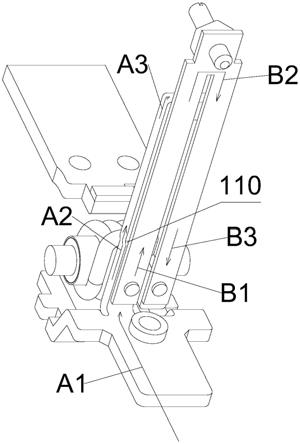
1.本实用新型涉及低压电器领域,特别是涉及一种热电磁脱扣器。
背景技术:2.热电磁脱扣器是断路器的关键执行元件,热电磁脱扣器的双金属片在温度变化时能够弯曲,如线路过载升温时,通过双金属片弯曲触发断路器跳闸。双金属片的工作原理通常分为直热式和旁热式,直热式让电流经过双金属片,通过双金属片直接发热弯曲,但只能用在额定电流较小的断路器上,否则容易导致双金属片出现熔断。旁热式的电流不经过双金属片,而是经过另一发热元件,通过发热元件对双金属片进行加热,虽然应用的更为广泛,但发热元件发热量较小,延时动作的一致性不好。
技术实现要素:3.本实用新型的目的在于克服现有技术的缺陷,提供一种同时具备直热和旁热加热方式的热电磁脱扣器。
4.为实现上述目的,本实用新型采用了如下技术方案:
5.一种热电磁脱扣器,其包括支架以及分别安装在支架上的线圈组件和发热组件,所述发热组件包括发热元件和双金属片,发热元件与线圈组件电连接,双金属片通过导电件与发热元件并联。
6.优选的,所述双金属片包括至少两个间隔设置的双金属条,至少两个双金属条的一端通过双金连接片连接在一起,至少两个双金属条的另一端分别通过导电件固定在发热元件上。
7.优选的,所述双金属片一体成型呈u型结构,双金属片的中部设有开槽,双金属片包括相对设置在开槽两侧的两个双金属条,以及连接在两个双金属条一端之间的双金连接片,两个双金属条的另一端分别通过导电件固定在发热元件上。
8.优选的,所述发热元件包括加热部和固定部,加热部和所述双金属片分别呈u字形结构,加热部和双金属片的两端分别相连,加热部和双金属片的其它部分间隔设置,加热部的一端与固定部连接,加热部的另一端与固定部间隔设置。
9.优选的,所述加热部设有第二开槽,加热部包括相对设置在第二开槽两侧的两个加热条,以及连接在两个加热条一端之间的加热片,其中一个加热条的另一端分别与双金属片的一端和固定部连接,另一个加热条的另一端与双金属片的一端连接,并与固定部间隔设置,两个加热条与加热片相连的一端分别向远离双金属片的一侧折弯,在发热元件与双金属片之间形成间隔槽。
10.优选的,还包括转动安装在支架上的衔铁,所述线圈组件包括绝缘组件以及设置在绝缘组件内的导线组,在导线组的内侧设有铁芯,导线组一端与连接板连接,另一端通过软连接连接在发热元件与双金属片间隔设置的部分上。
11.优选的,所述支架包括相对设置的左侧板和右侧板,在左侧板和右侧板的内侧分
别固定安装有左磁轭和右磁轭,左磁轭和右磁轭相对设置在线圈组件的两侧。
12.优选的,所述导线组的内侧设有包括在铁芯上的热缩管。
13.优选的,所述衔铁的两侧分别设有凸点,所述左侧板和右侧板的顶侧分别设有呈u型结构的凹槽,凸点能够分别插入对应的左侧板和右侧板的凹槽内转动,左侧板和右侧板在靠近衔铁的侧面分别设有用于限位衔铁的限位部。
14.优选的,所述铁芯和/或发热元件上分别设有凸台结构,所述左磁轭和右磁轭上分别设有与凸台结构对应的通孔结构,凸台结构穿过对应的通孔结构后铆接固定。
15.优选的,所述左磁轭和右磁轭上分别设有凸台结构,所述左侧板和右侧板分别设有与凸台结构对应的通孔结构,凸台结构穿过对应的通孔结构后铆接固定。
16.本实用新型的热电磁脱扣器,在线圈组件与发热元件串联的基础上,又将双金属片通过导电件与发热元件进行并联,不仅分流了发热元件与双金属片的电流,能够避免双金属片出现熔断,而且双金属片能够在自发热的同时,又能够被发热元件加热,即使额定电流较小,也不会出现因发热量小导致的延时动作不一致问题。
17.此外,通过在双金属片的中部设置开槽,使双金属片呈u型结构,通过两个双金属条进行分流,能够避免大电流烧毁双金属片。
附图说明
18.图1是本实用新型热电磁脱扣器的结构示意图;
19.图2是本实用新型热电磁脱扣器的左视图;
20.图3是本实用新型热电磁脱扣器的俯视爆炸图;
21.图4是本实用新型热电磁脱扣器的爆炸图;
22.图5是本实用新型图4的局部放大图;
23.图6是本实用新型双金属片与发热元件的配合示意图;
24.图7是本实用新型双金属片和发热元件一侧的电流流动示意图;
25.图8是本实用新型双金属片和发热元件另一侧的电流流动示意图。
具体实施方式
26.以下结合附图1至6给出的实施例,进一步说明本实用新型的热电磁脱扣器的具体实施方式。本实用新型的热电磁脱扣器不限于以下实施例的描述。
27.如图1
‑
