯-乙烯醇共聚物、聚偏二氯乙烯、聚酰胺中的至少一种。
14.进一步地,所述乙烯-乙烯醇共聚物中乙烯含量为29wt%~55wt%。
15.进一步地,所述pp-rct层的材料为α或β晶型的pp-rct。
16.进一步地,所述管材还包括设于pp-rct层与阻氧层之间、阻氧层与防垢层之间的热熔胶层。
17.进一步地,热熔胶层的材料为马来酸酐接枝聚丙烯、丙烯酸热熔胶、乙烯-醋酸乙烯共聚物、丙烯基预交联热熔胶、聚酯类热熔胶、聚酰胺热熔胶中的至少一种。
18.第二方面,本发明提供上述管材的制备方法,包括如下步骤:
19.将pp-rct层、阻氧层、防垢层各层材料分别投入挤出机,经多层共挤制得阻氧、防垢型pp-rct管材。
20.进一步地,防垢层材料由pp-rct中添加1wt%~5wt%的防垢母粒制得,所述防垢母粒的制备方法包括如下步骤:
21.s1:将20wt%~50wt%纳米二氧化硅与50wt%~80wt%硅氧烷于80℃~100℃搅匀后,加入分散剂、抗氧剂继续搅匀、冷却制得硅氧烷改性纳米二氧化硅;
22.s2:将30wt%~60wt%经s1制得的硅氧烷改性纳米二氧化硅、2wt%~5wt%润滑剂、35wt%~65wt%pp-rct经熔融共混、挤出造粒制得防垢母粒。
23.进一步地,抗氧剂的添加量为纳米二氧化硅和硅氧烷总量的0.5wt%~0.7wt%。
24.本发明采用在防垢母粒制备过程中使用抗氧剂,经试验发现,抗氧剂有助于提高防垢母粒的耐老化稳定性,并有助于改善管材防垢层的防垢性能。随着抗氧剂添加量的增加,防垢母粒的氧化诱导期(oit值)呈升高趋势,当抗氧剂的添加量为0.5wt%,防垢母粒已具有较优的耐老化稳定性,基于成本考虑,抗氧剂的添加量以0.5wt%~0.7wt%为宜。
25.进一步地,抗氧剂由主抗氧剂与辅抗氧剂复配而成,主抗氧剂为抗氧剂1010、抗氧剂1076中的至少一种;辅抗氧剂为抗氧剂168、硫代二丙酸二月桂酯(dltp)、硫代二丙酸双十八醇酯(dstp)中的至少一种。
26.进一步地,分散剂为磷酸三(-2-乙基己基)酯、十二烷基硫酸钠、甲基戊醇中的至少一种;所述润滑剂为聚乙烯蜡、氧化聚乙烯蜡、甲基丙烯酸甲酯中的至少一种。
27.与现有技术相比,本发明的有益效果如下:
28.本发明管材由外至里依次包括pp-rct层、阻氧层和防垢层,防垢层材料为添加有防垢母粒的pp-rct,防垢母粒中含有硅氧烷改性纳米二氧化硅,使得管材的内表面粗糙度低至0.01μm,表面接触角达110
°
,极大改善了管材内层的防垢性能,并且本发明管材还具有良好的阻氧性能和耐压性能。
附图说明
29.图1为本发明管材的结构示意图。
具体实施方式
30.为更好地说明本发明的目的、技术方案和优点,下面将结合具体实施例对本发明作进一步说明。本领域技术人员应当理解,此处所描述的具体实施例仅用以解释本发明,并不用于限定本发明。
31.实施例中所用的试验方法如无特殊说明,均为常规方法;所用的材料、试剂等,如无特殊说明,均可从商业途径得到,其中,丙烯基预交联热熔胶购自法国阿科玛公司、美国杜邦公司。
32.实施例1
33.本实施例提供一种阻氧、防垢型pp-rct管材,其结构如图1所示,由外至内依次为pp-rct层1、热熔胶层2、阻氧层3、热熔胶层2、防垢层4。其中,pp-rct层1的制备原料为α晶型pp-rct;热熔胶层2的制备原料为马来酸酐接枝聚丙烯;阻氧层3的制备原料为含38%乙烯的乙烯-乙烯醇共聚物;防垢层4由α晶型pp-rct原料添加2wt%防垢母粒制得。
34.其中,防垢母粒由如下方法制得:
