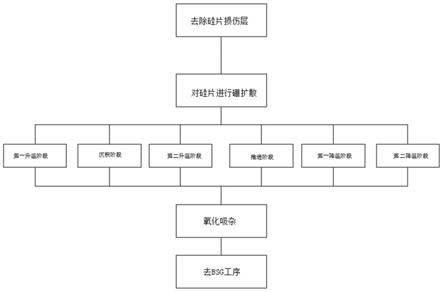
1.本发明属于太阳能电池片制备技术领域,尤其是涉及一种提升硅片转换效率的预处理方法。
背景技术:2.目前,光伏领域使用的硅片种类很多,但是控制硅片电阻率的方法大部分是通过晶体拉制过程中的工艺来限制电阻率的波动,电阻率大会使得硅片的转换效率差,而拉至一次晶体便能得到很多硅片,不能因为电阻率原因而将所有硅片直接废弃。
3.为了进一步降低晶硅电池产品的光衰值,各电池厂家纷纷导入使用掺镓硅片,但因镓的分凝系数较低,会导致单晶硅片的电阻率分布范围较大,而高电阻率的掺镓硅片,又会对电池片的转换效率产生极大的负面影响,从而一定程度上降低了掺镓硅片的经济性。
技术实现要素:4.本发明要解决的问题是提供一种提升硅片转换效率的预处理方法,有效的解决掺杂硅片中镓的分凝系数较低,会导致单晶硅片的电阻率分布范围较大,而高电阻率的掺镓硅片,又会对电池片的转换效率产生极大的负面影响,从而一定程度上降低了掺镓硅片的经济性的问题。
5.为解决上述技术问题,本发明采用的技术方案是:一种提升硅片转换效率的预处理方法,包括:
6.去除硅片表面的损伤层;
7.对去除损伤层的所述硅片的正表面进行硼扩散处理,形成p+掺杂层,并在所述p+掺杂层表面还形成一硼硅玻璃层;
8.将硼扩散后的所述硅片置入氧化炉中,向所述氧化炉内通入氧气,在所述硼硅玻璃层表面形成一氧化层;
9.去除所述氧化层和所述硼硅玻璃层,保留所述p+掺杂层,预处理完成。
10.优选地,所述硅片包括掺镓硅片。
11.优选地,去除硅片表面的损伤层过程中,采用第一腐蚀液对所述硅片表面进行腐蚀,来去除所述硅片正表面以及背表面的损伤层,其中,
12.所述第一腐蚀液采用naoh,浓度范围为1.2-1.4%,腐蚀时间为 120-140s。
13.优选地,对所述硅片的正表面进行硼扩散处理中,硼源采用三溴化硼或者三氯化硼,扩散温度为750-1100℃,扩散时间为7200-9600s。
14.优选地,对所述硅片的正表面进行硼扩散处理的阶段包括:
15.第一升温阶段:在硼扩散设备中通入所述硼源,随后升温至第一温度,所述第一温度为800-900℃,第一升温时间为1000-1400s;
16.沉积阶段:保持所述第一温度不变,所述硼源沉积在所述硅片正表面,沉积时间为1900-2300s;
17.第二升温阶段:待所述硼源沉积后,再次升温值第二温度,所述第二温度为900-1100℃,第二升温时间为700-1100s;
18.推进阶段:保持所述第二温度不变,硼元素推进至所述硅片内部,推进时间为700-1100s;
19.第一降温阶段:待所述硼元素推进完成后,降温至第三温度,所述第三温度为820-900℃,第三降温时间为1300-1700s;
20.第二降温阶段:待第一降温阶段结束后,再次降温至第四温度,所述第四温度为750-850℃,第四降温时间为1600-2000s。
21.优选地,推进阶段中,所述硼元素推进至所述硅片的深度为0.8-1.2μm。
22.优选地,将硼扩散后的所述硅片置入氧化炉中,向所述氧化炉内通入氧气,在所述硼硅玻璃层表面形成一氧化层的过程中,氧化温度为700-900℃,氧化时间为60-90min。
23.优选地,所述氧化层的厚度为10-30nm。
24.优选地,去除所述氧化层和所述硼硅玻璃层的步骤中,采用第二腐蚀液对所述氧化层和所述硼硅玻璃层进行腐蚀,其中,