6所示,本实用新型的热电磁脱扣器包括支架以及分别安装在支架上的线圈组件和发热组件,所述发热组件包括发热元件11和双金属片13,发热元件11通过软连接16与线圈组件电连接,双金属片13通过导电件12与发热元件11并联。本实施例中发热元件11远离双金属片13的一侧通过软连接16与线圈组件连接,双金属片13通过导电件12固定在发热元件11的另一侧。
28.本实用新型的热电磁脱扣器,在线圈组件与发热元件11通过软连接16串联的基础上,又将双金属片13通过导电件12与发热元件11进行并联,不仅分流了发热元件11与双金属片13的电流,能够避免双金属片13出现熔断,而且双金属片13能够在自发热的同时,又能够被发热元件11加热,即使额定电流较小,也不会出现因发热量小导致的延时动作不一致问题。
29.如图5
‑
6所示,所述双金属片包括至少两个间隔设置的双金属条132,至少两个双金属条132的一端通过双金连接片133连接在一起,至少两个双金属条132的另一端分别通过导电件12固定在发热元件11上。本实施例的双金属片13一体成型呈u型结构,双金属片13的中部设有开槽131,双金属片13包括相对设置在开槽131两侧的两个双金属条132,以及连接在两个双金属条132一端之间的双金连接片133,两个双金属条132的另一端分别通过导电件12固定在发热元件11上,在双金连接片133上设有调节螺钉14,双金属片13弯曲时带动调节螺钉14触发断路器的操作机构,使操作机构驱动断路器跳闸,调整调节螺钉14旋入的长度可以调节延时特性。本实施例通过在双金属片13的中部设置开槽131,使双金属片13呈u型结构,通过两个双金属条132进行分流,能够避免大电流烧毁双金属片13。
30.优选的,上所述导电件12为铆钉,导电件12也可以采用其它零件,不做具体限定。可以理解的是,所述双金属片包括至少两个间隔设置的双金属条132,双金属条132可以为三个或更多个,如双金属片13可以为三个双金属条132构成的w型结构,至少两个双金属条132的一端通过双金连接片133连接在一起,至少两个双金属条132的另一端分别通过导电件12固定在发热元件11上,同样具有分流效果,都属于本实用新型的保护范围。
31.如图5
‑
6所示,所述发热元件11包括加热部和固定部,加热部呈u型结构,加热部和所述双金属片13分别呈u字形结构,加热部和双金属片13的两端分别相连,加热部和双金属片13的其它部分间隔设置,加热部的一端与固定部连接,加热部的另一端与固定部间隔设置。
32.加热部呈u型结构不仅能够减少截面面积,并增加发热量,在小安培电流时也能够可靠工作,而且与双金属片13的u字形结构匹配,能够与双金属片13直接并联在一起,又不会占用额外的空间,具有体积小的特点。
33.具体的,所述发热元件11包括加热部和固定部,固定部包括相对设置在加热部两侧的两个固定脚114,以及分别与两个固定脚114连接的固定板115,加热部呈与双金属片13对应的u型结构,加热部的中部设有第二开槽111,加热部包括相对设置在第二开槽111两侧的两个加热条112,以及连接在两个加热条112一端之间的加热片113,其中一个加热条112的另一端分别与双金属片13的一端和与固定板115连接,另一个加热条112的另一端与双金属片13的一端连接,并与固定部间隔设置,双金属片13的两个双金属条132分别通过导电件12与两个加热条112固定,双金属片13的开槽131与加热部上的第二开槽111对应,两个加热条112与加热片113相连的一端分别向远离双金属片13的一侧折弯,在发热元件11与双金属片13之间形成间隔槽110。使加热部和双金属片13的其它部分间隔设置,即加热部和双金属片13的中部形成间隔槽110的部分间隔设置。
34.如图1
‑
4所示,本实施例还包括转动安装在支架上的衔铁15,所述支架包括相对设置的左侧板8和右侧板9,在左侧板8和右侧板9的内侧分别固定安装有左磁轭6和右磁轭5,左磁轭6和右磁轭5相对设置在线圈组件的两侧,衔铁15分别与左侧板8和右侧板9转动连接,衔铁15上设有上挂钩21,左磁轭6设有下挂钩20,弹簧10连接在上挂钩21与下挂钩20之间用于驱动衔铁15。不仅可以通过调整弹簧10的弹力大小,可以满足不同安培数产品的瞬间动作倍数,而且左磁轭6和右磁轭5能够保证小安培断路器在过载保护时能放大磁场,可防止产品误动作或不动作。
35.优选的,所述衔铁15垂直设置在左侧板8和右侧板9之间,衔铁15的两侧分别设有
