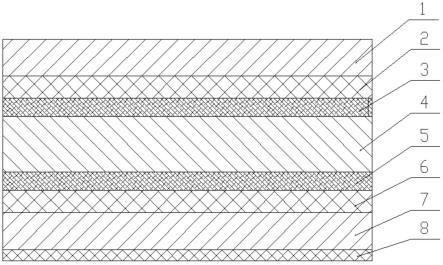
1.本实用新型属于锂电池外包装材料技术领域,具体为一种锂电池用耐压复合膜。
背景技术:2.当前锂电池的外包型式主要分为软包、方形、圆柱三个体系,其中,软包锂电池所用代表性外包材料是铝塑复合膜,方形锂电池外包材料通常采用铝壳,圆柱锂电池外包材料通常采用钢壳。铝壳、钢壳都是具有较强的内部抗压力优点,在内部产气增压时具有稳定、形状不变形等特点,但铝壳、钢壳由于采用全密封工艺,在出现安全事故如内短路等情况下,气压不易排出,容易引发爆炸,增大了安全隐患。而软包所用铝塑复合膜因其重量轻、能量密度高等优势而得到广泛应用,同时,软包锂电池的机械强度不高,在出现安全事故如内短路等情况下,软包电池最多只会鼓气裂开,降低了爆炸风险。
3.但铝塑复合膜也具有如下缺陷:
4.1、铝塑复合膜较软,在包装成电池后,充放电产生的气体容易使电池鼓包变形,对电池模组内部产生一定的相互挤压变形,影响电池安全。
5.2、在软包电池的冲壳过程中,如图3和图4所示,在拉伸位置会存在局部拉伸过度现象,造成局部残留厚度降低,导致拉伸严重位置易塌陷,稍微触碰会有变形,使电池局部存在弱点,可能成为电池安全隐患的突破点。
技术实现要素:6.本实用新型在于提供一种锂电池用耐压复合膜,以克服背景技术中所述缺陷,使耐压复合膜具备耐压不变形及冲壳过程中不会造成拉伸过度的冲壳特点,使软包锂电池抗内外压性能更稳定,电池使用更安全。
7.为实现上述目的,本实用新型提供如下技术方案:
8.一种锂电池用耐压复合膜,包括由上至下依次排列的保护层、第一粘接层、第一耐腐蚀涂层、耐压层、第二耐腐蚀涂层、第二粘接层、热封层、爽滑剂层,所述保护层、第一粘接层、第一耐腐蚀涂层、耐压层、第二耐腐蚀涂层、第二粘接层、热封层通过干式复合或高温热压成型为整体复合膜结构,所述爽滑剂层涂布于热封层下表面,所述耐压层厚度为10-150μm,所述耐压层材质为铜箔、铝箔、钢箔中的一种。
9.进一步的,所述保护层厚度为10-60μm,所述保护层材质为尼龙薄膜、聚酯薄膜、尼龙薄膜与聚酯薄膜的共挤膜、尼龙薄膜与聚酯薄膜的胶粘复合膜中的一种。
10.进一步的,所述第一粘接层和第二粘接层的厚度均为2-10μm,所述第一粘接层和第二粘接层的材质为聚氨酯树脂、聚烯烃树脂中的一种。
11.进一步的,所述热封层厚度为20-120μm,所述热封层材质为聚丙烯薄膜。
12.进一步的,所述爽滑剂层厚度为10-50nm,所述爽滑剂层材质为芥酸酰胺、油酸酰胺中的一种。
13.制备步骤如下:
14.(1)发送耐压层材料,在耐压层上下两面分别涂布第一耐腐蚀涂层和第二耐腐蚀涂层,然后在第二耐腐蚀涂层上涂布第二粘接层材料,烘干后与热封层材料热压贴合,得到半成品a;
15.(2)发送步骤(1)中得到的半成品a,在第一耐腐蚀涂层上涂布第一粘接层材料,烘干后与保护层材料热压贴合,得到半成品b;
16.(3)将步骤(2)中得到的半成品b放入烘箱熟化,熟化温度30-60℃,熟化时间6-8天,熟化后取出得到半成品c;
17.(4)将爽滑剂层材料涂布于步骤(3)中得到的半成品c的热封层下表面,且控制爽滑剂层摩擦系数在0.3以下,即得锂电池用耐压复合膜。
18.与现有技术相比,本实用新型的有益效果是:
19.通过耐压层采用硬度较高的金属箔,将软包电池用复合膜的硬度提高,进而提高电池的耐压能力,同时在热封层表面涂布爽滑剂,以提高冲壳性能,使复合膜同时兼具良好的冲壳性能、耐压性能等优点,不仅解决了现有技术中冲壳的塌陷问题,也解决了锂电池在使用过程中的胀气鼓包变形问题,主要提高了电池的安全性能,进一步对新能源行业的安全提供一种方案。
附图说明
20.图1为本实用新型耐压复合膜结构示意图;
21.图2为现有技术软包锂电池所用铝塑复合膜结构示意图;
22.图3为软包电池冲壳拉伸后的俯视图;
23.图4为软包电池冲壳拉伸后的界面图;
