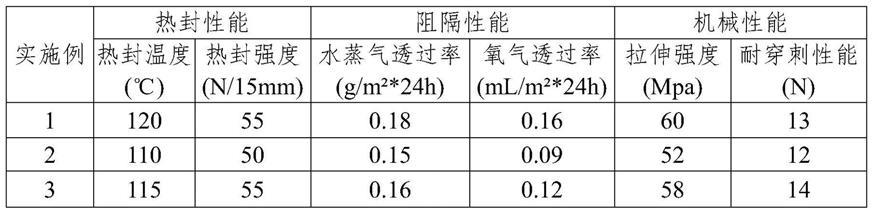
1.本发明涉及食品包装膜技术领域,具体涉及一种可回收高阻隔包装膜及其制备方法。
背景技术:2.包装膜广泛应用于生活的各个领域,如食品、医药、化妆品等,主要用于保护产品,防止产品吸湿受潮、氧化等,从而使产品变质。在不同的领域应用时,对包装膜的要求也是不同的,如医用产品往往要求包装膜抗菌、对水氧阻隔性好,电子产品要求包装膜耐穿刺、防静电,而对于大部分食品包装膜而言,水氧阻隔性则是评价包装膜性能好坏的重要标准,特别是对于一些易受潮和氧化的产品,如饼干、薯片等等。
3.目前市面上主流的高阻隔包装膜中,一般采用铝箔作为水氧阻隔层,包装膜多是堆叠结构为外保护层/胶黏剂/铝箔/胶黏剂/热封层的五层膜,铝箔包装膜的水蒸气透过率可达到0.2g/(m2*24h)以下,氧气透过率可达到0.2cm3/(m2*24h*0.1mpa)以下,水氧阻隔性能优异。然而,随着环保经济的提出,研究学者们发现,铝箔包装膜回收再利用非常困难,主要表现在,第一,铝箔回收困难,第二,包装膜是由不同材质通过胶粘剂固化结合在一起的,分离难度非常大,不同材质固化在一起无法回收利用,没有回收价值,使用后只能丢弃处理,对环境污染较大,第三,胶黏剂中通常会含有一些有害物质,对人类健康和环境都会产生威胁。
4.近年来,用镀铝膜代替铝箔制作的包装膜在食品等领域的应用越来越多,和铝箔相比,镀铝膜中镀铝层的厚度较薄,虽然解决了铝箔难以回收利用的难题,但由于其对水蒸气和氧气的阻隔性能较差,在很多方面的应用仍然受到限制。一些研究学者通过使用聚乙烯作为热封层并对热封层进行改性,虽然从整体上改善了包装膜对水氧的阻隔性能,但由于改性时引入了其他材料,导致改性聚乙烯膜在加工时存在熔点高、吹塑困难等问题,影响了包装膜的制作,从而导致包装膜产品的综合性能下降,产品良品率降低。
技术实现要素:5.本发明的目的在于克服现有技术中存在的缺陷,采用改性聚乙烯层作为热封层,改性聚乙烯层为复合层、中间层和热封内层组成的三层膜结构,复合层包括高密度聚乙烯和茂金属线性低密度聚乙烯,中间层包括低密度聚乙烯、线性低密度聚乙烯和开口爽滑剂,热封内层包括线性低密度聚乙烯、茂金属线性低密度聚乙烯、聚烯烃塑性体、聚烯烃弹性体、低密度聚乙烯和开口爽滑剂。复合层、中间层和热封内层采用独特的配方,不仅可以降低材料的熔点,使得改性聚乙烯膜易加工,聚烯烃塑性体和聚烯烃弹性体的加入可以提高内层膜的热封性能、粘结性能和膜层的耐冲击性能,整个包装膜的水氧阻隔性能也较好,可达到铝箔包装膜的水平。双向拉伸聚丙烯层、阻隔层及热封层之间的复合采用无溶剂复合的方式进行,不仅不会对环境和人体健康产生威胁,各层回收剥离也比较容易,有利于整个产品的回收利用。
6.为了实现上述目的,本发明的技术方案是提供一种可回收高阻隔包装膜,其特征在于,包括从外向内依次设置的双向拉伸聚丙烯层、阻隔层和热封层,所述热封层包括复合层、中间层和热封内层,按质量百分比计,所述复合层包括高密度聚乙烯40~60%和茂金属线性低密度聚乙烯40~60%,所述中间层包括低密度聚乙烯60~70%、线性低密度聚乙烯25~35%和开口爽滑剂1~5%,所述热封内层的组分包括线性低密度聚乙烯30~50%、茂金属线性低密度聚乙烯20~40%、聚烯烃塑性体5~10%、聚烯烃弹性体5~15%、低密度聚乙烯5~10%、开口爽滑剂3~8%。
