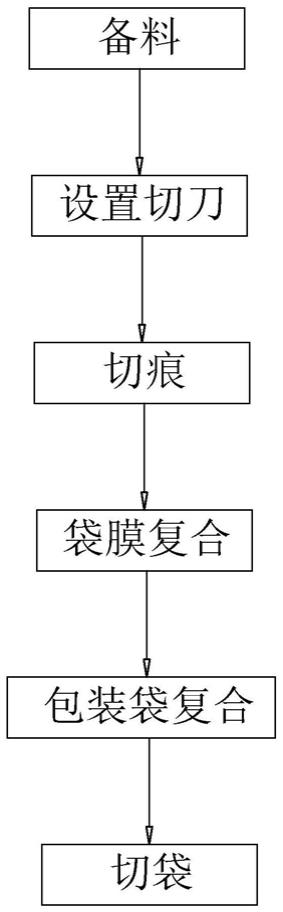
1.本申请涉及包装袋制备的领域,尤其是涉及一种直线易撕包装袋的加工工艺。
背景技术:2.包装袋是指用于包装各种用品的袋子,广泛用于日常生活和工业生产中。软包装袋是包装袋中的一种,软包装袋是指在充填或取出内装物后,容器形状可发生变化的包装袋。前很多包装袋在开口时困难,需要借助辅助的剪刀或刀片才能将包装袋打开,有些采用锯齿状结构的易撕结构,然而锯齿状的易撕结构在撕断的过程中难于保证撕的整齐性,往往仅撕开一点撕口就歪倒一边去了,给使用者造成很多困难,因此为保证包装袋撕断的整齐性,又出现了直线易撕包装袋。
3.相关技术文献公开了申请号为cn201822006529.0的中国实用新型专利,具体涉及一种直线易撕包装膜及包装袋,所述直线易撕包装膜由四层膜层构成,所述四层膜层依次为:聚对苯二甲酸乙二醇酯薄膜层、铝箔薄膜层、尼龙薄膜层和聚丙烯薄膜层。其中所述尼龙薄膜层设有用于撕开所述包装膜的直线型激光线。用户在撕开这种包装膜时,撕裂的力量会集中在直线型激光线上,从而撕出直线型的撕裂口,并且由于仅在尼龙薄膜层设置激光线,因此能使包装膜具有良好的密封性能。该实用新型还提供一种使用上述包装膜制备的包装袋,同样具备以上优点。
4.针对上述中的相关技术,发明人认为采用激光打线技术虽然也可以形成直线易撕线,但激光打线技术的激光打线设备价格高,设备损坏率较高,且在使用前后都需要大量的调试,导致包装袋的生产稳定性也有较大的影响。
技术实现要素:5.为了提高直线易撕包装袋的稳定成型,本申请提供一种直线易撕包装袋的加工工艺。
6.本申请提供的一种直线易撕包装袋的加工工艺,采用如下的技术方案:一种直线易撕包装袋的加工工艺,包括以下步骤:步骤一、备料,根据使用的需求选择两薄膜作为原料;步骤二、设置切刀,根据所需切割薄膜的数量设置切刀数量,切刀包括刀盘以及与刀盘同轴线且分别设置于刀盘两侧的定位盘,刀盘的半径大于定位盘半径,且刀盘与定位盘的半径之差小于待切割的对应薄膜厚度;步骤三、切割,在薄膜的传送过程中,带动刀盘沿薄膜的宽度方向划过,刀盘切割过程中保证定位盘压紧薄膜待切割一侧,从而在薄膜的一侧形成深度小于薄膜厚度的切割槽;步骤四、袋膜复合,将两薄膜均未开设有切割槽的一侧进行复合形成袋膜;步骤五、包装袋复合,取两袋膜,使两袋膜切割槽的位置对应,然后对袋膜的侧边进行复合;
步骤六、切袋,对袋膜进行切割形成袋体。
7.通过采用上述技术方案,在袋膜制备过程中,双层复合袋膜的至少一原料薄膜切槽,然后将两袋膜的切槽位置对应,在将袋膜复合成袋体,能够使袋体的两侧均形成切槽,且不会使袋体破裂,而撕裂袋体时,由于袋体两侧袋膜切槽的设置,能够保证袋体的撕裂口沿两袋膜的切槽方向整齐撕裂,且由于切槽减弱了袋体撕裂位置的强度,袋体的撕裂也更为方便,成型方便稳定,袋体的质量高。
8.可选的,备料时,选用一高阻隔膜与一非高阻隔膜作为原料,设置切刀时,使刀盘半径与切刀半径之差小于非高阻隔膜的厚度;切割时,在非高阻隔膜传送时,通过切刀对非高阻隔膜切出切割槽;袋膜复合时,将开设有切割槽的非高阻隔薄膜远离切割槽的一侧与高阻隔膜复合形成袋膜;包装袋复合时,将两袋膜开设有切割槽的一侧相对设置,然后将两袋膜进行复合切割形成包装袋。