25.所述第二腐蚀液为hf,浓度范围为45-55%,腐蚀时间为20-30min,最终保留所述p+掺杂层,预处理完成。
26.采用上述技术方案,在掺镓硅片的正表面进行硼扩散,使得硼元素掺杂至高电阻率的掺杂硅片表面,形成了硼镓共掺的状态,增加了硅片整体的杂质浓度,使得硅片内的杂质浓度提升至10
13
/cm2,因硅片电阻率的大小与杂质浓度成反比,故可以大大降低硅片的电阻率,从而在后续的生产工艺中,提升电池片电流,进而提升电池片的转换效率。
27.采用上述技术方案,硼扩散完成后,通过氧化炉,将硅片表面的杂质元素,氧化吸附进氧化层中,从而通过后续去氧化层和硼硅玻璃层的工序,将带有杂质元素的氧化层去除,进而起到进一步去除硅片杂质的目的,为后续电池片效率的进一步提升,提供助力。
附图说明
28.图1是本发明实施例一种提升硅片转换效率的预处理方法流程图
具体实施方式
29.下面结合实施例和附图对本发明作进一步说明:
30.在本发明实施例的描述中,需要理解的是,术语“正表面”、“背表面”等指示的方位或位置关系为基于附图所示的方位或位置关系,仅是为了便于描述本发明和简化描述,而不是指示或暗示所指的装置或元件必须具有特定的方位、以特定的方位构造和操作,因此不能理解为对本发明的限制。
31.如图1所示,一种提升硅片转换效率的预处理方法,包括:
32.s1:去除硅片表面的损伤层,其中,
33.为进一步降低晶硅电池产品的光衰值,硅片设置为掺镓硅片;
34.去除硅片表面的损伤层过程中,损伤层一般指硅片在切割过程中在硅片的表面造成的细小损伤,例如突刺或者表面过于粗糙等缺陷,通过去除后可以得到较光滑的硅片表面;
35.采用第一腐蚀液对硅片的正表面以及背表面进行腐蚀,来去除硅片正表面以及背表面的损伤层,其中,
36.第一腐蚀液采用naoh,浓度范围为1.2-1.4%,腐蚀时间为120-140s,因为第一腐蚀液的浓度范围较低,不会影响硅片的厚度,即硅片厚度不会发生变化。
37.s2:对去除损伤层的硅片的正表面进行硼扩散处理,形成p+掺杂层,并在p+掺杂层表面还形成一硼硅玻璃层,其中;
38.对硅片的正表面进行硼扩散处理中,硼源采用三溴化硼或者三氯化硼,扩散温度范围为750-1100℃,总的扩散时间范围为7200-9600s;
39.对硅片的正表面进行硼扩散处理的阶段包括:
40.第一升温阶段:在硼扩散设备中通入硼源,随后升温至第一温度,第一温度为800-900℃,第一升温时间为1000-1400s;
41.沉积阶段:保持第一温度不变,硼源沉积在硅片正表面,沉积时间为 1900-2300s;
42.第二升温阶段:待硼源沉积后,再次升温值第二温度,第二温度为 900-1100℃,第二升温时间为700-1100s;
43.推进阶段:保持第二温度不变,硼元素推进至硅片内部,推进时间为 700-1100s;
44.第一降温阶段:待硼元素推进完成后,降温至第三温度,第三温度为 820-900℃,第三降温时间为1300-1700s;
45.第二降温阶段:待第一降温阶段结束后,再次降温至第四温度,第四温度为750-850℃,第四降温时间为1600-2000s。
46.在推进阶段中,硼元素推进至硅片的深度为0.8-1.2μm。
47.通过再高电阻率的硅片表面掺杂硼元素,增加硅片整体的杂质浓度,且能够形成硼镓共掺状态,使得硅片的电阻率大大降低,在后续的工艺过程中提升电池片的电流,仅为提升电池片的转换效率。