7.进一步优选的技术方案为,所述阻隔层为镀铝多层共挤双向拉伸聚丙烯膜,按质量百分比计,多层共挤双向拉伸聚丙烯膜的组分包括均聚聚丙烯70~85%、共聚聚丙烯10~20%和乙烯-乙烯醇共聚物3~10%。
8.进一步优选的技术方案为,所述双向拉伸聚丙烯层的外表面设置有印刷图案层,所述双向拉伸聚丙烯层、阻隔层和热封层之间通过粘结剂无溶剂复合粘结,所述粘结剂为双组份聚氨酯粘结剂。
9.进一步优选的技术方案为,所述聚烯烃塑性体的密度为0.89~0.91g/cm3,熔指为3~10g/(10min),维卡软化温度为70~90℃;所述聚烯烃弹性体的密度为0.865~0.88g/cm3,熔指为0.1~5g/(10min),维卡软化温度为30~50℃。
10.进一步优选的技术方案为,所述双向拉伸聚丙烯层的厚度为18~20μm,所述阻隔层的厚度为16~18μm,所述热封层的厚度为40~60μm,在热封层中,所述复合层的厚度为10~20μm,所述中间层的厚度为10~20μm,所述热封内层的厚度为15~30μm。
11.进一步优选的技术方案为,所述阻隔层包括多层共挤双向拉伸聚丙烯膜层、依次沉积的镀铝层和表层氧化铝层,所述镀铝层的厚度为600~1000nm,所述氧化铝的厚度为200~500nm。
12.本发明还提供了一种可回收高阻隔包装膜的制备方法,其特征在于,包括以下步骤:
13.(1)多层共挤双向拉伸聚丙烯膜的制备:分别称取均聚聚丙烯、共聚聚丙烯和乙烯-乙烯醇共聚物,将其分别放入挤出机的三个料筒中挤出成型,并对其进行横向和纵向拉伸,拉伸后在150℃的条件下进行热定型;
14.(2)镀铝膜层的制备:将步骤(1)制备的薄膜放入真空蒸发设备中镀制铝膜,镀膜时先对乙烯-乙烯醇共聚物面进行等离子体处理,再分别镀制铝膜和表层氧化铝膜;
15.(3)热封层的制备:分别称取复合层、中间层和热封内层的材料,将其分别放入吹膜设备的挤出料筒中,挤出后吹塑成型,挤出温度为160~170℃,吹塑时吹胀比为2.5~3.0,牵引比为4~6;
16.(4)无溶剂复合:采用高速无溶剂复合工艺使热封层、阻隔层以及双向拉伸聚丙烯层粘结在一起,复合速度为400~600m/min,复合时预热温度为40~45℃,复合温度为40~45℃,冷却温度为20~25℃;
17.(5)熟化:将复合膜放入熟化设备中进行熟化处理,熟化温度为40℃,熟化时间为36h。
18.进一步优选的技术方案为,在所述多层共挤双向拉伸聚丙烯膜的制备步骤中,横向拉伸时温度为160~165℃,拉伸倍数为5~6倍,纵向拉伸时温度为70~90℃,拉伸倍数为
4~5倍。
19.进一步优选的技术方案为,在所述镀铝膜层的制备步骤中,镀膜时真空度为6*10-4
~1*10-3
pa,镀制氧化铝膜时,通氧量为50~80sccm。
20.进一步优选的技术方案为,在所述无溶剂复合步骤中,复合压力为0.3~0.5mpa,上胶压力为0.4~0.6mpa。
