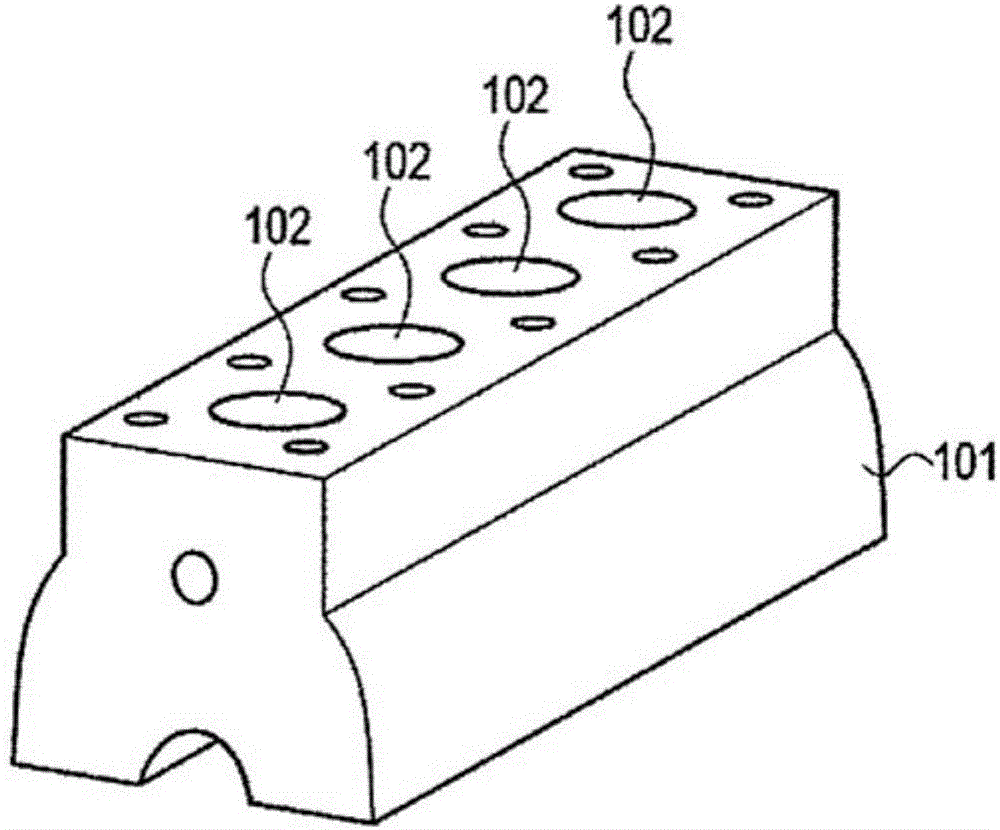
本发明涉及一种缺陷检查装置以及生产系统。
背景技术:
已知一种喷涂技术(喷涂孔),其在搭载于汽车等的气缸体的缸孔内表面喷涂金属或陶瓷而形成涂层(喷涂层),通过随后的珩磨加工而形成平滑的滑动面。
喷涂层是将熔滴层叠多层而形成的,因此通常成为含有较多气孔、氧化铁等的细微缺陷的多孔构造。因此,在进行喷涂后的珩磨等后加工时,存在喷涂层的表层脱落而产生微小的表面缺陷的问题。另外,在缸孔内表面存在铸造孔的情况下,也产生表面缺陷而未正常地形成喷涂层。这些表面缺陷作为机油积存处起作用,有利于提高与活塞的润滑性,但另一方面,如果体积过大则机油消耗量恶化。因此,优选对缸孔内表面的表面缺陷进行检查,并规定表面缺陷的体积的上限。
作为缸孔内表面的表面缺陷的检查方法,通常的方法是利用CCD照相机等对缸孔内表面进行拍摄而获取二维图像,根据二维图像对表面缺陷的数量、尺寸进行检测(例如,参照专利文献1)。
专利文献1:日本特开平11-23477号公报
技术实现要素:
然而,在专利文献1中,根据二维图像对表面缺陷的数量、尺寸进行检测,但未检测与缺陷的深度相关的信息。因此,难以高精度地测定缸孔内表面的表面缺陷的体积。
本发明就是鉴于上述课题而提出的,其目的在于提供一种能够高精度地测定表面缺陷的体积的缺陷检查装置以及生产系统。
本发明的一个方式涉及的缺陷检查装置以及生产系统的特征在于,对检查对象的图像进行拍摄,针对图像利用互不相同的第1以及第2二值化阈值而进行第1以及第2二值化处理,由此针对图像中的同一缺陷而计算出第1以及第2尺寸,对第2尺寸相对于第1尺寸的第1比率进行计算,根据第1比率而判定缺陷的深度。
附图说明
图1是表示本发明的实施方式涉及的生产系统的结构的一个例子的框图。
图2是表示本发明的实施方式涉及的气缸体的一个例子的概略图。
图3是表示本发明的实施方式涉及的加工装置的结构的一个例子的概略图。
图4是表示缸孔内表面的包含表面缺陷在内的喷涂层的一个例子的剖面图。
图5是表示本发明的实施方式涉及的拍摄装置的结构的一个例子的概略图。
图6是表示像素的光量与缺陷的深度之间的关系的一个例子的图表。
图7是表示二值化阈值与检测出的缺陷的长度之间的关系的一个例子的图表。
图8是表示二值化阈值与检测出的彼此深度不同的缺陷的长度之间的关系的一个例子的图表。
图9是表示本发明的实施方式涉及的表面缺陷检查方法的一个例子的流程图。
图10(a)是表示第1变形例涉及的二值化阈值与缺陷的尺寸之间的关系的图表。图10(b)是表示第1变形例涉及的缺陷的深度的判定结果的图表。
图11是表示第1变形例涉及的表面缺陷检查方法的一个例子的流程图。
图12(a)是表示第2变形例涉及的二值化阈值与缺陷的尺寸之间的关系的图表。图12(b)是表示第2变形例涉及的缺陷的深度的判定结果的图表。
图13是表示第2变形例涉及的表面缺陷检查方法的一个例子的流程图。
具体实施方式
参照附图对实施方式进行说明。在附图的记载中,对相同部分标注相同标号而省略说明。
[生产系统以及缺陷检查装置]
