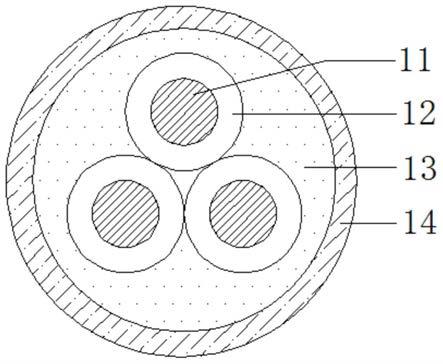
一种b1级高阻燃多芯电缆及其制造方法
技术领域
1.本发明涉及一种b1级高阻燃多芯电缆及其制造方法。
背景技术:2.多芯电缆指两芯或两芯以上的电缆,其结构包括缆芯、缆芯包覆层、隔氧层及外护套。其中,缆芯由绝缘芯线和填充绳绞合而成,缆芯外包覆一层或多层包带,包带外为挤包隔氧层,隔氧层外为外护套。
3.现有的b1级高阻燃多芯电缆,通常采用的结构如图1所示,包括:导体1、绝缘层2、填充绳3、包带4、隔氧层5、外护套6等。其中,填充绳3、包带4、隔氧层5、外护套6均采用高阻燃材料,其中,包带采用2~4层高阻燃包带,隔氧层厚度一般在2.5mm及以上。以达到b1级阻燃的效果。
4.现有技术方案存在的问题是:采用填充绳是无法紧密压实地对缆芯成缆间隙填充,在填充绳与芯线之间或填充绳之间始终会留有较多的空气间隙。并且,对于部分小截面的多芯电缆,由于芯线之间的间隙较小,无合适的填充绳填充芯线间的间隙,因此通常未使用填充绳。这样一来,绝缘芯线之间存在较大的间隙。
5.绝缘芯线是由可燃的材料制成的,在电缆燃烧条件下,绝缘芯线之间和填充绳之间的间隙中存在的空气,给可燃的绝缘芯线提供了燃烧所需氧气。绝缘芯线引燃后,顺着这些间隙向上蔓延,形成烟囱效应,并进一步加剧了绝缘芯线的燃烧,造成缆芯膨胀,破坏外护套的结壳性,进一步加剧了绝缘材料的燃烧,并释放出大量的热量和烟气,达不到b1级阻燃要求。
技术实现要素:6.为了克服现有技术的缺点,本发明提供了一种b1级高阻燃多芯电缆及其制造方法。
7.本发明所采用的技术方案是:一种b1级高阻燃多芯电缆,包括导体、绝缘层、挤压式隔氧层和外护套,其中:导体和挤包在导体上的绝缘层构成绝缘芯线,所述绝缘芯线绞制成缆芯,在缆芯外包覆挤压式隔氧层,所述挤压式隔氧层的内表面为锯齿形,在挤压式隔氧层外挤包外护套;所述挤压式隔氧层的平均厚度t=0.8~2.0mm。
8.本发明还提供了一种b1级高阻燃多芯电缆的制造方法,包括如下步骤:
9.步骤一、制作绝缘芯线;
10.步骤二、成缆:将两根以上的绝缘芯线直接通过成缆机进行绞制,形成电缆的缆芯;
11.步骤三、在缆芯外挤包隔氧层:
12.通过挤塑机采用挤压式模具进行填充和隔氧层一次性挤出,使隔氧层紧密挤包在缆芯上,其中:所述挤压式模具的配模方法为:
13.(1)按如下公式确定模芯孔径d1:
14.d1=d0+k115.其中:d0为缆芯的最大外径;k1为模芯选取系数,k1=0.5~3.5mm;
16.(2)按如下公式确定模盖孔径d2:
17.d2=d0+2*t+k218.其中:t为隔氧层的平均厚度;k2为模盖选取系数,k2=
‑
1.0~1.0mm;
19.(3)确定模芯与模盖的端面距离d为2~5倍隔氧层的平均厚度t,且大于等于5mm;
20.步骤四、在隔氧层外挤包外护套。
21.与现有技术相比,本发明的积极效果是:
22.本发明采用挤压式隔氧层,即缆芯绞合后,直接将填充和隔氧层一次性挤出,形成填充与隔氧层一体的挤压式隔氧层。挤压式隔氧层通过采用挤压方式挤出,形成锯齿状隔氧层,这些锯齿状正好填满绝缘芯线之间的空隙,将可燃绝缘层完整包覆,从而消除了空隙,解决了因烟囱效应导致的阻燃性能降低的问题。具体优点如下:
23.1、采用挤压式隔氧层,隔氧层可以从原来的2.5mm以上减至0.8~2.0mm,加上减少了缆芯包覆层,省去了填充绳、阻燃包带材料,节约材料,大大降低了电缆成本(比现有电缆成本低10%
‑
30%);
24.2、阻燃效果提高,可达到gb/t 31247
‑
2014《电缆及光缆燃烧性能分级》标准中b1级阻燃要求。
25.3、电缆外径比现有技术方案小,且电缆结构和用料简单,更方便施工。
附图说明
26.本发明将通过例子并参照附图的方式说明,其中:
27.图1为现有的b1级高阻燃多芯电缆的结构示意图;
28.图2为本发明的b1级高阻燃多芯电缆的结构示意图。
具体实施方式
29.一种b1级高阻燃多芯电缆,如图2所示,包括:导体11、绝缘层12、挤压式隔氧层13和外护套14,其中:
30.所述挤压式隔氧层13的内表面为锯齿形,采用流动性较好、且不与绝缘表面发生粘结的高阻燃隔氧料,通过挤压式挤包工艺制造而成。所述挤压式隔氧层的平均厚度t=0.8~2.0mm,其中缆芯外径10mm以下,隔氧层的平均厚度为0.8~1.2mm;缆芯外径10~20mm时,隔氧层的平均厚度为1.0~1.5mm;缆芯外径为20~30mm时,隔氧层的平均厚度为1.2~1.7mm;缆芯外径为30mm及以上时,隔氧层的平均厚度为1.5~2.0mm。
