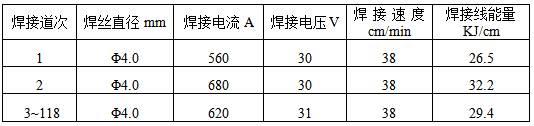
1.本发明属于冶金技术领域,涉及一种超大厚度加氢反应器用钢板焊接工艺。
背景技术:2.12cr2mo1vr钢因高温性能、抗氢腐蚀及抗堆焊剥离等性能均优于传统cr-mo钢,已成为制造大型加氢反应器的首选材料,但该类钢中含有的大量cr、mo、v等碳化物形成元素,常常导致焊接接头出现脆硬区,从而增大焊接冷裂纹和再热裂纹的风险,也降低了结构疲劳强度和抗应力腐蚀开裂性。随着加氢反应器尺寸和功率的不断增大,容器壁板厚也在不断增加,最大厚度已经达到150~200mm。这种超大厚度12cr2mo1vr钢板在焊接过程中焊缝拘束度高,焊接残余应力大,焊后应力和变形大,极易出现焊接缺陷。
3.已有专利或研究报告大多是针对150mm以下 12cr2mo1vr钢板的焊接工艺;150mm以上特厚板的相关焊接工艺尚未见报道。如何采用合理的焊接工艺,既避免焊接裂纹的产生,又可确保最终焊接接头的强度和韧性满足标准要求,是12cr2mo1vr钢超大厚度钢板焊接的一大技术难题。
技术实现要素:4.本发明的目的是针对上述已有技术存在的问题,提供一种150~200mm超大厚度加氢反应器用钢板的焊接工艺,解决超大厚度加氢反应器用12cr2mo1vr钢板焊接过程中出现的焊缝拘束度高、焊接残余应力大,焊后应力和变形大,更易出现焊接缺陷等技术问题。
5.本发明的技术方案:一种超大厚度加氢反应器用钢板的焊接工艺,包括以下步骤:s1,制作坡口:使钢板对接时形成上下对称的双u型坡口,上下坡口之间作留钝处理;s2,预热:对待焊接部位进行预热,控制预热温度在180℃以上;s3,打底焊接:坡口预热达标后,使用埋弧自动焊对留钝部位焊接道次(1)实施打底焊接,其焊材采用pf-500/us-521h型耐热钢埋弧焊丝与焊剂;s4,填充焊:坡口预热达标后,采用多层多道焊接方式使用埋弧自动焊对上、下部坡口按照焊接道次顺序进行填充焊,其焊材采用pf-500/us-521h型耐热钢埋弧焊丝与焊剂,控制层间温度在180~250℃;s5,热处理:填充焊完成后,立即对焊接接头进行消氢处理和焊后热处理;消氢处理完成前控制温度不低于层间温度;分别在消氢处理后和焊后热处理完成24h后进行无损检测。
6.作为优选实施例,步骤s1中,所述u型坡口,由底边为r=8mm的圆弧,斜边是与开口方向呈10
°
倾角的直线构成。
7.作为优选实施例,步骤s1中,所述留钝处理为设置一个间隙,所述间隙的竖向高度为8~10mm,间隙宽度为1~2mm。
8.作为优选实施例,步骤s3中,所述的打底焊接采用较小的焊接线能量,控制在22~27kj/cm。
9.作为优选实施例,步骤s4中,所述的填充焊的焊接线能量控制在29~33kj/cm;作为优选实施例,步骤s5中,所述的消氢处理工艺条件是:保温温度300~350℃,保温时间2h。
10.作为优选实施例,步骤s5中,所述的焊后热处理分为最小焊后热处理、最大焊后热处理两种热处理制度,均需进行。最小焊后热处理工艺条件是;当温度≥400℃时,升温/降温速度:≤55℃/h;保温温度705℃;保温时间8h;最大焊后热处理工艺保温时间为32h,其余条件与最小焊后热处理工艺相同。
11.作为优选实施例,步骤s5中,在消氢处理后和焊后热处理完成24h后,需要使用超声波(ut)方法进行无损检测,确保所有焊缝不出现焊接裂纹。
12.本发明的有益效果:通过采用优化的u形坡口设计达到焊缝金属量最少,焊件产生的变形小,焊缝金属中母材金属所占比例也小的效果;采用埋弧焊焊接方法,严格控制预热温度和层间温度,配以合理的消氢处理和焊后热处理,保证焊接接头具有低的回火脆化敏感性,获得良好的拉伸性能、弯曲性能和低温冲击韧性,同时又可以避免焊接裂纹的产生,实现了150~200mm加氢反应器用12cr2mo1vr超厚板的高质量焊接。