35.s1:将40wt%纳米二氧化硅与60wt%硅氧烷添加于烧瓶中,水浴加热至80℃,搅拌30min,随后向烧瓶中加入1%的磷酸三(-2-乙基己基)酯,继续搅拌20min后,再向烧瓶中加入0.5%的主抗氧剂1010和0.2%的辅抗氧剂168,继续搅拌5min,经冷却制得硅氧烷改性纳米二氧化硅。其中,磷酸三(-2-乙基己基)酯、主抗氧剂1010、辅抗氧剂168的加入量均以纳米二氧化硅和硅氧烷总重量的百分比计。
36.s2:将40wt%由步骤s1制得的硅氧烷改性纳米二氧化硅、3wt%润滑剂和57wt%的pp-rct原料于搅拌机中充分混合15min制得混合料,其中,润滑剂为聚乙烯蜡、氧化聚乙烯蜡或甲基丙烯酸甲酯,将混合料加入双螺杆造粒机中,挤出造粒制得防垢母粒。
37.于210℃下测得防垢母粒的氧化诱导期(oit)为38min。相对于在防垢母粒制备过程中未使用抗氧剂的情形,添加抗氧剂能够防止纳米二氧化硅对pp-rct分子链的破坏,有助于提高防垢母粒的耐老化稳定性。经试验发现,在防垢母粒制备过程中,抗氧剂的添加量达到0.5%时,所制得的防垢母粒已经具有较好的耐老化稳定性,随着抗氧剂添加量的增加,防垢母粒的oit值虽呈增加趋势,但由于抗氧剂的成本较高,故抗氧剂的添加量以0.5%~0.7%较为适宜。
38.将pp-rct层1、热熔胶层2、阻氧层3、热熔胶层2、防垢层4制备原料分别按照图1所示顺序置于挤出机中,经五层共挤模具挤出成型制得阻氧、防垢型pp-rct管材。
39.本发明采用将硅氧烷改性纳米二氧化硅分散于pp-rct材料中制得防垢母粒后,再由防垢母粒与pp-rct材料混合制得防垢层,由于本技术防垢层中硅氧烷改性纳米二氧化硅经过两次pp-rct材料分散,使得防垢层中硅氧烷改性纳米二氧化硅分散的更为均匀,防垢层的防结垢性能均一。
40.经试验发现,若直接将硅氧烷改性纳米二氧化硅分散于pp-rct材料中制备防垢层,硅氧烷改性纳米二氧化硅与pp-rct无法得到充分的物理分散,使得管材的防垢层中硅氧烷改性纳米二氧化硅分散不均匀,防垢层的防结垢性能不均一。
41.由本实施例所述制备原料及方法制得的阻氧、防垢型pp-rct管材通过了20℃、1h的15.0mpa环应力耐压,95℃、22h的4.2mpa环应力耐压,95℃、165h的4.0mpa环应力耐压,95℃、1000h的3.8mpa环应力耐压测试。
42.本实施例阻氧、防垢型管材于80℃透氧率为0.25mg/(m2·
d);管材的内表面粗糙度为0.02μm,表面接触角为108
°
。
43.实施例2
44.本实施例提供一种阻氧、防垢型pp-rct管材,其结构如图1所示,由外至内依次为pp-rct层1、热熔胶层2、阻氧层3、热熔胶层2、防垢层4。其中,pp-rct层1的制备原料为β晶型pp-rct;热熔胶层2的制备原料为丙烯基预交联热熔胶;阻氧层3的制备原料为聚偏二氯乙烯;防垢层4由β晶型pp-rct原料添加5wt%防垢母粒制得。
45.其中,防垢母粒由如下方法制得:
46.s1:将50wt%纳米二氧化硅(5~50nm)与50wt%硅氧烷添加于烧瓶中,水浴加热至100℃,搅拌60min,随后向烧瓶中加入2%的磷酸三(-2-乙基己基)酯,继续搅拌20min后,再向烧瓶中加入0.5%的主抗氧剂1076和0.2%的辅抗氧剂硫代二丙酸二月桂酯(dltp),继续搅拌5min,经冷却制得硅氧烷改性纳米二氧化硅。其中,磷酸三(-2-乙基己基)酯、主抗氧剂、辅抗氧剂的加入量均以纳米二氧化硅和硅氧烷总重量的百分比计。
47.s2:将50wt%由步骤s1制得的硅氧烷改性纳米二氧化硅、2wt%润滑剂和48wt%的pp-rct原料于搅拌机中充分混合15min制得混合料,其中,润滑剂为聚乙烯蜡、氧化聚乙烯蜡或甲基丙烯酸甲酯,将混合料加入双螺杆造粒机中,挤出造粒制得防垢母粒。于210℃下测得防垢母粒的氧化诱导期(oit)为40min。
