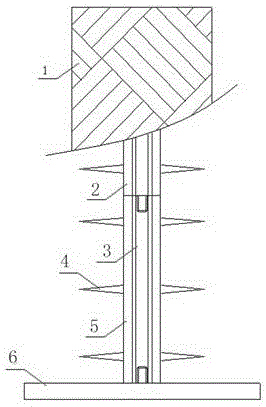
本发明属于微连续流体器件领域,尤其涉及一种用于液体酸烷基化反应的微通道反应器内构件及其装填方法。
背景技术:
:微通道反应器是一种借助于特殊微加工技术的新型反应器,具有返混小、传质传热效率高、反应时间与反应温度便于控制、易于放大等特征。但微通道加工难度大,制作成本高,因此开发简单的微通道构件加工方法,降低微通道反应器的成本是急需要解决的难题。CN105396528A公开了一种具有防腐性能的微通道反应器,该反应器结构紧凑、密封简单、加工难度小、换热和反应效率高、可移动、可实现成套设备微型化。CN105126721A公开一种带有冷却系统的非叠层结构微反应器,可进行拆卸清洗和系统冷却,有效防止微反应器微通道的堵塞和微反应器装置的局部过热。CN102421515A公开了一种送液量小、混合性能高的微反应器,通过至少一次的流体分割混合来实现流体的均匀混合与快速反应。已经公开的专利致力于增加防腐性能、提高传热传质速率及强化流体的混合与分布,未能有效的降低微通道反应器的加工成本。技术实现要素:针对微通道反应器制作成本高的缺陷,本发明公开了一种用于液体酸烷基化反应的微通道反应器内构件及其装填方法,可精准控制反应温度,提高传质速率与宏观反应速率。微通道构件具有耐酸,耐腐蚀性能,可实现高效、节能、安全、低碳和环保的连续化生产。为解决上述技术问题,本发明是这样实现的。用于液体酸烷基化反应的微通道反应器内构件,它包括纤维填料、支撑轴Ⅰ、轴键、穿钉、支撑轴Ⅱ及支撑板;所述纤维填料缠绕于支撑轴Ⅰ及支撑轴Ⅱ之上。在所述支撑轴Ⅰ上沿侧面垂直开设支撑轴Ⅰ键槽;所述轴键与支撑轴Ⅰ键槽固定嵌合;在所述支撑轴Ⅰ上沿纵向开有支撑轴Ⅰ水平孔;所述穿钉与支撑轴Ⅰ水平孔串接。在所述支撑轴Ⅱ上沿侧面垂直开设支撑轴Ⅱ键槽;所述轴键与支撑轴Ⅱ键槽固定嵌合;在所述支撑轴Ⅱ上沿纵向开有支撑轴Ⅱ水平孔;所述穿钉与支撑轴Ⅱ水平孔串接。所述支撑轴Ⅰ的一端部与支撑轴Ⅱ的一端部纵向固定相接;在所述支撑轴Ⅱ另一端水平固定设有支撑板;在所述支撑板上设有筛孔。作为一种优选方案,所述支撑轴Ⅰ为实心轴,高度为200~2000mm,外径为10~200mm;支撑轴Ⅰ一端设有内螺母Ⅰ,另一端设有外螺杆;内螺母Ⅰ直径为0.1~0.5d,长度为5~30mm;外螺杆直径为0.1~0.5d,长度为5~30mm;所述支撑轴Ⅰ键槽横截面为梯形;键槽深度0.15~0.4d;短边宽度0.05~0.4d;长边宽度0.1~0.55d。所述支撑轴Ⅱ为实心轴,高度为200~2000mm,外径为10~200mm;支撑轴Ⅱ两端设有内螺母Ⅱ;内螺母Ⅱ直径0.1~0.5d,长度为5~30mm;所述支撑轴Ⅱ键槽横截面为梯形;键槽深度0.15~0.4d;短边宽度0.05~0.4d;长边宽度0.1~0.55d;所述支撑轴Ⅱ一端内螺母Ⅱ与支撑轴Ⅰ的外螺杆固定相接;所述支撑轴Ⅱ另一端内螺母Ⅱ与支撑板上的螺杆固定相接;其中d为支撑轴Ⅰ的外径。进一步地,本发明所述纤维填料具有致密孔隙状结构;骨架密度为0.1~3.0g/mL,平均直径为10~240μm,比表面积为0.1~30m2/g。进一步地,本发明所述纤维填料可采用玻璃纤维、聚乙烯纤维、聚丙烯纤维、丙纶纤维、芳纶纤维、聚苯硫醚纤维或耐酸聚酰亚胺纤维中的一种或两种以上的混合材料。进一步地,本发明所述支撑板开孔率为5%~25%;支撑板中心垂直向上设置一个螺杆;螺杆高度及直径尺寸与支撑轴Ⅰ上外螺杆相同。