附图说明
13.图1为150mm超厚板实施例坡口示意图。
14.图2 为150mm超厚板实施例焊接道次顺序示意图。
15.图3 为180mm超厚板实施例坡口示意图。
16.图4 为180mm超厚板实施例焊接道次顺序示意图。
17.图5 为200mm超厚板实施例坡口示意图。
18.图6 为200mm超厚板实施例焊接道次顺序示意图。
具体实施方式
19.下面用实施例进一步说明。
20.实施例1:一种超大厚度加氢反应器用钢板的焊接工艺,所用12cr2mo1vr母材钢板厚度为150mm,包括如下步骤:s1,制作坡口,切割超厚板待焊接部位使钢板对接时形成上下对称的“双u”型坡口,上下坡口之间作留钝处理;s2,对待焊接部位进行预热,控制预热温度在180℃以上;s3,打底焊接,坡口预热达标后,使用埋弧焊对留钝部位焊接道次1实施打底焊接;s4,填充焊,坡口预热达标后,采用多层多道焊接方式,使用埋弧自动焊对上、下部坡口按照焊接道次顺序进行填充焊2~118焊道,控制层间温度在180~250℃;s5,热处理,对焊后钢板依次进行消氢处理和焊后热处理。消氢处理完成前控制温度不低于层间温度;在消氢处理后和焊后热处理完成24h后进行无损检测。
21.作为本发明的一个实施例,步骤s1中,所述u型坡口如图1所示,由底边为r=8mm的
圆弧,斜边是与开口方向呈10
°
倾角的直线构成;该坡口便于加工及清渣,能够减小坡口、减小侧壁未熔合几率。
22.步骤s1中,所述留钝处理为设置一个间隙,竖向高度为8~10mm,间隙宽度为1~2mm。间隙的竖向高度能够防止根部烧穿,具体地,竖向高度过大不宜焊透,竖向高度太小,打底焊容易烧穿。间隙宽度的作用是保证打底焊时根部焊透,避免形成虚焊。
23.步骤s2中,所述的预热温度≥180℃;预热能够避免冷裂纹和再热裂纹的出现,预热温度过高可能会导致局部焊缝金属晶粒粗大。
24.实施例1的焊接道次顺序示意图如图2所示,焊接工艺焊接参数见表1。
25.表1150mm超厚板实施例焊接工艺焊接参数。
26.首先,坡口预热达标后,对留钝处理位置的焊接道次1进行打底焊接。打底焊接采用较小的焊接线能量,控制在22~27kj/cm,防止焊穿;然后调整焊接参数,线能量控制在29~33kj/cm,按照焊接道次顺序2~118进行填充焊接;控制层间温度180~250℃;焊接时采用pf-500/us-521h型耐热钢埋弧焊丝与焊剂,可得到具有优异的抗裂纹性能和低温冲击韧性,回火脆化敏感性低的焊缝金属。金属焊丝的化学成分及机械性能与母材匹配,既能保证焊缝金属的化学成分与母材匹配,还能保证焊接接头的机械性能尤其是抗拉强度、屈服强度及伸长率与母材匹配。
27.焊接完成后立即进行消氢处理,以便溢出扩散氢,降低接头中的扩散氢含量,避免氢聚集导致延迟裂纹。消氢处理工艺条件是:保温温度300~350℃,保温时间2h。
28.超厚板焊接接头消氢处理后,使用超声波方法进行无损检测,确保所有焊缝不出现焊接裂纹。具体地,根据nb/t47013.3-2015,使用超声波方法进行无损检测,所有焊缝没有出现焊接裂纹,为ti级合格。
29.检测无裂纹后,对超厚板焊接接头分别进行最小、最大焊后热处理,最小焊后热处理工艺条件是;当温度≥400℃时,升温/降温速度:≤55℃/h;保温温度705℃;保温时间8h;最大焊后热处理工艺保温时间为32h,其余条件与最小焊后热处理工艺相同。利用焊后热处理改善焊接接头的组织性能,使焊接接头的强度、硬度和韧性恢复到与母材金属相当的水平。