48.将pp-rct层1、热熔胶层2、阻氧层3、热熔胶层2、防垢层4制备原料按照图1所示顺序分别置于挤出机中,经五层共挤模具挤出成型制得阻氧、防垢型pp-rct管材。
49.由本实施例所述制备原料及方法制得的阻氧、防垢型pp-rct管材通过了20℃、1h的15.0mpa环应力耐压,95℃、22h的4.2mpa环应力耐压,95℃、165h的4.0mpa环应力耐压,95℃、1000h的3.8mpa环应力耐压测试。
50.本实施例阻氧、防垢型管材于80℃透氧率为0.10mg/(m2·
d);管材的内表面粗糙度为0.01μm,表面接触角为119.5
°
。
51.实施例3
52.本实施例提供一种阻氧、防垢型pp-rct管材,其结构如图1所示,由外至内依次为pp-rct层1、热熔胶层2、阻氧层3、热熔胶层2、防垢层4。其中,pp-rct层1的制备原料为α晶型pp-rct;热熔胶层2的制备原料为马来酸酐接枝聚丙烯;阻氧层3的制备原料为含38%乙烯的乙烯-乙烯醇共聚物;防垢层4由α晶型pp-rct原料添加3wt%防垢母粒制得。
53.其中,防垢母粒由如下方法制得:
54.s1:将40wt%纳米二氧化硅与60wt%硅氧烷添加于烧瓶中,水浴加热至80℃,搅拌40min,随后向烧瓶中加入2%的磷酸三(-2-乙基己基)酯,继续搅拌20min后,再向烧瓶中加入0.5%的主抗氧剂1010和0.2%的辅抗氧剂168,继续搅拌5min,经冷却制得硅氧烷改性纳米二氧化硅。其中,磷酸三(-2-乙基己基)酯、主抗氧剂1010、辅抗氧剂168的加入量均以纳米二氧化硅和硅氧烷总重量的百分比计。
55.s2:将40wt%由步骤s1制得的硅氧烷改性纳米二氧化硅、2wt%润滑剂和58wt%的pp-rct原料于搅拌机中充分混合15min制得混合料,其中,润滑剂为聚乙烯蜡、氧化聚乙烯蜡或甲基丙烯酸甲酯,将混合料加入双螺杆造粒机中,挤出造粒制得防垢母粒。
56.于210℃下测得防垢母粒的氧化诱导期(oit)为39min。相对于在防垢母粒制备过
程中未使用抗氧剂的情形,添加抗氧剂能够防止纳米二氧化硅对pp-rct分子链的破坏,有助于提高防垢母粒的耐老化稳定性。经试验发现,在防垢母粒制备过程中,抗氧剂的添加量达到0.5%时,所制得的防垢母粒已经具有较好的耐老化稳定性,随着抗氧剂添加量的增加,防垢母粒的oit值虽呈增加趋势,但由于抗氧剂的成本较高,故抗氧剂的添加量以0.5%~0.7%较为适宜。
57.将pp-rct层1、热熔胶层2、阻氧层3、热熔胶层2、防垢层4制备原料分别按照图1所示顺序置于挤出机中,经五层共挤模具挤出成型制得阻氧、防垢型pp-rct管材。
58.由本实施例所述制备原料及方法制得的阻氧、防垢型pp-rct管材通过了20℃、1h的15.0mpa环应力耐压,95℃、22h的4.2mpa环应力耐压,95℃、165h的4.0mpa环应力耐压,95℃、1000h的3.8mpa环应力耐压测试。
59.本实施例阻氧、防垢型管材于80℃透氧率为0.20mg/(m2·
d);管材的内表面粗糙度为0.015μm,表面接触角为115
°
。
60.实施例4
61.本实施例拟分析防垢层中防垢母粒的添加量对管材性能的影响,具体试验方法如下:
62.以实施例2中所述方法制得的防垢母粒为试验对象,通过向防垢层pp-rct原料中添加不同比例的上述防垢母粒,防垢母粒的添加量如表1所示,并参照实施例2所述方法制备pp-rct管材,分析防垢层pp-rct原料中防垢母粒的添加量对最终pp-rct管材性能的影响,结果如表1所示。
