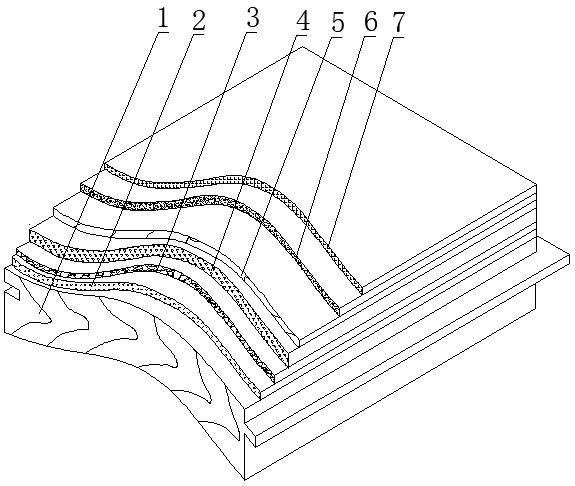
1.本发明涉及木地板生产技术领域,尤其是涉及一种实木复合木地板,本发明还涉及一种实木复合木地板生产方法。
背景技术:2.实木复合地板因具有天然木纹,结构稳定,低甲醛释放等特点,受到越来越多的消费者喜爱,但存在遇火易燃的不足,从而限制了人们在室内装饰装修的应用。如果能在未改变实木复合地板原有性能的情况下,增加其防火阻燃性能,将会促进实木复合地板产业的发展。
3.cn111548766a公开了一种无醛阻燃型实木复合地板及其制备方法,包括油漆涂饰层、表板、阻燃胶层、阻燃多层基材层、阻燃胶层、背板,阻燃多层基材层由桉木单板与阻燃胶按实木复合地板用胶合板基材组坯而成。制备方法包括以下步骤:一、制备活化改性阻燃剂在高速混料机中依次加入20~40份聚磷酸铵app、10~20份三聚氰胺磷酸盐mp、2~3.5份偶联剂、4~7份分散剂,搅拌10~20min,再加入50~80份氢氧化铝或氢氧化镁,再搅拌10~20min至均匀,即制得活化改性阻燃剂;二、制备改性大豆无醛阻燃胶在反应釜中依次加入100份交联改性剂、50~100份水、100~200份脱脂豆粉、50~150份活化改性阻燃剂、5~7份水性增粘剂、0.1~0.2份助剂,在55~110℃条件下搅拌1.5~3h至均匀,即制得改性大豆无醛阻燃胶;所述步骤二中水性增粘剂为松香脂和非松香树脂的混合物,固体含量57%、粘度300mpa
·
s;三、制备无醛阻燃型实木复合地板1)在桉木单板表面涂布步骤二制得的改性大豆无醛阻燃胶,按实木复合地板用多层胶合板每层纵横交错组坯,经冷压、热压后制成阻燃多层基材层;2)阻燃多层基材层经平衡后,涂布步骤二制得的改性大豆无醛阻燃胶,上表面粘合表板、下表面粘合底板,组坯后经冷压、热压、养生、开片、砂光、开槽加工、油漆工序制得无醛阻燃型实木复合地板。
4.目前,阻燃实木复合地板的生产技术线路多为阻燃胶合板加uv阻燃树脂方案,阻燃胶合板一般采用阻燃剂改性单板或成品胶合板,工艺流程复杂,大幅度提高了生产成本;阻燃涂料一般也是采用有机阻燃树脂改性或直接添加阻燃剂的方法,成本比普通uv涂料翻倍,且其在地板表面的用量不可能太大,否则涂装施工性能不好,漆膜装饰功效下降。因而开发一种低成本、高性能的阻燃实木复合地板显得具有重要意义。
技术实现要素:5.为了克服现有技术的缺陷,本发明所要解决的技术问题是提供一种实木复合木地板,具有良好的阻燃性能的特点,且生产成本较低;本发明还提供一种实木复合木地板的生产方法。
6.为了解决上述技术问题,一方面,本发明提供一种实木复合木地板,它包括由原木或胶合板制作的基材层,下表面与所述基材层的上表面粘接的第一三聚氰胺甲醛树脂浸渍纸固化层,下表面与所述第一三聚氰胺甲醛树脂浸渍纸固化层的上表面粘接的无机微粒固
化隔离层,下表面与所述无机微粒固化隔离层的上表面粘接的第二三聚氰胺甲醛树脂浸渍纸固化层,下表面与所述第二三聚氰胺甲醛树脂浸渍纸固化层的上表面粘接的木皮装饰层,粘附在所述木皮装饰层的上表面的颜料层,粘附在所述颜料层的上表面的uv阻燃树脂层;所述实木复合木地板由至少包含以下步骤制得:1)用定量为100~110g/
㎡