21.本发明为了解决传统铝箔包装膜回收困难的问题,选择镀铝多层共挤双向拉伸聚丙烯膜代替铝箔作为阻隔层,由于镀铝膜直接沉积在聚丙烯膜上,虽然可以解决铝箔难回收的问题,但较薄的镀铝膜对水蒸气和氧气的阻隔性能均较差,远不能达到铝箔的水平。为了进一步提高包装膜的水氧阻隔性能,本发明针对热封层聚乙烯层进行了改性,采用三层结构的聚乙烯作为热封层制作包装膜,热封层的外层选用高密度聚乙烯,中间层选用低密度聚乙烯,内层选用线性低密度聚乙烯。虽然高密度聚乙烯具有优异的耐腐蚀性能和电绝缘性能,表面硬度和拉伸强度都较高,但由于高密度聚乙烯熔点和软化点温度较高,在用挤出吹塑法制作热封层时,高密度聚乙烯与中间层以及内层复合时加工比较困难,造成产品良率较低。
22.为了降低高密度聚乙烯的软化点,同时提高热封层的外层、中间层以及内层在制作时的可加工性能,本发明的技术方案是在外层材料中加入茂金属线性低密度聚乙烯,中间层增加一定比例的线性低密度聚乙烯以及开口爽滑剂,对于内层材料,在加入茂金属线性低密度聚乙烯改善线性低密度聚乙烯的软化点的同时,还需要考虑内层的热封性能,包括热封温度和热封强度。因此,本发明的技术方案中,热封内层组分包括线性低密度聚乙烯、茂金属线性低密度聚乙烯、低密度聚乙烯、聚烯烃塑性体、聚烯烃弹性体以及开口爽滑剂,聚烯烃塑性体的加入不仅可以进一步降低热封内层材料的软化点,使材料易于加工制作,同时也提高了热封内层的热粘性能,而聚烯烃弹性体的加入则增加了热封内层材料的可加工性,使制作的膜层具有较好的机械性能。
23.为了提高镀铝包装膜的水氧阻隔性能,本发明选用的镀铝膜的基底材料为多层共挤双向拉伸聚丙烯膜,该聚丙烯膜由乙烯-乙烯醇共聚物、共聚聚丙烯和均聚聚丙烯组成,镀铝膜制作在乙烯-乙烯醇共聚物面,镀铝膜表面镀有氧化铝膜。共聚聚丙烯和均聚聚丙烯的设置除了用于阻隔水蒸气外,主要起到增强阻隔膜的耐冲击、穿刺等机械性能的作用,乙烯-乙烯醇共聚物作为阻隔层的内层材料,对氧气、二氧化碳等气体具有较好的阻隔作用,在乙烯-乙烯醇共聚物膜的表面镀制镀铝膜可进一步阻止水蒸气和氧气的进入,镀铝膜外层的氧化铝膜的设置主要是为了保护镀铝膜,防止镀铝膜的氧化,并进一步增加阻隔层对水蒸气和氧气的阻隔性能。
24.本发明在制作高阻隔包装膜时,先分别制作阻隔层和热封层,再将印刷有图案的双向拉伸聚丙烯层、阻隔层和热封层通过无溶剂复合的方式粘结在一起。无溶剂复合采用的粘结剂为双组份聚氨酯粘结剂,其中不含任何有机溶剂,不会造成溶剂残留和挥发性溶剂的排放,对环境污染小。另一方面,采用无溶剂复合的方式制作的复合膜,在回收利用时,可很容易的实现层与层之间的分离,各膜层经过分离回收后可重复利用,既有益于环境,也可以节约资源。无溶剂复合采用高速无溶剂复合工艺,复合速度为400~600m/min,在复合过程中,通过控制固化温度、固化时间、张力、复合压力和上胶压力等参数来提高包装膜的整体性能。
25.本发明的优点和有益效果在于:
26.1、采用三层结构的聚乙烯膜作为热封层,复合层、中间层和热封内层采用低软化点的配方方案不仅有利于加工,使得在使用共挤吹塑方法制作聚乙烯膜时三层能更好的的粘结在一起,同时还增加了包装膜产品的低温热封性能、水氧阻隔性。