9.通过采用上述技术方案,使用时,选用高阻隔膜与非高阻隔膜作为原料,然后对非高阻隔膜划出切槽再将非高阻隔膜与高阻隔膜进行复合形成袋膜,并使袋膜滑槽的一侧相对设置复合袋体,能够使成型后的袋体外观无变化,且不损坏袋体的高阻隔性能,并且在袋体撕裂时保证袋体的撕裂口呈直线设置。
10.可选的,所述的步骤二、设置切刀,设置一切刀,切刀包括刀盘以及与刀盘同轴线且分别设置于刀盘两侧的定位盘,刀盘的半径大于定位盘半径,且刀盘与定位盘的半径之差小于待切割的对应薄膜厚度;步骤三、切割,在薄膜的传送过程中,带动刀盘沿薄膜的宽度方向划过,刀盘切割过程中保证定位盘压紧薄膜待切割一侧,从而在薄膜的一侧形成深度小于薄膜厚度的切割槽;步骤四、袋膜复合,保持开设有切割槽的薄膜停止传送,将另一薄膜趋向靠近开设有切割槽的薄膜方向靠近,使未开设有切割槽的薄膜远离切割槽的一侧与另一薄膜复合。
11.通过采用上述技术方案,在完成一薄膜的切割后,停止薄膜的传送,采用将另一未切槽的薄膜贴合于已切槽的薄膜,完成两薄膜的复合,能够避免开设有切槽的薄膜在开设切槽后强度降低,避免切槽后的薄膜复合过程中撕裂,进而保证了袋膜的复合稳定性。
12.可选的,所述步骤三中薄膜传送采用传送部件,所述传送部件包括固定架,所述固定架的一端转动连接有上输送辊,且固定架的另一端转动连接有出料辊,所述固定架的中部水平设置有上表面与上输送辊外缘上侧平齐的切割台,所述固定架对应切割台的上方水平设置有能够沿垂直于薄膜输送方向滚动的转动轴,所述刀盘以及定位盘固定于所述转动轴、所述刀盘、定位盘以及转动轴同轴线设置。
13.通过采用上述技术方案,工作时,待切割的薄膜将通过固定架端部的上输送辊传送至切割台上侧并由出料辊传送出切割台,当待切割薄膜的切割位置运动至切割台后,出料辊停止转动,薄膜停止传送,通过转动轴沿垂直于薄膜的传送方向运动,即可带动定位盘以及刀盘沿薄膜宽度方向从薄膜的上侧滚过,实现薄膜切割槽的切割。
14.可选的,所述切割台内设置有抽风腔,切割台的表面对应刀盘切割路径的两侧开设有多个风孔。
15.通过采用上述技术方案,当薄膜送至切割台时,通过多个抽风腔与多个风孔相互配合,能够将薄膜吸附于切割台的上表面,从而使薄膜紧贴于切割台,保证薄膜的精准切割。
16.可选的,所述上输送辊以及下输送辊的周面以其轴线方向中部为中心对称设置有螺旋橡胶条。
17.通过采用上述技术方案,当薄膜在上输送辊或下输送辊上输送时,由于对称设置于上输送辊和下输送辊周面的螺旋橡胶条,能够在薄膜传送时对薄膜起到展平作用,保证薄膜的平整的传送。
18.可选的,所述切割台沿薄膜的传送方向滑移连接于固定架,所述切割台远离上输送辊的一端转动连接有与上输送辊轴线方向相同的上压辊,所述上压辊能够抵接于切割台上传送出薄膜的上侧,所述切割台对应上压辊的下侧转动连接有与上压辊轴线方向相同的下压辊,所述固定架对应上输送辊的下侧转动连接有与上输送辊轴线方向相同的下输送辊,所述切割台对应上压辊与下压辊之间的位置固接有喷胶管,所述喷胶管的上下两侧均设置有喷胶口,所述固定架上设置有能够驱动切割台往复运动的往复机构。
