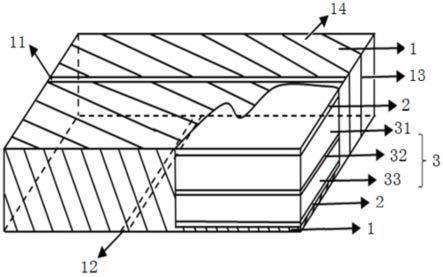
1.本实用新型涉及装甲防护结构技术领域,特别是涉及一种织物捆绑约束的防弹复合装甲板。
背景技术:2.目前的防弹复合装甲板材料通常是由陶瓷面板与超高分子量聚乙烯背板通过热固性树脂胶黏剂粘合而成。该防弹复合装甲板在弹道侵彻作用下,由于弱的界面结合能力使得陶瓷面板和背板之间容易发生分离,并且由于超高分子量聚乙烯本身的变形能力较大,使得背板在受到弹丸冲击后发生变形,产生严重的背凸现象或被穿透,因此现有的防弹复合装甲板材料会造成严重的非贯性钝伤以及穿透伤害。
3.由此可见,上述现有的防弹复合装甲板在结构与使用上,显然仍存在有不便与缺陷,而亟待加以进一步改进。如何能创设一种新的织物捆绑约束的防弹复合装甲板,使其通过织物捆绑层的约束设置,加强陶瓷层和背板层之间的结合强度,提高防弹复合装甲板在弹道侵彻下整体结构的稳定性,进而提高防弹复合装甲板的防弹性能,成为当前业界极需改进的目标。
技术实现要素:4.本实用新型要解决的技术问题是提供一种织物捆绑约束的防弹复合装甲板,使其通过织物捆绑层的约束设置,加强陶瓷层和背板层之间的结合强度,提高防弹复合装甲板在弹道侵彻下整体结构的稳定性,进而提高防弹复合装甲板的防弹性能,从而克服现有的防弹复合装甲板的不足。
5.为解决上述技术问题,本实用新型提供一种织物捆绑约束的防弹复合装甲板,包括复合防弹层和通过第一界面层设置在所述复合防弹层外周表面的织物捆绑层,所述复合防弹层包括通过第二界面层粘接的陶瓷层和背板层。
6.进一步改进,所述织物捆绑层采用十字形结构,所述十字形结构的中间部分与所述复合防弹层的下表面长度尺寸相等,所述十字形结构的两组相对设置的伸出部分均在所述复合防弹层的上表面上对齐形成捆绑接口。
7.进一步改进,所述织物捆绑层包括两个矩形织物片,第一矩形织物片的宽度为所述复合防弹层的长度,所述第一矩形织物片的长度为所述复合防弹层的宽度和高度之和的2倍,第二矩形织物片的宽度为所述复合防弹层的宽度,所述第二矩形织物片的长度为所述复合防弹层的长度和高度之和的2倍。
8.进一步改进,两个所述矩形织物片十字交叉设置,且两个所述矩形织物片的捆绑接口分别位于所述复合防弹层的上表面和下表面。
9.进一步改进,两个所述矩形织物片十字交叉设置,且两个所述矩形织物片的捆绑接口均位于所述复合防弹层的上表面或下表面。
10.进一步改进,所述织物捆绑层采用平纹、斜纹或缎纹结构的芳纶1414纤维织物、芳
ⅲ
纤维织物、pi纤维织物、pipd纤维织物、pbo纤维织物或uhmwpe纤维织物。
11.进一步改进,所述织物捆绑层的织物克重为100-300g/m2。
12.进一步改进,所述陶瓷层采用碳化硅陶瓷板、碳化硼陶瓷板或氧化铝陶瓷板,所述背板层采用超高分子量聚乙烯背板层。
13.进一步改进,所述第一界面层和第二界面层均采用高弹性热塑性树脂基胶膜。
14.进一步改进,所述第一界面层采用的高弹性热塑性树脂基胶膜的层数与所述第二界面层采用的高弹性热塑性树脂基胶膜的层数比为2-3:5-7。
15.采用这样的设计后,本实用新型至少具有以下优点:
16.本实用新型防弹复合装甲板通过织物捆绑层对复合防弹层的约束,能够提高弹道侵彻下防弹复合装甲板的整体结构稳定性,保证在不增加防弹复合装甲板重量的前提下,降低防弹复合装甲板受到子弹冲击后陶瓷层与背板层之间的分离以及背板的背凸高度,显著降低弹道侵彻作用下的非贯穿性钝伤,提高防弹复合装甲板的防弹性能。且本实用新型防弹复合装甲板是一种全包裹结构,可实现系列化、模块化、标准化、轻量化生产。且制备工艺简单、生产效率高,成本低廉。
附图说明
17.上述仅是本实用新型技术方案的概述,为了能够更清楚了解本实用新型的技术手段,以下结合附图与具体实施方式对本实用新型作进一步的详细说明。
18.图1是本实用新型织物捆绑约束的防弹复合装甲板实施例一的结构示意图。
19.图2是本实用新型织物捆绑约束的防弹复合装甲板实施例一的面层分解结构示意图。
20.图3是本实用新型织物捆绑约束的防弹复合装甲板实施例二中织物捆绑层的包裹结构示意图。
21.图4是本实用新型织物捆绑约束的防弹复合装甲板实施例三中织物捆绑层的包裹结构示意图。
具体实施方式
22.实施例一
