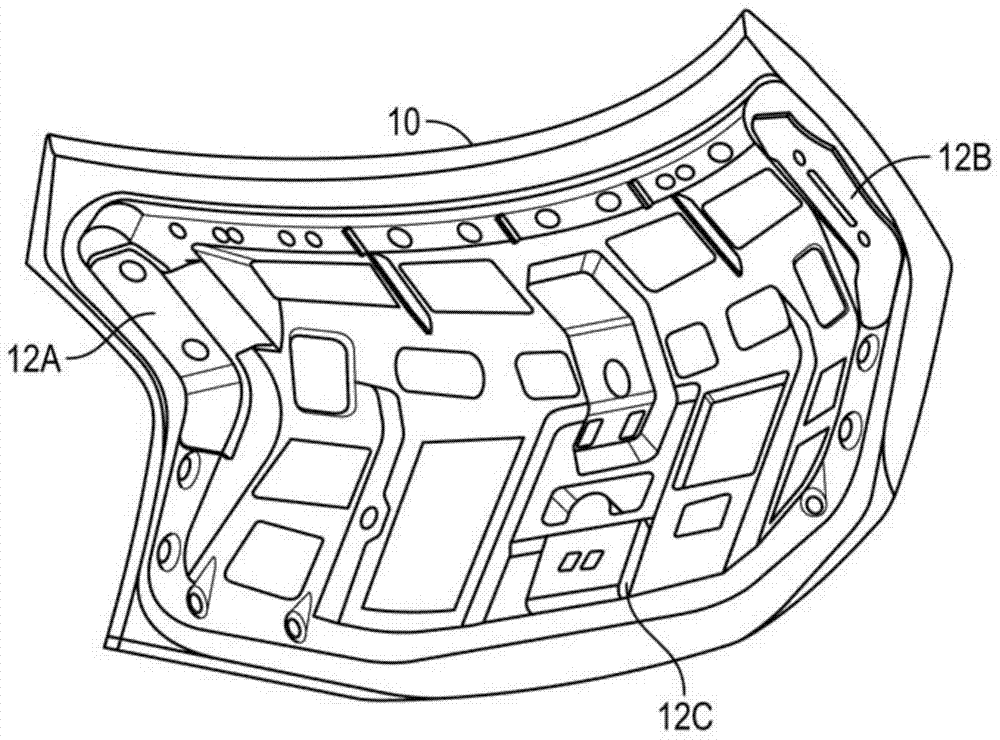
本发明一般地包括用于在组装多个部件物品的组装期间进行部件定位的系统和方法,所述部件物品例如是但不限于是车辆本体部件、船、建设设备、草坪设备或机器人。
背景技术:车辆本体包括许多结构部件,所述部件必须以足够的精确度被彼此组装,以用于适当功能和美观要求。本体包括多个子组件,其每一个具有多个子部件。通常,专用固定件设计为用于让每一个子部件相对于其要组装的一个或多个子部件呈现(present)并定位。这些固定件要求很长的提前时间和大量投资以在用在组装本体部件之前进行设计和制造。另外,固定件占据大量地面空间。
技术实现要素:一种用于将第一部件和第二部件彼此组装的系统,包括在没有任何固定件的情况下操作性地支撑第一部件的支撑件。在一些实施例中,部件可以是金属(钢、铝、镁和其合金)、塑料、或例如碳纤维或玻璃纤维的复合材料的。另外,部件可以是车辆结构部件,例如车辆本体部件,但不限于此。部件可以用于汽车车辆,或非汽车载具,例如农场载具、航海载具、航空载具等。还应理解,代替载具,部件可组装以形成设施、构造、设备、草坪设备、机器人等。支撑件的目的或功能是防止在组装操作期间第一部件不期望地移位、偏向或变形。在一些实施例中,针对用于不同部件,支撑件是可重构的。系统包括视觉系统,其配置为观察支撑的第一部件和第二部件且确定其位置。机器人系统配置为将第二部件相对于第一部件运动和定位。控制器操作性地连接到视觉系统和机器人系统,且可操作为控制机器人系统以基于通过视觉系统确定的位置将第二部件相对于第一部件定位。过程连结系统可以用于在部件已经相对于彼此定位之后通过一个或多个“过程接头”将部件连结(即保持)在一起,以便形成正确的子组件几何(subassemblygeometry)(即几何设定(geo-set))。如在本文使用的,“过程接头”包括任何机构或模式,第一部件和第二部件通过该机构或模式保持在预定相对位置。在不同实施例,过程接头可以通过机械特征部、机械连接方法、熔接结合方法、固态结合方法、粘接剂或通过机器人手臂的协作定位控制而建立。机械连接方法包括铆钉、自攻螺钉和机械铆接。熔接结合方法包括激光焊接和电阻点焊。固态结合方法包括搅拌摩擦焊和超声波焊接。可以利用包括各种方法和其组合的其他混合连接方法。在机械特征部建立过程接头时可以利用弹性平均(elasticaveraging)。控制器可以使用定位和力控制的混合来让一个或多个机器人手臂运动,以满足力限制条件和定位需求。各种过程接头和视觉系统可以实现快速单面或双面点焊,例如但不限于远程激光焊接或电阻点焊。在一实施例中,第一部件具有第一特征部,且第二部件具有与第一特征部互补的第二特征部,使得第一特征部和第二特征部建立过程接头,所述过程接头配置为具有预定强度,该预定强度足以维持第二车辆部件相对于第一车辆部件位于通过视觉系统确定的位置。在一实施例中,第一特征部是第一紧固特征部,且第二特征部是第二紧固特征部,其配置为接合第一紧固特征部。在一实施例中,粘接剂定位在第一部件和第二部件之间,建立过程接头,所述过程接头配置为具有足以维持第二车辆部件相对于第一车辆部件位于通过视觉系统确定的位置的预定强度。例如,粘接剂可以具有在第一部件和第二部件之间建立相隔距离的厚度,且相隔距离可以与第一部件到第二部件的随后结构焊接部关联。在一实施例中,涂有粘合剂的颗粒定位在第一部件和第二部件之间,建立配置为具有预定强度的过程接头,预定强度足以将第二车辆部件相对于第一车辆部件保持在通过视觉系统确定的位置。涂有粘合剂的颗粒可以具有建立第一部件和第二部件之间相隔距离的厚度,且相隔距离可以与第一部件到第二部件的随后结构焊接部关联。在一实施例中,可释放粘接剂定位在第一部件和第二部件之间,建立过程接头,所述过程接头配置为具有足以维持第二车辆部件相对于第一车辆部件位于通过视觉系统确定的位置的预定强度。可释放粘接剂建立第一部件和第二部件之间的相隔距离,且相隔距离与第一部件到第二部件的随后结构焊接部关联。在一实施例中,支撑件包括形状记忆聚合物材料,其具有临时形状和永久形状。形状记忆聚合物在应用预定激活刺激时建立永久形状。临时形状与第一部件的外表面的至少一部分互补。支撑件在第一和第二部件组装期间保持临时形状。在一实施例中,支撑件包括符合(conformto)第一部件的外表面的三维打印塑料芯部,和覆盖三维打印塑料芯部的表面的衬里。在一实施例中,机器人系统具有力传感器,且控制器控制机器人系统,以使用从力传感器确定的力水平建立第二部件抵靠第一部件的预定保持力。在一实施例中,机器人系统建立第一部件和第二部件之间的相隔距离,且相隔距离与第一部件到第二部件的随后结构焊接部关联。在一实施例中,机器人系统包括第一机器人手臂和第二机器人手臂,第一机器人手臂操作性地将第二部件保持在通过视觉系统确定的位置,以通过支撑件建立过程接头,且第二机器人手臂配置为将第一部件焊接到第二部件,同时第一机器人手臂配置为将第二部件保持在通过视觉系统确定的位置。在这样的实施例中,支撑件可以是另一机器人手臂或可重新定位的支撑件。在一实施例中,支撑件包括多个可滑动销,其配置为在第一部件置于可滑动销上时一致地滑动不同的相应距离而与第一部件的外表面相符合,支撑件由此符合第一部件的外表面。组装部件的方法包括,经由视觉系统和经由控制器确定未固定第一部件的位置,视觉系统具有至少一个摄像头,控制器操作性地连接到摄像头。方法可以进一步包括,基于确定的位置用第一机器人获取第一部件,且使用第一机器人将第一部件置于支撑件上,而没有固定件。支撑件上第一部件的位置和第二部件的位置随后经由相同或不同视觉系统和控制器确定。方法随后包括使用第一机器人或第二机器人且基于第一部件在支撑件上的确定位置将第二部件相对于第一部件定位。第一部件随后经由无固定件的过程接头根据所述定位相对于第二部件保持。定位可以包括提供部件之间的适当相隔距离(即间隙),以便实现随后激光焊接过程。例如,在焊接部区域中材料之间存在约0.3mm的相隔距离时,镀锌钢的激光焊接可以具有改进的质量和减小的多孔性。该相隔距离可以通过允许在固化之前焊接气体从焊接区域逃逸而改善焊接质量。在一些情况下,相隔距离应该被最小化。例如铝对铝的激光焊接应该在焊接部区域中相隔距离小于约0.125mm的情况下完成。在一实施例中,通过用具有第一预定强度的过程接头将第一部件连结到第二部件而进行所述保持,且所述连结之后,用具有大于第一预定强度的第二预定强度的结构接头将第一部件焊接到第二部件。在所述焊接期间仅通过过程接头而不使用固定件保持第二部件相对于第一部件的定位。在一实施例中,定位是经由一个机器人(即第一机器人)实现的,且在第一机器人保持定位时通过额外机器人(即第二机器人)将第一部件焊接到第二部件。在该方法下,将第一部件相对于第二部件保持可以包括保持第二部件抵靠第一部件的预定力。一种用于使用可释放粘接剂系统组装第一部件和第二部件的系统,可释放粘接剂系统用于将第一部件与第二部件连结,包括主材料,具有(i)第一部分,第一部分配置为定位为与第一部件的第一表面接触,和(ii)与第一部分相对的第二部分,其配置为定位为与第二部件的第二表面接触;定位为与第一表面的部分接触的主材料的第一部分配置为(i)维持与第一部件的第一表面的结合,直至第一预定剪切力施加在第一表面上,(ii)维持与第一部件的第一表面结合,直至第一预定拉力施加在第一表面上,和(iii)响应于施加在第一表面上的至少第一预定剥离力,释放与第一部件的第一表面结合。在一实施例中,定位为与第二部件的第二表面接触的主材料的第二部分配置为:(i)维持与第二部件的第二表面的结合,直至第二预定剪切力施加在第二表面上,(ii)维持与第二部件的第二表面的结合,直至第二预定拉力被施加在第二表面上,且(iii)响应于施加在第二表面上的至少第二预定剥离力,释放与第二部件的第二表面的结合。在一实施例中,用于组装第一部件和第二部件的系统包括配置为在没有任何固定件的情况下支撑第一部件的支撑件。第一部件包括第一紧固特征部。系统包括定位系统,所述定位系统确定第一部件在被支撑件支撑时第一部件的位置和确定第二部件相对于第一部件的位置。第二部件包括第二紧固特征部。系统包括机器人系统,其将第二部件相对于第一部件移动和定位。系统包括与定位系统和机器人系统通信的控制器,以操作机器人系统,所述机器人系统基于通过定位系统确定的位置将第二部件的第二紧固特征部相对于第一部件的第一紧固特征部定位。第一和第二紧固特征部彼此接合以将第一和第二部件固定在一起,以形成具有预定强度的过程接头,所述过程接头将第二部件相对于第一部件保持。