24.附图中的标记为:1-保护层,2-第一粘接层,3-第一耐腐蚀涂层,4-耐压层,5-第二耐腐蚀涂层,6-第二粘接层,7-热封层,8-爽滑剂层,9-第一钝化层,10-第二钝化层,11-拉伸位置,12-未拉伸位置。
具体实施方式
25.为了使本实用新型所解决的技术问题、技术方案及有益效果更加清楚明白,以下结合实施例,对本实用新型进行进一步详细说明。应当理解,此处所描述的具体实施例仅仅用以解释本实用新型,并不用于限定本实用新型。
26.实施例1:
27.一种锂电池用耐压复合膜:
28.请参阅图1,一种锂电池用耐压复合膜,包括由上至下依次排列的保护层1、第一粘接层2、第一耐腐蚀涂层3、耐压层4、第二耐腐蚀涂层5、第二粘接层6、热封层7、爽滑剂层8,保护层1、第一粘接层2、第一耐腐蚀涂层3、耐压层4、第二耐腐蚀涂层5、第二粘接层6、热封层7通过干式复合或高温热压成型为整体复合膜结构,爽滑剂层8涂布于热封层7下表面。
29.其中,保护层1厚度为10-60μm,本实施例中保护层1厚度为25μm,保护层1材质为尼龙薄膜、聚酯薄膜、尼龙薄膜与聚酯薄膜的共挤膜、尼龙薄膜与聚酯薄膜的胶粘复合膜中的一种,本实施例选用尼龙薄膜与聚酯薄膜的胶粘复合膜。
30.其中,第一粘接层2和第二粘接层6的厚度均为2-10μm,本实施例中第一粘接层2和
第二粘接层6的厚度均为5μm,第一粘接层2和第二粘接层6的材质为聚氨酯树脂、聚烯烃树脂中的一种,本实施例选用聚氨酯树脂。
31.其中,耐压层4厚度为10-150μm,本实施例中耐压层4厚度为40μm,耐压层4材质为铜箔、铝箔、钢箔中的一种,本实施例选用压延铝箔。
32.其中,热封层7厚度为20-120μm,本实施例中热封层7厚度为80μm,热封层7材质为聚丙烯薄膜。
33.其中,爽滑剂层8厚度为10-50nm,本实施例中爽滑剂层8厚度为20nm,爽滑剂层8材质为芥酸酰胺、油酸酰胺中的一种,本实施例选用芥酸酰胺。
34.制备步骤如下:
35.(1)发送耐压层材料1材料压延铝箔,在压延铝箔上下两面分别涂布第一耐腐蚀涂层3和第二耐腐蚀涂层5,然后在第二耐腐蚀涂层5上涂布第二粘接层6材料聚氨酯树脂,烘干后与热封层7材料聚丙烯薄膜热压贴合,得到半成品a;
36.(2)发送步骤(1)中得到的半成品a,在第一耐腐蚀涂层3上涂布第一粘接层2材料聚氨酯树脂,烘干后与保护层1材料(尼龙薄膜与聚酯薄膜的胶粘复合膜)热压贴合,得到半成品b;
37.(3)将步骤(2)中得到的半成品b放入烘箱熟化,熟化温度30-60℃,本实施例采用40℃,熟化时间6-8天,本实施例采用7天,熟化后取出得到半成品c;
38.(4)将爽滑剂层8材料芥酸酰胺涂布于步骤(3)中得到的半成品c的热封层7下表面,且控制爽滑剂层8摩擦系数在0.3以下,即得锂电池用耐压复合膜。
39.经测试,本实施例制备的锂电池用耐压复合膜,冲壳破损时深度为7.9mm;冲壳5mm后,按压顶角(图3和图4中拉伸位置11),出现塌陷现象;充气1.0kgf情况下,电池臌胀严重。
40.实施例2:
41.本实施例与实施例1基本相同,不同之处在于耐压层4材料选用压延铜箔。
42.经测试,本实施例制备的锂电池用耐压复合膜,冲壳破损时深度为8.2mm;冲壳5mm后,按压顶角(图3和图4中拉伸位置11),出现塌陷现象;充气1.0kgf情况下,电池臌胀严重。
43.实施例3:
44.本实施例与实施例1基本相同,不同之处在于耐压层4材料选用压延不锈钢箔。
45.经测试,本实施例制备的锂电池用耐压复合膜,冲壳破损时深度为5.1mm;冲壳5mm后,按压顶角(图3和图4中拉伸位置11),没有出现塌陷现象;充气1.0kgf情况下,电池有轻微臌胀;充气1.5kgf情况下,电池臌胀严重。
46.实施例4:
47.本实施例与实施例3基本相同,不同之处在于耐压层4厚度为60μm。
48.经测试,本实施例制备的锂电池用耐压复合膜,冲壳破损时深度为7.5mm;冲壳5mm后,按压顶角(图3和图4中拉伸位置11),没有出现塌陷现象;充气1.5kgf情况下,电池有轻微臌胀。
49.实施例5:
50.本实施例与实施例3基本相同,不同之处在于耐压层4厚度为80μm。
