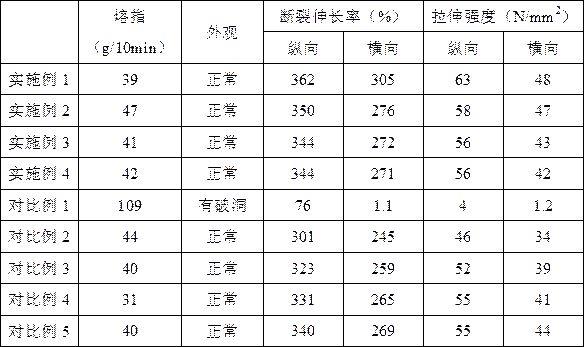
一种基于回收料的三层结构tpx离型膜及其制备方法
技术领域
1.本发明涉及tpx离型膜技术领域,尤其涉及一种基于回收料的三层结构tpx离型膜及其制备方法。
背景技术:2.柔性电路板又称“软板”,即fpc,是用柔性的绝缘基材制成的印刷电路,它能提供优良的电性能,满足更小型和更高密度安装的设计需要,同时也有助于减少组装工序和增强可靠性,并能大大缩小电子产品的体积和重量,在电子产品向高密度、小型化、高可靠方向发展的进程中具有重要意义。
3.在fpc的制备中,为防止金属线路被空气、水汽等物质氧化腐蚀,影响其电气性能,通常需要在印刷电路的一面覆盖一层保护膜。保护膜通过热压合粘结在印刷电路表面上,如果直接进行压合,覆盖的保护膜很容易粘接在加热板表面。因此,保护膜表面需要覆盖离型膜,一方面可以避免保护膜的粘结,另一方面能够减少压合过程中缺陷的产生,例如阻胶、褶皱。
4.生产fpc用离型膜最常见也是最关键的原料是tpx(聚-4-甲基-1-戊烯),但tpx粒子价格一直居高不下,造成tpx离型膜的生产成本较高。并且,tpx离型膜的生产过程中会产生回边料、有瑕疵的产品,这些都是含有大量的tpx原料,如果不加以利用,将是一种很大的浪费;同时,tpx离型膜作为fpc压合过程中的一道工序,仅仅是一个消耗品,相当于一次性的,用完一次便会被处理掉,如果不能被回收利用,同样也会造成tpx粒子的浪费。
5.专利cn110948975a公开了一种离型膜及其制备方法,该离型膜包括依次设置的上层、中间层和下层,其中,中间层包括多个纳米粒子、tpx原料、tpx回收料。该专利中对tpx回收料进行了再次利用,能在一定程度上降低离型膜的生产成本,但其制得的离型膜力学性能较差,纵向拉伸强度仅为20~33mpa,在压合过程中易发生破损。
技术实现要素:6.为了解决现有技术中基于回收料的tpc离型膜力学性能差的技术问题,本发明提供了一种基于回收料的三层结构tpx离型膜及其制备方法。本发明通过在tpx回收料中添加改性碳酸钙粉末、改性增韧剂和聚丙烯,能在实现tpx回收料再次利用的同时,使tpx离型膜具有较好的力学性能。
7.本发明的具体技术方案为:第一,本发明提供了一种基于回收料的三层结构tpx离型膜,包括上层、中间层和下层,所述上层和下层均为纯tpx层,所述中间层为回收料层;所述回收料层的原料按重量份计,包括以下组分:tpx回收料100份,改性碳酸钙粉末1~2份,改性增韧剂6~13份,聚丙烯9~20份,抗氧剂0~1份;所述改性碳酸钙粉末为表面接枝有多个马来酰亚胺基团的碳酸钙粉末;所述改性增韧剂为经糠醇接枝改性的马来酸酐接枝乙烯-丙烯酸丁酯共聚物。
8.相较于纯tpx而言,tpx回收料的熔融指数(熔指)明显增大,会造成在挤出流延的
过程中,中间层的流速明显快于表层,导致表层与中间层挤出不均匀,进而造成tpx离型膜的力学性能不佳。为此,本发明在中间层添加了一定量的改性碳酸钙粉末、改性增韧剂和聚丙烯,能够有效降低中间层的熔指,赋予tpx离型膜较好的力学性能。