系统可以具有多个第一紧固特征部和多个第二紧固特征部。在一实施例中,第一紧固特征部和第二紧固特征部彼此接合以建立第一部件和第二部件之间的相隔距离。相隔距离与随后的结构焊接部的置放关联,所述结构焊接部将第一和第二部件固定在一起。在一实施例中,第一和第二紧固特征部中的一个包括凸片,而第一和第二紧固特征部中的另一个限定洞。凸片设置在洞中以形成过程接头。第一紧固特征部和第二紧固特征部可以彼此接合以建立第一部件和第二部件的相隔距离,且第一和第二紧固特征部中邻近洞的那个和凸片中的至少一个包括延伸部,以限制凸片插入到洞的距离,以建立相隔距离。在一实施例中,第一和第二紧固特征部中的一个包括突出部而第一和第二紧固特征部中的另一个限定开口。突出部定位在开口中以形成过程接头。第一紧固特征部和第二紧固特征部彼此接合以建立第一部件和第二部件之间的相隔距离。第一和第二部件中的至少一个包括延伸部,以限制突出部插入到开口中的距离,以建立相隔距离。。在一实施例中,第二紧固特征部包括限定开口的保持构件,保持构件是柔性的,使得在突出部和保持构件彼此接合时突出部使得保持构件变形。在一实施例中,第一紧固特征部和第二紧固特征部彼此接合以建立第一部件和第二部件之间的相隔距离。突出部包括限定了沟槽的外周边,保持构件接合所述沟槽,以限制突出部插入到保持构件的开口中的距离以建立相隔距离。在一实施例中,第一紧固特征部包括第一凸片且第二紧固特征部包括第二凸片,第一和第二凸片彼此接合以形成过程接头。例如,第一紧固特征部和第二紧固特征部可以彼此接合以建立第一部件和第二部件之间的相隔距离。第一和第二凸片中的至少一个包括延伸部,以限制第一和第二凸片彼此接合的距离,以建立相隔距离。在一实施例中,第一和第二紧固特征部中的一个包括第一突出部且第一和第二紧固特征部中的另一个包括限定了中空部的第二突出部,第一突出部设置在第二突出部的中空部中以形成过程接头。例如,第一紧固特征部和第二紧固特征部可以彼此接合以建立第一部件和第二部件之间的相隔距离,且第一和第二突出部中的至少一个可以是锥形的以限制第一突出部插入到中空部分中的距离,以建立相隔距离。在一实施例中,定位系统可以包括视觉系统以定位第一部件。视觉系统可以包括摄像头,所述摄像头观察第一部件以识别第一部件的位置。摄像头可以观察第二部件,以识别第二部件的位置。组装第一部件和第二部件的方法包括,使用机器人将第一部件置于没有固定件的支撑件上,第一部件包括第一紧固特征部,经由定位系统在第一部件位于支撑件时确定第一部件的位置,和经由定位系统确定第二部件的位置,第二部件包括第二紧固特征部。方法进一步包括,使用机器人基于经由定位系统确定的第一部件在支撑件上的位置而将第二部件相对于第一部件定位,且基于通过定位系统确定的位置根据第二部件相对于第一部件的定位将第一部件的第一紧固特征部和第二部件的第二紧固特征部接合在一起,以形成具有第一预定强度的过程接头,过程接头将第二部件相对于第一部件保持。在一实施例中,方法进一步包括将第一部件和第二部件焊接在一起,以在形成过程接头之后形成结构接头,结构接头具有大于第一预定强度的第二预定强度。在第一部件和第二部件彼此焊接期间通过过程接头在没有固定件的情况下保持第一部件和第二部件的相对位置。在一实施例中,将第一部件的第一紧固特征部和第二部件的第二紧固特征部接合在一起进一步包括将凸片插入到洞中,以形成过程接头。在一实施例中,将第一部件的第一紧固特征部和第二部件的第二紧固特征部接合在一起进一步包括将突出部插入到开口中,以形成过程接头。例如,将突出部插入开口以形成过程接头进一步包括,将突出部插入限定了开口的保持构件。方法可以进一步包括在突出部插入到开口中时使保持构件变形。在一实施例中,将第一部件的第一紧固特征部和第二部件的第二紧固特征部接合在一起进一步包括将第一凸片和第二凸片接合在一起,以形成过程接头。在一实施例中,将第一部件的第一紧固特征部和第二部件的第二紧固特征部接合在一起进一步包括将第一突出部插入第二突出部的中空部,以形成过程接头。在一实施例中,将第一部件的第一紧固特征部和第二部件的第二紧固特征部接合在一起进一步包括将多个第一紧固特征部与相应第二紧固特征部接合在一起。用于组装第一部件和第二部件的系统包括配置为支撑第一部件而没有任何固定件的支撑件。组件系统还包括定位系统,所述定位系统确定第一部件在被支撑件支撑时第一部件的位置和确定第二部件相对于第一部件的位置。组装系统进一步包括机器人系统和施加器系统,机器人系统将第二部件相对于第一部件运动和定位,施加器系统将粘接剂施加到第一部件和第二部件中的至少一个。组装系统包括与定位系统和机器人系统通信的控制器,以操作机器人系统,机器人系统基于通过定位系统确定的位置将第二部件相对于第一部件定位,以将第一和第二部件粘接在一起,以形成具有预定强度的过程接头,过程接头将第二部件相对于第一部件保持。在一实施例中,粘接剂具有建立第一部件和第二部件之间相隔距离的厚度。相隔距离与随后的结构焊接部的置放关联,所述结构焊接部将第一和第二部件固定在一起。在一实施例中,粘接剂施加到第二部件,且第二部件粘接到第一部件,使得粘接剂定位在第一部件和第二部件之间,以形成过程接头。在一实施例中,第一和第二部件相对于彼此定位且粘接剂施加到第二部件的边缘,这使得粘接剂位于第一和第二部件之间以形成过程接头。在一实施例中,在将第一和第二部件粘接在一起之后,过程接头从约1.0秒到约50.0秒固化。系统可以进一步包括施加到过程接头的加速手段,以减少固化过程接头的时间。在一实施例中,定位系统包括视觉系统,以定位第一部件,且视觉系统可以包括摄像头,其观察第一部件以识别第一部件的位置。摄像头观察第二部件以识别第二部件的位置。在一实施例中,机器人系统包括与控制器通信的力传感器,以在将第一和第二部件粘接在一起时测量施加到第一部件和第二部件中的至少一个的力的量。组装第一部件和第二部件的方法包括使用机器人将第一部件置于没有固定件的支撑件上,经由定位系统在第一部件位于支撑件时确定第一部件的位置,和经由定位系统确定第二部件的位置。方法进一步包括将粘接剂施加到第一部件和第二部件中的至少一个,且基于经由定位系统确定的第一部件在支撑件上的位置使用机器人将第二部件相对于第一部件定位。方法进一步包括基于通过定位系统确定的位置根据第二部件相对于第一部件的定位将第一部件和第二部件粘接在一起,以形成具有第一预定强度的过程接头,过程接头将第二部件相对于第一部件保持。在一实施例中,方法进一步包括将第一部件和第二部件焊接在一起,以在形成过程接头之后形成结构接头,结构接头具有大于第一预定强度的第二预定强度。在第一部件和第二部件焊接在一起期间通过过程接头在没有固定件的情况下保持第一部件和第二部件相对位置。在一实施例中,将粘接剂施加到第一部件和第二部件中的至少一个进一步包括将粘接剂施加到第二部件的边缘,使得粘接剂位于第一和第二部件之间以形成过程接头。在一实施例中,方法进一步包括在将第一和第二部件粘接在一起之后,过程接头从约1.0秒到约50.0秒固化。方法可以进一步包括对过程接头施加加速手段,以减少固化过程接头的时间。方法可以进一步包括在将第一和第二部件粘接在一起时经由力传感器测量施加到第一部件和第二部件中的至少一个的力的量。用于组装第一部件和第二部件的系统包括配置为操作性地支撑第一部件而没有任何固定件的无固定件的支撑件。系统包括定位系统,其配置为确定第一部件的位置和将第一部件位置结果返回且确定第二部件位置和将第二部件位置结果返回。系统包括机器人系统,其配置为将第二部件拾取和运动且进一步配置为将第二部件相对于第一部件定位。系统包括施加器,其散布涂有粘合剂的颗粒且将涂有粘合剂的颗粒施加到第一部件和第二部件中的至少一个。系统包括与定位系统、机器人系统和施加器系统每一个通信的控制器。控制器具有处理器和实体的非瞬时存储器,在其上记录有指令,所述指令用于基于第一部件位置结果和第二部件位置结果联接第一部件和第二部件以形成过程接头,从而涂有粘合剂的颗粒在过程接头处设置在第一部件和第二部件之间。涂有粘合剂的颗粒建立和第二部件之间的相隔距离,使得相隔距离与随后的焊接结构接头的位置关联,结构接头将第一部件和第二部件牢固地(rigidly)固定。系统可以配置为使得过程接头具有将第二部件相对于第一部件保持的第一预定强度,且焊接结构接头具有大于第一预定强度的第二预定强度。在系统的实施例中,第一部件具有第一过程接头界面,且第二部件具有第二过程接头界面。在机器人系统在第一过程接头界面和第二过程接头界面处将第一部件与第二部件联接时,过程接头被形成,使得第一部件与第二部件的联接使得涂有粘合剂的颗粒与第一过程接头界面和第二过程接头界面每一个接触。