的原纸浸渍三聚氰胺甲醛树脂,控制浸胶量为原纸重量的120%~150%,浸渍后干燥至挥发物含量为6wt%~10wt%、预固化度为5%~10%,制得第一三聚氰胺甲醛树脂浸渍纸固化层用浸渍纸;2)往100质量份固含量为30wt%~35wt%的浸渍用三聚氰胺甲醛树脂中加入0.8~1.5质量份三聚氰胺甲醛树脂固化剂,搅拌混和均匀,依次加入20~25质量份400~600目的生石膏、10~15质量份600~800目轻质碳酸钙、1~3质量份纳米碳酸钙,搅拌均匀,用60%~70%(v/v)乙醇水溶液调节涂料的粘度为6~9pa.s;3)将步骤2)制得的混合料涂布在步骤1)制得的第一三聚氰胺甲醛树脂浸渍纸固化层用浸渍纸的一面上,控制涂布厚度为0.2~0.3mm,涂布后干燥至挥发物含量为3wt%~5wt%,制得涂布浸渍纸;4)用定量为110~120g/
㎡
的原纸浸渍三聚氰胺甲醛树脂,控制浸胶量为原纸重量的180%~200%,浸渍后干燥至挥发物含量为5wt%~8wt%、预固化度为20%~30%,制得第二三聚氰胺甲醛树脂浸渍纸固化层用浸渍纸;5)在基材层的上表面依次铺装步骤3)制得的涂布浸渍纸、步骤4)制得的第二三聚氰胺甲醛树脂浸渍纸固化层用浸渍纸、木皮装饰层,送入热压机,在温度为130~140℃、压力为3.0~4.0mpa的条件下保持4~6min,取出冷却,锯切成地板规格板材;热压过程中使产品达到半树脂化、密实化,木皮装饰层中密度为0.5~0.8g/cm3的木皮密实化到1.0~1.2g/cm3;基材层中密度为0.4~0.7g/cm3的木材密实化到0.8~0.9g/cm3;6)经过步骤5)后制得的地板规格板材,在其上表面涂布水性或油性颜料或染料,经干燥后,上含有uv阻燃剂的腻子,干燥,砂光,再滚涂1~2道uv阻燃树脂,干燥,开企口,然后经砂光,辊涂1~2道uv阻燃树脂底漆,干燥,最后辊涂2道uv阻燃树脂面漆,制得实木复合木地板。
7.在上述基本方案的基础上,作为进一步的改进技术方案,本发明提供的实木复合木地板,步骤2)涂料制备过程中,在浸渍用三聚氰胺甲醛树脂、三聚氰胺甲醛树脂固化剂混合液中,加入生石膏、轻质碳酸钙和纳米碳酸钙后,还添加颜料进行调色。
8.作为优选技术方案,本发明提供的实木复合木地板,所述uv阻燃树脂层的厚度为0.05~0.09mm。
9.作为优选技术方案,本发明提供的实木复合木地板,所述木皮装饰层的厚度为0.02~0.06mm。
10.为了解决上述技术问题,另一方面,本发明提供一种实木复合木地板生产方法,包括以下步骤:1)用定量为100~110g/
㎡
的原纸浸渍三聚氰胺甲醛树脂,控制浸胶量为原纸重量的120%~150%,浸渍后干燥至挥发物含量为6wt%~10wt%、预固化度为5%~10%,制得第一三聚氰胺甲醛树脂浸渍纸固化层用浸渍纸;2)往100质量份固含量为30wt%~35wt%的浸渍用三聚氰胺甲醛树脂中加入0.8~
1.5质量份三聚氰胺甲醛树脂固化剂,搅拌混和均匀,依次加入20~25质量份400~600目的生石膏、10~15质量份600~800目轻质碳酸钙、1~3质量份纳米碳酸钙,搅拌均匀,用60%~70%(v/v)乙醇水溶液调节涂料的粘度为6~9pa.s;3)将步骤2)制得的混合料涂布在步骤1)制得的第一三聚氰胺甲醛树脂浸渍纸固化层用浸渍纸的一面上,控制涂布厚度为0.2~0.3mm,涂布后干燥至挥发物含量为3wt%~5wt%,制得涂布浸渍纸;4)用定量为110~120g/
㎡
