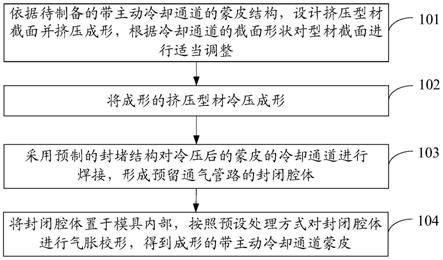
1.本发明属于精密钣金加工技术领域,尤其涉及一种带主动冷却通道蒙皮挤压冷压气胀成形方法。
背景技术:2.铝合金、镁合金因其具有优秀的综合力学性能和良好的散热性能,在航空航天,武器装备、轨道交通等领域应用十分广泛。在航空航天领域,带冷却通道的蒙皮一般需承受要复杂的受力环境、震动、高温等工况。因此,对此类零件的整体性、轻量化设计、制造精度的要求也越来越高。
3.在蒙皮成形领域,带主动冷却通道蒙皮常用的制造方法有焊接成形,铸造成形和增材制造成形。焊接成形方法通常先机加工开放式冷却沟槽,然后通过与板材进行焊接成形,这种成形方法破坏了通道的整体性,且复杂通道截面很难实现。铸造方法成形带冷却通道蒙皮,由于铸造合金本身的限制,其力学性能以及致密性等都不如变形合金,为了达到使用要求,通常会做加厚处理,这样会导致蒙皮的超重问题,通道内壁为铸造表面,难以加工,其表面质量难以保证。增材制造成形虽然能快速制造带冷却通道蒙皮,但其加工成本较高,成形后的表面粗粗糙度较大,通常需要后续加工,增材制造的零件普遍存在较大的内应力,在消除内应力的过程中容易导致零件变形。
技术实现要素:4.本发明要解决的技术问题为:现有蒙皮成形工艺加工精度低、加工成本高且所加工的零件整体性差的问题。
5.为了解决上述技术问题,本发明公开了一种带主动冷却通道蒙皮挤压冷压气胀成形方法,其中,所述方法包括:
6.依据待制备的带主动冷却通道的蒙皮结构,设计挤压型材截面并挤压成形,根据冷却通道的截面形状对型材截面进行适当调整;
7.将成形的挤压型材冷压成形;
8.采用预制的封堵结构对冷压后的蒙皮的冷却通道进行焊接,形成预留通气管路的封闭腔体;
9.将所述封闭腔体置于模具内部,按照预设处理方式对所述封闭腔体进行气胀校形,得到成形的带主动冷却通道蒙皮。
10.可选地,所述将成形的挤压型材冷压成形的步骤,包括:
11.在将所述成形的挤压型材冷压成形过程中,采用硫代硫酸钠对所述成形的挤压型材中的中空结构进行填充。
12.可选地,所述封闭腔体置于模具内部,按照预设处理方式对所述封闭腔体进行气胀校形,得到成形的带主动冷却通道蒙皮的步骤,包括:
13.将所述封闭腔体置于模具内部;
14.将所述模具置于成形机上加热至指定温度后闭合所述模具;
15.按照设定压力通过所述预留通气管路向所述封闭腔体内通气对所述封闭腔体加压校形,以使带主动冷却通道蒙皮的内外侧形成光滑曲面。
16.可选地,所述挤压型材截面通道的形状包括:圆形、圆角矩形以及多边形中的至少之一。
17.可选地,所述挤压型材截面的外形轮廓的形状包括:长方形、多边形以及圆弧形中的至少之一。
18.可选地,所述挤压型材材质包括:铝合金、镁合金中的至少之一。
19.可选地,在所述带主动冷却通道蒙皮的材质为铝合金材质的情况下,所述指定温度范围为420℃~520℃。
20.可选地,在所述带主动冷却通道蒙皮的材质为镁合金材质的情况下,所述指定温度范围为350℃~420℃。
21.可选地,所述设定压力范围为0.1mpa~3mpa。
22.与现有技术相比,本发明具有如下优点:
23.本申请实施例提供的带主动冷却通道蒙皮挤压冷压气胀成形方法,依据待制备的带主动冷却通道的蒙皮结构,设计挤压型材截面并挤压成形,根据冷却通道的截面形状对型材截面进行适当调整;将成形的挤压型材冷压成形;采用预制的封堵结构对冷压后的蒙皮的冷却通道进行焊接,形成预留通气管路的封闭腔体;将封闭腔体置于模具内部,按照预设处理方式对封闭腔体进行气胀校形,得到成形的带主动冷却通道蒙皮。第一方面,采用本发明实施例提供的方法所成形的带主动冷却通道蒙皮,整体性好,零件尺寸精度、型面精度以及表面质量高;第二方面,采用气胀校形的技术可以实现零件的近净成形,能有效减少后续加工量,避免后续手工校形,提高效率,降低成本;第三方面,本发明实施例提供的方法成本低、加工效率高,型面精度容易控制,残余应力低。
附图说明
24.图1为本发明实施例的一种带主动冷却通道蒙皮挤压冷压气胀成形方法的步骤流程图;
25.图2为带主动冷却通道蒙皮的结构示意图;
26.图3为带主动冷却通道蒙皮挤压成形后的结构示意图;
27.图4为带主动冷却通道蒙皮冷压成形后的结构示意图;
28.图5为带主动冷却通道蒙皮焊接封堵,形成封闭内腔后的结构示意图。
29.图6为带主动冷却通道蒙皮热胀形模具示意图。
具体实施方式
30.下面根据具体的实施例,结合附图针对本发明进行详细说明。应当理解,此处所述的具体实施例仅用于解释本发明,并不用于限定本发明。
31.附图1为本发明实施例提供的一种带主动冷却通道蒙皮挤压冷压气胀成形方法的步骤流程图。
32.本发明实施例提供的带主动冷却通道蒙皮挤压冷压气胀成形方法,对蒙皮进行挤
压、冷压、气胀处理后生成成形蒙皮,它适用于整体性好、尺寸精度、型面精度以及表面质量要求较高的带冷却通道蒙皮。
33.本发明实施例的带主动冷却通道蒙皮挤压冷压气胀成形方法包括以下步骤:
34.步骤101:依据待制备的带主动冷却通道的蒙皮结构,设计挤压型材截面并挤压成形,根据冷却通道的截面形状对型材截面进行适当调整。
35.其中,挤压型材截面通道的形状包括但不限于:圆形、圆角矩形以及多边形中的至少之一。
36.挤压型材截面的外形轮廓的形状包括但不限于:长方形、多边形以及圆弧形中的至少之一。
37.挤压型材材质可以包括但不限于:铝合金、镁合金中的至少之一。
38.步骤102:将成形的挤压型材冷压成形。
39.在一种可选地实施例中,在将成形的挤压型材冷压成形过程中,采用硫代硫酸钠对成形的挤压型材中的中空结构进行填充,可有效防止冷压过程中中空结构失稳。
40.上述仅是示例性地列举了采用硫代硫酸钠作为填充材料,在实际实现过程中,并不局限于这一种材料,本领域技术人员可以根据实际需求选择任意适当的材质作为填充材料,本申请实施例中对此不做具体限制。
41.步骤103:采用预制的封堵结构对冷压后的蒙皮的冷却通道进行焊接,形成预留通气管路的封闭腔体。
42.步骤104:将封闭腔体置于模具内部,按照预设处理方式对封闭腔体进行气胀校形,得到成形的带主动冷却通道蒙皮。
43.在一种可选地实施例中,封闭腔体置于模具内部,按照预设处理方式对封闭腔体进行气胀校形,得到成形的带主动冷却通道蒙皮的步骤,包括以下子步骤:
44.子步骤一:将封闭腔体置于模具内部;
45.子步骤二:将模具置于成形机上加热至指定温度后闭合模具;
46.蒙皮的材质不同其对应的指定温度不同。一种可选地实施例中,在带主动冷却通道蒙皮的材质为铝合金材质的情况下,指定温度范围设置为420℃~520℃。在带主动冷却通道蒙皮的材质为镁合金材质的情况下,指定温度范围设置为350℃~420℃。