如图1所示,本发明的实施方式涉及的生产系统具备缺陷检查装置1以及加工装置4。缺陷检查装置1具备控制装置2以及拍摄装置3。
作为本发明的实施方式涉及的缺陷检查装置1的检查对象的一个例子,对汽车等的发动机的气缸体进行说明。如图2所示,气缸体101具有用于对活塞进行收容的圆筒形孔即多个缸孔102。
作为加工装置4,例如可以使用等离子喷涂装置。如图3所示,加工装置(等离子喷涂装置)4具备:喷枪主体41;以及喷枪42,其在喷枪主体41的下方凸出地设置。在喷涂孔中,喷枪主体41沿着箭头A方向移动而进入至气缸体101的缸孔102的圆筒内,沿圆周方向B进行旋转。与此同时,从喷枪42的前端部分将金属或者陶瓷的喷流喷射至气缸体101的缸孔102的内表面,形成喷涂层。此外,作为加工装置4,可以是珩磨加工机等能够对喷涂层的表面缺陷施加影响的加工装置,也可以具有多种加工装置。作为加工装置4,能够根据检查对象而适当使用对表面缺陷施加影响的装置。
喷涂层是将熔滴层叠多层而形成的,因此通常成为含有较多气孔、氧化铁等的细微缺陷的多孔构造。因此,在进行喷涂后的珩磨等后加工时,如图4示意性所示,喷涂层103的表层的一部分脱落,产生相对于表面103a而凹陷的微小的表面缺陷(凹坑)104。另外,在缸孔102的内表面存在铸造孔的情况下,也不会在铸造孔的表面正常地形成喷涂层,而是产生相对于表面103a而凹陷的表面缺陷(气孔)。这些表面缺陷作为机油积存处起作用,有利于提高与活塞的润滑性,但另一方面,如果体积过大则机油消耗量恶化。因此,优选对喷涂层的表面缺陷进行检查,并针对表面缺陷的体积的总和而规定上限。
作为喷涂层的表面缺陷,如上所述,主要列举因后加工引起的凹坑和因铸造孔引起的气孔。通常,气孔的直径(最大长度)呈现与凹坑的直径(最大长度)等同或者大于或等于凹坑的直径的倾向,气孔的深度呈现比凹坑的深度深5倍~10倍左右的倾向。此外,作为喷涂层103的表面缺陷,并不限定于凹坑以及气孔,包含相对于表面103a凹陷的部分。
图1所示的拍摄装置3对检查对象的表面进行拍摄,获取二维图像(浓淡图像)。拍摄装置3例如如图5所示,具有驱动部30、安装于驱动部30的光源31和反射镜32、以及在驱动部30的上方固定的拍摄部33。驱动部30进入至作为检查对象的缸孔102的圆筒内,沿圆周方向C进行旋转驱动。光源31将光向缸孔102的内表面照射。反射镜32对来自检查对象的反射光进行反射并向拍摄部33引导。拍摄部33是CCD照相机等,通过接收来自反射镜32的反射光而对检查对象的表面进行拍摄,获取二维图像。此外,在本发明的实施方式中,示出能够对缸孔102等圆筒状部件的内表面进行拍摄的拍摄装置3的一个例子,但拍摄装置3的结构能够根据检查对象而适当变更。
由拍摄装置3得到的二维图像例如是8位的灰度图像,以从黑(0)至白(255)的光量而规定各像素。图6表示喷涂层的表面缺陷的深度与像素的光量之间的关系的一个例子。如图6所示,在检查对象的不存在表面缺陷的正常的部位,来自检查对象的反射光相对变亮,图像中的像素的光量变多。另一方面,在检查对象的表面缺陷的部位,来自检查对象的反射光相对变暗,图像中的像素的光量变少。另外,表面缺陷越深,则图像中的像素的光量越小。