48.s3:将硼扩散后的硅片置入氧化炉中,向氧化炉内通入氧气,在硼硅玻璃层表面形成一氧化层;
49.硼扩散的所有阶段完成后,硼扩散设备还保持750-800℃的待机温度,从硼扩散设备中取出处理后的硅片,再将硅片置入氧化炉中;
50.当硅片置入氧化炉内后,向氧化炉内通入氧气,进行氧化吸杂反应,氧化温度为700-900℃,氧化时间为60-90min,氧化完成后,在硼硅玻璃层表面形成一氧化层,其中,
51.氧化层的厚度为10-30nm。
52.s4:去除氧化层和硼硅玻璃层,保留p+掺杂层,预处理完成。
53.去除氧化层和硼硅玻璃层又称去bsg工序,待硅片出氧化炉后逐渐冷却至室温,然后去除工作。
54.采用第二腐蚀液对氧化层和硼硅玻璃层进行腐蚀,其中,
55.第二腐蚀液为hf,第二腐蚀液的浓度范围为45-55%,腐蚀时间为 20-30min,最终保留p+掺杂层,即只有硅片以及硅片正表面的p+掺杂层,预处理完成。
56.在正常的perc工艺流程前增加本发明中的去除硅片表面损伤层、对其进行硼扩散、氧化吸杂以及去除氧化层和硼硅玻璃层的步骤工序,其中,去除表面损伤可以使硅片的表面更好的沉积钝化层,且能够使硅片更加美观;硼扩散能够增加硅片整体的杂质浓度,将
杂质浓度提升至10
18
cm-3
左右,形成硼镓共掺状态,因硅片电阻率的大小与杂质浓度成反比,故可以大大降低硅片的电阻率,从而在后续的生产工艺中,提升电池片电流,进而提升电池片的转换效率;氧化吸杂能够将硅片表面的杂质元素,吸附进氧化层中,从而通过后续去bsg工序,将带有杂质元素的氧化层和硼硅玻璃层去除,进而起到进一步去除硅片杂质的目的,为后续电池片效率的进一步提升,提供助力。
57.下面列举几个具体实施例:
58.实施例1
59.s1:去除硅片表面的损伤层,其中,
60.为进一步降低晶硅电池产品的光衰值,硅片设置为掺镓硅片;
61.去除硅片表面的损伤层过程中,损伤层一般指硅片在切割过程中在硅片的表面造成的细小损伤,例如突刺或者表面过于粗糙等缺陷,通过去除后可以得到较光滑的硅片表面;
62.采用第一腐蚀液对硅片的正表面以及背表面进行腐蚀,来去除硅片正表面以及背表面的损伤层,其中,
63.第一腐蚀液采用naoh,浓度为1.3%,腐蚀时间为130s,因为第一腐蚀液的浓度范围较低,不会影响硅片的厚度,即硅片厚度不会发生变化。
64.s2:对去除损伤层的硅片的正表面进行硼扩散处理,形成p+掺杂层,并在p+掺杂层表面还形成一硼硅玻璃层,其中;
65.对硅片的正表面进行硼扩散处理中,硼源采用三溴化硼或者三氯化硼,
66.对硅片的正表面进行硼扩散处理的阶段包括:
67.第一升温阶段:在硼扩散设备中通入硼源,随后升温至第一温度,第一温度为865℃,第一升温时间为1200s;
68.沉积阶段:保持第一温度不变,硼源沉积在硅片正表面,沉积时间为 2100s;
69.第二升温阶段:待硼源沉积后,再次升温值第二温度,第二温度为965℃,第二升温时间为900s;
70.推进阶段:保持第二温度不变,硼元素推进至硅片内部,推进时间为 900s;
71.第一降温阶段:待硼元素推进完成后,降温至第三温度,第三温度为 870℃,第三降温时间为1500s;
72.第二降温阶段:待第一降温阶段结束后,再次降温至第四温度,第四温度为830℃,第四降温时间为1800s。
73.在推进阶段中,硼元素推进至硅片的深度为1μm。
74.通过再高电阻率的硅片表面掺杂硼元素,增加硅片整体的杂质浓度,且能够形成硼镓共掺状态,使得硅片的电阻率大大降低,在后续的工艺过程中提升电池片的电流,仅为提升电池片的转换效率。