在该系统的实施例中,施加器系统施加单层涂有粘合剂的颗粒到第一过程接头界面和第二过程接头界面中之一,且单层涂有粘合剂的颗粒具有一厚度,该厚度建立激光焊接所需的相隔距离,从而单层涂有粘合剂的颗粒联接第一部件和第二部件且其厚度保持所需相隔距离。在该系统的一实施例中,施加器系统施加至少一层涂有粘合剂的颗粒到第一过程接头界面处的第一部件和第二过程接头界面处的第二部件的每一个。施加器系统可以施加第一层涂有粘合剂的颗粒和第二层涂有粘合剂的颗粒到第一过程接头界面和第二过程接头界面每一个,使得第二层的涂有粘合剂的颗粒间断置于第一层涂有粘合剂的颗粒上和之间。在系统的一实施例中,施加第一层和第二层的涂有粘合剂的颗粒,以便沿第一过程接头界面和第二过程接头界面之一限定多个颗粒空腔。施加第一层和第二层的涂有粘合剂的颗粒,以便沿第一过程接头界面和第二过程接头界面之另一限定多个颗粒柱体,使得在第一过程接头界面和第二过程接头界面联接以形成过程接头时,每一个颗粒空腔配置为接收多个颗粒柱体中之一,在它们之间形成集合体。在系统的实施例中,多个颗粒空腔和多个颗粒柱体的集合体联接第一部件和第二部件,同时将至少一个第二部件相对于第一部件对准。多个颗粒空腔和多个颗粒柱体的集合体保持激光焊接所需的相隔距离。在系统的一实施例中,第一过程接头界面沿其限定多个沟道。施加器系统可以至少将第一层和第二层的涂有粘合剂的颗粒施加到第二过程接头界面。第一层的涂有粘合剂的颗粒可以在第二过程接头界面上间断地间隔开,且第二层的颗粒可以间断且直接置于第一层颗粒上,使得第一层和第二层形成沿第二过程接头界面彼此间隔开的多个涂有粘合剂的颗粒柱体。在系统的实施例中,通过第一过程接头界面限定的相应沟道每一个配置为接收通过施加到第二过程接头界面的涂有粘合剂的颗粒形成的多个柱体中之一,在它们之间形成连接,使得多个沟道和多个柱体的连接将第一部件和第二部件联接且保持激光焊接所需的相隔距离。在系统的一实施例中,定位系统包括至少一个摄像头,其观察第一部件以确定第一部件的位置,且该至少一个摄像头还观察第二部件,以确定第二部件的位置。该至少一个摄像头可以将第一部件位置结果返回到控制器且将第二部件位置结果返回到控制器。在该系统的实施例中,机器人系统包括与控制器通信的力传感器,以在第一部件和第二部件联接时测量施加到第一部件和第二部件中至少一个的力的量。在该系统的实施例中,第一部件和第二部件包括镀锌钢,且相隔距离为约0.3毫米。组装第一部件和第二部件的方法包括,经由控制器信号通知定位系统以确定第一部件在无固定件的支撑件上的位置,且将第一部件位置结果返回到控制器。方法进一步包括,经由控制器信号通知定位系统以确定第二部件位置且将第二部件位置结果返回到控制器。方法包括经由控制器命令施加器系统将涂有粘合剂的颗粒施加到第一过程接头界面处的第一部件和第二过程接头界面处的第二部件中的至少一个,且经由控制器命令机器人系统基于通过定位系统返回的第一部件位置结果将第二部件相对于第一部件定位。方法进一步包括,经由控制器命令机器人系统在第一过程接头界面和第二过程接头界面处联接第一部件和第二部件,以形成具有第一预定强度的过程接头,其将第二部件相对于第一部件维持。在一实施例中,方法进一步包括,经由控制器命令焊接设备在过程接头处将第一部件焊接到第二部件,以形成具有第二预定强度的结构接头,第二预定强度大于第一预定强度。在结构接头形成期间仅通过过程接头且在没有固定件的情况下将第一部件和第二部件相对于彼此保持。在一实施例中,命令施加器系统将涂有粘合剂的颗粒施加到在第一过程接头界面处的第一部件和在第二过程接头界面处的第二部件的至少一个进一步包括,通过施加器系统将单层涂有粘合剂的颗粒(其具有限定的厚度)施加到第一过程接头界面和第二过程接头界面中之一,使得单层涂有粘合剂的颗粒联接第一部件和第二部件,且单层涂有粘合剂的颗粒的厚度保持激光焊接所需的相隔距离。在一实施例中,命令施加器系统将涂有粘合剂的颗粒施加到第一过程接头界面处的第一部件和在第二过程接头界面处的第二部件中的至少一个进一步包括,通过施加器系统将第一层涂有粘合剂的颗粒和第二层涂有粘合剂的颗粒施加到第一过程接头界面和第二过程接头界面的每一个,使得第二层涂有粘合剂的颗粒间断置于第一层涂有粘合剂的颗粒上和之间,以便沿第一过程接头界面和第二过程接头界面中之一限定多个颗粒空腔,且沿第一过程接头界面和第二过程接头界面之另一限定多个颗粒柱体。第一部件和第二部件联接以形成过程接头,多个颗粒空腔每一个配置为接收多个颗粒柱体中的一个,在它们之间形成集合体,使得多个颗粒空腔和多个颗粒柱体的集合体联接第一部件和第二部件且保持激光焊接所需的相隔距离。在一实施例中,命令施加器系统将涂有粘合剂的颗粒施加到在第一过程接头界面处的第一部件和在第二过程接头界面处的第二部件中的至少一个一个进一步包括,通过施加器系统将至少第一层和第二层涂有粘合剂的颗粒施加到第二过程接头界面。第一层的颗粒在第二过程接头界面上间断间隔开,且第二层颗粒间断且直接置于第一层颗粒上,使得第一层和第二层沿第二过程接头界面形成彼此间隔开的多个柱体。第一过程接头界面沿其限定多个沟道,使得通过第一过程接头界面限定的相应沟道每一个配置为接收通过涂有粘合剂的颗粒形成的多个柱体中的一个,所述涂有粘合剂的颗粒施加到第二过程接头界面,在它们之间形成连接,使得多个沟道和多个柱体的连接将第一部件和第二部件联接同时将第二部件相对于第一部件对准。多个颗粒柱体和多个沟道的连接保持激光焊接所需的相隔距离。用于组装第一部件和第二部件的系统包括,操作性地支撑第一部件而没有任何固定件的支撑件;机器人系统,配置为将第二部件相对于第一部件保持就位;控制器,操作性地连接到机器人系统且可操作为控制机器人系统,以将第二部件相对于第一部件定位;和焊接器,配置为在第二部件保持就位时将第一和第二部件彼此焊接。在用于组装第一部件和第二部件的系统的实施例中,第二部件相对于第一部件的位置建立部件之间的相隔距离。相隔距离与通过焊接器将第一部件与第二部件进行随后的激光焊接关联。在用于组装第一部件和第二部件的系统的实施例中,机器人系统具有力传感器。控制器控制机器人系统,以建立第二部件抵靠第一部件的预定保持力。在用于组装第一部件和第二部件的系统的实施例中,机器人系统包括第一机器人手臂和第二机器人手臂,第一机器人手臂操作性地将第二部件保持在通过视觉系统确定的位置,且第二机器人手臂配置为将第一部件焊接到第二部件,同时第一机器人手臂配置为将第二部件保持在通过视觉系统确定的位置。在一实施例中,支撑件可以是另一机器人手臂或可重新定位的支撑件。焊接器可以整合在机器人手臂的末端执行器中,所述机器人手臂还保持第二部件。在用于组装第一部件和第二部件的系统的实施例中,视觉系统配置为观察被支撑的第一部件和第二部件且确定其位置。控制器操作性地连接到视觉系统,且进一步基于通过视觉系统确定的位置控制机器人系统。组装第一部件和第二部件的方法包括,经由第一机器人将第一部件置于没有固定件的支撑件上,确定第一部件在支撑件上的位置和第二部件的位置,且使用第一机器人或第二机器人且基于第一部件在支撑件上的被确定的位置将第二部件相对于第一部件定位。方法进一步包括,根据定位将第二部件相对于第一部件保持以建立过程接头,且在将第二部件相对于第一部件保持期间将第一部件与第二部件焊接。在所述焊接期间在没有固定件的情况下保持第一部件和第二部件的相对位置。在一实施例中,将第二部件相对于第一部件保持是经由一个机器人实现的,且在保持期间第一部件与第二部件的焊接经由额外机器人实现。在一实施例中,将第二部件相对于第一部件保持和在保持期间将第一部件与第二部件焊接经由单个机器人实现。在一实施例中,将第二部件相对于第一部件保持包括保持第二部件抵靠第一部件的预定力。本文所述的系统和方法可以降低生产成本和提前时间,例如引入包括例如新的车辆模块这样的部件的新的产品时,其中部件是车辆本体部件。生产成本和提前时间可以减小,因为不需要用于不同阶段的专用固定件和夹持件。复杂的零件保持托盘和固定件不被需要,因为视觉系统能获得部件和定位部件,而不需要其精确的初始定位。另外,因为本文公开的许多无固定件支撑件和末端执行器是可重构的,所以实现用于不同子组件的灵活且快速重构。在下文结合附图进行的对实施本发明的较佳模式做出的详尽描述中能容易地理解上述的本发明的特征和优点以及其他的特征和优点。附图说明图1是以分解视图显示的车辆本体部件的组件的示意图。图2是图1的组件的示意性透视图。图3是组装车辆本体部件的方法流程图。图4是利用图3方法的本体车间组装系统的示意图。图5是基于来自视觉系统的信息获得第一车辆本体部件的机器人的示意图。