27.2、阻隔层使用镀铝多层共挤双向拉伸聚丙烯膜,聚丙烯膜从外向内依次为均聚聚丙烯、共聚聚丙烯和乙烯-乙烯醇共聚物,均聚聚丙烯和共聚聚丙烯的存在不仅起到进一步阻止水蒸气的作用,也同时提升了包装膜的耐穿刺、拉伸强度等机械性能,乙烯-乙烯醇共聚物的存在可使得镀铝膜的阻氧性能进一步提高。
28.3、阻隔层中氧化铝膜的存在不仅对镀铝膜起到保护作用,防止镀铝层的氧化,也进一步提升了包装膜的水氧阻隔性能。
29.4、使用高速无溶剂复合工艺将双向拉伸聚丙烯层、阻隔层和热封层通过双组份聚氨酯粘结剂粘结在一起,粘结剂中不含任何有机溶剂,不会造成溶剂残留和挥发性溶剂的排放,对环境污染小。采用无溶剂复合的方式制作的复合膜,在回收利用时,可很容易的实现层与层之间的分离,各膜层经过分离回收后可重复利用,既有益于环境,也节约了资源。
具体实施方式
30.下面结合实施例,对本发明的具体实施方式作进一步描述。以下实施例仅用于更加清楚地说明本发明的技术方案,而不能以此来限制本发明的保护范围。
31.实施例1
32.一种可回收高阻隔包装膜,包括从外向内依次设置的双向拉伸聚丙烯层、阻隔层和热封层,热封层包括复合层、中间层和热封内层,按质量百分比计,复合层包括高密度聚乙烯40%和茂金属线性低密度聚乙烯60%,中间层包括低密度聚乙烯60%、线性低密度聚乙烯35%和开口爽滑剂5%,热封内层的组分包括线性低密度聚乙烯30%、茂金属线性低密度聚乙烯40%、聚烯烃塑性体5%、聚烯烃弹性体10%、低密度聚乙烯10%、开口爽滑剂5%。聚烯烃塑性体的密度为0.89g/cm3,熔指为3g/(10min),维卡软化温度为70℃;聚烯烃弹性体的密度为0.865g/cm3,熔指为0.1g/(10min),维卡软化温度为30℃。阻隔层为镀铝多层共挤双向拉伸聚丙烯膜,按质量百分比计,多层共挤双向拉伸聚丙烯膜的组分包括均聚聚丙烯70%、共聚聚丙烯20%和乙烯-乙烯醇共聚物10%,厚度为1000nm的铝膜镀制在乙烯-乙烯醇共聚物膜上。双向拉伸聚丙烯层的外表面上设置有印刷图案层,双向拉伸聚丙烯层、阻隔层和热封层之间通过双组份聚氨酯粘结剂无溶剂复合粘结。在该包装膜中,双向拉伸聚丙烯层的厚度为18μm,阻隔层的厚度为16μm,热封层中,复合层的厚度为15μm,中间层的厚度为10μm,热封内层的厚度为20μm。
33.一种可回收高阻隔包装膜的制备方法,包括以下步骤:
34.(1)多层共挤双向拉伸聚丙烯膜的制备:按比例称取均聚聚丙烯、共聚聚丙烯和乙烯-乙烯醇共聚物,将其分别放入挤出机的三个料筒中挤出成型,并对其进行横向和纵向拉伸,横向拉伸时温度为160℃,拉伸倍数为5倍,纵向拉伸时温度为70℃,拉伸倍数为4倍,拉伸后在150℃的条件下进行热定型;
35.(2)镀铝膜层的制备:将步骤(1)制备的薄膜放入真空蒸发设备中镀制铝膜,镀膜时先对乙烯-乙烯醇共聚物面进行等离子体处理,再分别镀制铝膜和表层氧化铝膜,镀膜时
真空度为1*10-3
pa,镀制氧化铝膜时,通氧量为80sccm;
36.(3)热封层的制备:分别称取复合层、中间层和热封内层的材料,将其分别放入吹膜设备的挤出料筒中,挤出后吹塑成型,挤出温度为160℃,吹塑时吹胀比为2.5,牵引比为4;