19.通过采用上述技术方案,常态下,待切割的薄膜一端从上输送辊上侧送至切割台上侧并由上压辊与下压辊之间传送出,另一薄膜则由下输送辊上侧输送并从切割台的下侧经过并由上压辊与下压辊之间传送出,从上输送辊上传送出的薄膜经过切割台时,通过切刀盘对薄膜的上侧切割出切割槽后,往复机构带动切割台趋向上输送辊的方向运动,能够通过切割台同时带动上压辊、下压辊以及喷胶管同步趋向上输送辊的方向运动,同时,开启喷胶管,则随切割台的滑移,出料辊停止转动,两薄膜停止输送,喷胶管随切割台滑移对上下两侧薄膜喷胶,上压辊与下压辊压紧喷胶后的两薄膜的相互靠近一侧,使两薄膜复合成袋膜,然后,往复机构推动切割台复位,同时,待切割薄膜与未切割薄膜继续输送,重复上述步骤即可实现袋膜的成型与切槽,由于在切槽后,薄膜强度降低,但在袋膜的复合过程中,切割后的薄膜保持静止不动,薄膜不受拉力,而切槽后的薄膜与另一薄膜复合后,再通过出料辊带动复合后的袋膜传送,能够保证切槽后的薄膜在复合过程中不会产生断裂等情况,保证袋膜的复合。
20.可选的,所述上压辊与下压辊内均设置有加热装置。
21.通过采用上述技术方案,采用的加热装置能够对上压辊与下压辊进行加热,从而使上压辊与下压辊提高热量,进而使两薄膜快速复合。
22.综上所述,本申请包括以下至少一种有益技术效果:1.在袋膜制备过程中,双层复合袋膜的至少一原料薄膜切槽,然后将两袋膜的切槽位置对应,在将袋膜复合成袋体,能够使袋体的两侧均形成切槽,且不会使袋体破裂,而撕裂袋体时,由于袋体两侧袋膜切槽的设置,能够保证袋体的撕裂口沿两袋膜的切槽方向整齐撕裂,且由于切槽减弱了袋体撕裂位置的强度,袋体的撕裂也更为方便,成型方便稳定,袋体的质量高;2.使用时,选用高阻隔膜与非高阻隔膜作为原料,然后对非高阻隔膜划出切槽再将非高阻隔膜与高阻隔膜进行复合形成袋膜,并使袋膜滑槽的一侧相对设置复合袋体,能够使成型后的袋体外观无变化,且不损坏袋体的高阻隔性能,并且在袋体撕裂时保证袋体的撕裂口呈直线设置;
3.在完成一薄膜的切割后,停止薄膜的传送,采用将另一未切槽的薄膜贴合于已切槽的薄膜,完成两薄膜的复合,能够避免开设有切槽的薄膜在开设切槽后强度降低,避免切槽后的薄膜复合过程中撕裂,进而保证了袋膜的复合稳定性。
附图说明
23.图1是本申请的一种直线易撕包装袋的加工工艺的工艺流程图。
24.图2是本申请的一种直线易撕包装袋的加工工艺的中切刀结构爆炸示意图。
25.图3是本申请的一种直线易撕包装袋的加工工艺的实施例三的传送部件的整体结构示意图。
26.图4是本申请的一种直线易撕包装袋的加工工艺的实施例三的切割台的整体结构示意图。
27.图5是本申请的一种直线易撕包装袋的加工工艺的实施例三的喷胶管的结构示意图。
28.附图标记说明:1、切刀;11、刀盘;12、定位盘;2、固定架;21、上输送辊;22、下输送辊;23、出料辊;24、螺旋橡胶条;25、承接架;251、滑槽;253、齿条;26、转动轴;261、承接环;262、齿轮;27、推动缸;28、往复缸;3、切割台;31、风孔;32、上压辊;33、下压辊;34、喷胶管;35、喷胶口。
具体实施方式
29.以下结合附图1
‑
5对本申请作进一步详细说明。
30.本申请实施例公开一种直线易撕包装袋的加工工艺。