图1所示的控制装置2由中央处理装置(CPU)、RAM、ROM、硬盘等构成。控制装置2从功能上具有二值化处理部11、比率计算部12、深度判定部13、体积计算部14以及是否合格判定部15。
二值化处理部11针对由拍摄部33拍摄的二维图像进行二值化处理。二值化处理是利用二值化阈值将二维图像中的具有灰度图像的光量的各像素变换为白或者黑这2个灰阶的处理。如图6所示,在像素的光量大于或等于规定的二值化阈值Th的情况下将像素变换为白。另一方面,在像素的光量小于二值化阈值的情况下,将像素变换为黑。因此,二值化阈值Th越大,则黑的区域越增大。
图7表示在使二值化阈值发生变化时检测出的喷涂层的表面缺陷的尺寸(长度)的变化的一个例子。如图7所示,二值化阈值越大,则图像中的与黑的区域的集合体相当的缺陷的尺寸检测为越大。在图7中,还示意性示出使用了互不相同的二值化阈值的二值化处理后的图像I1~I3。可知缺陷的尺寸以图像I1、I2、I3的顺序变小。另外,在图7的一个例子中,二值化阈值与表面缺陷的尺寸之间的变化作为整体为非线性的,如果减小二值化阈值,则在超过拐点P之前表面缺陷的尺寸也大致成正比地缓慢变小,但如果超过拐点P则表面缺陷的尺寸急剧变小。
这里,二值化处理部11针对由拍摄部33拍摄的二维图像而分别使用互不相同的第1以及第2二值化阈值Th1、Th2进行2次(第1以及第2)二值化处理。第1以及第2二值化阈值Th1、Th2可以根据产品、缺陷的种类等而适当设定。第1二值化阈值Th1例如设定为100。第2二值化阈值Th2比第1二值化阈值Th1小,例如设定为50。第1以及第2二值化阈值Th1、Th2例如预先存储于控制装置2的存储器,并被适当读出。
二值化处理部11根据第1二值化处理后的图像以及第2二值化处理后的图像而分别检测出与黑的区域的集合体相当的缺陷,针对同一缺陷而分别计算出缺陷的尺寸。这里,缺陷的尺寸包含缺陷的面积或者长度中的至少一者。作为缺陷的长度,例如对缺陷的最大长度(长直径)进行计算。作为缺陷的面积,例如对缺陷的最大长度(长直径)的外接圆的面积进行计算。第1二值化处理后的图像中的缺陷和第2二值化处理后的图像中的缺陷能够利用位置坐标而将同一缺陷关联。此外,由于第1二值化阈值Th1比第2二值化阈值Th2大,因此通过利用了第1二值化阈值Th1的第1次二值化处理而得到的缺陷的尺寸大于或等于通过利用了第2二值化阈值Th2的第2次二值化处理而得到的缺陷的尺寸。
例如,如图8所示,对存在相对较深的缺陷A(例如,气孔)和相对较浅的缺陷B(例如,凹坑)的情况进行说明。如图8所示,二值化阈值越小,则检测出的缺陷A、B的长度越小,如果超过某个拐点P1、P2,则变化变大。二值化处理部11针对缺陷A利用第1二值化阈值Th1而进行二值化处理,对缺陷A的长度XA1进行检测。并且,二值化处理部11利用第2二值化阈值Th2而进行二值化处理,对缺陷A的长度XA2进行检测。另一方面,二值化处理部11针对缺陷B利用第1二值化阈值Th1而进行二值化处理,对缺陷B的长度XB1进行检测。并且,二值化处理部11利用第2二值化阈值Th2而进行二值化处理,对缺陷B的长度XB2进行检测。