图6是图4的一部分系统的示意图,包括无固定件的支撑件、视觉系统和机器人系统,如包括在图4的系统中的那些。图7是第一实施例的可重构无固定件的支撑件的部分截面示意图,所述支撑件显示为支撑第一车辆本体部件。图8是第二实施例的可重构无固定件的支撑件的部分截面示意图,所述支撑件显示为支撑第一车辆本体部件。图9是第三实施例的可重构无固定件的支撑件的部分截面示意图,所述支撑件显示为支撑第一车辆本体部件。图10是第四实施例的可快速制造的无固定件的支撑件的部分截面示意图,所述支撑件显示为支撑第一车辆本体部件。图11是第五实施例的可重构无固定件的支撑件的透视示意图,所述支撑件显示为支撑第一车辆本体部件。图12是保持了一些第二车辆本体部件的无固定件箱的透视示意图。图13是具有机械过程接头的第一和第二车辆本体部件的部分分解示意图。图14是在机械过程接头处连结的第一和第二车辆本体部件的部分截面示意图。图15是具有粘接过程接头的第一和第二车辆本体部件的部分截面示意图。图16是具有通过涂有粘合剂的颗粒层建立的过程接头的第一和第二车辆本体部件的部分截面示意图。图17是通过机器人建立的过程接头且显示了协作远程激光焊接的示意性部分侧视图。图18是彼此间隔开的第一紧固特征部和第二紧固特征部的实施例的示意性部分侧视图。图19是彼此接合的图18实施例的第一和第二紧固特征部的示意性部分侧视图。图20是图18-19的第一和第二紧固特征部的示意性部分侧视图。图21是彼此间隔开的另一实施例的第一紧固特征部和第二紧固特征部的示意性部分侧视图。图22是彼此接合的图21实施例的第一和第二紧固特征部的示意性部分侧视图。图23是彼此间隔开的另一实施例的第一紧固特征部和第二紧固特征部的示意性透视图。图24是彼此间隔开的图23实施例的第一和第二紧固特征部的示意图。图25是彼此接合图23-24的实施例的第一和第二紧固特征部的示意图。图26是彼此接合的图23-25的实施例的第一和第二紧固特征部的示意性侧视图。图27是另一实施例的第一紧固特征部和第二紧固特征部的示意图。图28是彼此接合的图27的实施例的第一和第二紧固特征部的示意图。图29是第一和第二本体部件的示意性分解透视图。图30是结构上连结在一起的第一和第二本体部件的示意性部分截面图。图31是组装多个本体部件的方法的示意性流程图。图32是施加到第一本体部件的粘接剂的示意性透视图。图33是具有粘接剂的第一和第二本体部件的示意性部分截面图,在它们之间形成过程接头。图34是施加到第二本体部件的粘接剂的示意性部分截面图。图35是第一和第二本体部件的示意性部分侧视图,粘接剂施加到第二本体部件的边缘。图36是第一和第二本体部件的示意性部分截面图,具有形成相隔距离的过程接头。图37是组装多个本体部件的方法的示意性流程图。图38是组装系统的示意图,包括无固定件的支撑件、定位系统、机器人系统和施加器系统,如被包括在图4的本体车间系统中的。图39是以单层施加到第一部件和第二本体部件中的至少一个的涂有粘合剂的颗粒的第一示意图。图40是第一部件和第二部件的部分截面示意图。在它们之间具有涂有粘合剂的颗粒,如在图39中所施加的。图41是第一部件和第二部件的部分截面示意图,在它们之间具有涂有粘合剂的颗粒,如在图39所施加的,使得单层涂有粘合剂的颗粒的厚度保持激光焊接所需的相隔距离。图42是以多层施加到第一部件和第二本体部件每一个的涂有粘合剂的颗粒的第二示意图。图43是第一部件和第二部件的部分截面示意图,在它们之间具有涂有粘合剂的颗粒,如在图42中所施加的。图44是第一部件和第二部件的部分截面示意图,在它们之间具有涂有粘合剂的颗粒,如在图42所施加的,使得施加到第一部件的涂有粘合剂的颗粒层和施加到第二部件的涂有粘合剂的颗粒层的集合体保持激光焊接所需的相隔距离。图45是以多层施加到与第一部件关联的第二部件每一个的涂有粘合剂的颗粒的第三示意图,所述第一部件沿其第一过程接头界面限定多个沟道。图46是第一部件和第二部件的部分截面示意图,在它们之间具有涂有粘合剂的颗粒,如在图45中所施加的。图47是第一部件和第二部件的部分截面示意图,在它们之间具有涂有粘合剂的颗粒,如在图45所施加的,使得施加到第二部件的涂有粘合剂的颗粒层和通过第一部件限定的多个沟道的集合体保持激光焊接所需的相隔距离。图48是组装多个本体部件的本发明方法的步骤的详细流程图。图49是组装车辆本体部件的方法流程图。图50是系统一部分的侧视示意图,包括无固定件的支撑件、视觉系统和机器人系统,以建立过程接头和实施协作焊接。图51是系统一实施例的侧视示意图,其使用可重构无固定件的支撑件和具有可重构末端执行器的机器人手臂,以建立过程接头和实现协作电阻点焊。图52是系统一实施例的侧视示意图,其使用可重构无固定件的支撑件和具有可重构末端执行器的机器人手臂以建立过程接头,且具有与末端执行器整合的焊接头以实现协作激光焊接。图53示出了根据本发明实施例的可拆卸粘接剂的侧视图。图54是图53的可拆卸粘接剂的替换实施例透视图的。图55是图53的可拆卸粘接剂的第二替换实施例的侧视图。图56是图53的可拆卸粘接剂的第三替换实施例的透视图。图57是图53用于施加图53的可释放粘接剂的胶带布散器的平面示意图。图58是在无固定件应用中使用图57的胶带布散器将第一和第二部件彼此固定的过程的透视示意图。图59是进一步显示了图58的过程的透视示意图。具体实施方式参见附图,其中相同的附图标记在附图中表示相同的部件,图1显示了第一部件10和多个第二部件12A、12B、12C的分解视图。在所示实施例中,第一部件10是第一车辆本体部件10,且可以如此称谓。更具体地,第一车辆本体部件10为行李箱盖内板。第二部件12A、12B、12C为用于第一车辆本体部件10的加强部件,且可以称为第二车辆本体部件。附图标记12也可以用于指任何第二车辆部件12A、12B、12C。图2显示了在完成组装之后的第一部件10和第二部件12A、12B、12C。如本文描述的,在不使用专用固定件以呈现(present)、定位或保持部件10、12A、12B、12C的情况下,实现了第一车辆部件10和第二车辆部件12A、12B、12C的组装。代替地,一个或多个视觉引导的机器人将部件相对于彼此置放就位。如此,不需要要被彼此组装的每一个部件的确切位置的精确几何设定,因为视觉系统能在机器人操作期间将相对部件位置通知给机器人。一旦部件相对于彼此定位,则建立过程接头以将部件保持在相对位置(包括材料之间的相隔距离),直到结构接头在随后的处理操作中形成。过程接头可以用机械特征部、机械连结方法、熔接结合方法、固态结合方法、粘接剂、通过一个或多个机器人提供的保持力或以其他方式实现。换句话说,不需要或不使用夹持件,因为它们被一个或多个过程接头所代替。过程接头具有第一强度,且结构接头具有更大的第二强度。结构接头可以是激光焊接部、电阻点焊部、其他熔接焊接部(例如MIG焊接部)、固态结合部(例如超声波焊接部或摩擦搅拌焊接部)、机械接头(例如铆钉、自攻螺钉)、结构粘接剂、或上述方法的混合方法,其配置为在组件在安装在车辆上时的可用寿命期间将第一和第二部件彼此保持在一起。如果激光焊接用于结构接头,则过程接头可以提供预定的相隔距离。例如,在材料在焊接部区域中在它们之间具有约0.3mm的相隔距离时,镀锌钢板的激光焊接可以具有改进的质量和减小的多孔性。该相隔距离可以通过允许焊接气体在固化之前从焊接区域逃逸而改善焊接质量。在一些情况下,相隔距离应该被最小化。例如铝对铝的激光焊接应该在焊接部区域中相隔距离小于约0.125mm的情况下完成。在本文公开了用于定位部件和用于形成过程接头的各种模式。图3显示了组装方法100的流程图,且图4显示了从部件引入到完成卷边(hem)的过程中利用方法100的组装系统200的一个例子(显示为本体车间组装系统)。在图3中,方法100包括图框110,其中机器人从不被固定的初始支撑件13拾取并置放第一部件10,初始支撑件例如是标准平坦传动带输送器、存储箱或运输架。初始支撑件13在图4中显示为运输架。多个相似的第一车辆本体部件10显示为堆叠在初始支撑件13中。在该系统中各第一车辆本体部件显示为处于方法100的不同阶段。控制器C(如图5所示)使用任何合适的定位系统确定不被固定的第一部件10在初始支撑件13上的位置,所述定位系统例如具有至少一个摄像头18的视觉系统16。视觉系统16的各种结构中的任何一个或多个可以用于将视觉信息提供到控制器C。在图5所示的在一个例子中,视觉系统16包括三维静止摄像头18,其在视野20上提供光,在第一部件10在传送带14上于摄像头18下方经过时跨经第一部件10形成光条纹(或其他样式)。