75.s3:将硼扩散后的硅片置入氧化炉中,向氧化炉内通入氧气,在硼硅玻璃层表面形成一氧化层;
76.硼扩散的所有阶段完成后,硼扩散设备还保持800℃的待机温度,从硼扩散设备中取出处理后的硅片,再将硅片置入氧化炉中;
77.当硅片置入氧化炉内后,向氧化炉内通入氧气,进行氧化吸杂反应,氧化温度为
800℃,氧化时间为75min,氧化完成后,在硼硅玻璃层表面形成一氧化层,其中,
78.氧化层的厚度为20nm。
79.s4:去除氧化层和硼硅玻璃层,保留p+掺杂层,预处理完成。
80.去除氧化层和硼硅玻璃层又称去bsg工序,待硅片出氧化炉后逐渐冷却至室温,然后去除工作。
81.采用第二腐蚀液对氧化层和硼硅玻璃层进行腐蚀,其中,
82.第二腐蚀液为hf,第二腐蚀液的浓度为50%,腐蚀时间为25min,最终保留p+掺杂层,即只有硅片以及硅片正表面的p+掺杂层,预处理完成。
83.实施例2
84.s1:去除硅片表面的损伤层,其中,
85.为进一步降低晶硅电池产品的光衰值,硅片设置为掺镓硅片;
86.去除硅片表面的损伤层过程中,损伤层一般指硅片在切割过程中在硅片的表面造成的细小损伤,例如突刺或者表面过于粗糙等缺陷,通过去除后可以得到较光滑的硅片表面;
87.采用第一腐蚀液对硅片的正表面以及背表面进行腐蚀,来去除硅片正表面以及背表面的损伤层,其中,
88.第一腐蚀液采用naoh,浓度范围为1.2%,腐蚀时间为40s,因为第一腐蚀液的浓度范围较低,不会影响硅片的厚度,即硅片厚度不会发生变化。
89.s2:对去除损伤层的硅片的正表面进行硼扩散处理,形成p+掺杂层,并在p+掺杂层表面还形成一硼硅玻璃层,其中;
90.对硅片的正表面进行硼扩散处理中,硼源采用三溴化硼或者三氯化硼,
91.对硅片的正表面进行硼扩散处理的阶段包括:
92.第一升温阶段:在硼扩散设备中通入硼源,随后升温至第一温度,第一温度为800℃,第一升温时间为1400s;
93.沉积阶段:保持第一温度不变,硼源沉积在硅片正表面,沉积时间为 2300s;
94.第二升温阶段:待硼源沉积后,再次升温值第二温度,第二温度为900℃,第二升温时间为1100s;
95.推进阶段:保持第二温度不变,硼元素推进至硅片内部,推进时间为 1100s;
96.第一降温阶段:待硼元素推进完成后,降温至第三温度,第三温度为 820℃,第三降温时间为1700s;
97.第二降温阶段:待第一降温阶段结束后,再次降温至第四温度,第四温度为750℃,第四降温时间为2000s。
98.在推进阶段中,硼元素推进至硅片的深度为0.9μm。
99.通过再高电阻率的硅片表面掺杂硼元素,增加硅片整体的杂质浓度,且能够形成硼镓共掺状态,使得硅片的电阻率大大降低,在后续的工艺过程中提升电池片的电流,仅为提升电池片的转换效率。
100.s3:将硼扩散后的硅片置入氧化炉中,向氧化炉内通入氧气,在硼硅玻璃层表面形成一氧化层;
101.硼扩散的所有阶段完成后,硼扩散设备还保持800℃的待机温度,从硼扩散设备中
取出处理后的硅片,再将硅片置入氧化炉中;
102.当硅片置入氧化炉内后,向氧化炉内通入氧气,进行氧化吸杂反应,氧化温度为700℃,氧化时间为90min,氧化完成后,在硼硅玻璃层表面形成一氧化层,其中,
103.氧化层的厚度为25nm。
104.s4:去除氧化层和硼硅玻璃层,保留p+掺杂层,预处理完成。