23.参照附图1和2所示,本实施例织物捆绑约束的防弹复合装甲板,包括复合防弹层3和通过第一界面层2设置在所述复合防弹层3外周表面的织物捆绑层1。所述复合防弹层3的外周表面是指其上表面、下表面、前表面、后表面、左表面和右表面。
24.本实施例中所述复合防弹层3包括陶瓷层31、第二界面层32和背板层33。所述陶瓷层31采用碳化硅陶瓷板、碳化硼陶瓷板或氧化铝陶瓷板。所述背板层33采用超高分子量聚乙烯背板层。所述织物捆绑层1采用平纹、斜纹或缎纹结构的芳纶1414纤维织物、芳ⅲ纤维织物、pi纤维织物、pipd纤维织物、pbo纤维织物或uhmwpe纤维织物。所述织物捆绑层1的织物克重为100-300g/m2。所述第一界面层2和第二界面层32均采用高弹性热塑性树脂基胶膜。所述第一界面层2采用的高弹性热塑性树脂基胶膜的层数与所述第二界面层32采用的高弹性热塑性树脂基胶膜的层数比为2-3:5-7。
25.本实施例中陶瓷层31、第二界面层32和背板层33的复合,以及织物捆绑层1、第一
界面层2和复合陶瓷层3的复合均采用现有真空袋或热压罐复合工艺步骤进行。
26.本实施例中所述织物捆绑层1的具体结构为:包括两个矩形织物片13、14,第一矩形织物片14的宽度为所述复合防弹层3的长度,所述第一矩形织物片14的长度为所述复合防弹层3的宽度和高度之和的2倍,第二矩形织物片13的宽度为所述复合防弹层3的宽度,所述第二矩形织物片13的长度为所述复合防弹层3的长度和高度之和的2倍。所述矩形织物片13围绕所述复合防弹层3的下表面、左表面、上表面和右表面设置,且所述矩形织物片13的织物捆绑接口12位于所述复合防弹层3的下表面中位线处。然后所述矩形织物片14与所述矩形织物片13垂直交叉设置,围绕所述复合防弹层3的上表面、前表面、下表面和后表面设置,且所述矩形织物片14的织物捆绑接口11位于所述复合防弹层3的上表面中位线处。这样,两个矩形织物片13、14通过十字交叉的设置能将复合防弹层形成全包裹的纤维约束结构,大大提升防弹复合装甲板的整体结构稳定性。
27.实施例二
28.本实施例与上述实施例一的主要区别在于,两个矩形织物片13、14对复合防弹层3的包裹结构不同,如附图3所示,两个矩形织物片13、14均从复合防弹层3的底部向上包裹,两个矩形织物片13、14的捆绑接口12、11均位于所述复合防弹层的上表面。
29.当然,两个矩形织物片13、14的捆绑接口12、11也可均位于所述复合防弹层的下表面。
30.实施例三
31.本实施例与上述实施例一的主要区别在于,如附图4所示,所述织物捆绑层1直接采用十字形结构,所述十字形结构的中间部分与所述复合防弹层3的下表面长度尺寸相等,所述十字形结构的两组相对设置的伸出部分均在所述复合防弹层3的上表面上对齐形成捆绑接口11、12,同样能实现对复合防弹层的全包裹结构。
32.结果实施例
33.将上述实施例得到的防弹复合装甲板进行弹道测试,以同等面密度42
±
0.1kg/m2(单位面积内材料的重量)下的现有装甲板作为对比,在同样的弹道试验条件下进行测试,评价指标为防弹复合装甲板背面鼓包的高度(背凸高度)和背板层的剩余厚度百分比(余量)。现有装甲板的结构为:纤维布止裂层+界面层+陶瓷层+界面层+pe背板层。
34.本实施例弹道试验条件为:54式12.7mm机枪弹(穿甲燃烧弹),入射角0
°
,子弹着靶速度为488
±
10m/s,射距为100m。结果见下表1。
35.表1本实施例防弹复合装甲板和现有装甲板的弹道测试结果对比
36.37.从上述表1结果可知:现有装甲板与本技术的防弹复合装甲板相比,面密度基本不变。即在同等面密度和弹道试验条件下,本技术实施例得到的防弹复合装甲板在弹道侵彻时,背凸减小,背板层的厚度余量显著提升,降低了背板层的非贯穿性损伤和被穿透的风险。表明本技术防弹复合装甲板具有优异的防弹性能。
38.在本实用新型的描述中,需要说明的是,术语“上”、“下”、“前”、“后”、“左”、“右”等指示的方位或位置关系为基于附图所示的方位或位置关系,仅是为了便于描述本实用新型和简化描述,而不是指示或暗示所指的装置或元件必须具有特定的方位、以特定的方位构造和操作,因此不能理解为对本实用新型的限制。
39.以上所述,仅是本实用新型的较佳实施例而已,并非对本实用新型作任何形式上的限制,本领域技术人员利用上述揭示的技术内容做出些许简单修改、等同变化或修饰,均落在本实用新型的保护范围内。