9.并且,本发明通过对碳酸钙粉末和增韧剂进行改性,有利于提高tpx离型膜的力学性能,具体机制如下:马来酸酐接枝乙烯-丙烯酸丁酯共聚物(eba-g-mah)是一种通过马来酸酐改性的乙烯-丙烯酸丁酯共聚物,其主链中含有酸酐基团,在现有技术中常作为增韧剂、相容剂使用。本发明将糠醇接枝到eba-g-mah上(可利用酸酐与羟基之间的酯化反应实现接枝),在eba-g-mah的侧链引入了呋喃基团。在较低温度下,呋喃基团与马来酰亚胺基团能够发生diels-alder反应,形成da键;当温度升高时,da键断裂,恢复呋喃基团和马来酰亚胺基团,当温度下降后,da键又能重新形成。因此,在对中间层的原料进行熔融共混时,在熔融所需的高温下,改性碳酸钙表面的马来酰亚胺基团与改性增韧剂侧链上的呋喃基团之间不形成da键,故乙烯-丙烯酸丁酯共聚物(eba)易分散到熔融的tpx回收料中,形成均匀的互穿网络,从而较好地发挥增韧作用;在tpx离型膜冷却定型的过程中,温度下降,马来酰亚胺基团与呋喃基团之间形成da键,从而使eba以碳酸钙粉末为交联点,形成共价交联网络,有利于提高tpx离型膜的力学性能。
10.本发明采用将马来酰亚胺基团接枝在碳酸钙粉末上的方式,在中间层中引入马来酰亚胺基团,具有以下优点:一方面,一个碳酸钙颗粒表面能够接枝上多个马来酰亚胺基团,以其作为eba的交联点,能够在更大程度上提高tpx离型膜的力学性能;另一方面,在tpx离型膜中,利用改性碳酸钙与改性增韧剂之间形成的da键,能提高碳酸钙与聚合物基体的结合强度,同样有利于提高tpx离型膜的力学性能。
11.此外,由于da键在温度控制下的成键和断键具有可逆性,因此,本发明的tpx离型膜在使用后回收再次制成tpx离型膜时,da键能够在中间层熔融共混时再次断开,并在tpx离型膜冷却定型时再次形成,故改性碳酸钙粉末和改性增韧剂能重复发挥作用,无需再额外加入新的改性碳酸钙粉末和改性增韧剂,能在确保tpx离型膜的高力学性能的同时,尽可能减小成本。
12.作为优选,所述改性碳酸钙粉末的制备方法包括以下步骤:(1)在惰性气体保护下,将马来酸酐和氨基硅烷偶联剂溶解到有机溶剂中,在20~30℃下反应1~2h后,加入氯化锌,并加入六甲基二硅氮烷溶液,在60~90℃下反应4~5h,分离出产物,获得马来酰亚胺基硅烷偶联剂;步骤(1)中,经过开环成酸和脱水环化后,马来酸酐接枝到氨基硅烷偶联剂中的氨基上,形成马来酰亚胺基团。
13.(2)将碳酸钙粉末分散到反应溶剂中,升温至30~40℃后,边搅拌边向其中滴加马来酰亚胺基硅烷偶联剂,滴加完成后,继续在30~40℃下反应1.5~4h,分离出产物,获得改性碳酸钙粉末;步骤(2)中,马来酰亚胺基硅烷偶联剂中的硅烷氧基(-sior)与碳酸钙粉末表面的羟基发生脱水缩合反应,使马来酰亚胺基团接枝到碳酸钙粉末上。
14.进一步地,步骤(1)中,所述马来酸酐和氨基硅烷偶联剂的摩尔比为1:0.6~1.0。
15.进一步地,步骤(2)中,所述碳酸钙粉末、马来酰亚胺基硅烷偶联剂和反应溶剂的质量比为1:0.2~0.5:10~15。
16.作为优选,所述改性增韧剂的制备方法包括以下步骤:将马来酸酐接枝乙烯-丙烯酸丁酯共聚物和糠醇加入密闭容器中,在惰性气体保护下,混合加热至190~200℃,搅拌反应20~30min后,冷却,获得改性增韧剂。
17.eba-g-mah中含有酸酐,能在熔融下,与糠醇中的羟基发生酯化反应,从而使糠醇中的呋喃基团接枝到eba-g-mah分子链上。
18.进一步地,所述马来酸酐接枝乙烯-丙烯酸丁酯共聚物和糠醇的质量比为1:0.15~0.35。
19.作为优选,所述tpx回收料包括tpx离型膜生产中的在线回边料、有瑕疵tpx离型膜产品和已使用过的tpx离型膜中的一种或多种。