比率计算部12例如以缺陷A为一个例子,对在第2次二值化处理中所得到的尺寸XA2相对于在第1次二值化处理中所得到的尺寸XA1的比率Y=XA2/XA1进行计算。在第2次二值化处理中未检测出在第1次二值化处理中所检测出的缺陷的情况下,尺寸XA2为0,比率Y计算为0。由于在第1次二值化处理中所得到的尺寸XA1大于或等于在第2次二值化处理中所得到的尺寸XA2,因此比率Y处于大于或等于0且小于或等于1的范围。
深度判定部13基于比率Y对表面缺陷的相对深度(是深还是浅)进行判定(判别)。深度判定部13在比率Y小于或等于阈值N的情况下,判定为表面缺陷浅,在比率Y比阈值N大的情况下,判定为表面缺陷深。阈值N在大于0且小于1的范围内可根据产品、缺陷的种类等而适当设定,例如设定为0.5。阈值N例如预先存储于控制装置2的存储器,并被适当读出。例如缺陷A的比率Y为0.8,比阈值N的0.5大,因此深度判定部13将缺陷A判定为深。另外,例如缺陷B的比率Y为0.4,小于或等于阈值N的0.5,因此深度判定部13将缺陷B判定为浅。
体积计算部14根据通过深度判定部13得到的深度的判定结果而设定缺陷的深度。例如,在由深度判定部13判定为深的缺陷的情况下,体积计算部14将缺陷的深度设定为100μm。另一方面,在由深度判定部13判定为浅的缺陷的情况下,体积计算部14将缺陷的深度设定为10μm。与通过深度判定部13得到的深度的判定结果相对应的缺陷的深度的设定值能够根据产品、缺陷的种类等而适当设定。缺陷的深度的设定值例如预先存储于控制装置2的存储器,并被适当读出。
体积计算部14还基于所设定的缺陷的深度、和缺陷的尺寸对缺陷的体积进行计算。用于计算体积的缺陷的尺寸可以使用在第1次二值化处理中得到的缺陷的尺寸,还可以使用在第2次二值化处理中得到的缺陷的尺寸,还可以使用它们的平均值等。例如,如果缺陷的尺寸(面积)为20mm2、缺陷的深度为100μm,则体积被计算为2mm3。体积计算部14对图像中所包含的所有的缺陷的深度以及体积进行计算。体积计算部14还将各缺陷的体积进行合计而计算出缺陷的体积的总和。
是否合格判定部15对由体积计算部14计算出的缺陷的体积的总和是否小于或等于容许值(阈值)进行判定。是否合格判定部15在缺陷的体积的总和小于或等于容许值的情况下,将检查对象判定为合格品,在比容许值大的情况下,将检查对象判定为不合格品。容许值能够根据机油消耗的容许值等而适当设定。容许值例如预先存储于控制装置2的存储器,并被适当读出。
另外,由体积计算部14计算出的缺陷的体积的总和以及通过是否合格判定部15得到的是否合格判定结果被反馈至加工装置4。加工装置4基于由体积计算部14计算出的缺陷体积的总和以及其容许值而对加工条件进行调整,以使得缺陷的体积的总和小于或等于容许值。此外,可以代替对加工装置4的加工条件进行调整,或者对加工装置4的加工条件进行调整,并且还对通过加工装置4进行的等离子喷涂后的珩磨等加工工艺的加工条件进行调整。
[缺陷检查方法]
下面,参照图9的流程图对本发明的实施方式涉及的表面缺陷检查方法的一个例子进行说明。