上述用于液体酸烷基化反应的微通道反应器内构件的装填方法,可按如下步骤进行。A、纤维填料膨化后编制成宽度与支撑轴Ⅰ高度相同的纤维布;利用轴键及支撑轴Ⅰ键槽,将纤维布固定在支撑轴Ⅰ上。B、顺时针旋转支撑轴Ⅰ形成纤维柱,并使用纤维捻将缠绕的纤维柱临时束缚;支撑轴Ⅰ每旋转180°,将穿钉从支撑轴Ⅰ的一侧移动到另一侧。C、纤维填料膨化后编制成宽度与支撑轴Ⅱ高度相同的纤维布;利用轴键及支撑轴Ⅱ键槽,将纤维布固定在支撑轴Ⅱ上。D、顺时针旋转支撑轴Ⅱ形成纤维柱,并使用纤维捻将缠绕的纤维柱临时束缚;支撑轴Ⅱ每旋转180°,将穿钉从支撑轴Ⅱ的一侧移动到另一侧。E、将两个纤维柱连接,进一步将纤维柱与支撑板连接,套入微通道反应器外壳,同时解除纤维捻的束缚,逆时针旋转至纤维填料与微通道反应器的外壳紧密接触,完成装填。通过改变纤维柱的填充率,可灵活的调控反应过程的压降与物料停留时间。若异丁烷或注入反应器的惰性制冷剂的饱和蒸汽压接近反应器的平均压力,此时反应器压降的变化,可用于调整异丁烷或惰性取热介质的汽化量,精准调控反应温度。与现有技术相比,本发明具有的优点和积极效果是:使用模块化的纤维柱作为微通道构件,降低了微通道反应器的制作成本;反应物料与催化剂实现膜接触,提高传质速率与宏观反应速率;通过改变纤维柱的填充率,可灵活的调控反应过程的压降与物料停留时间,并精准控制反应温度。本发明的微通道构件具有耐酸,耐腐蚀性能,可实现高效、节能、安全、低碳和环保的连续化生产。附图说明下面结合附图和具体实施方式对本发明作进一步说明。本发明的保护范围不仅局限于下列内容的表述。图1为本发明用于液体酸烷基化反应的微通道反应器内构件整体结构示意图。图2为本发明支撑轴Ⅰ剖视图。图3为本发明图2中A-A向剖视图。图4为本发明轴键剖视图。图5为本发明图4中轴键俯视图。图6为本发明支撑板整体结构示意图。图7为本发明图6中支撑板俯视图。图8为本发明支撑轴Ⅱ剖视图。图9为本发明图8中A-A向剖视图。图中:1、纤维填料;2、支撑轴Ⅰ;3、轴键;4、穿钉;5、支撑轴Ⅱ;6、支撑板;2-1、外螺杆;2-2、支撑轴Ⅰ水平孔;2-3、内螺母Ⅰ;2-4、支撑轴Ⅰ键槽;2-5、支撑轴Ⅰ键槽内螺纹;3-1、轴键螺孔;5-1、内螺母Ⅱ;5-2、支撑轴Ⅱ水平孔;5-3、内螺母Ⅱ;5-4、支撑轴Ⅱ键槽;5-5、支撑轴Ⅱ键槽内螺纹;6-1、筛孔;6-2、螺杆。具体实施方式如图所示,用于液体酸烷基化反应的微通道反应器内构件,包括纤维填料1、支撑轴Ⅰ2、轴键3、穿钉4、支撑轴Ⅱ5及支撑板6;所述纤维填料1缠绕于支撑轴Ⅰ2及支撑轴Ⅱ5之上。在所述支撑轴Ⅰ2上沿侧面垂直开设支撑轴Ⅰ键槽2-4;所述轴键3与支撑轴Ⅰ键槽2-4固定嵌合;在所述支撑轴Ⅰ2上沿纵向开有支撑轴Ⅰ水平孔2-2;所述穿钉4与支撑轴Ⅰ水平孔2-2串接。在所述支撑轴Ⅱ5上沿侧面垂直开设支撑轴Ⅱ键槽5-4;所述轴键3与支撑轴Ⅱ键槽5-4固定嵌合;在所述支撑轴Ⅱ5上沿纵向开有支撑轴Ⅱ水平孔5-2;所述穿钉4与支撑轴Ⅱ水平孔5-2串接。本发明所述支撑轴Ⅰ2的一端部与支撑轴Ⅱ5的一端部纵向固定相接;在所述支撑轴Ⅱ5另一端水平固定设有支撑板6;在所述支撑板6上设有筛孔6-1。本发明所述支撑轴Ⅰ2为实心轴,高度为200~2000mm,外径为10~200mm;支撑轴Ⅰ2一端设有内螺母Ⅰ2-3,另一端设有外螺杆2-1;内螺母2-3直径为0.1~0.5d,长度为5~30mm;外螺杆直径为0.1~0.5d,长度为5~30mm;所述支撑轴Ⅰ键槽2-4横截面为梯形;键槽深度0.15~0.4d;短边宽度0.05~0.4d;长边宽度0.1~0.55d。