20.作为优选,所述三层结构tpx离型膜的总厚度为110~130μm,纯tpx层和回收料层的厚度比为1~5:2~7。
21.作为优选,所述聚丙烯的熔融指数为10~14g/10min。
22.作为优选,所述抗氧剂为受阻酚类抗氧剂和亚磷酸酯类抗氧剂的复配抗氧剂。
23.第二,本发明提供了所述三层结构tpx离型膜的制备方法,包括以下步骤:s1:将回收料层的所有原料混匀后,进行熔融挤出和切粒,获得中间层造粒料;s2:采用纯tpx粒子和中间层造粒料,进行三层共挤和流延后,获得三层结构tpx离型膜。
24.作为优选,步骤s1中,所述熔融挤出采用双螺杆挤出机进行,温度为210~270℃,主机转速为40~100rpm,喂料机转速1.5~3rpm。
25.作为优选,步骤s2中,所述三层共挤的过程中,将纯tpx粒子和中间层造粒料分别置于主机a和主机b中;主机a和主机b的转速分别为12~20rpm和28~40rpm,温度为240~300℃;模头温度为270~290℃。
26.与现有技术相比,本发明具有以下优点:(1)通过在tpx回收料中加入一定量的改性碳酸钙粉末、改性增韧剂和聚丙烯,能在实现tpx回收料再次利用的同时,有效降低中间层的熔指,提高tpx离型膜的力学性能;(2)采用接枝有马来酰亚胺基团的改性碳酸钙粉末和接枝有呋喃基团的改性增韧剂,能在中间层原料熔融共混时,确保原料混合均匀,并在tpx离型膜冷却定型后,提高中间层的交联程度,因而能赋予tpx离型膜较好的力学性能;(3)采用将马来酰亚胺基团接枝在碳酸钙粉末上的方式,在中间层中引入马来酰亚胺基团,有利于提高tpx离型膜的力学性能。
具体实施方式
27.下面结合实施例对本发明作进一步的描述。
28.总实施例一种基于回收料的三层结构tpx离型膜,包括上层、中间层和下层,所述上层和下层均为纯tpx层,所述中间层为回收料层。所述三层结构tpx离型膜的总厚度为110~130μm,纯tpx层和回收料层的厚度比为1~5:2~7。
29.所述回收料层的原料按重量份计,包括以下组分:tpx回收料100份,改性碳酸钙粉末1~2份,改性增韧剂6~13份,聚丙烯(熔指为10~14g/10min)9~20份,抗氧剂0~1份。所述tpx
回收料包括tpx离型膜生产中的在线回边料、有瑕疵tpx离型膜产品和已使用过的tpx离型膜中的一种或多种。所述抗氧剂为受阻酚类抗氧剂和亚磷酸酯类抗氧剂的复配抗氧剂。
30.所述改性碳酸钙粉末的制备方法包括以下步骤:(1)在惰性气体保护下,将摩尔比为1:0.6~1.0的马来酸酐和氨基硅烷偶联剂溶解到有机溶剂中,在20~30℃下反应1~2h后,加入氯化锌,并加入六甲基二硅氮烷溶液,在60~90℃下反应4~5h,分离出产物,获得马来酰亚胺基硅烷偶联剂;(2)将碳酸钙粉末分散到反应溶剂中,升温至30~40℃后,边搅拌边向其中滴加马来酰亚胺基硅烷偶联剂,所述碳酸钙粉末、马来酰亚胺基硅烷偶联剂和反应溶剂的质量比为1:0.2~0.5:10~15,滴加完成后,继续在30~40℃下反应1.5~4h,分离出产物,获得改性碳酸钙粉末。
31.所述改性增韧剂的制备方法包括以下步骤:将质量比为1:0.15~0.35的马来酸酐接枝乙烯-丙烯酸丁酯共聚物和糠醇加入密闭容器中,在惰性气体保护下,混合加热至190~200℃,搅拌反应20~30min后,冷却,获得改性增韧剂。