31.实施例1参照图1和图2,一种直线易撕包装袋的加工工艺,包括以下步骤:步骤一、备料,选用两薄膜作为原料,薄膜可以采用相同材质也可以采用不同材质,如pe膜或尼龙膜,pet膜,cpp膜、opp膜等;步骤二、设置切刀1,设置两切刀1,切刀1均包括刀盘11以及同轴设置于刀盘11的两侧的定位盘12,刀盘11的半径大于定位盘12半径,两切刀1的刀盘11半径与对应定位盘12的半径差分别小于两薄膜的厚度;步骤三、切痕,将两薄膜同时装载于复合设备的传送部件,将两切刀1分别设置于两薄膜的传送部件一侧,当两薄膜分别传送至对应的切刀1位置时,使对应切刀1的定位盘12压紧于对应薄膜,通过刀盘11以及定位盘12沿垂直于薄膜的传送方向滚动,实现刀盘11沿薄膜的宽度方向切割,在两薄膜上分别形成直线切割槽;步骤四、袋膜复合,将两薄膜未开设切割槽的一侧分别进行涂胶,然后,将两薄膜的涂胶侧进行复合形成袋膜;步骤五、包装袋复合,将两复合后的袋膜同时送至包装袋复合设备,使两袋膜开设有切割槽的位置户对应设置,对两袋膜的两侧位置进行复合,并随两袋膜的传送沿两袋膜的宽度方向进行复合,形成多个首尾依次连接的袋体区,并使各袋体区的一端均设置有切割槽;步骤六、切袋,将复合后的两袋膜,沿各袋体区的两端位置进行切割,形成多个直
线易撕包装袋。
32.实施例1的实施原理为:在袋膜制备过程中,双层复合袋膜的至少一原料薄膜切槽,然后将两袋膜的切槽位置对应,在将袋膜复合成袋体,能够使袋体的两侧均形成切槽,且不会使袋体破裂,而撕裂袋体时,由于袋体两侧袋膜切槽的设置,能够保证袋体的撕裂口沿两袋膜的切槽方向整齐撕裂,且由于切槽减弱了袋体撕裂位置的强度,袋体的撕裂也更为方便,成型方便稳定,袋体的质量高。
33.实施例2参照图1和图2,一种直线易撕包装袋的加工工艺,包括以下步骤:步骤一、备料,选用高阻隔膜与非高阻隔膜作为原料;步骤二、设置切刀1,设置一切刀1,切刀1均包括刀盘11以及同轴设置于刀盘11的两侧的定位盘12,刀盘11的半径大于定位盘12半径,且刀盘11半径与定位盘12半径差小于两非高阻隔膜的厚度;步骤三、切槽,将高阻隔膜与非高阻隔膜装载于复合设备的传送部件,将切刀1装载于非高阻隔膜的传送位置一侧,当非高阻隔膜传送至切刀1位置时,使定位盘12压紧于待非高阻隔薄膜的一侧,通过刀盘11以及定位盘12沿垂直于非高阻隔膜的传送方向滚动,实现刀盘11沿非高阻隔膜的宽度方向切割,在非高阻隔膜上形成直线切割槽;步骤四、袋膜复合,将切割后的非高阻隔膜远离切割槽一侧与高阻隔膜一侧涂胶,然后,将高阻隔膜与非高阻隔膜复合,形成袋膜;步骤五、包装袋复合,将两复合后的袋膜同时送至包装袋复合设备,使两袋膜开设有切割槽的一侧相对设置,并使两袋膜的切割槽位置对应设置,对两袋膜的两侧边位置进行复合,并随两袋膜的传送沿两袋膜的宽度方向进行复合,形成多个首尾依次连接的袋体区,并使各袋体区的一端均设置有切割槽;步骤六、切袋,将复合后的两袋膜,沿各袋体区的两端位置进行切割,形成多个直线易撕包装袋。
34.实施例2的实施原理为:使用时,选用高阻隔膜与非高阻隔膜作为原料,然后对非高阻隔膜划出切槽再将非高阻隔膜与高阻隔膜进行复合形成袋膜,并使袋膜滑槽251的一侧相对设置复合袋体,能够使成型后的袋体外观无变化,且不损坏袋体的高阻隔性能,并且在袋体撕裂时保证袋体的撕裂口呈直线设置。