63.由表1可知,防垢层pp-rct原料中防垢母粒的添加量小于5%wt时,随着防垢母粒添加量的增加,pp-rct管材防垢层的内表面粗糙度呈下降趋势,表面接触角呈增加趋势,表明pp-rct管材防垢层的防垢性能随着防垢母粒添加量的增加呈现提升趋势。
64.当防垢层pp-rct原料中防垢母粒的添加量超过5%wt时,pp-rct管材防垢层的表面粗糙度不再减小,接触角不再增大,对管材内表面的防垢性能提升不明显,并且对管材的耐液压起到负面作用,管材未通过95℃、1000h的3.8mpa环应力耐压测试。
65.表1防垢母粒添加量对管材耐液压性能影响
[0066][0067]
对比例1
[0068]
本对比例提供一种阻氧、防垢型pp-rct管材,其结构如图1所示,由外至内依次为pp-rct层1、热熔胶层2、阻氧层3、热熔胶层2、防垢层4。其中,pp-rct层1的制备原料为α晶型pp-rct;热熔胶层2的制备原料为马来酸酐接枝聚丙烯;阻氧层3的制备原料为含38%乙烯
的乙烯-乙烯醇共聚物;防垢层4由α晶型pp-rct原料添加2wt%防垢母粒制得。
[0069]
其中,防垢母粒由如下方法制得:
[0070]
s1:将40wt%微米级二氧化硅与60wt%硅氧烷添加于烧瓶中,水浴加热至80℃,搅拌30min,随后向烧瓶中加入1%的磷酸三(-2-乙基己基)酯,继续搅拌20min后,再向烧瓶中加入0.5%的主抗氧剂1010和0.2%的辅抗氧剂168,继续搅拌5min,经冷却制得硅氧烷改性微米二氧化硅。其中,磷酸三(-2-乙基己基)酯、主抗氧剂1010、辅抗氧剂168的加入量均以二氧化硅和硅氧烷总重量的百分比计。
[0071]
s2:将40wt%由步骤s1制得的硅氧烷改性微米二氧化硅、3wt%润滑剂和57wt%的pp-rct原料于搅拌机中充分混合15min制得混合料,其中,润滑剂为聚乙烯蜡、氧化聚乙烯蜡或甲基丙烯酸甲酯,将混合料加入双螺杆造粒机中,挤出造粒制得防垢母粒。于210℃下测得防垢母粒的氧化诱导期(oit)为38min。
[0072]
将pp-rct层1、热熔胶层2、阻氧层3、热熔胶层2、防垢层4制备原料分别按照图1所示顺序置于挤出机中,经五层共挤模具挤出成型制得阻氧、防垢型pp-rct管材。
[0073]
由本对比例所述制备原料及方法制得的阻氧、防垢型pp-rct管材通过了20℃、1h的15.0mpa环应力耐压,95℃、22h的4.2mpa环应力耐压,95℃、165h的4.0mpa环应力耐压,95℃、1000h的3.8mpa环应力耐压测试。
[0074]
本对比例阻氧、防垢型管材于80℃透氧率为0.25mg/(m2·
d);管材的内表面粗糙度为0.03μm,表面接触角为106
°
。
[0075]
本对比例与实施例1的区别仅在于,本对比例在制备防垢母粒中所用二氧化硅为微米级二氧化硅,而实施例1中所用二氧化硅为纳米二氧化硅。由管材的耐压试验及管材内表面防垢性能结果可知,由微米级二氧化硅或纳米二氧化硅制得的防垢母粒对最终管材的耐压性能影响较小,区别在于管材防垢层防垢性能性能不同,相对于由微米级二氧化硅制得的防垢母粒,由纳米二氧化硅制得的防垢母粒更有利于提升管材内表面的防垢性能。这是由于纳米二氧化硅的比表面积相对较大,能够承载更多硅氧烷,有助于提升防垢层的防污性能。
[0076]
对比例2
[0077]
本对比例提供一种阻氧、防垢型pp-rct管材,其结构如图1所示,由外至内依次为pp-rct层1、热熔胶层2、阻氧层3、热熔胶层2、防垢层4。其中,pp-rct层1的制备原料为α晶型pp-rct;热熔胶层2的制备原料为马来酸酐接枝聚丙烯;阻氧层3的制备原料为含38%乙烯的乙烯-乙烯醇共聚物;防垢层4由α晶型pp-rct原料添加2wt%防垢母粒制得。