32.上述三层结构tpx离型膜的制备方法,包括以下步骤:s1:将回收料层的所有原料混匀后,采用双螺杆挤出机进行熔融挤出,温度为210~270℃,主机转速为40~100rpm,喂料机转速1.5~3rpm;对获得的料条进行切粒,获得中间层造粒料;s2:将纯tpx粒子和中间层造粒料分别置于主机a和主机b中,控制主机a和主机b的转速分别为12~20rpm和28~40rpm,温度为240~300℃,模头温度为270~290℃,进行三层共挤和流延,获得三层结构tpx离型膜。
33.实施例1通过以下步骤,制备一种三层结构tpx离型膜:s1:制备改性碳酸钙粉末:s1.1:在氮气保护下,按照1:1.85:20的质量比,将马来酸酐和硅烷偶联剂kh-550溶解到甲苯中,在25℃下搅拌反应1h后,加入质量分别为马来酸酐1倍的氯化锌和10倍的20wt%六甲基二硅氮烷溶液(溶剂为甲苯),在70℃下反应5h,过滤,旋蒸去除甲苯,获得马来酰亚胺基硅烷偶联剂;s1.2:按照1:10的质量比,将碳酸钙粉末分散到无水乙醇中,升温至40℃后,边搅拌边向其中滴加质量为碳酸钙粉末0.3倍的马来酰亚胺基硅烷偶联剂,滴加完成后,继续在40℃下反应2.5h,离心,水洗,烘干,获得改性碳酸钙粉末。
34.s2:制备改性增韧剂:向密闭反应釜中加入质量比为1:0.25的马来酸酐接枝乙烯-丙烯酸丁酯共聚物和糠醇,将釜内空气置换成氮气,升温至190℃,搅拌反应20min后,冷却,获得改性增韧剂。
35.s3:制备中间层造粒料:s3.1:按照重量份称取以下原料:tpx回收料(由tpx离型膜生产中的在线回边料、有瑕疵tpx离型膜产品和已使用过的tpx离型膜组成)100份,改性碳酸钙粉末1.3份,改性增韧剂11.5份,聚丙烯(熔指为10g/10min)20份,2,6-二叔丁基-4-甲基苯酚0.6份,亚磷酸三(2,4-二叔丁基苯基)酯0.17份;s3.2:将所有原料混匀后,采用双螺杆挤出机进行熔融挤出,温度为250℃,主机转
速为60rpm,喂料机转速2.5rpm,得到料条;将料条牵引至切粒机中,进行切粒,获得中间层造粒料。
36.s4:制膜:将纯tpx粒子和中间层造粒料分别置于主机a和主机b中,控制主机a和主机b的转速分别为17rpm和36rpm,温度为260℃,模头温度为280℃,进行三层共挤和流延,获得三层结构tpx离型膜。
37.本实施例制得的三层结构tpx离型膜中,上层和下层均为纯tpx层,厚度均为30μm;中间层为回收料层,厚度为60μm。
38.实施例2通过以下步骤,制备一种三层结构tpx离型膜:s1:制备改性碳酸钙粉末:s1.1:在氮气保护下,按照1:2.2:20的质量比,将马来酸酐和硅烷偶联剂kh-550溶解到甲苯中,在20℃下搅拌反应2h后,加入质量分别为马来酸酐1.5倍的氯化锌和12.5倍的20wt%六甲基二硅氮烷溶液(溶剂为甲苯),在60℃下反应5h,过滤,旋蒸去除甲苯,获得马来酰亚胺基硅烷偶联剂;s1.2:按照1:10的质量比,将碳酸钙粉末分散到无水乙醇中,升温至30℃后,边搅拌边向其中滴加质量为碳酸钙粉末0.5倍的马来酰亚胺基硅烷偶联剂,滴加完成后,继续在30℃下反应4h,离心,水洗,烘干,获得改性碳酸钙粉末。
39.s2:制备改性增韧剂:向密闭反应釜中加入质量比为1:0.15的马来酸酐接枝乙烯-丙烯酸丁酯共聚物和糠醇,将釜内空气置换成氮气,升温至200℃,搅拌反应20min后,冷却,获得改性增韧剂。