在步骤S101中,拍摄装置3对检查对象的表面进行拍摄,获取二维图像。在步骤S102中,二值化处理部11针对由拍摄装置3获取的二维图像,利用第1二值化阈值Th1而进行第1次二值化处理。并且,二值化处理部11从第1次二值化处理后的图像中对缺陷进行提取,计算出缺陷的尺寸X1。
在步骤S103中,是否合格判定部15对第1次二值化处理后的缺陷的尺寸X1是否小于或等于容许值(阈值)进行判定。容许值能够根据产品、缺陷的种类等而适当设定,例如设定为1.5mm。在包含比容许值大的缺陷的情况下,转入步骤S112,判定为不合格品。另一方面,在步骤S103中判定为所有的缺陷的尺寸X1小于或等于容许值的情况下,转入步骤S104。
在步骤S104中,二值化处理部11针对由拍摄装置3获取的二维图像,利用第2二值化阈值Th2而进行第2次二值化处理。并且,二值化处理部11从第2次二值化处理后的图像中对缺陷进行提取,计算出缺陷的尺寸X2。
在步骤S105中,比率计算部12针对同一缺陷,对在第2次二值化处理中所得到的缺陷的尺寸X2相对于在第1次二值化处理中所得到的缺陷的尺寸X1的比率Y=X2/X1进行计算。
在步骤S106中,深度判定部13通过判定由比率计算部12计算出的比率Y是否小于或等于阈值N,从而对缺陷的相对深度进行判定。在比率Y小于或等于阈值N的情况下,判定为浅的缺陷(例如,凹坑),转入步骤S107。在步骤S107中,体积计算部14对浅的缺陷的深度D1进行设定。并且,体积计算部14根据浅的缺陷的深度D1以及缺陷的尺寸X1等对缺陷的体积进行计算。
另一方面,在步骤S106中,深度判定部13在比率Y比阈值N大的情况下,判定为深的缺陷(例如,气孔),转入步骤S108。在步骤S108中,体积计算部14将判定为深的缺陷的深度D2设定为比深度D1深的值。并且,体积计算部14根据缺陷的深度D2以及缺陷的尺寸X1等对缺陷的体积进行计算。
在步骤S109中,体积计算部14将在步骤S107以及步骤S108中计算出的所有的缺陷的体积进行合计,计算出缺陷的体积的总和。在步骤S110中,是否合格判定部15对由体积计算部14计算出的缺陷的体积的总和是否小于或等于容许值进行判定。在缺陷的体积的总和小于或等于容许值的情况下,转入步骤S111,是否合格判定部15判定为检查对象是合格品、能够出货。另一方面,在步骤S110中判定为缺陷的体积的总和比容许值大的情况下,转入步骤S112,是否合格判定部15判定为检查对象是不合格品。
根据本发明的实施方式,能够针对二维图像利用互不相同的二值化阈值而进行2次二值化处理,针对各缺陷而检测出2个尺寸X1、X2,计算出2个尺寸X1、X2的比率Y=X2/X1,根据比率Y而判别缺陷的深度。因此,与如以往那样仅以缺陷的尺寸进行评价、或者将缺陷的深度一律以预想的最大值进行设定的情况相比,能够高精度地判别缺陷的深度,能够高精度地对缺陷的体积进行计算。
另外,根据缺陷的深度的判别结果对所有的缺陷的体积进行合计,判定缺陷的体积的总和是否小于或等于容许值,由此能够高精度地对产品进行是否合格的判定。
另外,将发动机的气缸体101作为检查对象,由此能够高精度地判别作为发动机的气缸体101的主要表面缺陷的相对较深的气孔和相对较浅的凹坑。