凸点151,所述左侧板8和右侧板9的顶侧分别设有呈u型结构的凹槽22,凸点151能够分别插入对应的左侧板8和右侧板9的凹槽22内转动,左侧板8和右侧板9在靠近衔铁15的侧面分别设有用于限位衔铁15的限位部23,将衔铁15分别与左侧板8和右侧板9转动连接,同时通过限位部23限位衔铁15,防止衔铁15脱落。本实施例的凹槽22呈u型结构,便于凸点151插入,能够降低衔铁15的装配难度,而且通过限位部23限位衔铁15,衔铁15在转动时也不会脱落。
36.如图3
‑
4所示,所述线圈组件包括绝缘组件7以及设置在绝缘组件7内的导线组2,在导线组2的内侧设有热缩管3,在热缩管3的内侧设有铁芯4,导线组2的一端伸出绝缘组件7与连接板1连接,导线组2的另一端伸出绝缘组件7后通过软连接16连接在发热元件11与双金属片13间隔设置的部分上,导线组2用于放大铁芯4的磁场,通过放大磁场可以提高衔铁15与铁芯4之间的吸力。
37.本实施例的热电磁脱扣器的电流路径为连接板1、导线组2、软连接16,然后是并联的发热元件11和双金属片13,相对于现有的连接板、导线组、软连接16、双金属片、发热元件的常规路径,分流了发热元件11与双金属片13的电流,能够避免双金属片13出现熔断,而且双金属片13能够在自发热的同时,又能够被发热元件11加热,提高延时动作一致性。
38.如图2所示,所述铁芯4和/或发热元件11上分别设有凸台结构,所述左磁轭6和右磁轭5上分别设有与凸台结构对应的通孔结构,凸台结构上可以设置凸点结构,凸台结构穿过对应的通孔结构后铆接固定。具体的,所述左磁轭6和右磁轭5上分别设有作为通孔结构的第一通孔190,所述铁芯4的两端分别设有作为凸台结构的第一凸台19,铁芯4两端的第一凸台19分别穿过左磁轭6和右磁轭5上的第一通孔190后铆接固定。所述发热元件11的两个固定脚114的外侧分别设有作为凸台结构的第三凸台116,所述左磁轭6和右磁轭5分别设有与第三凸台116对应且作为通孔结构的第三通孔117,第三凸台116分别穿过对应的第三通孔117后铆接固定。
39.进一步,所述左磁轭6和右磁轭5上分别设有凸台结构,所述左侧板8和右侧板9分别设有与凸台结构对应的通孔结构,凸台结构穿过对应的通孔结构后铆接固定。具体的,所述左磁轭6和右磁轭5的外侧分别设有三个作为凸台结构的第二凸台18,所述左侧板8和右侧板9分别设有与第二凸台18对应的三个作为通孔结构的第二通孔180,左磁轭6和右磁轭5外侧的第二凸台18分别穿过对应的第二通孔180后铆接固定。可以理解的是,所述第一凸台19、第二凸台18和第三凸台116并不限于图中示出的数量和形状,第一凸台19、第二凸台18和第三凸台116的数量和形状可以调整,第一通孔190第二通孔180和第三通孔117的数量和形状相应匹配即可,能够减少螺钉和铆钉的使用,降低装配难度。
40.本实施例的热电磁脱扣器的装配过程为:
41.连接板1先与导线组2的一端焊接在一起,使热缩管3受热包裹铁心4后,再穿在导线组2与绝缘组件7中,发热元件11与双金属片13通过导电件12进行铆接,再将左磁轭6和右磁轭5分别安装到发热元件11上,再将衔铁15装在左侧板8和右侧板9上,装配凸点151与凹槽22时要注意卡到位,最后通过弹簧10分别与左磁轭与衔铁15连接。本实施例的双金属片13能够充分利用其他零部件结构特点,在分断时分流了双金属片13上的大电流,从而避免双金属片13被烧蚀,同时兼顾了直热式双金自发热与旁热式式热元件发热,保证了产品延时动作可靠性。
42.如图7
‑
8所示,图中a1
‑
a4为发热元件11中电流的流向,b1
‑
b4为新增的并联线路,
由于发热元件11电阻较小,因此大部分电流会按照a1
‑
a4方向流动,较小部分按照b1
‑
b4方向流动。参阅图7,并联由左侧的间隔槽110开始,电流a1分成a2和b1两个方向分别在发热元件11和双金属片13中流动,发热元件11中的电流依次经过a2
‑
a4,与双金属片13中依次经过b1
‑
b4,最后在软连接16处汇流为电流a5
‑
a6。发热元件11和双金属片13同为u型,可以减少导体截面积,电流流经路径又长,可以有效增加发热量,避免小安培电流发热不足的问题。
43.以上内容是结合具体的优选实施方式对本实用新型所作的进一步详细说明,不能认定本实用新型的具体实施只局限于这些说明。对于本实用新型所属技术领域的普通技术人员来说,在不脱离本实用新型构思的前提下,还可以做出若干简单推演或替换,都应当视为属于本实用新型的保护范围。