40.s3:制备中间层造粒料:s3.1:按照重量份称取以下原料:tpx回收料(由tpx离型膜生产中的在线回边料、有瑕疵tpx离型膜产品和已使用过的tpx离型膜组成)100份,改性碳酸钙粉末1份,改性增韧剂13份,聚丙烯(熔指为10g/10min)9份,2,6-二叔丁基-4-甲基苯酚0.7份,亚磷酸三(2,4-二叔丁基苯基)酯0.3份;s3.2:将所有原料混匀后,采用双螺杆挤出机进行熔融挤出,温度为250℃,主机转速为60rpm,喂料机转速2.5rpm,得到料条;将料条牵引至切粒机中,进行切粒,获得中间层造粒料。
41.s4:制膜:将纯tpx粒子和中间层造粒料分别置于主机a和主机b中,控制主机a和主机b的转速分别为17rpm和36rpm,温度为260℃,模头温度为280℃,进行三层共挤和流延,获得三层结构tpx离型膜。
42.本实施例制得的三层结构tpx离型膜中,上层和下层均为纯tpx层,厚度均为30μm;中间层为回收料层,厚度为60μm。
43.实施例3通过以下步骤,制备一种三层结构tpx离型膜:s1:制备改性碳酸钙粉末:s1.1:在氮气保护下,按照1:1.4:20的质量比,将马来酸酐和硅烷偶联剂kh-550溶
解到甲苯中,在30℃下搅拌反应1h后,加入质量分别为马来酸酐0.8倍的氯化锌和7.5倍的20wt%六甲基二硅氮烷溶液(溶剂为甲苯),在90℃下反应4h,过滤,旋蒸去除甲苯,获得马来酰亚胺基硅烷偶联剂;s1.2:按照1:15的质量比,将碳酸钙粉末分散到无水乙醇中,升温至40℃后,边搅拌边向其中滴加质量为碳酸钙粉末0.2倍的马来酰亚胺基硅烷偶联剂,滴加完成后,继续在40℃下反应1.5h,离心,水洗,烘干,获得改性碳酸钙粉末。
44.s2:制备改性增韧剂:向密闭反应釜中加入质量比为1:0.35的马来酸酐接枝乙烯-丙烯酸丁酯共聚物和糠醇,将釜内空气置换成氮气,升温至190℃,搅拌反应30min后,冷却,获得改性增韧剂。
45.s3:制备中间层造粒料:s3.1:按照重量份称取以下原料:tpx回收料(由tpx离型膜生产中的在线回边料、有瑕疵tpx离型膜产品和已使用过的tpx离型膜组成)100份,改性碳酸钙粉末2份,改性增韧剂6份,聚丙烯(熔指为10g/10min)15份,2,6-二叔丁基-4-甲基苯酚0.6份,亚磷酸三(2,4-二叔丁基苯基)酯0.1份;s3.2:将所有原料混匀后,采用双螺杆挤出机进行熔融挤出,温度为250℃,主机转速为60rpm,喂料机转速2.5rpm,得到料条;将料条牵引至切粒机中,进行切粒,获得中间层造粒料。
46.s4:制膜:将纯tpx粒子和中间层造粒料分别置于主机a和主机b中,控制主机a和主机b的转速分别为17rpm和36rpm,温度为260℃,模头温度为280℃,进行三层共挤和流延,获得三层结构tpx离型膜。
47.本实施例制得的三层结构tpx离型膜中,上层和下层均为纯tpx层,厚度均为30μm;中间层为回收料层,厚度为60μm。
48.实施例4本实施例与实施例1的区别仅在于,步骤s3.1中,将熔指为10g/10min的聚丙烯换成熔指为14g/10min的聚丙烯。
49.对比例1本对比例与实施例1的区别仅在于,在步骤s3制备中间层造粒料的过程中,仅采用tpx回收料,不添加改性碳酸钙粉末、改性增韧剂、聚丙烯、2,6-二叔丁基-4-甲基苯酚和亚磷酸三(2,4-二叔丁基苯基)酯。
50.对比例2本对比例与实施例1的区别仅在于,将步骤s3.1中的原料换成:纯tpx 100份,聚丙烯(熔指为10g/10min)41份,2,6-二叔丁基-4-甲基苯酚1份,亚磷酸三(2,4-二叔丁基苯基)酯0.4份。