37.(4)无溶剂复合:采用高速无溶剂复合工艺使热封层、阻隔层以及双向拉伸聚丙烯层粘结在一起,复合速度为400m/min,复合时预热温度为40℃,复合温度为40℃,冷却温度为20℃,复合压力为0.3mpa,上胶压力为0.4mpa;
38.(5)熟化:将复合膜放入熟化设备中进行熟化处理,熟化温度为40℃,熟化时间为36h。
39.实施例2
40.一种可回收高阻隔包装膜,包括从外向内依次设置的双向拉伸聚丙烯层、阻隔层和热封层,热封层包括复合层、中间层和热封内层,按质量百分比计,复合层包括高密度聚乙烯50%和茂金属线性低密度聚乙烯50%,中间层包括低密度聚乙烯68%、线性低密度聚乙烯31%和开口爽滑剂1%,热封内层的组分包括线性低密度聚乙烯40%、茂金属线性低密度聚乙烯30%、聚烯烃塑性体10%、聚烯烃弹性体5%、低密度聚乙烯7%、开口爽滑剂8%。聚烯烃塑性体的密度为0.902g/cm3,熔指为7.5g/(10min),维卡软化温度为77.2℃;聚烯烃弹性体的密度为0.87g/cm3,熔指为0.5g/(10min),维卡软化温度为44℃。阻隔层为镀铝多层共挤双向拉伸聚丙烯膜,按质量百分比计,多层共挤双向拉伸聚丙烯膜的组分包括均聚聚丙烯82%、共聚聚丙烯15%和乙烯-乙烯醇共聚物3%,厚度为600nm的铝膜镀制在乙烯-乙烯醇共聚物膜上,铝膜表面镀制有500nm的氧化铝膜。双向拉伸聚丙烯膜的外表面上设置有印刷图案层,双向拉伸聚丙烯层、阻隔层和热封层之间通过双组份聚氨酯粘结剂无溶剂复合粘结。在该包装膜中,双向拉伸聚丙烯层的厚度为20μm,阻隔层的厚度为18μm,热封层中,复合层的厚度为10μm,中间层的厚度为15μm,热封内层的厚度为30μm。
41.一种可回收高阻隔包装膜的制备方法,包括以下步骤:
42.(1)多层共挤双向拉伸聚丙烯膜的制备:按比例称取均聚聚丙烯、共聚聚丙烯和乙烯-乙烯醇共聚物,将其分别放入挤出机的三个料筒中挤出成型,并对其进行横向和纵向拉伸,横向拉伸时温度为165℃,拉伸倍数为6倍,纵向拉伸时温度为90℃,拉伸倍数为5倍,拉伸后在150℃的条件下进行热定型;
43.(2)镀铝膜层的制备:将步骤(1)制备的薄膜放入真空蒸发设备中镀制铝膜,镀膜时先对乙烯-乙烯醇共聚物面进行等离子体处理,再分别镀制铝膜和表层氧化铝膜,镀膜时真空度为6*10-4
pa,镀制氧化铝膜时,通氧量为60sccm;
44.(3)热封层的制备:分别称取复合层、中间层和热封内层的材料,将其分别放入吹膜设备的挤出料筒中,挤出后吹塑成型,挤出温度为165℃,吹塑时吹胀比为3,牵引比为5;
45.(4)无溶剂复合:采用高速无溶剂复合工艺使热封层、阻隔层以及双向拉伸聚丙烯层粘结在一起,复合速度为500m/min,复合时预热温度为40℃,复合温度为40℃,冷却温度为20℃,复合压力为0.4mpa,上胶压力为0.5mpa;
46.(5)熟化:将复合膜放入熟化设备中进行熟化处理,熟化温度为40℃,熟化时间为36h。
47.实施例3