另外,将由体积计算部14计算出的缺陷的体积的总和反馈至喷涂或其后的加工,逐次变更加工条件以使缺陷的体积的总和恒定、或者小于或等于容许值,由此能够预先抑制缺陷的产生。
(第1变形例)
在本发明的实施方式中对进行2次二值化处理的情况进行了说明,但作为第1变形例,对进行3次二值化处理并以3个阶段来判定缺陷的相对深度的情况进行说明。
二值化处理部11利用彼此尺寸不同的第1~第3二值化阈值而进行3次(第1~第3)二值化处理,由此针对同一缺陷而计算出第1~第3尺寸。例如如图10(a)所示,对存在缺陷A、B、C的情况进行说明。如图10(a)所示,对于缺陷A、B、C的长度,隔着拐点PA、PB、PC而二值化阈值越小其线性地越小,在比拐点PA、PB、PC小的那一侧其变化幅度大。
二值化处理部11针对缺陷A、B、C而分别利用第1~第3二值化阈值Th1、Th2、Th3进行3次二值化处理,由此计算出缺陷A的尺寸XA1、XA2、XA3、缺陷B的尺寸XB1、XB2、XB3、缺陷C的尺寸XC1、XC2。在第3次二值化处理时未检测出缺陷C,将缺陷C的尺寸作为0而进行计算。
以缺陷A作为一个例子,比率计算部12对第2尺寸XA2相对于第1尺寸XA1的第1比率Y1=XA2/XA1进行计算。比率计算部12还对第3尺寸XA3相对于第1尺寸XA1的第2比率Y2=XA3/XA1进行计算。比率计算部12针对缺陷B、C也与缺陷A相同地对第1以及第2比率进行计算。
深度判定部13基于第1以及第2比率Y1、Y2而以3个阶段判定缺陷的相对深度。更具体而言,深度判定部13分别将第1以及第2的比率Y1、Y2与阈值N进行比较,对缺陷的深度进行2次判定。在2次判定中使用的阈值N可以彼此相同,也可以互不相同。深度判定部13基于2次的判定结果而综合地判定缺陷的深度。
深度判定部13例如针对A、B、C,在第1次判定中判定第1比率Y1是否小于或等于阈值N,在第2次判定中判定第2比率Y2是否小于或等于阈值N。如图10(b)所示,针对缺陷A,由于2次的深度的判定结果均为深,因此综合判定为最深。对于缺陷B,由于2次的深度的判定结果的一者为深、另一者为浅,因此综合判定为中等深度。对于缺陷C,由于2次的深度的判定结果均为浅,因此综合判定为最浅。
体积计算部14根据通过深度判定部13得到的判定结果而以3个阶段对缺陷的深度进行设定。体积计算部14例如将判定为最深的缺陷A的深度D1设定为10μm,将判定为中等深度的缺陷B的深度D1设定为50μm,将判定为最浅的缺陷C的深度D3设定为100μm。
其他结构与本发明的实施方式涉及的结构实质上相同,因此省略重复的说明。
下面,参照图11的流程图对第1变形例涉及的表面缺陷检查方法的一个例子进行说明。
步骤S201~S205的流程与图9的步骤S101~S105相同,因此省略重复的说明。在步骤S206中,深度判定部13判定第1比率Y1是否小于或等于阈值N。在判定为第1比率Y1小于或等于阈值N的情况下,将缺陷的深度判定为在3个阶段之中最浅,转入步骤S207而不进行第3次二值化处理。在步骤S207中,体积计算部14对判定为最浅的缺陷的深度D1进行设定,利用深度D1对缺陷的体积进行计算。