105.去除氧化层和硼硅玻璃层又称去bsg工序,待硅片出氧化炉后逐渐冷却至室温,然后去除工作。
106.采用第二腐蚀液对氧化层和硼硅玻璃层进行腐蚀,其中,
107.第二腐蚀液为hf,第二腐蚀液的浓度范围为45%,腐蚀时间为30min,最终保留p+掺杂层,即只有硅片以及硅片正表面的p+掺杂层,预处理完成。
108.实施例3
109.s1:去除硅片表面的损伤层,其中,
110.为进一步降低晶硅电池产品的光衰值,硅片设置为掺镓硅片;
111.去除硅片表面的损伤层过程中,损伤层一般指硅片在切割过程中在硅片的表面造成的细小损伤,例如突刺或者表面过于粗糙等缺陷,通过去除后可以得到较光滑的硅片表面;
112.采用第一腐蚀液对硅片的正表面以及背表面进行腐蚀,来去除硅片正表面以及背表面的损伤层,其中,
113.第一腐蚀液采用naoh,浓度范围为1.4%,腐蚀时间为140s,因为第一腐蚀液的浓度范围较低,不会影响硅片的厚度,即硅片厚度不会发生变化。
114.s2:对去除损伤层的硅片的正表面进行硼扩散处理,形成p+掺杂层,并在p+掺杂层表面还形成一硼硅玻璃层,其中;
115.对硅片的正表面进行硼扩散处理中,硼源采用三溴化硼或者三氯化硼,
116.对硅片的正表面进行硼扩散处理的阶段包括:
117.第一升温阶段:在硼扩散设备中通入硼源,随后升温至第一温度,第一温度为900℃,第一升温时间为1000s;
118.沉积阶段:保持第一温度不变,硼源沉积在硅片正表面,沉积时间为 1900s;
119.第二升温阶段:待硼源沉积后,再次升温值第二温度,第二温度为 1000℃,第二升温时间为700s;
120.推进阶段:保持第二温度不变,硼元素推进至硅片内部,推进时间为 700s;
121.第一降温阶段:待硼元素推进完成后,降温至第三温度,第三温度为 850℃,第三降温时间为1300s;
122.第二降温阶段:待第一降温阶段结束后,再次降温至第四温度,第四温度为850℃,第四降温时间为1600s。
123.在推进阶段中,硼元素推进至硅片的深度为1.0μm。
124.通过再高电阻率的硅片表面掺杂硼元素,增加硅片整体的杂质浓度,且能够形成硼镓共掺状态,使得硅片的电阻率大大降低,在后续的工艺过程中提升电池片的电流,仅为提升电池片的转换效率。
125.s3:将硼扩散后的硅片置入氧化炉中,向氧化炉内通入氧气,在硼硅玻璃层表面形
成一氧化层;
126.硼扩散的所有阶段完成后,硼扩散设备还保持800℃的待机温度,从硼扩散设备中取出处理后的硅片,再将硅片置入氧化炉中;
127.当硅片置入氧化炉内后,向氧化炉内通入氧气,进行氧化吸杂反应,氧化温度为900℃,氧化时间为60min,氧化完成后,在硼硅玻璃层表面形成一氧化层,其中,
128.氧化层的厚度为30nm。
129.s4:去除氧化层和硼硅玻璃层,保留p+掺杂层,预处理完成。
130.去除氧化层和硼硅玻璃层又称去bsg工序,待硅片出氧化炉后逐渐冷却至室温,然后去除工作。
131.采用第二腐蚀液对氧化层和硼硅玻璃层进行腐蚀,其中,
132.第二腐蚀液为hf,第二腐蚀液的浓度范围为55%,腐蚀时间为20min,最终保留p+掺杂层,即只有硅片以及硅片正表面的p+掺杂层,预处理完成。
133.以上对本发明的实施例进行了详细说明,但所述内容仅为本发明的较佳实施例,不能被认为用于限定本发明的实施范围。凡依本发明申请范围所作的均等变化与改进等,均应仍归属于本发明的专利涵盖范围之内。