[0078]
其中,防垢母粒由如下方法制得:
[0079]
s1:将40wt%钠米二氧化硅与60wt%硅氧烷添加于烧瓶中,水浴加热至80℃,搅拌30min,随后向烧瓶中加入1%的磷酸三(-2-乙基己基)酯,继续搅拌20min后,经冷却制得硅氧烷改性钠米二氧化硅。其中,磷酸三(-2-乙基己基)酯的加入量以二氧化硅和硅氧烷总重量的百分比计。
[0080]
s2:将40wt%由步骤s1制得的硅氧烷改性钠米二氧化硅、3wt%润滑剂和57wt%的pp-rct原料于搅拌机中充分混合15min制得混合料,其中,润滑剂为聚乙烯蜡、氧化聚乙烯蜡或甲基丙烯酸甲酯,将混合料加入双螺杆造粒机中,挤出造粒制得防垢母粒。于210℃下测得防垢母粒的氧化诱导期(oit)为6min。
[0081]
将pp-rct层1、热熔胶层2、阻氧层3、热熔胶层2、防垢层4制备原料分别按照图1所示顺序置于挤出机中,经五层共挤模具挤出成型制得阻氧、防垢型pp-rct管材。
[0082]
由本对比例所述制备原料及方法制得的阻氧、防垢型pp-rct管材通过了20℃、1h的15.0mpa环应力耐压,95℃、22h的4.2mpa环应力耐压,95℃、165h的4.0mpa环应力耐压,95℃、1000h的3.8mpa环应力耐压测试。
[0083]
本对比例阻氧、防垢型管材于80℃透氧率为0.25mg/(m2·
d);管材的内表面粗糙度为0.035μm,表面接触角为105
°
。
[0084]
本对比例与实施例1的区别仅在于,本对比例防垢母粒制备过程中未使用抗氧剂,可见,本对比例所制得的防垢母粒的氧化诱导期显著缩短,表明在防垢母粒制备过程中添加抗氧剂,能够防止纳米二氧化硅对pp-rct分子链的破坏,有助于提高防垢母粒的耐老化稳定性。
[0085]
由管材性能测试结果可知,防垢母粒制备过程中是否使用抗氧剂对最终管材的耐压性能、阻氧性能影响较小,对管材防垢层的防垢性能有一定的影响,防垢母粒制备过程中未使用抗氧剂则会降低防垢层的防垢性能。
[0086]
对比例3
[0087]
本对比例提供一种阻氧、防垢型pp-rct管材,其结构如图1所示,由外至内依次为pp-rct层1、热熔胶层2、阻氧层3、热熔胶层2、防垢层4。其中,pp-rct层1的制备原料为β晶型pp-rct;热熔胶层2的制备原料为丙烯基预交联热熔胶;阻氧层3的制备原料为聚偏二氯乙烯;防垢层4由β晶型pp-rct原料添加5wt%防垢母粒制得。
[0088]
其中,防垢母粒由如下方法制得:
[0089]
s1:将50wt%微米级二氧化硅与50wt%硅氧烷添加于烧瓶中,水浴加热至100℃,搅拌60min,随后向烧瓶中加入2%的磷酸三(-2-乙基己基)酯,继续搅拌20min后,再向烧瓶中加入0.5%的主抗氧剂1076和0.2%的辅抗氧剂硫代二丙酸二月桂酯(dltp),继续搅拌5min,经冷却制得硅氧烷改性纳米二氧化硅。其中,磷酸三(-2-乙基己基)酯、主抗氧剂、辅抗氧剂的加入量均以纳米二氧化硅和硅氧烷总重量的百分比计。
[0090]
s2:将50wt%由步骤s1制得的硅氧烷改性纳米二氧化硅、2wt%润滑剂和48wt%的pp-rct原料于搅拌机中充分混合15min制得混合料,其中,润滑剂为聚乙烯蜡、氧化聚乙烯蜡或甲基丙烯酸甲酯,将混合料加入双螺杆造粒机中,挤出造粒制得防垢母粒。于210℃下测得防垢母粒的氧化诱导期(oit)为35min。
[0091]
将pp-rct层1、热熔胶层2、阻氧层3、热熔胶层2、防垢层4制备原料按照图1所示顺序分别置于挤出机中,经五层共挤模具挤出成型制得阻氧、防垢型pp-rct管材。
[0092]