31.本发明还提供了一种b1级高阻燃多芯电缆的制造方法,包括如下步骤:
32.步骤一、制作绝缘芯线:
33.绝缘芯线由导体11和绝缘层12构成,其中导体11由具有高导电系数的铜、铝、铝合金或铜包铝制成;绝缘层12在导体外,保证产品的电气绝缘性能。绝缘层12挤包在导体上,其材料为交联聚乙烯或其他材料;绝缘层12与导体间也可增加绕包绝缘层,材料为云母带或其他类似材料,以提高其耐火性能。
34.步骤二、成缆:
35.两芯或两芯以上的绝缘芯线,通过成缆机进行绞制,形成电缆的缆芯。缆芯绞制时,在绝缘芯线之间不使用填充绳,缆芯外也不使用包带包覆缆芯。
36.缆芯绞制后,由于未包覆包带,容易出现缆芯端头处绝缘芯线松散,将影响电缆的成型和后工序的加工。为解决这个问题,可以采用金属网套将缆芯端头抱紧的方式。即用金属网套套在绝缘芯线的所有芯线端头上,拉紧,再将金属网套与引线连接。缆芯绞制时,金属网套可以随绞笼的转动而转动,并带动绝缘芯线形成节距,从而防止绝缘芯线端头散开。
37.步骤三、挤包挤压式隔氧层:
38.在缆芯外挤包挤压式隔氧层,挤压式隔氧层采用高阻燃材料,通过挤塑机采用挤压式模具进行挤出,使隔氧层紧密挤包在缆芯上。其中:
39.(一)采用挤压式隔氧层的配模方法为:
40.1、按如下公式确定模芯孔径d1:
41.d1=d0+k142.其中:d0为缆芯的最大外径;k1为模芯选取系数。
43.由于缆芯制造时未加填充绳,也未包覆包带,因此缆芯既不圆整,也同时存在弯曲。因此,模芯孔径尺寸不宜过大,否则可能使隔氧层挤包得不紧密,使缆芯与隔氧层之间仍存在较大的间隙。模芯孔径尺寸也不宜过小,否则缆芯可能受到损伤,挤包的隔氧层可能偏心严重。
44.选取k1=0.5~3.5mm
45.当d0小于5mm时,k1=0.5~1.0mm;当d0为5mm~10mm时,k1=1.0~1.5mm;当d0为10mm~20mm时,k1=1.2~1.8mm;当d0为20mm~30mm时,k1=1.5~3.0mm;当d0为30mm以上时,k1=2.0~3.5mm。
46.2、按如下公式确定模盖孔径d2:
47.d2=d0+2*t+k248.其中:t为隔氧层的平均厚度;k2为模盖选取系数。
49.模盖的尺寸按常规方法选取,以下为参考值。
50.k2的选取:k2=
‑
1.0~1.0mm
51.当d0小于10mm时,k2=0~1.0mm;当d0为10mm~30mm时,k2=
‑
0.5~1.0mm;当d0为30mm以上时,k2=
‑
1.0~1.0mm。
52.3、确定模芯与模盖的端面距离d:
53.模芯与模盖的端面距离d,可选取d=2~5t,一般不小于5mm。
54.(二)挤压式隔氧层配方
55.挤压式隔氧层采用高阻燃隔氧料。为更好地使挤压式隔氧层在挤出时填满绝缘芯线之间的空隙,挤压式隔氧层可采用流动性好、且不与绝缘表面发生粘结的高阻燃隔氧料。
56.所述高阻燃隔氧料由以下质量百分比的原料制成:
[0057][0058]
其中,乙烯
‑
醋酸乙烯共聚物与乙烯
‑
辛烯共聚弹性体的质量比为1:1~5:1,且总和不超过配方总量的35%。
[0059]
无卤低烟阻燃剂为:氢氧化铝和氢氧化镁的混合物。氢氧化铝和氢氧化镁的比例为2:1
‑
3:1。
[0060]
为更好的提高隔氧料的阻燃性能,加入熔点在500~800℃的物质,比如低温玻璃和/或三氧化二锑,加入的比例为5~20%。
[0061]
相容剂为马来酸酐接枝相容剂,如pe
‑
mah。
[0062]
成炭剂可采用硅树脂、蒙脱土。
[0063]
加工助剂:包括抗氧剂、润滑剂、防粘剂及颜料等。抗氧剂可选用抗氧剂1010、抗氧剂1024、硅酮、抗氧剂168,其中一种或多种的组合。
[0064]
所述高阻燃隔氧料在170℃,10kg的条件下,熔融指数为10
‑
20g/10min。
[0065]
步骤四、挤包外护套:
[0066]
挤压式隔氧层外挤包外护套,外护套材料为低烟无卤阻燃聚烯烃材料或其他低烟无卤阻燃材料。
[0067]
在完成步骤三所述的挤包挤压式隔氧层后,对于需要承受较大拉力和压力的场合则可以在挤压式隔氧层外增加一层铠装层。
[0068]
本发明可以用在阻燃b1级多芯控制电缆,阻燃b1级6mm2及以下多芯电力电缆。