在各种实施例中,光可以是激光束。摄像头18和控制器C可以配置为定位各种特征,例如部件10的孔或凸缘。替换地或额外地,控制器C可以基于光在部件10表面上的各种深度而记录部件10的轮廓。在一些实施例中,多个摄像头18可位于组装单元中的固定位置,或可以安装在机器人手臂22上。图6显示了两个摄像头18,其在框架19上彼此邻近安装,以提供在机器人手臂22上的部件10和部件12A、12B、或12C的立体视觉。在实施例任何中,摄像头(一个或多个)18操作性地连接到控制器C,控制器C还控制机器人系统24的一个或多个机器人23。基于从摄像头18接收的信息,控制器C则提供控制信号,所述控制信号促动在方法100中使用的一个或多个机器人的机器人手臂(一个或多个)22。控制器C可包括处理器和在其上记录指令的存储器,所述指令用于与视觉系统16、机器人系统24、传感器(一个或多个)等通信。控制器C配置为经由处理器执行来自存储器的指令。例如,控制器C可以是主机或分布式系统,例如数字计算机或微电脑这样的计算机,其用作具有处理器的车辆的控制模块,且作为存储器,例如只读存储器(ROM)或闪速存储器这样的实体非瞬时计算机可读存储器。控制器C还可具有随机访问存储器(RAM)、电可消除可编程只读存储器(EEPROM)、高速时钟、模拟-数字(A/D)和/或数字-模拟(D/A)电路,和任何所需的输入/输出电路和相关的装置,以及任何所需的信号调节和/或信号缓冲电路。因此,控制器C可包括对于监测和控制视觉系统16来说必要的所有软件、硬件、存储器、算法、连接件、传感器等。如此,控制方法可实施为与控制器C相关的软件或固件。应理解,控制器C还可包括能分析来自各种传感器的数据、比较数据、作出控制和监测视觉系统16、机器人系统24、传感器等所需的必要决定的任何装置。如图5所示,手臂22上的末端执行器26可以包括定位为连接到部件10的一系列抓持器28。机器人手臂22则被控制器C促动,以通过末端执行器26将部件10从传送带14退回,使用从视觉系统16的视觉位置数据确定的位置将末端执行器26定位在部件10上。抓持器28可以包括可重构吸盘、让吸盘相对于彼此运动的滑动销、类似于针对图7所述的适形材料(conformablematerial)、磁体等。在图6中,末端执行器26保持要被定位在部件10上的部件12B,如箭头A1所示。部件12A、12C仅出于参考目的被示意性地示出,且其每一个将通过相同或不同的机器人手臂22被分别运动到在被支撑的第一部件10上的位置,如箭头A2和A3示出。可适于使用的末端执行器的其他实施例包括如下公开的那些,其每一个通过参考以其全部内容并入:Lin等人的美国专利No.8,684,418;Lin等人的美国专利No.8,496,425;Lin的美国专利No.8,371,631;Lin等人的美国专利No.8,087,845;Lin等人的美国专利No.8,033,002;Lin等人的美国专利No.8,025,277;Lin等人的美国专利No.7,971,916;Lin等人的美国专利申请公开No.20120280527;Lin等人的美国专利申请公开No.20110182655;和Lin等人的美国专利申请公开No.20110017007。再次参见图3和4,在方法100的图框120中,第一部件10被机器人系统24置于无固定件(fixtureless)的支撑件30上,如图6所示。无固定件的支撑件30可以称为零件搁置结构(partrest),且在基部32上。在一个实施例中,基部32可以是缓慢运动传送带,其在图4的组装系统200的工作站之间运动。替换地,基部32可以是静止的,且所使用的各种机器人23可朝向基部32和支撑件30运动,以实现一系列组装步骤。在各种实施例中,无固定件的支撑件30可以是可重构的支撑件,使其在不同组装过程中用于不同配置的本体部件。在其他实施例中,无固定件的支撑件可以是不可重构的,但是具有相对便宜的材料。在所有实施例中,无固定件的支撑件30仅需要将部件10支撑到相对不太精确(与所使用的机器人系统是“盲的”的组装系统相比)的位置。这是因为,得益于从视觉系统16收集的位置信息,机器人23能相对于第一部件10定位第二车辆本体部件12A、12B、或12C。图7显示了图6的无固定件的支撑件30的一个实施例,其被标记为附图标记30A。支撑件30A是可重构的柔性容器40,其限定了填充有颗粒44的空腔42,类似于豆包(beanbag)。容器40具有聚合物或其他耐久平滑材料的柔性衬里。颗粒44可以具有各种形状,其至少一些可以是非球形的。在控制器C促动可开闭阀46以打开阀46时,真空源V操作性地置于与空腔42流体连通。样本第一部件10可被压靠容器40,而真空V作用在空腔42中以从该空腔42除去空气。颗粒44由于真空V而被彼此拉近抵靠且抵靠部件10,且符合部件10的外表面的形状。形成在容器40中的凹部48由此足够地符合部件10,以支撑部件10,用于方法100的随后阶段。支撑件30A由此提供机械灵活性(flexibility)和可重构性。例如,为了重构支撑件30A,使得真空V的应用去除,且通气阀(未示出)允许空气进入空腔42。颗粒44和容器40随后松弛且可重新塑形以重构支撑件30A。在具有与部件10不同形状或相同形状的不同部件被压靠柔性容器40时,真空V可随后被应用。图8显示了图6的无固定件的支撑件30的另一实施例,其被标记为附图标记30B。支撑件30B是可重构的柔性容器40A。容器40A具有聚合物或其他耐久平滑材料的柔性衬里。一丛(abedof)刚性销50包含在容器40A的空腔42中。销50布置为彼此平行。每一个销50的底部可固定到受控制器控制的相应促动器52,以朝向部件10提供预定高度和/或力。销50可以伸缩,或可以具有固定长度,促动器52根据需要延伸。促动器52可以是电磁的、液压、气动或任何其他合适类型的促动器。样本部件10可置于容器40A上。一旦被促动,与部件10的一部分对准的那些销50将由于部件10而经历反作用力,且将停止向上运动。以这种方式,容器40A将提供与部件10的外表面的形状符合的凹部48。压力P可被维持以便在方法100的随后阶段期间充分地支撑部件10。替换地,销50可锁定到该位置,以使用适当轴锁定方法(例如液压锁或机械楔形锁)维持该形状。该方法可以在制造具有相同几何结构的批量组件时使用。支撑件30B由此提供机械灵活性和可重构性,因为促动器52的去激活允许销50滑动或运动到不促动位置,且容器40A可重新塑形以用于不同形状的部件。图9显示了图6的无固定件的支撑件30的另一实施例,其被标记为附图标记30C。支撑件30C是可重构柔性容器40B。容器40B可以是聚合物或其他耐久平滑材料的柔性衬里。容器40B的空腔42填充有形状记忆聚合物58。形状记忆聚合物58可被涂有耐久材料而形成涂层作为衬里56。在一些实施例中,形状记忆聚合物可以足够耐久以使得其不必被置于容器中。在形状记忆聚合物58处于第一永久(即已记忆)形状时,样本部件10被压靠容器40B。形状记忆聚合物58随后被激活,例如通过将聚合物58加热到激活温度以上而热激活,以使得形状记忆聚合物获得符合部件10外表面的临时形状。凹部48符合部件10的外表面的形状。临时形状显示在图9中。支撑件30C随后冷却到室温,使得形状记忆聚合物保持临时形状,直到再次被激活,例如通过再次加热到激活温度以上。支撑件30C由此提供械灵活性和重构性,因为重新激活允许容器40B重新塑形以用于不同形状的部件。图10显示了图6的无固定件的支撑件30的另一实施例,其被标记为附图标记30D。支撑件30D具有实心塑料芯部60,所述芯部基于部件10的尺寸规格用三维打印机打印。换句话说,芯部60被打印为提供符合部件10的外表面的形状的凹部48。例如被涂层塑料表面40C的衬里被施加到芯部60,以具有耐久性。支撑件30D可被快速制造,且与具有固定件的支撑件相比相对便宜。图11显示了图6的无固定件的支撑件30的额外实施例。在图11中,支撑件30的实施例被标记为附图标记30E。支撑件30E具有磁性基部70,也称为磁性卡盘,其可以包括多个磁性构件71,磁场可被选择性地应用到所述磁性构件。在磁场去除时,磁性的多部件定位元件72可被重新塑形且重新定位在基部32上,以提供用于具体成形的车辆本体部件的支撑,例如部件10A。在磁场被重新应用时,定位元件72通过磁场被保持为在基部70上固定就位。在另一实施例中,支撑件可以具有基部,相协作配置的互连支撑构件可安装到基部。支撑构件可具有各种形状和大小,且可以以各种构造卡扣安装到基部且安装到彼此,以提供与车辆本体部件10形状互补的期望构造,以通过基于视觉的机器人系统24以适度的精确性将部件10支撑就位,以用于部件10的随后定位。