另一方面,在步骤S206中判定为第2比率Y2比阈值N大的情况下,转入步骤S208。在步骤S208中,二值化处理部11利用第3二值化阈值Th3而进行第3次二值化处理,计算出缺陷的尺寸X3。在步骤S209中,比率计算部12对在第3次二值化处理中得到的尺寸X3相对于在第1次二值化处理中得到的尺寸X1的第2比率Y2=X3/X1进行计算。
在步骤S210中,判定第2比率Y2是否小于或等于阈值N。在判定为第2比率Y2小于或等于阈值N的情况下,判定为中等深度,转入步骤S211。在步骤S211中,体积计算部14对判定为中等深度的缺陷的深度D2(>D1)进行设定,利用深度D2对缺陷的体积进行计算。另一方面,在步骤S210中判定为第2比率Y2比阈值N大的情况下,判定为最深的缺陷,转入步骤S212。在步骤S212中,体积计算部14对最深的缺陷的深度D3(>D2)进行设定,利用深度D3对缺陷的体积进行计算。
在步骤S213中,对在步骤S207、S211、S212中得到的缺陷的体积的总和进行计算。步骤S214~S216的流程与图9的步骤S110~S112的流程实质上相同,因此省略重复的说明。
根据第1变形例,利用互不相同的3个二值化阈值而进行3次二值化处理,由此能够以3个阶段对缺陷的深度进行判别,因此能够更高精度地对缺陷的体积进行计算。此外,在第1变形例中,对进行3次二值化处理的情况进行了说明,但也可以利用互不相同的大于或等于4个的二值化阈值而进行大于或等于4次的二值化处理,以4个阶段对缺陷的深度进行判定。
(第2变形例)
下面,作为第2变形例,对二值化处理仍为2次、且多次判定缺陷的深度的情况进行说明。
例如如图12(a)所示,针对缺陷A、B、C而分别利用2个二值化阈值Th1、Th2来进行2次二值化处理,由此计算出缺陷A的尺寸XA1、XA2、缺陷B的尺寸XB1、XB2、缺陷C的尺寸XC1、XC2。比率计算部12针对缺陷A,对第2尺寸XA2相对于第1尺寸XA1的比率Y=XA2/XA1进行计算。比率计算部12针对缺陷B、C也与缺陷A相同地对比率进行计算。
深度判定部13将由比率计算部12计算出的比率Y与彼此尺寸不同的多个(2个)阈值N1、N2进行比较,多次(2次)判定缺陷的深度。阈值N1、N2能够根据产品、缺陷的种类等而适当设定。阈值N1例如设定为0.5,阈值N2比阈值N1大,例如设定为0.7。
深度判定部13针对各缺陷A、B、C,在第1次判定中判定比率Y是否小于或等于阈值N1,在第2次判定中判定比率Y是否小于或等于阈值N2。深度判定部13基于2次判定结果而判定综合的缺陷的深度。
如图12(b)所示,对于缺陷A,由于在第1次判定中比率Y小于或等于阈值N1,且在第2次判定中比率Y小于或等于阈值N2,因此作为综合判定而判定为最深。对于缺陷B,由于在第1次判定中比率Y比阈值N1大,且在第2次判定中比率Y小于或等于阈值N2,因此作为综合判定而判定为中等深度。对于缺陷C,由于在第1次判定中比率Y比阈值N1大,且在第2次判定中也是比率Y比阈值N2大,因此作为综合判定而判定为最浅。