的原纸浸渍三聚氰胺甲醛树脂,控制浸胶量为原纸重量的180%~200%,浸渍后干燥至挥发物含量为5wt%~8wt%、预固化度为20%~30%,制得第二三聚氰胺甲醛树脂浸渍纸固化层用浸渍纸;5)在基材层的上表面依次铺装步骤3)制得的涂布浸渍纸、步骤4)制得的第二三聚氰胺甲醛树脂浸渍纸固化层用浸渍纸、木皮装饰层,送入热压机,在温度为130~140℃、压力为3.0~4.0mpa的条件下保持4~6min,取出冷却,锯切成地板规格板材;热压过程中使产品达到半树脂化、密实化,木皮装饰层中密度为0.5~0.8g/cm3的木皮密实化到1.0~1.2g/cm3;基材层中密度为0.4~0.7g/cm3的木材密实化到0.8~0.9g/cm3;6)经过步骤5)后制得的地板规格板材,在其上表面涂布水性或油性颜料或染料,经干燥后,上含有uv阻燃剂的腻子,干燥,砂光,再滚涂1~2道uv阻燃树脂,干燥,开企口,然后经砂光,辊涂1~2道uv阻燃树脂底漆,干燥,最后辊涂2道uv阻燃树脂面漆,制得实木复合木地板。
11.在上述基本方案的基础上,作为进一步的改进技术方案,本发明提供的实木复合木地板生产方法,步骤2)涂料制备过程中,在浸渍用三聚氰胺甲醛树脂、三聚氰胺甲醛树脂固化剂混合液中,加入生石膏、轻质碳酸钙和纳米碳酸钙后,还添加颜料进行调色。
12.在不冲突的情况下,前述改进技术方案可以单独或组合实施。
13.本发明提供的技术方案,实木复合木地板具有五层阻燃层结构,一是表面的uv阻燃树脂层;二是木皮经三聚氰胺甲醛树脂热压浸渍并密实化的改性层;三是三聚氰胺甲醛树脂浸渍纸固化层;四是生石膏、碳酸钙等无机材料与三聚氰胺甲醛树脂共混形成的高密度隔离层;五是另一三聚氰胺甲醛树脂浸渍纸固化层。通过五层阻燃结构形成整体阻燃组合隔离保护,使实木复合地板阻燃等级达到gb 8624-2012《建筑材料及制品燃烧性能分级》难燃b1级。
附图说明
14.附图用来提供对本发明的进一步理解,构成本技术的一部分,本发明的示意性实施例及其说明用于解释本发明,并不构成对本发明的不当限定。在附图中:图1为实施例实木复合木地板的结构示意图。
具体实施方式
15.下面结合实施例对本发明进行进一步详述:本发明中三聚氰胺甲醛树脂为浸渍三聚氰胺甲醛树脂、uv阻燃树脂、生石膏、轻质碳酸钙、纳米碳酸钙、浸渍原纸均为市售,木皮为用木材制成的天然装饰木皮,三聚氰胺甲醛树脂固化剂可以使用市售的氨基树脂固化剂和酸性固化剂,如草酸、脲苯二甲酸等。
16.各实施例制得的实木复合木地板,如图1所示,均包括由原木或胶合板制作的基材层1,下表面与基材层1的上表面粘接的第一三聚氰胺甲醛树脂浸渍纸固化层2,下表面与第一三聚氰胺甲醛树脂浸渍纸固化层2的上表面粘接的无机微粒固化隔离层3,下表面与无机微粒固化隔离层3的上表面粘接的第二三聚氰胺甲醛树脂浸渍纸固化层4,下表面与第二三聚氰胺甲醛树脂浸渍纸固化层4的上表面粘接的木皮装饰层5,粘附在木皮装饰层5的上表面的颜料层6,粘附在颜料层6的上表面的uv阻燃树脂层7。木皮装饰层5的厚度为0.02~0.06mm;uv阻燃树脂层7的厚度为0.05~0.09mm。
17.实施例1实木复合木地板由至少包含以下步骤制得:1)用定量为100g/
㎡
的原纸浸渍三聚氰胺甲醛树脂,控制浸胶量为原纸重量的150%,浸渍后干燥至挥发物含量为6wt%、预固化度为10%,制得第一三聚氰胺甲醛树脂浸渍纸固化层2用浸渍纸;2)往100质量份固含量为30wt%的浸渍用三聚氰胺甲醛树脂中加入1.5质量份湛新allnex cycat296-9氨基树脂固化剂,搅拌混和均匀,依次加入20质量份400目的生石膏、15质量份800目轻质碳酸钙、1质量份纳米碳酸钙,搅拌均匀,添加颜料进行调色,达到同浸渍用原纸颜色相一致,用60%(v/v)乙醇水溶液调节涂料的粘度为9pa.s;3)将步骤2)制得的混合料涂布在步骤1)制得的第一三聚氰胺甲醛树脂浸渍纸固化层2用浸渍纸的一面上,控制涂布厚度为0.3mm,涂布后干燥至挥发物含量为3wt%,制得涂布浸渍纸;4)用定量为110g/