应理解,与非视觉系统所需的相比,支撑件30A、30B、30C、30D、30E的任何实施例在被支撑部件10的几何置放方面可提供提供较小程度的精确性,因为视觉系统16可使机器人系统24定位部件10,用于与第二车辆部件12进行组装。另外,如果支撑件30A、30B、30C、30D、30E用于仅在过程接头的形成期间支撑部件10,则与随后的结构接头形成期间相比,需要较少的精确性。可适于使用的可重构支撑件的其他实施例包括下面公开的,其每一个通过参考以其全部内容并入:Lin的美国专利No.7,210,212;Lin等人的美国专利No.7,201,059;Shen等人的7,055,679;Kramarczyk等人的美国专利No.7,000,966;Lin等人的美国专利No.6,877,729;Kramarczyk等人的美国专利No.6,712,348;和Shen等人的美国专利No.6,644,637。应理解,支撑件30A、30B、30C、30D、30E的任何实施例还可应用于使机器人手臂22上的可重构末端执行器26能够支撑第二部件12A、12B、或12C,以用于相对于第一部件10定位。例如,填充有颗粒44且可经由真空V而符合构型(conformable)的柔性容器40可以被调整尺寸,以用于连接到机器人末端执行器,用于在通过机器人手臂22定位期间抓持第二部件12A。再次参见图3和4,一旦第一部件10定位在支撑件30上,则继续图框120,使用视觉系统16以确定第一部件10在支撑件上的位置和第二车辆本体部件(一个或多个)12A、12B、12C的位置(一个或多个)。方法100设计为使得第二车辆本体部件12A、12B、12C是尺寸比第一部件10更小的部件。第二车辆本体部件可以足够小以用于在无固定件的箱90中组装,如图4和12所示。图4显示了完整的箱90,其在传送带14上运动到相同或不同的机器人23。在图6中更详细示出的视觉系统16辅助机器人23将第二部件12A、12B或12C定位在相应的箱90中,且让其运动到保持在支撑件30中的第一部件10附近。控制器C处理从视觉系统16接收的位置信息且控制机器人手臂22,以每次一个地将第二部件12A、12B、或12C相对于第一部件10定位。方法100随后前进到图框130,其中过程接头设置为维持第二部件12A、12B、或12C相对于第一部件10的期望位置。换句话说,过程接头是这样的机构:在建立一个或多个最终结构接头之前,通过该机构将部件10和12A、12B和/或12C相对于彼此保持。支撑件30和过程接头由此在建立结构接头之前用作第一部件10和第二部件12A、12B、或12C的地理位置设定特征(geographysettingfeature)。可以在方法100的范围内提供过程接头的许多不同实施例。图13显示了第一部件10具有第一特征部302,且第二部件12A具有与第一特征部302互补的第二特征部304、306,使得第一特征部302和第二特征部304、306压配合到彼此,以建立过程接头J1,如图14所示。第一特征部302被显示为相对于第二特征部304、306从插入位置转动90度,在插入位置中轴线307和309平行,如图14所示。过程接头J1配置为具有预定的强度,其足以维持通过视觉系统16确定的第二车辆部件12A相对于第一车辆部件10的位置。具体说,第一特征部302是突出部且可以如此称谓,且第二特征部为邻近凹部304被冲压到第二部件12A中的多个柔性保持构件306,且可以如此称谓。多个保持构件306配置为柔性柄脚(tang)或凸片,随机器人手臂22将第二部件12A运动到相对于第一部件10的确定的位置而将突出部302插入到凹部304中时,所述柄脚或凸片弹性地变形,建立卡扣的过程接头J1。接头J1可以配置为按照需要将第二车辆部件12A维持为距第一部件10预定的相隔距离,用于随后的激光焊接操作,例如在激光焊接被用于建立结构接头时,如进一步在本文描述。接头J1消除了在随后的激光焊接或电阻点焊操作期间对将部件10、12A彼此保持的夹持件的需要。部件12B、12C可配置为具有相似的特征部304、306,以接收第一部件10的额外突出部302。替换地,第一部件10可配置为具有特征部304、306,且部件12A、12B、12C可配置为具有特征部302。具有保持构件306的凹部304允许在突出部302相对于凹部304的中心定位方面存在一些差异或游隙。换句话说,突出部302具有比凹部304的最大宽度W略小的直径。在需要将几个突出部302定位在部件10上的不同位置以将几个凹部34与部件12A上的保持构件36对准时,用于以一些游隙将相应每一对突出部302和凹部304对准的能力使得部件10、12A在特征部302、304、306的尺寸公差范围内装配到彼此。例如,如果突出部302的中心轴线307略微与凹部304的中心轴线309偏开,则周向地围绕轴线309的保持构件306的弹性变形将倾向于使得部件10、12A彼此自对准。所有成对的第一车辆本体构件10的突出部302和第二车辆本体构件12A的保持特征部306之间的平均弹性变形使得第一车辆本体构件10相对于第二车辆本体构件12A对准。图15显示了通过置于第一部件10和第二部件12A之间的粘接剂308建立的过程接头J2的另一实施例。粘接剂308可以在相对定位之前预先施加到部件10、12A中之任一。粘接剂可以是快干结构粘接剂,具有的预定强度足以将第二部件12A维持在期望预定位置,直到例如通过激光焊接或电阻点焊设置随后的结构接头。粘接剂308可以配置为在干燥时具有厚度T1,在干燥时,其足以将第二车辆部件12A维持随后激光焊接操作所需的预定相隔距离T1,例如在激光焊接被用于建立本文进一步描述的结构接头时。另外,通过在机器人手臂22上的末端执行器26处集成力传感器31,可控制第二部件12A在第一部件10上施加的力,如图6所示。力传感器31操作性地连接到控制器C,且被控制为确保通过末端执行器26施加的用于形成过程接头的力保持在预定临界值以下。例如,在使用粘接剂308时,力传感器31可以被控制为确保适当的施加力作用在粘接剂308上,而不使得部件10、12A变形。在所有实施例中,如果形成过程接头期间部件10、12A之间存在操作性接触,直接接触或通过粘接剂或以其他方式的间接接触,则控制器C可控制机器人手臂22,以允许在垂直于力的平面中运动(例如如果力沿Z方向则是在X-Y平面中),由此在建立过程接头时允许优先针对位置信息采取力的控制。以这种方式,部件10、12A的定位和保持被整合在机器人手臂运动和力的混合控制中。图16显示了过程接头J3的另一实施例,其中具有粘合剂涂层312的颗粒310置于第一部件10和第二部件12A之间。涂有粘合剂的颗粒310的层可以在相对定位之前预先施加到部件10、12A中之任一,且可以配置为在第二部件12A运动抵靠第一部件10时快速设定(set)。可以经由图6的力传感器31使用力控制。涂有粘合剂的颗粒310可以在设定时具有预定强度,以足以将第二部件12A维持在期望的预定位置,直到设置随后的结构接头,例如通过激光焊接或电阻点焊。涂有粘合剂的颗粒310的层可以配置为在固化时具有厚度T1,其足以将第二车辆部件12A维持处于随后的激光焊接操作所需的预定相隔距离T1处,例如在激光焊接用于建立本文进一步描述的结构接头时。作为部件10、12A的结构特征的替换,或对例如粘接剂或涂有粘合剂的颗粒的替换,一个或多个机器人可被协作地控制,以将第二车辆部件12A保持在相对于第一车辆部件10的期望位置,由此建立过程接头。在图17中,第一机器人23具有第一机器人手臂22,所述第一机器人手臂具有保持部件12A的末端执行器26,且还具有实现混合力和位置控制的力传感器31。第二机器人23A具有保持第一部件10的第二机器人手臂22A。第二手臂22A的末端执行器26A可以是一个或多个夹持件。机器人23、23A由此提供类似于传统夹持件的功能,所述传统夹持件用于保持部件10、12A的相对位置。如果要应用激光焊接,则相对位置可以包括预定的相隔距离T1。替换地,并非机器人的可调整支撑件可用于支撑部件10。具有第三机器人手臂22B的第三机器人23B可用于提供一个或多个焊接部,以将部件彼此保持。第三机器人23B显示为实现远程激光焊接,激光焊接头35和3D摄像头18包括在末端执行器26B中。另外,可动镜子系统37可包括在末端执行器26B中且被控制器C控制,以按期望偏转激光束B。控制器C由此经由镜子系统37远程地让激光束B转向。镜子系统37具有促动器39,所述促动器让镜子41相对于光束B运动。