30.待焊后热处理完成24h后,还需使用超声波方法进行无损检测,确保所有焊缝不出现焊接裂纹。具体地,根据nb/t47013.3-2015,使用超声波方法进行无损检测,所有焊缝没有出现焊接裂纹,为ti级合格;焊后性能检测:最大焊后热处理后,全厚度强度:25℃室温拉伸rel≥485mpa,rm≥610mpa;500℃高温拉伸rel=361mpa,rm=452mpa。-30℃冲击吸收能量:焊缝≥124j;热影响区≥161j。全厚度焊接接头的拉伸性能、弯曲性能和冲击性能良好,均满足规范要求。
31.实施例2:
一种超大厚度加氢反应器用钢板的焊接工艺,所用12cr2mo1vr母材钢板厚度为180mm,包括如下步骤:s1,制作坡口,切割超厚板待焊接部位使钢板对接时形成上下对称的“双u”型坡口,上下坡口之间作留钝处理;s2,对待焊接部位进行预热,控制预热温度在180℃以上;s3,打底焊接,坡口预热达标后,使用埋弧自动焊对留钝部焊接道次1实施打底焊接;s4,填充焊,坡口预热达标后,采用多层多道焊接方式,使用埋弧自动焊对上、下部坡口按照焊接道次顺序进行填充焊2~118焊道,控制层间温度在180~250℃;s5,热处理,对焊后钢板依次进行消氢处理和焊后热处理。消氢处理完成前控制温度不低于层间温度;在消氢处理后和焊后热处理完成24h后进行无损检测;作为本发明的一个实施例,步骤s1中,所述u型坡口如图3所示,由底边为r=8mm的圆弧,斜边是与开口方向呈10
°
倾角的直线构成;该坡口便于加工及清渣,能够减小坡口、减小侧壁未熔合几率。
32.步骤s1中,所述留钝处理为设置一个间隙,竖向高度为8~10mm,间隙宽度为1~2mm。间隙的竖向高度能够防止根部烧穿,具体地,竖向高度过大不宜焊透,竖向高度太小,打底焊容易烧穿。间隙宽度的作用是保证打底焊时根部焊透,避免形成虚焊。
33.步骤s2中,所述的预热温度≥180℃;预热能够避免冷裂纹和再热裂纹的出现,预热温度过高可能会导致局部焊缝金属晶粒粗大。
34.实施例2的焊接道次顺序示意图如图3所示,焊接工艺焊接参数见表2。
35.表2180mm超厚板实施例焊接工艺焊接参数。
36.首先,坡口预热达标后,对留钝处理位置的焊接道次1进行打底焊接。打底焊接采用较小的焊接线能量,控制在22~27kj/cm,防止焊穿;控制层间温度300~350℃;然后调整焊接线能量,控制在29~33kj/cm,按照焊接道次顺序进行填充焊接;控制层间温度180~250℃。
37.焊接时采用pf-500/us-521h型耐热钢埋弧焊丝与焊剂,可得到具有优异的抗裂纹性能和低温冲击韧性,回火脆化敏感性低的焊缝金属。金属焊丝的化学成分及机械性能与母材匹配,既能保证焊缝金属的化学成分与母材匹配,还能保证焊接接头的机械性能尤其是抗拉强度、屈服强度及伸长率与母材匹配。
38.焊接完成后立即进行消氢处理,以便溢出扩散氢,降低接头中的扩散氢含量,避免氢聚集导致延迟裂纹。消氢处理工艺条件是:保温温度300~350℃,保温时间2h。
39.超厚板焊接接头消氢处理后,使用超声波方法进行无损检测,确保所有焊缝不出现焊接裂纹。具体地,根据nb/t47013.3-2015,使用超声波方法进行无损检测,所有焊缝没有出现焊接裂纹,为ti级合格。
40.检测无裂纹后,对超厚板焊接接头分别进行最小、最大焊后热处理,最小焊后热处
理工艺条件是;当温度≥400℃时,升温/降温速度:≤55℃/h;保温温度:705℃;保温时间:8h;最大焊后热处理工艺保温时间为32h,其余条件与最小焊后热处理工艺相同。利用焊后热处理改善焊接接头的组织性能,使焊接接头的强度、硬度和韧性恢复到与母材金属相当的水平。
41.待焊后热处理完成24h后,还需使用超声波方法进行无损检测,确保所有焊缝不出现焊接裂纹。具体的,根据nb/t47013.3-2015,使用超声波方法进行无损检测,所有焊缝没有出现焊接裂纹,为i级合格;焊后性能检测结果:最大焊后热处理后,全厚度强度:25℃室温拉伸rel≥551mpa,rm≥673mpa;550℃高温拉伸rel=400mpa,rm=430mpa。-30℃冲击吸收能量:焊缝≥49j;热影响区≥204j。全厚度焊接接头的拉伸性能、弯曲性能和冲击性能良好,均满足规范要求。