㎡
的原纸浸渍三聚氰胺甲醛树脂,控制浸胶量为原纸重量的200%,浸渍后干燥至挥发物含量为5wt%、预固化度为30%,制得第二三聚氰胺甲醛树脂浸渍纸固化层4用浸渍纸;5)在基材层1的上表面依次铺装步骤3)制得的涂布浸渍纸、步骤4)制得的第二三聚氰胺甲醛树脂浸渍纸固化层4用浸渍纸、木皮装饰层5,送入热压机,在温度为130~140℃、压力为3.0~4.0mpa的条件下保持4~6min,取出冷却,锯切成地板规格板材;热压过程中使产品达到半树脂化、密实化,木皮装饰层5中密度为0.5g/cm3的木皮密实化到1.0g/cm3;基材层1中密度为0.4g/cm3的木材密实化到0.8g/cm3;6)经过步骤5)后制得的地板规格板材,在其上表面涂布水性或油性颜料或染料,经干燥后,上含有uv阻燃剂的腻子,干燥,砂光,再滚涂1~2道uv阻燃树脂,干燥,开企口,然后经砂光,辊涂1~2道uv阻燃树脂底漆,干燥,最后辊涂2道uv阻燃树脂面漆,制得实木复合木地板。
18.实施例2实木复合木地板由至少包含以下步骤制得:1)用定量为105g/
㎡
的原纸浸渍三聚氰胺甲醛树脂,控制浸胶量为原纸重量的135%,浸渍后干燥至挥发物含量为8wt%、预固化度为8%,制得第一三聚氰胺甲醛树脂浸渍纸固化层2用浸渍纸;2)往100质量份固含量为33wt%的浸渍用三聚氰胺甲醛树脂中加入1.2质量份湛新allnex酸催化剂cycat4040,搅拌混和均匀,依次加入22质量份500目的生石膏、13质量份700目轻质碳酸钙、2质量份纳米碳酸钙,搅拌均匀,添加颜料进行调色,达到同浸渍用原纸
颜色相一致,用65%(v/v)乙醇水溶液调节涂料的粘度为7.5pa.s;3)将步骤2)制得的混合料涂布在步骤1)制得的第一三聚氰胺甲醛树脂浸渍纸固化层2用浸渍纸的一面上,控制涂布厚度为0.25mm,涂布后干燥至挥发物含量为4wt%,制得涂布浸渍纸;4)用定量为116g/
㎡
的原纸浸渍三聚氰胺甲醛树脂,控制浸胶量为原纸重量的190%,浸渍后干燥至挥发物含量为6.5wt%、预固化度为25%,制得第二三聚氰胺甲醛树脂浸渍纸固化层4用浸渍纸;5)在基材层1的上表面依次铺装步骤3)制得的涂布浸渍纸、步骤4)制得的第二三聚氰胺甲醛树脂浸渍纸固化层4用浸渍纸、木皮装饰层5,送入热压机,在温度为130~140℃、压力为3.0~4.0mpa的条件下保持4~6min,取出冷却,锯切成地板规格板材;热压过程中使产品达到半树脂化、密实化,木皮装饰层5中密度为0.65g/cm3的木皮密实化到1.1g/cm3;基材层1中密度为0.55g/cm3的木材密实化到0.85g/cm3;6)经过步骤5)后制得的地板规格板材,在其上表面涂布水性或油性颜料或染料,经干燥后,上含有uv阻燃剂的腻子,干燥,砂光,再滚涂1~2道uv阻燃树脂,干燥,开企口,然后经砂光,辊涂1~2道uv阻燃树脂底漆,干燥,最后辊涂2道uv阻燃树脂面漆,制得实木复合木地板。
19.实施例3实木复合木地板由至少包含以下步骤制得:1)用定量为110g/
㎡