在所示位置,镜子41与光束B偏开且不使得光束B转向。通过让镜子系统37运动,快速焊接可在部件10和部件12A之间的不同界面位置处实现。机器人手臂22B可随后运动到相对于部件10、12A的新的位置,且镜子系统37被控制为提供部件10、12A的另一系列远程激光焊接部。替换地,机器人手臂22、22A可使得部件10、12A置于彼此接触,且第三机器人23B可被配置为提供电阻焊接。可通过以机器人方式定位“传统的”激光焊接头实现焊接,所述焊接头不同于远程激光焊接头。传统的激光焊接头将具有“固定”光学结构,其仅相对于机器人末端执行器朝向单个方向指向。“传统的”激光焊接器也通常具有能提供距焊接点相对短的相隔距离(例如100mm)的光学结构。也可以通过机器人方式定位的“远程”激光焊接头实现焊接,其中激光束和光学结构在焊接头内部。光学结构具有相对长的焦距,其还包括可控制的镜子,允许激光束快速重新朝向距远程激光焊接头约1米距离的不同位置。可从静止机器人位置焊接许多位置。随后机器人可按照需要将远程激光焊接头重新定位到新的位置,以在位于视野外的位置中进行焊接。进一步地,可通过一个或多个静止(固定)远程激光焊接器实现焊接,所述焊接器安装在固定件上(而不是在机器人上)。每一个远程激光焊接头具有激光束和光学结构,所述光学结构具有相对长的焦距,其还包括可控制的镜子,允许激光束快速重新朝向距远程激光焊接头约1米或更远距离的不同位置。因为远程激光焊接头具有有限的覆盖窗(windowofcoverage)(由于镜子角度的限制)(例如1sq.m窗),故按照需要使用额外焊接头,以确保焊接部在零件表面上的完全覆盖。参考图3和4,在于图框130中建立过程接头之后,部件10、12A、12B、12C被认为相对于彼此按几何方式定位,且方法100前进到图框140。组件10可从支撑件30去除且被置于例如输送器14这样的可动支撑件上。在图框140执行组件的最终结构连接,例如通过用激光或电阻点焊接焊接。图4显示了可以通过用位于扫描工作站202的三维视觉系统126进行扫描来检查具有过程接头的组件。视觉系统126基本上可以类似于视觉系统16,且或可以用在组装系统200中。如果经由过程接头的定位充分,则组件可被另一机器人23从输送器14移动到远程激光焊接工作站204,在该处激光焊接可通过远程激光焊接器执行,该远程激光焊接器具有末端执行器26B,其具有视觉系统和镜子系统,如图17所示和所述的。在部件10已经运动离开输送器14的情况下,轮廓11显示了输送器14上部件10的之前位置。在焊接之后,机器人23将组件返回到输送器14。在粘接剂工作站206,粘接剂可被施加到另一车辆本体部件,例如行李箱盖外板15,且机器人23将外板运动到内板10和结构部件12A、12B、12C的组件上的位置。机器人23、视觉系统和柔性末端执行器可被控制器C协作地控制,以实现粘接剂的快速施加。可随后在扫描工作站208通过用类似于在扫描工作站202使用的三维视觉系统的三维视觉系统126进行扫描而检查被粘接的部件10、15是否符合预定的定位规范。如果经由粘接剂的定位充分,则组件可被另一机器人23从输送器14运动到一个或多个额外处理工作站,例如用于让附接部件10、15卷边的卷边压机210。参见图18-31,本发明的一些方面被显示,其中第一部件10包括第一紧固特征部454A,454B、或454D(在本文通常被称为454),且第二部件12A、12B、或12C(在本文通常被称为12)包括第二紧固特征部456A、456B、或456D(在本文通常称为456)。第一和第二紧固特征部454、456彼此接合,以将第一和第二部件10、12A、12B、12C固定或附接在一起。在一些实施例中,第一紧固特征部454进一步限定为多个第一紧固特征部454,且第二紧固特征部456进一步限定为多个第二紧固特征部456。在利用多个紧固特征部454、456时,第二紧固特征部456中的至少一个接合第一紧固特征部454中的至少一个。因此,在一些实施例中,多个第二紧固特征部456可接合第一紧固特征部454中的一个,且反过来也可以。替换地,第二紧固特征部456中的一个可接合第一紧固特征部454中的一个,且第二紧固特征部456中的另一个可接合第一紧固特征部454中的另一个,等。第一和第二紧固特征部454、456可以以任何合适的方式彼此接合,例如摩擦或干涉配合、压配合、卡扣配合、弹性配合等。第一和第二紧固特征部454、456可与相应的第一和第二部件10、12A、12B、12C整合,即形成一个部件或单元,或可通过任何合适的方法附接到相应第一和第二部件10、12A、12B、12C,即通过焊接、粘接剂、紧固件等。在附接第一和第二紧固特征部454、456时,这可在形成了第一和第二部件10、12A、12B、12C之后的任何时候发生,例如正好在将第一和第二部件10、12A、12B、12C固定在一起之前。第一和第二紧固特征部454、456提供第二部件12A、12B、12C相对于第一部件10的最小保持力。第一和第二紧固特征部454、456消除了专用固定件(其用于呈现、定位或保持部件10、12A、12B、12C)的使用。视觉系统16可用于将第一紧固特征部454和第二紧固特征部456相对于彼此对准。在利用多个紧固特征部时,视觉系统16可用于将第一紧固特征部454和第二紧固特征部456相对于彼此对准。因此,视觉系统16(例如摄像头18)可用于找出一位置,该位置处第一和第二紧固特征部454、456或坐标定位器可被利用以将第一紧固特征部(一个或多个)454和第二紧固特征部(一个或多个)456对准到具体位置以彼此接合。第一紧固特征部(一个或多个)454和第二紧固特征部(一个或多个)456可具有许多不同构造,这些构造中的一些在下文描述。一旦部件10、12A、12B、12C相对于彼此定位,则过程接头482被形成或建立,以将部件10、12A、12B、12C保持在相对位置(在期望时包括材料之间的相隔距离),直到结构接头496(见图30)或结构焊接部在随后的操作中形成。结构接头496提供部件10、12A、12B、12C之间的永久附接。夹持件被一个或多个过程接头482代替。换句话说,第一和第二紧固特征部454、456形成过程接头482,而不需要使用夹持件来在随后的激光焊接或电阻点焊操作期间将部件10、12A、12B、12C彼此保持住。过程接头482具有如上所述的预定强度,其可被称为第一预定强度。在结构接头496形成时,结构接头496具有大于第一预定强度的第二预定强度。因此,结构接头496提供部件10、12A、12B、12C之间更永久的附接。通常,第一和第二紧固特征部454、456,且具体说是过程接头482,提供足以将第二部件12A、12B、12C保持或维持在期望预定位置的预定强度,直到例如通过激光焊接、电阻点焊等提供随后的结构接头496。结构接头496可以是激光焊接的、电阻点焊的、其他熔接结合或焊接的(例如金属惰性气体(MIG)焊接)、固态结合的(例如超声波焊接或摩擦搅拌焊接)、机械连结的(例如铆钉、自攻螺钉或机械铆紧)、结构粘接的或上述方法的混合(一个或多个上述方法的组合),其配置为在组件安装在车辆、器具等上时在组件的可用寿命中将第一和第二部件10、12A、12B、12C保持到彼此。在一些实施例中,过程接头482和视觉系统16可实现快速的单面或双面再点焊(re-spotweld),例如但不限于远程激光焊接或电阻点焊。再点焊在过程接头482之后执行,且再点焊可在不使用夹持件的支撑件30上或固定件上执行,这可降低复杂性和成本,以及改善对焊接可用性。结构接头496或焊接部可位于相对于过程接头482的任何合适位置。在一些情况下,结构接头496可形成为远离过程接头482,即彼此间隔开。在其他情况下,结构接头496可形成为靠近或接近过程接头482。在其他情况下,结构接头496可形成在过程接头482上。转到不同的紧固特征部454、456,图18-20示出了一个实施例。在该实施例中,第一和第二紧固特征部454A、456A中的一个包括凸片461,而第一和第二紧固特征部454A、456A中的另一个限定洞462。凸片461设置在洞462中,以形成过程接头482。例如,第一紧固特征部454A可限定洞462且第二紧固特征部456A可以是凸片461。第一部件10可包括围绕洞462的内壁463,同时凸片461接合内壁463以将第一和第二部件10、12固定在一起。凸片461可偏置以对第一部件10,例如内壁463,施加力,以维持第二部件12相对于第一部件10的相对位置。通常,凸片461卡扣配合到第一部件10。应理解,凸片461可被冲压和弯曲成期望的取向。