35.实施例3,参照图1和图2,一种直线易撕包装袋的加工工艺,包括以下步骤:步骤一、备料,选用两薄膜作为原料,薄膜可以采用相同材质也可以采用不同材质,如pe膜或尼龙膜,pet膜,cpp膜、opp膜等;步骤二、设置切刀1,设置一切刀1,切刀1均包括刀盘11以及同轴设置于刀盘11的两侧的定位盘12,刀盘11的半径大于定位盘12半径,且刀盘11半径与定位盘12半径差小于一薄膜的厚度;步骤三、切槽,将两薄膜装载于复合设备的传送部件,将切刀1装载于待切割薄膜的传送位置一侧,同时输送两薄膜,当待切割薄膜传送至切刀1位置时停止两薄膜的输送,使定位盘12压紧于待切割薄膜的一侧,通过刀盘11以及定位盘12沿垂直于待切割薄膜的传送方向滚动,实现刀盘11沿待切割薄膜宽度方向切割,在待切割薄膜上形成直线切割槽;
步骤四、袋膜复合,保持开设有切割槽的薄膜静止,将切割后的薄膜远离切割槽一侧与另一薄膜一侧涂胶,保持开设有切割槽的薄膜停止传送,将另一薄膜趋向靠近开设有切割槽的薄膜方向靠近,使未开设有切割槽的薄膜远离切割槽的一侧与另一薄膜复合,形成袋膜;步骤五、包装袋复合,将两复合后的袋膜同时送至包装袋复合设备,使两袋膜开设有切割槽的一侧相对设置,并使两袋膜的切割槽位置对应设置,对两袋膜的两侧边位置进行复合,并随两袋膜的传送沿两袋膜的宽度方向进行复合,形成多个首尾依次连接的袋体区,并使各袋体区的一端均设置有切割槽;步骤六、切袋,将复合后的两袋膜,沿各袋体区的两端位置进行切割,形成多个直线易撕包装袋。
36.参照图3和图4,其中,步骤三的传送部件包括固定架2,固定架2的一端转动连接有上输送辊21,固定架2对应上输送辊21的下侧转动连接有与上输送辊21轴线方向相同的下输送辊22,且固定架2远离上输送辊21与下输送辊22的一端转动连接有两出料辊23,两出料辊23沿竖直方向排列,且两出料辊23之间留有出料间隙,固定架2对应下方出料辊23的一端固接有驱动电机,上输送辊21以及下输送辊22的周面以其轴线方向中部为中心对称设置有螺旋橡胶条24。固定架2的中部设置有切槽复合装置,两薄膜切槽复合时,分别从上输送辊21与下输送辊22的上侧传送,经过切槽复合装置切槽复合后从出料辊23传送出,且当薄膜在上输送辊21或下输送辊22上输送时,由于对称设置于上输送辊21和下输送辊22周面的螺旋橡胶条24,能够在薄膜传送时对薄膜起到展平作用,保证薄膜的平整的传送。
37.参照图4和图5,切槽复合装置包括固接于固定架2的中部的切割台3,切割台3水平设置,且其上表面与上输送辊21外缘上侧平齐,切割台3内设置有抽风腔,切割台3的表面对应刀盘11切割路径的两侧开设有多个风孔31。固定架2对应切割台3的上方水平设置有承接架25,承接架25的长度方向与固定架2的宽度方向相同,且承接架25的两侧均沿其长度方向开设有滑槽251,两滑槽251内插设有转动轴26,转动轴26的长度方向垂直于承接架25的长度方向,转动轴26的一端转动连接有承接环261,转动轴26的另一端还螺栓连接有齿轮262,承接架25对应齿轮262的下侧固接有与承接架25长度方向相同的齿条253,齿轮262啮合于齿条253。