本发明所述支撑轴Ⅱ5为实心轴,高度为200~2000mm,外径为10~200mm;支撑轴Ⅱ5两端设有内螺母Ⅱ;内螺母Ⅱ直径0.1~0.5d,长度为5~30mm;所述支撑轴Ⅱ键槽5-4横截面为梯形;键槽深度0.15~0.4d;短边宽度0.05~0.4d;长边宽度0.1~0.55d;所述支撑轴Ⅱ5一端内螺母Ⅱ5-3与支撑轴Ⅰ2的外螺杆2-1固定相接;所述支撑轴Ⅱ5另一端内螺母Ⅱ5-1与支撑板6上的螺杆6-2固定相接;其中d为支撑轴Ⅰ的外径。本发明所述纤维填料1具有致密孔隙状结构;骨架密度为0.1~3.0g/mL,平均直径为10~240μm,比表面积为0.1~30m2/g。本发明所述纤维填料1采用玻璃纤维、聚乙烯纤维、聚丙烯纤维、丙纶纤维、芳纶纤维、聚苯硫醚纤维或耐酸聚酰亚胺纤维中的一种或两种以上的混合材料。本发明所述支撑板6开孔率为5%~25%;支撑板6中心垂直向上设置一个螺杆6-2;螺杆6-2高度及直径尺寸与支撑轴Ⅰ2上外螺杆2-1相同。上述用于液体酸烷基化反应的微通道反应器内构件的装填方法,可按如下步骤进行。A、纤维填料1膨化后编制成宽度与支撑轴Ⅰ2高度相同的纤维布;利用轴键3及支撑轴Ⅰ键槽2-4,将纤维布固定在支撑轴Ⅰ2上。B、顺时针旋转支撑轴Ⅰ2形成纤维柱,并使用纤维捻将缠绕的纤维柱临时束缚;支撑轴Ⅰ2每旋转180°,将穿钉4从支撑轴Ⅰ2的一侧移动到另一侧。C、纤维填料1膨化后编制成宽度与支撑轴Ⅱ5高度相同的纤维布;利用轴键3及支撑轴Ⅱ键槽5-4,将纤维布固定在支撑轴Ⅱ5上。D、顺时针旋转支撑轴Ⅱ5形成纤维柱,并使用纤维捻将缠绕的纤维柱临时束缚;支撑轴Ⅱ5每旋转180°;将穿钉4从支撑轴Ⅱ5的一侧移动到另一侧。E、将两个纤维柱连接,进一步将纤维柱与支撑板连接,套入微通道反应器外壳,同时解除纤维捻的束缚,逆时针旋转至纤维填料与微通道反应器的外壳紧密接触,完成装填。本发明纤维填料具有致密孔隙状结构,可以是玻璃纤维、聚乙烯纤维、聚丙烯纤维、丙纶纤维、芳纶纤维、聚苯硫醚纤维或耐酸聚酰亚胺纤维中的一种或几种。纤维填料耐腐蚀,适用于有强酸参与的化学反应。纤维填料具有亲酸疏烃性能,纤维填料外表面形成酸膜,反应物在酸膜外流动,酸粘度相对较大,而反应物粘度相对较小,反应物与酸之间存在速度差,液液两相之间形成内摩擦力将酸膜变薄实现膜接触,增大传质面积,提高传质效率。纤维填料骨架密度为0.1~3.0g/mL,平均直径为10~240μm,比表面积为0.1~30m2/g。使用纤维填料替代微加工技术,保留微通道反应器诸多优点的同时降低制造成本。本发明支撑轴Ⅰ2为实心轴,高度为200~2000mm,外径为10~200mm。支撑轴底部设有外螺杆2-1,顶部设有内螺母Ⅰ2-3,外螺杆与内螺母Ⅰ直径均为0.1~0.5d,长度均为5~30mm,通过螺纹,可实现多根支撑轴Ⅰ的串联连接,通过串联连接数目的变化,可能活调节微通道反应器的高度。支撑轴Ⅰ沿侧面垂直开设一条梯形支撑轴Ⅰ键槽2-4,键槽沿纵向设置2~4个支撑轴Ⅰ键槽内螺纹2-5,用于固定纤维填料的始端,键槽与支撑轴(不包括支撑轴外螺杆)等高,键槽深度0.15~0.4d,短边宽度0.05~0.4d,长边宽度0.1~0.55d。支撑轴Ⅰ沿纵向开若干支撑轴Ⅰ水平孔2-2,用于置放穿钉,开孔穿过轴心但不通过键槽,孔径为3~20mm,孔间距为100~500mm。本发明轴键为梯形,外形与支撑轴上键槽相对应,轴键与键槽等高,轴键长短边宽度及高度尺寸分别略小于与之对应的键槽长短边宽度及深度,差值分别为2~5mm。