48.一种可回收高阻隔包装膜,包括从外向内依次设置的双向拉伸聚丙烯层、阻隔层和热封层,热封层包括复合层、中间层和热封内层,按质量百分比计,复合层包括高密度聚乙烯60%和茂金属线性低密度聚乙烯40%,中间层包括低密度聚乙烯70%、线性低密度聚乙烯25%和开口爽滑剂5%,热封内层的组分包括线性低密度聚乙烯50%、茂金属线性低密度聚乙烯20%、聚烯烃塑性体7%、聚烯烃弹性体15%、低密度聚乙烯5%、开口爽滑剂3%。聚烯烃塑性体的密度为0.91g/cm3,熔指为10g/(10min),维卡软化温度为90℃;聚烯烃弹性体的密度为0.88g/cm3,熔指为5g/(10min),维卡软化温度为50℃。阻隔层为镀铝多层共挤双向拉伸聚丙烯膜,按质量百分比计,多层共挤双向拉伸聚丙烯膜的组分包括均聚聚丙烯85%、共聚聚丙烯10%和乙烯-乙烯醇共聚物5%,厚度为800nm的铝膜镀制在乙烯-乙烯醇共聚物膜上,铝膜表面镀制有200nm的氧化铝膜。双向拉伸聚丙烯膜的外表面上设置有印刷图案层,双向拉伸聚丙烯层、阻隔层和热封层之间通过双组份聚氨酯粘结剂无溶剂复合粘结。在该包装膜中,双向拉伸聚丙烯层的厚度为18μm,阻隔层的厚度为18μm,热封层中,复合层的厚度为20μm,中间层的厚度为20μm,热封内层的厚度为15μm。
49.一种可回收高阻隔包装膜的制备方法,包括以下步骤:
50.(1)多层共挤双向拉伸聚丙烯膜的制备:按比例称取均聚聚丙烯、共聚聚丙烯和乙烯-乙烯醇共聚物,将其分别放入挤出机的三个料筒中挤出成型,并对其进行横向和纵向拉伸,横向拉伸时温度为165℃,拉伸倍数为6倍,纵向拉伸时温度为90℃,拉伸倍数为5倍,拉伸后在150℃的条件下进行热定型;
51.(2)镀铝膜层的制备:将步骤(1)制备的薄膜放入真空蒸发设备中镀制铝膜,镀膜时先对乙烯-乙烯醇共聚物面进行等离子体处理,再分别镀制铝膜和表层氧化铝膜,镀膜时真空度为8*10-4
pa,镀制氧化铝膜时,通氧量为50sccm;
52.(3)热封层的制备:分别称取复合层、中间层和热封内层的材料,将其分别放入吹膜设备的挤出料筒中,挤出后吹塑成型,挤出温度为170℃,吹塑时吹胀比为3,牵引比为6;
53.(4)无溶剂复合:采用高速无溶剂复合工艺使热封层、阻隔层以及双向拉伸聚丙烯层粘结在一起,复合速度为500m/min,复合时预热温度为45℃,复合温度为45℃,冷却温度为25℃,复合压力为0.5mpa,上胶压力为0.6mpa;
54.(5)熟化:将复合膜放入熟化设备中进行熟化处理,熟化温度为40℃,熟化时间为36h。
55.裁取按照实施例1-3的方法制备的包装膜,并按照国标gb/t1037-1988的方法对其进行水蒸气透过率测试,按照国标gb/t1038-1988的方法对其进行氧气透过率测试,并测试这些包装膜的拉伸强度和穿刺性能,裁取实施例1-3中的包装膜,将其在封压力为200kpa的条件下进行热封,并绘制包装膜的热封强度随热封时间的变化曲线,记录最优的热封温度和热封强度,测试结果见下表。
56.57.从表中数据可以看出,本发明的技术方案制备出的包装膜不仅具有较优异的水氧阻隔性,热封性能也大大提高,同时具有较好的机械性能。
58.以上所述仅是本发明的优选实施方式,应当指出,对于本技术领域的普通技术人员来说,在不脱离本发明技术原理的前提下,还可以做出若干改进和润饰,这些改进和润饰也应视为本发明的保护范围。