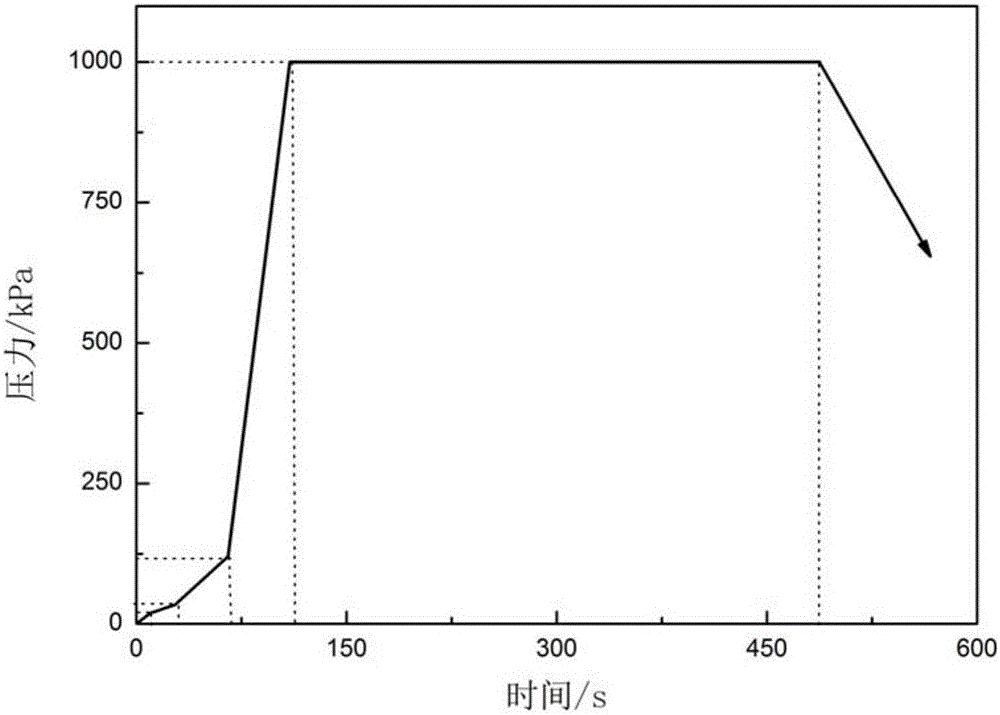
本发明涉及一种采用低压铸造工艺制作铝合金车轮的方法,更特别地说,是一种按照内外轮缘凝固时间分阶段增大结晶增压压力、制备铝合金车轮的、金属型低压铸造成型用结晶增压方法。
背景技术:与传统的重力铸造相比,低压铸造充型速度可控,金属液流动平稳、减少了二次夹杂。与砂型铸造相比,金属型铸造冷却速度快,更容易得到细小致密组织和高的力学性能,也更容易实现自动化和洁净化生产,所以,金属型低压铸造广泛用于生产铝合金车轮、底盘零件、发动机部件等汽车零部件生产领域和航空航天等军工生产领域。低压铸造工艺过程可由作用在金属液表面的压力-时间曲线来反映。典型的砂型低压铸造压力-时间曲线包括升液、充型、结壳增压、结壳保压、结晶增压、结晶保压和卸压七个阶段。金属型低压铸造与砂型低压铸造由于铸型材料的不同,一般省去结壳阶段,因此,金属型低压铸造工艺过程为:升液、充型、结晶增压、结晶保压和卸压五个阶段。铝合金车轮有助于汽车实现轻量化、降低油耗、减轻环境污染与改善操作性能。目前85%以上的乘用车配置了金属型低压铸造方法生产的铝合金车轮。然而,随着汽车轻量化要求日益增强,现有铝合金车轮低压铸造生产技术的局限性开始显现。如何进一步提高车轮力学性能,已成为制约铝合金车轮进一步轻量化的瓶颈。铝合金车轮典型结构如图1,自中心向外,依次为轮心、轮辐、轮辋,轮辋的内侧、外侧分别称为内轮缘、外轮缘。摘自《铝加工》,陈志,李昌海《Magmasoft模拟条件与低压铸造铝车轮生产条件匹配性研究》,2015年第6期总227期。对于15吋~26吋乘用车车轮,轮心部位壁厚一般为25~50mm,轮辐部位壁厚一般为10~25mm,轮辋部位壁厚一般为10~13mm,轮辐轮辋过渡处存在较大的热节,厚度约27~35mm。低压铸造生产中,必须依据车轮结构特征设计充型和冷却工艺,实现顺序凝固,以提高补缩效果、消除或减轻缩孔缩松等铸造缺陷。铸件在压力下凝固,是低压铸造区别于普通铸造的根本特征。结晶增压压力直接影响补缩效果。对于铝合金车轮金属型低压铸造,实际生产中考虑到铸型合模力的限制以及模具间缝隙带来的铝液飞溅、铸件飞边毛刺等问题,结晶增压压力一般为50~80kPa,特殊条件下增大到80~150kPa,限制了通过提高结晶增压压力进一步提高铸件组织致密度和力学性能的可行性。
技术实现要素:针对现有铝合金车轮经金属型低压铸造方法难以实现高结晶增压压力的问题,结合铝合金车轮结构特点和顺序凝固工艺要求,在保留现有低压铸造方法充型速度可控特点的前提下,提出一种按照内外轮缘凝固时间分阶段增大结晶增压压力、制备铝合金车轮的、金属型低压铸造成型用结晶增压方法,以进一步减少缩孔缩松等铸造缺陷、提高铝合金车轮组织致密度和力学性能。