承接架25的一端固接有与承接架25长度方向相同的推动缸27,推动缸27的伸缩杆固接于承接环261,刀盘11以及定位盘12螺栓连接于转动轴26,刀盘11、定位盘12以及转动轴26同轴线设置。当待切割的薄膜传送至切割台3后,出料辊23停止转动,通过推动缸27带动伸缩杆延伸,能够带动承接环261沿承接架25的长度方向滑移,同时,通过齿轮262与齿条253配合还能使承接轴在移动的过程中进行滚动,进而的,带动定位盘12以及刀盘11沿薄膜宽度方向从薄膜的上侧滚过,实现薄膜切割槽的切割。且当薄膜送至切割台3时,通过多个抽风腔与多个风孔31相互配合,能够将薄膜吸附于切割台3的上表面,从而使薄膜紧贴于切割台3,保证薄膜的精准切割。
38.参照图4和图5,切割台3沿固定架2的长度方向滑移,固定架2上设置有能够驱动切割台3往复运动的往复机构,往复机构包括固接于固定架2的往复缸28,往复缸28的轴线方向与固定架2的长度方向相同,且往复缸28的伸缩杆固接于切割台3。切割台3远离上输送辊21的一端转动连接有与上输送辊21轴线方向相同的上压辊32,上压辊32能够抵接于切割台3上传送出的薄膜的上侧,切割台3对应上压辊32的下侧转动连接有与上压辊32轴线方向相
同的下压辊33,上压辊32与下压辊33内均设置有加热装置,加热装置可以为电热棒。切割台3对应上压辊32与下压辊33之间的位置固接有喷胶管34,喷胶管34的上下两侧均设置有喷胶口35,喷胶管34可以连接外部喷胶设备。
39.参照图4和图5,常态下,待切割的薄膜一端从上输送辊21上侧送至切割台3上侧并由上压辊32与下压辊33之间传送出,另一薄膜则由下输送辊22上侧输送并从切割台3的下侧经过并由上压辊32与下压辊33之间传送出,从上输送辊21上传送出的薄膜经过切割台3时,通过切刀1盘对薄膜的上侧切割出切割槽后,往复机构带动切割台3趋向上输送辊21的方向运动,能够通过切割台3同时带动上压辊32、下压辊33以及喷胶管34同步趋向上输送辊21的方向运动,同时,开启喷胶管34,则随切割台3的滑移,出料辊23停止转动,两薄膜停止输送,喷胶管34随切割台3滑移对上下两侧薄膜喷胶,上压辊32与下压辊33压紧喷胶后的两薄膜的相互靠近一侧,使两薄膜复合成袋膜,然后,往复机构推动切割台3复位,同时,待切割薄膜与未切割薄膜继续输送,重复上述步骤即可实现袋膜的成型与切槽,由于在切槽后,薄膜强度降低,但在袋膜的复合过程中,切割后的薄膜保持静止不动,薄膜不受拉力,而切槽后的薄膜与另一薄膜复合后,再通过出料辊23带动复合后的袋膜传送,能够保证切槽后的薄膜在复合过程中不会产生断裂等情况,保证袋膜的复合,此外,采用的加热装置能够对上压辊32与下压辊33进行加热,从而使上压辊32与下压辊33提高热量,进而使两薄膜快速复合。
40.本申请实施例3的实施原理为:在完成一薄膜的切割后,停止薄膜的传送,采用将另一未切槽的薄膜贴合于已切槽的薄膜,完成两薄膜的复合,能够避免开设有切槽的薄膜在开设切槽后强度降低,避免切槽后的薄膜复合过程中撕裂,进而保证了袋膜的复合稳定性。
41.以上均为本申请的较佳实施例,并非依此限制本申请的保护范围,故:凡依本申请的结构、形状、原理所做的等效变化,均应涵盖于本申请的保护范围之内。