体积计算部14根据通过深度判定部13得到的判定结果而以3个阶段对缺陷的深度进行设定。例如,体积计算部14将判定为最深的缺陷A的深度D1设定为10μm,将判定为中等深度的缺陷B的深度D2设定为50μm,将判定为最浅的缺陷C的深度D3设定为100μm。
其他结构与本发明的实施方式涉及的结构实质上相同,因此省略重复的说明。
下面,参照图13的流程图对第2变形例涉及的表面缺陷检查方法的一个例子进行说明。
步骤S301~S305的流程与图9的步骤S101~S105相同,因此省略重复的说明。在步骤S306中,深度判定部13判定比率Y是否小于或等于阈值N1。在判定为比率Y小于或等于阈值N1的情况下,判定为缺陷的深度最浅,转入步骤S307。在步骤S307中,体积计算部14对判定为最浅的缺陷的深度D1进行设定,利用深度D1对缺陷的体积进行计算。
另一方面,在步骤S306中判定为比率Y比阈值N1大的情况下,转入步骤S308。在步骤S308中,深度判定部13判定比率Y是否小于或等于比阈值N1大的阈值N2。在判定为比率Y小于或等于阈值N2的情况下,判定为中等深度,转入步骤S309。在步骤S309中,体积计算部14对中等深度的缺陷的深度D2(>D1)进行设定,利用深度D2对缺陷的体积进行计算。
另一方面,在步骤S308中判定为比率Y比阈值N2大的情况下,判定为最深,转入步骤S310。在步骤S310中,体积计算部14对判定为最深的缺陷的深度D3(>D2)进行设定,利用深度D3对缺陷的体积进行计算。
在步骤S311中,对在步骤S307、S309、S310中得到的缺陷的体积的总和进行计算。步骤S312~S314的流程与图9的步骤S110~S112的流程实质上相同,因此省略重复的说明。
根据第2变形例,利用不同的阈值N1、N2对缺陷的深度进行2次判定,由此能够以3个阶段对缺陷的深度进行判定,因此能够更高精度地求出缺陷的深度以及体积。此外,在第2变形例中,利用2个阈值N1、N2对缺陷的深度进行2次判定,以3个阶段综合地进行判定,但并不限定于此。即,深度判定部13还可以利用大于或等于3个的阈值而以2个阶段对缺陷的深度进行大于或等于3次判定,以大于或等于4阶段综合地对缺陷的深度进行判别。
(其他实施方式)
如上所述,对本发明的实施方式进行了记载,但不应当理解为构成本公开的一部分的论述及附图对本发明进行限定。根据本公开,对本领域技术人员而言,各种各样的替代实施方式、实施例以及运用技术是显而易见的。
例如,在本发明的实施方式中,作为缺陷检查装置1的检查对象的一个例子,对发动机的气缸体101的缸孔102的内表面进行了说明,但检查对象并不特别地限定于此。本发明的实施方式涉及的缺陷检查装置1可以应用于可能具有表面缺陷的各种产品。另外,缺陷的种类也不特别地限定,例如相对于二值化阈值所检测的缺陷的尺寸也可以线性地变化。
标号的说明
1 缺陷检查装置
2 控制装置
3 拍摄装置
4 加工装置
11 二值化处理部
12 比率计算部
13 深度判定部
14 体积计算部
15 是否合格判定部
30 驱动部
31 光源
32 反射镜
33 拍摄部
41 喷枪主体
42 喷枪
101 气缸体
102 缸孔