本发明的一种金属型低压铸造成型用结晶增压方法,所述金属型低压铸造至少包括有升液阶段、充型阶段、结晶增压阶段、结晶保压阶段和卸压阶段;其特征在于:根据内外轮缘充型后的凝固时间,把结晶增压划分为两个阶段;第一阶段:充型阶段结束至内外轮缘凝固结束,结晶增压压力增大到80~150kPa;第二阶段:内外轮缘凝固结束后,结晶增压压力快速增大到160~1000kPa,增压速度为10~40kPa/s;内轮缘、外轮缘在充型完成后8~40s凝固结束;在压力达到160~1000kPa后,进入结晶保压阶段;(A)轮辋部位在充型完成后12~130s后凝固结束;(B)轮辐轮辋过渡部位在充型完成后30~260s后凝固结束;(C)轮心部位在充型完成后90~500s后凝固结束,继续保压10~60s后卸压。本发明的一种依据金属型低压铸造成型用结晶增压方法制备铝合金汽车车轮,其特征在于有下列步骤:步骤一,升液阶段;调节升液阶段的压力为18~21kPa,升液速度为1.8~2.2kPa/s;步骤二,充型阶段;调节充型阶段的充型压力为30~35kPa,充型速度为0.4~1.0kPa/s,使铝液从浇口进入型腔,直至将型腔全部充满;步骤三,结晶增压阶段;经步骤二后使铝液完全充满铸型后,进入结晶增压阶段:(A)充型阶段结束,开始增大结晶增压压力;(B)内轮缘、外轮缘在充型完成后8~40s凝固结束;(C)内外轮缘凝固结束时,结晶增压压力增大到80~150kPa;(D)内外轮缘凝固结束后,结晶增压压力快速增大到160~1000kPa,增压速度为10~40kPa/s:步骤四,结晶保压阶段;在压力达到160~1000kPa后,进入结晶保压阶段;(A)轮辋部位在充型完成后12~130s后凝固结束;(B)轮辐轮辋过渡部位在充型完成后30~260s后凝固结束;(C)轮心部位在充型完成后90~500s后凝固结束,继续保压10~60s;步骤五,卸压放气阶段;经步骤四后,待铝合金车轮凝固完毕,解除保温炉内的气体压力,使升液管和浇道口未凝固的铝液流回到保温炉中。本发明的一种制备铝合金车轮的金属型低压铸造成型用结晶增压方法优点在于:(1)采用本发明方法制备A356铝合金车轮,与目前现有低压铸造加压方法相比,凝固补缩效果显著提高,在模具结构和合模力不变的情况下,可将轮辐部位强度提高10~50%,延伸率提高25~70%。显著降低了对模具结构和合模力的要求,同时避免了铝液的溢出、飞溅和铸件飞边、毛刺等缺陷。(2)采用本发明方法与现有的铝合金车轮金属型低压铸造相比,按照内外轮缘凝固时间分阶段增大结晶增压压力,最终结晶增压压力达到160~1000kPa,内外轮缘凝固后增压速度达到10~40kPa/s。可进一步减少缩孔缩松等铸造缺陷、提高铝合金车轮组织致密度和力学性能。(3)采用本发明方法与现有差压铸造相比,差压铸造有上下两个压力罐,下压力罐为保温炉和铝液坩埚,上压力罐为铸型(砂型或金属型模具),同步压力一般在300~1000kPa。本发明仅有一个下压力罐,铸型直接暴露在大气中,结晶保压压力即可高达160~1000kPa,充分利用现有铝合金车轮金属型低压铸造成熟的模具结构、充型和冷却系统等工艺技术,继承了现有低压铸造机宽敞的四立柱支架结构和操作方便、容易实现自动化等特点。附图说明图1是铝合金车轮典型结构特征图。图2A是本发明的改进的压力-时间曲线图。图2B是对比实施例1制得的26吋A356合金车轮的力学性能图。图2C是实施例1制得的26吋A356合金车轮的力学性能图。具体实施方式下面将结合附图和实施例对本发明做进一步的详细说明。