47.子步骤三:按照设定压力通过预留通气管路向所述封闭腔体内通气对封闭腔体加压校形,以使带主动冷却通道蒙皮的内外侧形成光滑曲面。
48.其中,设定压力范围可设置为0.1mpa~3mpa。
49.在一种可选地实施例中,通过步骤104得到成形的带主动冷却通道蒙皮之后,可按照设计图纸将工艺余量去除,得到带主动冷却通道蒙皮。
50.本发明实施例提供的带主动冷却通道蒙皮成形方法,能够克服现有技术加工的零件整体性差、外形精度控制困难或成本较高的缺点,能有效地保证拓扑结构壁板精密成形。成形出的拓扑结构壁板类零件质量稳定,整体性好,减重效果明显,尺寸精度、型面精度以及表面质量较高,并且成形周期较短,加工成本较低。
51.本申请实施例提供的带主动冷却通道蒙皮挤压冷压气胀成形方法,依据待制备的带主动冷却通道的蒙皮结构,设计挤压型材截面并挤压成形;将成形的挤压型材冷压成形;采用预制的封堵结构对冷压后的蒙皮的冷却通道进行焊接,形成预留通气管路的封闭腔
体;将封闭腔体置于模具内部,按照预设处理方式对封闭腔体进行校形,得到成形的带主动冷却通道蒙皮。第一方面,采用本发明实施例提供的方法所成形的带主动冷却通道蒙皮,整体性好,零件尺寸精度、型面精度以及表面质量高;第二方面,采用气胀校形的技术可以实现零件的近净成形,能有效减少后续加工量,避免后续手工校形,提高效率,降低成本;第三方面,本发明实施例提供的方法成本低、加工效率高,型面精度容易控制,残余应力低。
52.下面以采用本发明实施例提供的方式,对铝合金带主动冷却通道蒙皮进行成形处理具体实例进行说明。铝合金带主动冷却通道蒙皮的形状尺寸见图2,零件材料为6061铝合金,外型面为圆面,长度500mm,半径260mm,弧长245mm,总厚度为10mm;中空结构为26
×
7mm的圆角矩形,圆角为r2,共9条冷却通道的蒙皮。
53.可采用如下工艺步骤制备带主动冷却通道蒙皮:
54.步骤一,根据零件外形及冷却通道尺寸,按照半径为255mm进行展开,其展开宽度为249.8mm,长度方向留切割余量,长度为540mm;
55.步骤二,根据展开尺寸设计截面形状,并进行热挤压成形,挤压成形后零件如图3所示;
56.步骤三,将挤压型材的中空结构内部填充硫代硫酸钠,然后进行冷压成形,冷压成形后零件如图4所示;
57.步骤四,用预制好的封堵结构将步骤三冷压后的蒙皮的冷却通道进行封堵焊接,形成密闭腔体,并预留通气管路,如图5所示;
58.步骤五,步骤四完成后,将模具和焊接完成后的零件在成形机上加热420~520℃,闭合模具,通过预留的通气管路,按照设定的随时间变化的压力向密闭型腔通气加压校形,压力为0.1~3mpa,使带主动冷却通道蒙皮的内外侧形成光滑曲面。其中,模具的结构示意图如图6所示。
59.采用此方法制备的铝合金拓扑结构壁板尺寸精度为
±
0.3mm,型面精度
±
0.5mm,表面粗糙度ra3.2以下,比现有方法制造成本降低10%以上,加工效率提高20%以上。
60.需要说明的是,以上说明仅是本发明的优选实施方式,应当理解,对于本领域技术人员来说,在不脱离本发明技术构思的前提下还可以做出若干改变和改进,这些都包括在本发明的保护范围内。
61.本发明说明书中未作详细描述的内容属于本领域技术人员的公知技术。