42.实施例3:本实施例中一种超大厚度加氢反应器用钢板的焊接工艺所用12cr2mo1vr母材钢板厚度为200mm,包括如下步骤:s1,制作坡口,切割超厚板待焊接部位使钢板对接时形成上下对称的“双u”型坡口,上下坡口之间作留钝处理;s2,对待焊接部位进行预热,控制预热温度在180℃以上;s3,打底焊接,坡口预热达标后,使用埋弧自动焊对留钝部焊接道次1实施打底焊接;s4,填充焊,坡口预热达标后,采用多层多道焊接方式,使用埋弧自动焊对上、下部坡口按照焊接道次顺序进行填充焊2~127焊道,控制层间温度在180~250℃;s5,热处理,对焊后钢板依次进行消氢处理和焊后热处理。消氢处理完成前控制温度不低于层间温度;在消氢处理后和焊后热处理完成24h后进行无损检测。
43.步骤s1中,所述u型坡口如图3所示,由底边为r=8mm的圆弧,斜边是与开口方向呈10
°
倾角的直线构成;该坡口便于加工及清渣,能够减小坡口、减小侧壁未熔合几率。
44.步骤s1中,所述留钝处理为设置一个间隙,竖向高度为8~10mm,间隙宽度为1~2mm。间隙的竖向高度能够防止根部烧穿,具体地,竖向高度过大不宜焊透,竖向高度太小,打底焊容易烧穿。间隙宽度的作用是保证打底焊时根部焊透,避免形成虚焊。
45.步骤s2中,所述的预热温度≥180℃;预热能够避免冷裂纹和再热裂纹的出现,预热温度过高可能会导致局部焊缝金属晶粒粗大。
46.实施例3的焊接道次顺序示意图如图4所示,焊接工艺焊接参数见表3。
47.表3200mm超厚板实施例焊接工艺焊接参数。
48.首先,坡口预热达标后,对留钝处理位置的焊接道次(1)进行打底焊接。打底焊接采用较小的焊接线能量,控制在22~27kj/cm,防止焊穿;控制层间温度300~350℃;然后调整
焊接线能量,控制在29~33kj/cm,按照焊接道次顺序进行填充焊接;控制层间温度180~250℃;焊接时采用pf-500/us-521h型耐热钢埋弧焊丝与焊剂,可得到具有优异的抗裂纹性能和低温冲击韧性,回火脆化敏感性低的焊缝金属。金属焊丝的化学成分及机械性能与母材匹配,既能保证焊缝金属的化学成分与母材匹配,还能保证焊接接头的机械性能尤其是抗拉强度、屈服强度及伸长率与母材匹配 ;焊接完成后立即进行消氢处理,以便溢出扩散氢,降低接头中的扩散氢含量,避免氢聚集导致延迟裂纹。消氢处理工艺条件是:保温温度300~350℃,保温时间2h;超厚板焊接接头消氢处理后,使用超声波方法进行无损检测,确保所有焊缝不出现焊接裂纹。具体的,根据nb/t 47013.3-2015,使用超声波方法进行无损检测,所有焊缝没有出现焊接裂纹,为ti级合格;检测无裂纹后,对超厚板焊接接头分别进行最小、最大焊后热处理,最小焊后热处理工艺条件是;当温度≥400℃时,升温/降温速度:≤55℃/h;保温温度705℃;保温时间8h;最大焊后热处理工艺保温时间为32h,其余条件与最小焊后热处理工艺相同。利用焊后热处理改善焊接接头的组织性能,使焊接接头的强度、硬度和韧性恢复到与母材金属相当的水平。
49.待焊后热处理完成24h后,还需使用超声波方法进行无损检测,确保所有焊缝不出现焊接裂纹。具体的,根据nb/t 47013.3-2015,使用超声波方法进行无损检测,所有焊缝没有出现焊接裂纹,为i级合格。
50.焊后性能检测结果:最大焊后热处理后,全厚度强度:25℃室温拉伸rel≥526mpa,rm≥632mpa;450℃高温拉伸rel=401mpa。-30℃冲击吸收能量:焊缝≥60j,热影响区≥200j。