一般地,金属型低压铸造方法制备铝合金车轮,通常浇口放在轮心部位。充型过程中,高温铝液自轮心经轮辐流向外轮缘,最后达到内轮缘。为了实现良好的补缩效果,必须控制铝合金车轮凝固的过程,实现顺序凝固,即首先由轮辋上下两端(即内轮缘、外轮缘)往中间轮辋轮辐过渡部位顺序凝固,随后轮辐部位由外向内顺序凝固,轮心部位最后凝固。一般地,凝固过程包括开始凝固、凝固中和凝固结束。对于常用的15吋~26吋铝合金汽车车轮,选用金属型低压铸造生产工艺;冷却方式为风冷、风冷与雾冷混合、或者风冷与水冷混合;模具选用金属铸型,可以是由上模、下模和四个侧模或者两个侧模组成的金属型模具。内外轮缘一般在充型完成后8~40后凝固结束,轮辋部位一般在充型完成后12~130s后凝固结束,轮辐轮辋过渡部位一般在充型完成后30~200s后凝固结束,轮心部位一般在充型完成后90~500s后凝固结束。为了进一步降低金属型低压铸造铝合金车轮的缩孔缩松等铸造缺陷、提高铝合金车轮的组织致密度和力学性能,本发明提出了一种铝合金车轮金属型低压铸造成型用结晶增压方法,所述结晶增压方法按照内外轮缘凝固时间分阶段增大结晶增压压力。所述的结晶增压方法充分考虑了铝合金车轮结构特征、冷却条件和模具结构特点。铝合金车轮结构特征如图1所示。本发明提出的是一种按照内外轮缘凝固时间分阶段增大结晶增压压力的金属型低压铸造方法来制备铝合金车轮,(即一种铝合金车轮金属型低压铸造成型用结晶增压方法)本发明方法包括有:升液阶段、充型阶段、结晶增压阶段、结晶保压阶段和卸压放气阶段。具体地说:步骤一,升液阶段;调节升液阶段的压力为18~21kPa,升液速度为1.8~2.2kPa/s;将18~21kPa的压缩空气通入密封的保温炉中,铝液在压力的作用下沿升液管平稳上升至铸型浇口处,并流入铸型中;步骤二,充型阶段;调节充型阶段的充型压力为30~35kPa,充型速度为0.4~1.0kPa/s,使铝液从浇口进入型腔,直至将型腔全部充满;步骤三,结晶增压阶段;经步骤二后使铝液完全充满铸型后,进入结晶增压阶段:(A)充型阶段结束,开始增大结晶增压压力;(B)内轮缘、外轮缘在充型完成后8~40s凝固结束;(C)内外轮缘凝固结束时,结晶增压压力增大到80~150kPa;(D)内外轮缘凝固结束后,结晶增压压力快速增大到160~1000kPa,增压速度为10~40kPa/s:步骤四,结晶保压阶段;在压力达到160~1000kPa后,进入结晶保压阶段;(A)轮辋部位在充型完成后12~130s后凝固结束;(B)轮辐轮辋过渡部位在充型完成后30~260s后凝固结束;(C)轮心部位在充型完成后90~500s后凝固结束,继续保压10~60s;步骤五,卸压放气阶段;经步骤四后,待铝合金车轮凝固完毕,解除保温炉内的气体压力,使升液管和浇道口未凝固的铝液流回到保温炉中。实施例126吋,A356合金车轮。H13钢模具,上模+下模+4侧模结构,直接暴露在大气中。浇注温度为710℃,模具初始温度为400℃,冷却方式为风冷。