51.经测试,本实施例制备的锂电池用耐压复合膜,冲壳破损时深度为7.2mm;冲壳5mm后,按压顶角(图3和图4中拉伸位置11),没有出现塌陷现象;充气1.5kgf情况下,电池有轻
微臌胀。
52.实施例6:
53.本实施例与实施例3基本相同,不同之处在于耐压层4厚度为100μm。
54.经测试,本实施例制备的锂电池用耐压复合膜,冲壳破损时深度为6.5mm;冲壳5mm后,按压顶角(图3和图4中拉伸位置11),没有出现塌陷现象;充气1.5kgf情况下,电池无臌胀。
55.实施例7:
56.本实施例与实施例3基本相同,不同之处在于熟化后不进行爽滑剂层8的涂布处理。
57.经测试,本实施例制备的锂电池用耐压复合膜,冲壳破损时深度为3.2mm;冲壳5mm后,按压顶角(图3和图4中拉伸位置11),没有出现塌陷现象;充气1.0kgf情况下,电池有轻微臌胀。
58.对比例:
59.现有技术铝塑复合膜:
60.如图2所示,铝塑复合膜包括由上至下依次排列的保护层1、第一粘接层2、第一钝化层9、耐压层4、第二钝化层10、第二粘接层6、热封层7。
61.其中,保护层1厚度为25μm,保护层1材质为尼龙薄膜与聚酯薄膜的胶粘复合膜。
62.其中,第一粘接层2和第二粘接层6的厚度均为5μm,第一粘接层2和第二粘接层6的材质均为聚氨酯树脂。
63.其中,耐压层4厚度为40μm,耐压层4材质为压延铝箔。
64.其中,热封层7厚度为80μm,热封层7材质为聚丙烯薄膜。
65.制备步骤如下:
66.(1)在压延铝箔上下两面做钝化处理,形成第一钝化层9和第二钝化层10,在第二钝化层10上涂布第二粘接层6材料聚氨酯树脂,通过干式复合工艺与热封层7材料聚丙烯薄膜热压贴合,得到半成品d;
67.(2)发送步骤(1)中得到的半成品d,在第一钝化层9涂布第一粘接层2材料聚氨酯树脂,通过干式复合工艺与保护层1材料(尼龙薄膜与聚酯薄膜的胶粘复合膜)热压贴合,得到半成品e;
68.(3)将步骤(2)中得到的半成品e放入烘箱熟化,熟化温度40℃,熟化时间7天,熟化后即得铝塑复合膜。
69.经测试,本例制备的铝塑复合膜,冲壳破损时深度为6.0mm;冲壳5mm后,按压顶角(图3和图4中拉伸位置11),出现塌陷现象;充气1.0kgf情况下,电池臌胀严重。
70.耐压层不同材质的耐压形变对比见表1:
[0071][0072]
表1:耐压层不同材质的耐压形变情况
[0073]
如表1所示,铜箔冲壳性能最优,冲壳破损时深度达8.2mm,不锈钢箔冲壳性能较弱,只有5.1mm,但不锈钢箔冲壳塌陷和耐压变形具有显著优势。同时,对比例和实施例1均采用铝箔,但由于对比例没有涂布爽滑剂层,实施例1涂布有爽滑剂层,实施例1的冲壳性能优于对比例,故可得出爽滑剂可提高冲壳性能。
[0074]
耐压层采用不锈钢箔时不同厚度的耐压形变对比见表2:
[0075][0076][0077]
表2:不锈钢箔耐压层不同厚度的耐压形变情况
[0078]
如表2所示,在采用不锈钢箔冲壳情况下,冲壳深度随着不锈钢箔厚度增加呈现先上升再下降趋势,其中在60um最优,不仅兼顾冲壳深度,也具有良好的耐压变形优点。
[0079]
爽滑剂对冲壳影响对比见表3:
[0080][0081]
表3:爽滑剂对冲壳影响对比
[0082]
如表3所示,进一步可得出爽滑剂可提高冲壳性能。
[0083]
综上,同等条件下,耐压层采用不同材料时的耐压性能,不锈钢箔优于铜箔和铝箔,冲壳性能则是铜箔优于铝箔,铝箔优于不锈钢箔,但不锈钢箔厚度达到某一值时,不锈钢箔的冲壳性能得到显著提高,另外,增加爽滑剂层也可提高冲壳性能。实施例4(耐压层采用60μm不锈钢箔且涂布爽滑剂)可同时兼具良好的冲壳性能、耐压变形等优点,是为较理想方案。
[0084]
尽管已经示出和描述了本实用新型的实施例,对于本领域的普通技术人员而言,可以理解在不脱离本实用新型的原理和精神的情况下可以对这些实施例进行多种变化、修改、替换和变型,本实用新型的范围由所附权利要求及其等同物限定。