51.对比例3本对比例与实施例1的区别仅在于,步骤s3.1中,将改性碳酸钙粉末换成等质量的碳酸钙粉末,将改性增韧剂换成等质量的乙烯-丙烯酸丁酯共聚物。
52.对比例4本对比例与实施例1的区别仅在于,步骤s3.1中,将改性增韧剂换成等质量的乙
烯-丙烯酸丁酯共聚物,将改性碳酸钙粉末换成等质量的羟基化碳酸钙粉末;所述羟基化碳酸钙粉末的制备方法如下:按照1:10的质量比,将碳酸钙粉末分散到无水乙醇中,升温至40℃后,边搅拌边向其中滴加质量为碳酸钙粉末0.3倍的硅烷偶联剂kh-550,滴加完成后,继续在40℃下反应2.5h,而后加入与kh-550等摩尔量的丙烯酸羟乙酯,继续在40℃下反应3h,离心,水洗,烘干,获得羟基化碳酸钙粉末。
53.对比例5本对比例与实施例1的区别仅在于,步骤s3.1中,将改性碳酸钙粉末换成等质量的碳酸钙粉末,并添加n,n'-(4,4'-亚甲基二苯基)双马来酰亚胺0.3份。
54.测试例在实施例1~4和对比例1~5中,检测中间层造粒料的熔指(测试条件为温度260℃、压力5kg),以及最终制得的tpx离型膜的断裂伸长率和拉伸强度,并记录tpx离型膜的外观有无破洞,结果见表1。
55.表1分析表1数据,可以看出:(1)相较于对比例1而言,实施例1~4和对比例3的中间层造粒料熔指明显降低,与纯tpx层的熔指差距更小(经检测,纯tpx的熔指为26~32g/10min),tpx离型膜在断裂伸长率和拉伸强度上有明显提升,甚至超过采用非回收料制备中间层的tpx离型膜。说明本发明通过在tpx回收料中加入一定量的改性碳酸钙粉末、改性增韧剂和聚丙烯,能够有效降低中间层的熔指,提高tpx离型膜的力学性能。
56.(2)相较于对比例3而言,实施例1的tpx离型膜断裂伸长率和拉伸强度明显较高。说明采用本发明的方法对碳酸钙粉末和eba-g-mah进行改性,能赋予tpx离型膜更好的力学性能。
57.(3)相较于对比例4而言,实施例1虽然中间层造粒料的熔指较大,但tpx离型膜断裂伸长率和拉伸强度明显较高。原因在于:对比例4在合成中间层造粒料时,熔融共混的过程中羟基化碳酸钙粉末与eba-g-mah反应,eba-g-mah形成交联网络,造成其不易均匀分散
到熔融的tpx回收料中,会对eba-g-mah的增韧效果产生不利影响;而实施例1采用接枝有呋喃基团的eba-g-mah和接枝有马来酰亚胺基团的碳酸钙,在熔融共混的高温下不会形成da键,有利于使eba-g-mah均匀分布在中间层,与tpx形成互穿网络,发挥更好的增韧作用。
58.(4)对比例5采用双马来酰亚胺代替改性碳酸钙,相较于对比例5而言,实施例1的tpx离型膜断裂伸长率和拉伸强度明显较高。原因在于:当采用将马来酰亚胺基团接枝在碳酸钙粉末上的方式,在中间层中引入马来酰亚胺基团时,一方面,一个碳酸钙颗粒表面能够接枝上多个马来酰亚胺基团,以其作为eba的交联点,能够在更大程度上提高tpx离型膜的力学性能;另一方面,在tpx离型膜中,利用改性碳酸钙与改性增韧剂之间形成的da键,能提高碳酸钙与聚合物基体的结合强度,同样有利于提高tpx离型膜的力学性能。
59.本发明中所用原料、设备,若无特别说明,均为本领域的常用原料、设备;本发明中所用方法,若无特别说明,均为本领域的常规方法。
60.以上所述,仅是本发明的较佳实施例,并非对本发明作任何限制,凡是根据本发明技术实质对以上实施例所作的任何简单修改、变更以及等效变换,均仍属于本发明技术方案的保护范围。