采用金属型低压铸造成型用结晶增压方法制备铝合金车轮的步骤有:步骤一,升液阶段;在升液压力为19kPa、升液速度为1.9kPa/s的条件下,铝液沿升液管平稳上升至铸型浇口处,并流入铸型中;步骤二,充型阶段;在充型压力为34kPa、充型速度为0.85kPa/s的条件下,铝液从浇口充入型腔,直至型腔全部充满;步骤三,结晶增压阶段;在本发明中,改进的结晶快速增压压力-时间曲线如图2A所示。(A)充型阶段结束,开始增大结晶增压压力;(B)内轮缘在充型完成后33s凝固结束,外轮缘在充型完成后38s凝固结束;(C)内外轮缘凝固结束时,结晶增压压力增大到120kPa;(D)内外轮缘凝固结束后,结晶增压压力快速增大到1000kPa,增压速度为20kPa/s:步骤四,结晶保压阶段;在压力达到1000kPa后,进入结晶保压阶段;(A)轮辋部位在充型完成后127s后凝固结束;(B)轮辐轮辋过渡部位在充型完成后260s后凝固结束;(C)轮心部位在充型完成后400s后凝固结束,继续保压60s;步骤五,卸压放气阶段;经步骤四后,解除保温炉内的气体压力,使升液管和浇道口未凝固的铝液流回到保温炉。对比实施例1采用与实施例1相同的步骤一至步骤二,不同之处在于步骤三采用传统的结晶增压方式,只有一个增压阶段,且结晶增压压力值为80kPa,然后开始结晶保压460s,随后解除保温炉内的气体压力,使升液管和浇道口未凝固的铝液流回到保温炉。采用Instron8801型号拉伸试验机测量,对比实施例1制得的26吋A356合金车轮轮辐部位的力学性能:如图2B所示,其抗拉强度、屈服强度和延伸率分别达到217.8MPa、150.4MPa、4.1%。采用Instron8801型号拉伸试验机测量,实施例1制得的26吋A356合金车轮轮辐部位的力学性能:如图2C所示,车轮轮辐部位的抗拉强度、屈服强度和延伸率分别达到289.7MPa、218.6MPa、5.9%。通过对比图2B与图2C可知,经本发明方法处理后的车轮轮辐部位的抗拉强度、屈服强度和延伸率提高了33.0%、45.3%和43.9%,且成品车轮轮辐部位平均壁厚可减少2.2mm,取得了良好的轻量化效果。实施例220吋,A356合金铸旋车轮。H13钢模具,上模+下模+4侧模结构,直接暴露在大气中。浇注温度为700℃,模具初始温度为350℃,冷却方式为风雾混合冷却。采用金属型低压铸造成型用结晶快速保压增压方法制备铝合金车轮的步骤有:步骤一,升液阶段;在升液压力为20kPa、升液速度为2.0kPa/s的条件下,铝液沿升液管平稳上升至铸型浇口处,并流入铸型中;步骤二,充型阶段;在充型压力为30kPa、充型速度为1.0kPa/s的条件下,铝液从浇口充入型腔,直至型腔全部充满;步骤三,结晶增压阶段;(A)充型阶段结束,开始增大结晶增压压力;(B)内轮缘在充型完成后29s凝固结束,外轮缘在充型完成后31s凝固结束;(C)内外轮缘凝固结束时,结晶增压压力增大到150kPa;(D)内外轮缘凝固结束后,结晶增压压力快速增大到500kPa,增压速度为35kPa/s:步骤四,结晶保压阶段;在压力达到500kPa后,进入结晶保压阶段;(A)轮辋部位在充型完成后58s凝固结束;(B)轮辐轮辋过渡部位在充型完成后164s凝固结束;(C)轮心部位在充型完成后215s凝固结束,继续保压30s;步骤五,卸压放气阶段;经步骤四后解除保温炉内的气体压力,使升液管和浇道口未凝固的铝液流回到保温炉。