由本对比例所述制备原料及方法制得的阻氧、防垢型pp-rct管材通过了20℃、1h的15.0mpa环应力耐压,95℃、22h的4.2mpa环应力耐压,95℃、165h的4.0mpa环应力耐压,95℃、1000h的3.8mpa环应力耐压测试。
[0093]
本对比例阻氧、防垢型管材于80℃透氧率为0.15mg/(m2·
d);管材的内表面粗糙度为0.025μm,表面接触角为113.5
°
。
[0094]
本对比例与实施例2的区别仅在于,本对比例在制备防垢母粒中所用二氧化硅为微米级二氧化硅,而实施例2中所用二氧化硅为纳米二氧化硅。由管材的耐压试验及管材内表面防垢性能结果可知,由微米级二氧化硅或纳米二氧化硅制得的防垢母粒对最终管材的
耐压性能影响较小,区别在于管材防垢层防垢性能以及阻氧性能不同,相对于由微米级二氧化硅制得的防垢母粒,由纳米二氧化硅制得的防垢母粒更有利于提升管材内表面的防垢性能及阻氧性能。这是由于纳米二氧化硅的比表面积相对较大,能够承载更多硅氧烷,有助于提升防垢层的防污性能和阻氧性能。
[0095]
对比例4
[0096]
本对比例提供一种阻氧、防垢型pp-rct管材,其结构如图1所示,由外至内依次为pp-rct层1、热熔胶层2、阻氧层3、热熔胶层2、防垢层4。其中,pp-rct层1的制备原料为β晶型pp-rct;热熔胶层2的制备原料为丙烯基预交联热熔胶;阻氧层3的制备原料为聚偏二氯乙烯;防垢层4由β晶型pp-rct原料添加5wt%防垢母粒制得。
[0097]
其中,防垢母粒由如下方法制得:
[0098]
s1:将50wt%纳米二氧化硅与50wt%硅氧烷添加于烧瓶中,水浴加热至100℃,搅拌60min,随后向烧瓶中加入2%的磷酸三(-2-乙基己基)酯,继续搅拌20min后,经冷却制得硅氧烷改性纳米二氧化硅。其中,磷酸三(-2-乙基己基)酯加入量以纳米二氧化硅和硅氧烷总重量的百分比计。
[0099]
s2:将50wt%由步骤s1制得的硅氧烷改性纳米二氧化硅、2wt%润滑剂和48wt%的pp-rct原料于搅拌机中充分混合15min制得混合料,其中,润滑剂为聚乙烯蜡、氧化聚乙烯蜡或甲基丙烯酸甲酯,将混合料加入双螺杆造粒机中,挤出造粒制得防垢母粒,其于210℃下的氧化诱导期(oit值)为5min。
[0100]
将pp-rct层1、热熔胶层2、阻氧层3、热熔胶层2、防垢层4制备原料按照图1所示顺序分别置于挤出机中,经五层共挤模具挤出成型制得阻氧、防垢型pp-rct管材。
[0101]
由本对比例所述制备原料及方法制得的阻氧、防垢型pp-rct管材通过了20℃、1h的15.0mpa环应力耐压,95℃、22h的4.2mpa环应力耐压,95℃、165h的4.0mpa环应力耐压,95℃、1000h的3.8mpa环应力耐压测试。
[0102]
本对比例阻氧、防垢型管材于80℃透氧率为0.10mg/(m2·
d);管材的内表面粗糙度为0.02μm,表面接触角为110
°
。
[0103]
本对比例与实施例2的区别在于,本对比例防垢母粒制备过程中未使用抗氧剂,可见,本对比例所制得的防垢母粒的氧化诱导期显著缩短,表明在防垢母粒制备过程中添加抗氧剂有助于提高防垢母粒的耐老化稳定性。
[0104]
由管材性能测试结果可知,防垢母粒制备过程中是否使用抗氧剂对最终管材的耐压性能、阻氧性能影响较小,对管材防垢层的防垢性能有一定的影响,防垢母粒制备过程中未使用抗氧剂则会降低防垢层的防垢性能。
[0105]
最后所应当说明的是,以上实施例仅用以说明本发明的技术方案而非对本发明保护范围的限制,尽管参照较佳实施例对本发明作了详细说明,本领域的普通技术人员应当理解,可以对本发明的技术方案进行修改或者等同替换,而不脱离本发明技术方案的实质和范围。