轴键沿纵向设置2~4个轴键螺孔3-1,轴键螺孔位置与键槽上内螺纹的位置相对应,纤维填料始端夹在轴键与键槽之间,通过螺栓将三者固定。本发明穿钉直径略小于支撑轴上水平孔孔径,差值为2~5mm,长度略小于微通道反应器外壳内径,差值为2~20mm;穿钉两端打磨锋利,穿过支撑轴中的水平孔与纤维填料,防止纤维填料塌陷。本发明支撑轴Ⅱ为实心轴,高度为200~2000mm,外径为10~200mm。支撑轴两端设有内螺母,螺母直径0.1~0.5d,螺母长度为5~30mm,内螺母Ⅱ5-3与支撑轴Ⅰ外螺杆2-1连接,内螺母Ⅱ5-1与支撑板螺杆6-2连接。支撑轴Ⅱ沿侧面垂直开设一条梯形支撑轴Ⅱ键槽5-4,键槽沿纵向设置2~4个支撑轴Ⅱ键槽内螺纹5-5,用于固定纤维填料的始端,键槽与支撑轴等高,键槽深度0.15~0.4d,短边宽度0.05~0.4d,长边宽度0.1~0.55d。支撑轴Ⅱ沿纵向开若干支撑轴Ⅱ水平孔5-2,用于置放穿钉,开孔穿过轴心但不通过键槽,孔径为3~20mm,孔间距为100~500mm。本发明支撑板为筛板,筛板筛孔6-1开孔率为5%~25%,支撑板能够支撑纤维填料,同时对向下流动的流体起到二次分布的作用。筛板中心垂直向上设置一个螺杆6-2,螺杆高度及直径与内螺母Ⅱ5-1相同,螺杆用于与支撑轴Ⅱ之间的连接。按照微通道反应器填充容重的要求,称取一定重量的膨化纤维填料,加工制成宽度与支撑轴Ⅰ高度相同的纤维布,纤维布厚度为0.5~20mm。将纤维布始端置于支撑轴Ⅰ键槽中,将轴键卡在键槽内,并使用螺栓将支撑轴Ⅰ、纤维布始端及轴键固定在一起。使用“十字”扳手将支撑轴Ⅰ两端固定后置于架台之上,匀速顺时针旋转支撑轴,将纤维填料布均匀缠绕到支撑轴Ⅰ上形成纤维柱。旋转过程中要对纤维布施加一定阻力,确保缠绕后纤维柱的外径略小于微通道反应器外壳内径。每旋转180°,将穿钉从轴的一侧移动到另一侧,确保穿钉穿过每一层纤维布,最终置于轴心处。纤维布全部缠绕之后,使用纤维捻对纤维柱进行束缚,保持形状不发生变化。本发明支撑轴Ⅱ采用与支撑轴Ⅰ相同的方法缠绕纤维填料。借助支撑轴Ⅰ底部外螺杆2-1与支撑轴Ⅱ顶部内螺母Ⅱ5-3,将两个支撑轴连接,进一步利用支撑轴Ⅱ底部内螺母Ⅱ5-1与支撑板螺杆6-2,将支撑轴与支撑板连接。将反应器外壳套入带有支撑板的纤维柱,同时解除纤维捻的临时束缚,并逆时针旋转至纤维填料与微通道反应器的外壳紧密接触,完成装填,进一步加装顶部封头与底部封头之后即构成微通道反应器。在本发明微通道内构件的反应器内,以硫酸为催化剂,以异丁烷或丙烷作为冷剂进行烷基化反应。具体反应条件见表1,反应结果见表2。比较例1~2。比较例1采用常规的内部设置制冷管束的卧式机械搅拌反应器,比较例2采用常规微通道反应器(微通道构件同实施例1),反应条件参见表1,反应结果参见表2。表1实施例与比较例烷基化反应主要条件。实施例1比较例1比较例2烷烯摩尔比9:19:19:1酸烃体积比1:11:11:1反应温度,℃0℃4℃4℃反应压力,MPa0.30.30.3停留时间,min102020表2实施例与比较例烷基化反应结果。实施例1比较例1比较例2丁烯转化率,mol%100100100酸耗,kg酸/t烷基化油436574烷基化油辛烷值(马达法)95.492.793.1以上所述仅为本发明较佳的实施例而已,并不用以限制本发明,凡在发明的精神和原则之内所做的任何修改,等同替换和改进等,均应包含在本发明保护范围之内。当前第1页1 2 3