对比实施例2采用与实施例2相同的步骤一至步骤二,不同之处在于步骤三采用传统的结晶增压方式,只有一个增压阶段,且结晶增压压力值为80kPa,然后开始结晶保压230s,随后解除保温炉内的气体压力,使升液管和浇道口未凝固的铝液流回到保温炉。采用Instron8801型号拉伸试验机测量,对比实施例2制得的20吋A356合金铸旋车轮轮辐部位的力学性能:其抗拉强度、屈服强度和延伸率分别达到217.5MPa、155.6MPa、4.2%。采用Instron8801型号拉伸试验机测量,实施例2制得的20吋A356合金铸旋车轮轮辐部位的力学性能:车轮轮辐部位的抗拉强度、屈服强度和延伸率分别达到296.1MPa、227.5MPa、6.5%。经本发明方法处理后的车轮轮辐部位的抗拉强度、屈服强度和延伸率提高了36.1%、46.2%及54.8%,且成品车轮轮辐部位平均壁厚可减少2.6mm,取得了良好的轻量化效果。实施例315吋,A356合金车轮。H13钢模具,上模+下模+2侧模结构,直接暴露在大气中。浇注温度为710℃,模具初始温度为400℃,冷却方式为风冷以及水冷。采用金属型低压铸造成型用结晶快速保压增压方法制备铝合金车轮的步骤有:步骤一,升液阶段;在升液压力为21kPa、升液速度为2.1kPa/s的条件下,、铝液沿升液管平稳上升至铸型浇口处,并流入铸型中;步骤二,充型阶段;在充型压力为32kPa、充型速度为0.55kPa/s的条件下,铝液从浇口充入型腔,直至型腔全部充满;步骤三,结晶增压阶段;(A)充型阶段结束,开始增大结晶增压压力;(B)内轮缘在充型完成后9s凝固结束,外轮缘在充型完成后9s凝固结束;(C)内外轮缘凝固结束时,结晶增压压力增大到150kPa;(D)内外轮缘凝固结束后,结晶增压压力快速增大到350kPa,增压速度为40kPa/s:步骤四,结晶保压阶段;在压力达到350kPa后,进入结晶保压阶段;(A)轮辋部位在充型完成后16s凝固结束;(B)轮辐轮辋过渡部位在充型完成后35s凝固结束;(C)轮心部位在充型完成后98s凝固结束,继续保压60s;步骤五,卸压放气阶段;经步骤四后解除保温炉内的气体压力,使升液管和浇道口未凝固的铝液流回到保温炉。对比实施例3采用与实施例3相同的步骤一至步骤三,不同之处在于步骤三采用传统的结晶增压方式,只有一个增压阶段,且结晶增压压力值为80kPa,此后结晶保压150s,随后解除保温炉内的气体压力,使升液管和浇道口未凝固的铝液流回到保温炉。采用Instron8801型号拉伸试验机测量,对比实施例3制得的15吋A356合金车轮轮辐部位的力学性能:其抗拉强度、屈服强度和延伸率分别达到231.5MPa、146.8MPa、4.4%。采用Instron8801型号拉伸试验机测量,实施例3制得的15吋A356合金车轮轮辐部位的力学性能:车轮轮辐部位的抗拉强度、屈服强度和延伸率分别达到300.9MPa、212.8MPa及6.7%。经本发明方法处理后的车轮轮辐部位的抗拉强度、屈服强度和延伸率提高了30.0%、45.0%及52.3%,且成品车轮轮辐部位平均壁厚可减少1.6mm,取得了良好的轻量化效果。