的原纸浸渍三聚氰胺甲醛树脂,控制浸胶量为原纸重量的120%,浸渍后干燥至挥发物含量为10wt%、预固化度为5%,制得第一三聚氰胺甲醛树脂浸渍纸固化层2用浸渍纸;2)往100质量份固含量为35wt%的浸渍用三聚氰胺甲醛树脂中加入0.8质量份脲苯二甲酸,搅拌混和均匀,依次加入25质量份600目的生石膏、10质量份600目轻质碳酸钙、3质量份纳米碳酸钙,搅拌均匀,添加颜料进行调色,达到同浸渍用原纸颜色相一致,用70%(v/v)乙醇水溶液调节涂料的粘度为6pa.s;3)将步骤2)制得的混合料涂布在步骤1)制得的第一三聚氰胺甲醛树脂浸渍纸固化层2用浸渍纸的一面上,控制涂布厚度为0.2mm,涂布后干燥至挥发物含量为5wt%,制得涂布浸渍纸;4)用定量为120g/
㎡
的原纸浸渍三聚氰胺甲醛树脂,控制浸胶量为原纸重量的180%,浸渍后干燥至挥发物含量为8wt%、预固化度为20%,制得第二三聚氰胺甲醛树脂浸渍纸固化层4用浸渍纸;5)在基材层1的上表面依次铺装步骤3)制得的涂布浸渍纸、步骤4)制得的第二三聚氰胺甲醛树脂浸渍纸固化层4用浸渍纸、木皮装饰层5,送入热压机,在温度为130~140℃、压力为3.0~4.0mpa的条件下保持4~6min,取出冷却,锯切成地板规格板材;热压过程中使产品达到半树脂化、密实化,木皮装饰层5中密度为0.8g/cm3的木皮密实化到1.2g/cm3;基材层1中密度为0.7g/cm3的木材密实化到0.9g/cm3;6)经过步骤5)后制得的地板规格板材,在其上表面涂布水性或油性颜料或染料,经干燥后,上含有uv阻燃剂的腻子,干燥,砂光,再滚涂1~2道uv阻燃树脂,干燥,开企口,然后经砂光,辊涂1~2道uv阻燃树脂底漆,干燥,最后辊涂2道uv阻燃树脂面漆,制得实木复合
木地板。
20.上述实施例获得的木地板,gb/t 8626-2007《建筑材料可燃性试验方法》进行点火15s试验,性能比较如下:
项目20s内焰尖高度点火燃烧变化15s后移开点火源过火面积炭化深度炭化状态普通实木复合地板60mm3~4s被点燃,燃烧剧烈,火苗红黄,不断有微粒飞溅继续燃烧5~150s60~70cm21.5~1.7mm粗大裂纹阻燃实木复合地板45mm4~6s被点燃,燃烧迟缓,火苗黄色,偶尔有微粒飞溅继续燃烧1~3s40~50cm21.0~1.4mm大裂纹实施例1产品40mm5~7s被点燃,燃烧缓慢,火苗浅黄,无微粒飞溅继续燃烧0~0.5s20~30cm20.4~0.7mm小裂纹实施例2产品32mm5~8s被点燃,燃烧缓慢,火苗浅黄,无微粒飞溅继续燃烧0s10~15cm20.2~0.4mm细裂纹实施例3产品36mm5~8s被点燃,燃烧缓慢,火苗浅黄,无微粒飞溅继续燃烧0~0.5s15~20cm20.5~0.7mm小裂纹
本发明提供的技术方案,实木复合木地板具有五层阻燃层结构,一是表面的uv阻燃树脂层;二是木皮经三聚氰胺甲醛树脂热压浸渍并密实化的改性层;三是三聚氰胺甲醛树脂浸渍纸固化层;四是生石膏、碳酸钙等无机材料与三聚氰胺甲醛树脂共混形成的高密度隔离层;五是另一三聚氰胺甲醛树脂浸渍纸固化层。通过五层阻燃结构形成整体阻燃组合隔离保护,使实木复合地板阻燃等级达到gb 8624-2012《建筑材料及制品燃烧性能分级》难燃b1级。
21.本发明不限于以上优选实施方式,还可在本发明权利要求和说明书限定的精神内,进行多种形式的变换和改进,能解决同样的技术问题,并取得预期的技术效果,故不重述。本领域的普通技术人员能从本发明公开的内容直接或联想到的所有方案,只要在权利要求限定的精神之内,也属于本发明的保护范围。