凸片461可在第一或第二部件10、12形成期间或之后被冲压。转到图23-26的实施例,第一和第二紧固特征部454B、456B中的一个包括突出部464,而第一和第二紧固特征部454B、456B中的另一个限定开口465。突出部464设置在开口465中以形成过程接头482。例如,第一紧固特征部454B可以是突出部464且第二紧固特征部456B可以被限定为开口465。具体说,在该实施例中,第二紧固特征部456B可包括限定了开口465的保持构件466。保持构件466可以是柔性的,从而在彼此接合时突出部64使得保持构件466变形。具体说,保持构件466弹性地可变形,从而在突出部464与保持构件466脱离时保持构件466返回到其原始构造。保持构件466可形成到第二部件12中或可以是附接到第二部件12的插入件。保持构件466可具有与第二部件12不同的厚度或相同的厚度。图24和25显示了具有与第二部件12不同厚度的保持构件466。开口465可以具有任何合适构造,且图23和26示出了开口465,其具有从开口465中心径向地延伸离开的多个凹部467,使得保持构件466呈现有多个指状物468,指状物468是柔性的。凹部467提供指状物468之间的额外柔性,使得指状物468可偏压和变形。因此,通常,突出部464卡扣配合或压配合到保持构件466。通过保持构件466限定的凹部467允许突出部464相对于开口465中心定位时的一些差异或游隙。换句话说,突出部464具有比中心开口465的最大宽度略小的直径。在几个突出部464定位在第一部件10上的不同位置时,这些突出部464必须对准保持构件466的几个不同的中心开口465。通过允许存在一些游隙而实现使得相应每一对突出部464和开口465对准的能力,所述游隙使得部件10、12能在特征部454B、456B的尺寸公差范围内彼此装配。例如,如果突出部464中的一个从相应开口465略微偏开,则保持构件466的指状物468可弹性地变形以使得部件10、12彼此自对准。所有成对的突出部464和保持构件466之间的平均弹性变形使得第一部件10相对于第二部件12对准。因此,在图23-26的实施例中,第一和第二紧固特征部454B、456B可设计为提供弹性平均以使得第二部件12相对于第一部件10自对准。突出部464可与第一部件10整体地形成或附接至第一部件。例如,突出部464可焊接或冲压到第一部件10。突出部464可从第一部件10向外延伸到远端469。可选地,远端469可以是锥形的,以有助于插入和/或将突出部464与开口465对准。参见图21和22的实施例,第一紧固特征部454C包括第一凸片471且第二紧固特征部456C包括第二凸片473。第一和第二凸片471、473彼此接合以形成过程接头482。第一和第二凸片471、473可偏置以彼此抵靠施加力,以维持第二部件12相对于第一部件10的相对位置。通常,第一和第二凸片471、473彼此卡扣配合。应理解,第一和第二凸片471、473可被冲压和弯曲到期望的取向。转到图27和28的实施例,第一和第二紧固特征部454D、456D中的一个包括第一突出部474,而第一和第二紧固特征部454D、456D中的另一个包括限定中空部分476的第二突出部475。第一突出部474设置在第二突出部475的中空部分476中以形成过程接头482。因此,第二突出部475大于第一突出部474从而第一突出部474可装配到中空部分476中。例如,第一紧固特征部454D可包括第一突出部474,且第二紧固特征部456D可包括限定中空部分476的第二突出部475。第一突出部474插入到第二突出部475的中空部分476直到第一和第二突出部474、475彼此接合。具体说,第一和第二突出部474、475在它们之间形成摩擦配合或压配合。第一突出部474可选地限定中空部分。应理解,第一和第二突出部474、475的中空部分476可完全地或整个地穿过第一和第二部件10、12。在一些实施例中,参见图19、22、25和28,过程接头482可建立第一部件10和第二部件12之间的相隔距离498(即间隙)。在一些实施例中,第一和第二紧固特征部454、456可建立相隔距离498。例如,在一些实施例中,第一紧固特征部454和第二紧固特征部456彼此接合以建立第一部件10和第二部件12之间的相隔距离498。相隔距离498可有助于随后的焊接过程。相隔距离498与随后的结构焊接部的置放相关联,所述结构焊接部将第一和第二部件10、12固定在一起。例如,如果激光焊接用于结构接头496,则可期望在部件10、12之间具有相隔距离498。例如,当在焊接部区域中材料具有约0.1毫米(mm)到约0.2mm的相隔距离498时,镀锌钢板的激光焊接可具有改进的质量,具有减小的多孔性。通过允许焊接气体在固化之前从焊接区域逃逸,该相隔距离498可改善焊接质量。在一些情况下,相隔距离498应该被最小化。例如铝到铝的激光焊接应该在在焊接部区域中相隔距离498被最小化(e.g.,小于约0.125mm)的情况下进行。对于图18-20的实施例,相隔距离498可通过延伸部477建立。第一和第二紧固特征部454A、456A中邻近洞462的那个和凸片461中的至少一个包括延伸部477,以限制插入到洞462的距离,以建立相隔距离498。在一个实施例中,第一部件10的第一紧固特征部454A包括在图18和19中以实线示出的延伸部477。例如,延伸部477可设置为邻近洞462,如此,延伸部477可从邻近洞462的第一部件10延伸。在另一实施例中,凸片461包括以477A示出的延伸部,如图18的虚线所示。在其他实施例中,凸片461和第一部件10两者可包括延伸部477或477A。应理解,一个或多个延伸部477或477A可在任何合适位置被使用和设置。通过改变延伸部477或477A的厚度,相隔距离498因此改变。本文使用的短语“至少一个”应该理解为包括非排他的逻辑“或”,即第一和第二紧固特征部454A、456A中的一个或凸片461中的至少一个。因此,在一些实施例中,凸片461包括延伸部477或477A,或第一和第二紧固特征部454A、456A中的一个包括延伸部477。在其他实施例中,凸片461和第一和第二紧固特征部454A、456A中的一个包括延伸部477或477A。与短语“至少一个”有关的相同原则适用于整个说明书。对于图23-26的实施例,可通过沟槽478建立相隔距离498。具体说,突出部464可包括限定沟槽478的外周边479。保持构件466接合沟槽478以限定突出部464插入到保持构件466的开口465中的距离,以建立相隔距离498。通过改变沟槽478的位置,相隔距离498因此改变。作为利用沟槽478建立相隔距离498的额外或替换方案,可通过在图24中以虚线所示的延伸部建立相隔距离498。第一和第二部件10、12中的至少一个包括延伸部480,以限制突出部464插入到开口465的距离,以建立相隔距离498。例如,延伸部480可从第二部件12、第一部件10或第一和第二部件10、12两者延伸。在图24中,仅出于展示的目的,延伸部480从第二部件12延伸。再次,通过改变延伸部480的厚度,相隔距离498因此改变。延伸部480可处于任何合适位置,且一个合适位置可邻近保持构件466。对于图21和22的实施例,相隔距离498可通过延伸部481建立。第一和第二凸片471、473中的至少一个包括延伸部481,以限制第一和第二凸片471、473彼此接合的距离,以建立相隔距离498。因此,在一个实施例中,第一凸片471包括延伸部481。在另一实施例中,第二凸片473包括延伸部481。在另一实施例中,第一和第二凸片471、473每一个包括延伸部481。可选的延伸部481在图21中以虚线示出。转到图27和28的实施例,第一和第二突出部474、475中的至少一个是锥形的,以限制第一突出部474插入到中空部分476的距离,以建立相隔距离498。在一个实施例中,第一突出部474是锥形的。在另一实施例中,第二突出部475是锥形的。在另一实施例中,第一和第二突出部474、475两者是锥形的,如在图27和28中仅出于展示的目的所示的。进而,第一和/或第二突出部474、475可以以期望构造弯曲,以建立相隔距离498。图31示出了组装多个部件10、12A、12B、12C的方法500的流程图,且图4示出了利用了从引入部件10、12A、12B、12C到完成卷边的方法500的组装系统200的一个例子。在图31中,方法500可包括图框502,其中机器人23从不被固定的(unfixtured)初始支撑件13(例如标准平坦传送带、存储箱、提包或...